Metalurgia do Pó
Summary
TLDRThis video explains the process of powder metallurgy, a technique for manufacturing parts from metallic and ceramic powders through compaction and sintering. It highlights the diverse applications of this process, including in automotive components, cutting tools, electrical contacts, and self-lubricating bushings. The video outlines the key stages: material preparation, mixing, compacting, sintering, and post-processing treatments like calibration and infiltration. Powder metallurgy allows the production of complex, cost-effective parts with specific mechanical and electrical properties, making it a vital process in various industries.
Takeaways
- 😀 Powder metallurgy is a process where metallic and ceramic powders are compacted and sintered to create complex parts.
- 😀 This process is ideal for producing small, intricate parts that are difficult or expensive to make with other methods.
- 😀 Applications of powder metallurgy include automotive components, electrical contacts, self-lubricating bushings, and cutting tools.
- 😀 The metal carbide material (metal duro) is widely used in machining tools because of its hardness, which comes from the carbide compounds in the material.
- 😀 The process involves mixing various powders (metals like iron, copper, and tin, or non-metals like graphite and ceramics) to achieve specific properties in the final part.
- 😀 The powder mixture is compacted in a die, where both top and bottom punches apply pressure to ensure uniform density in the final piece.
- 😀 Parts created in the compaction stage are called 'green parts' and are fragile, resembling a fragile plaster-like material.
- 😀 Sintering, the next step, involves heating the 'green part' to fuse the particles together without melting them, achieving a strong bond through atomic diffusion.
- 😀 The sintering process is typically done in a continuous furnace, with the parts entering on one side and exiting on the other after the heating process.
- 😀 The compacted parts' porosity can be controlled during compaction, which is crucial for applications like filters and lubricating bushings.
- 😀 After sintering, parts may undergo calibration to correct any dimensional distortion caused by thermal expansion or contraction during sintering.
- 😀 Additional treatments like impregnation or infiltration can be used to add lubricants or fill the pores of the part, enhancing its performance for specific applications.
Q & A
What is the Powder Metallurgy process, and how does it work?
-Powder Metallurgy is a manufacturing process in which metallic or ceramic powders are compacted and then sintered to create solid parts. The process involves mixing powders, compacting them into a desired shape, and heating them in a furnace to bond the particles together without melting the material.
What types of parts can be made using Powder Metallurgy?
-Parts made by Powder Metallurgy include complex geometries, small dimensions, and those with specific properties like porosity. These parts are commonly used in automotive, household appliances, electrical tools, and industries that require materials with special mechanical or electrical properties.
How does Powder Metallurgy contribute to cost-effective manufacturing?
-Powder Metallurgy is cost-effective because it can produce parts with complex shapes and fine details that would be difficult or expensive to make using traditional methods like machining. The process also allows for the use of mixed materials, such as hard alloys or composites, which can improve performance and reduce costs.
What are some specific examples of parts produced through Powder Metallurgy?
-Examples of parts produced include structural components for the automotive industry, cutting tools, electrical contacts, brushes for electric motors, self-lubricating bushings, ceramic insulators, friction materials like brake pads, and magnetic components like magnets.
What materials are typically used in Powder Metallurgy?
-Common materials include metallic powders like iron, copper, tin, and bronze, as well as non-metallic materials such as graphite and ceramic powders. These materials are mixed in precise proportions to achieve the required mechanical, electrical, and thermal properties.
What role does sintering play in the Powder Metallurgy process?
-Sintering is a key step in Powder Metallurgy where compacted powders are heated in a furnace to bond the particles together through atomic diffusion. This process increases the material's strength and structural integrity while maintaining its shape. It occurs at temperatures below the material's melting point.
What is the significance of porosity in Powder Metallurgy parts?
-Porosity is important in Powder Metallurgy because it can be controlled to create specific properties. For example, in self-lubricating bushings, porosity can hold lubricants, while in filters, it allows fluid flow. In structural parts, minimizing porosity increases mechanical strength.
Why is the mixing process critical in Powder Metallurgy?
-Mixing is critical because it ensures that the powders are evenly distributed, which is essential for achieving uniform mechanical properties. Uneven mixing can lead to sedimentation, where denser materials settle at the bottom, potentially causing defects in the final part.
What is the role of compacting in Powder Metallurgy, and how is it done?
-Compacting is the process of compressing the powder mixture into a mold to form a 'green' part. It involves applying pressure from both top and bottom punches to achieve a uniform density. The resulting green part is fragile and requires sintering to gain strength.
What are the post-sintering processes that might be required for Powder Metallurgy parts?
-After sintering, Powder Metallurgy parts may undergo several post-processing steps, including calibration to correct dimensional distortions, impregnation to add lubricants or other materials, infiltration to fill pores with low-melting-point metals, and surface treatments like coating for enhanced durability.
Outlines
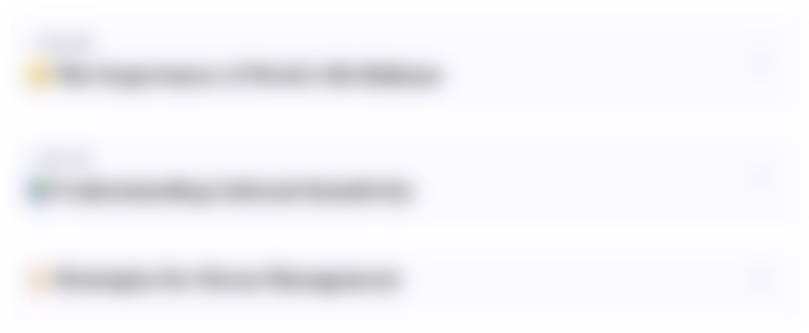
Esta sección está disponible solo para usuarios con suscripción. Por favor, mejora tu plan para acceder a esta parte.
Mejorar ahoraMindmap
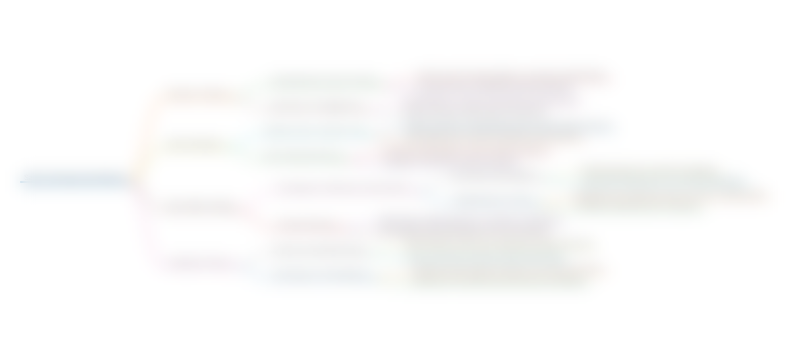
Esta sección está disponible solo para usuarios con suscripción. Por favor, mejora tu plan para acceder a esta parte.
Mejorar ahoraKeywords
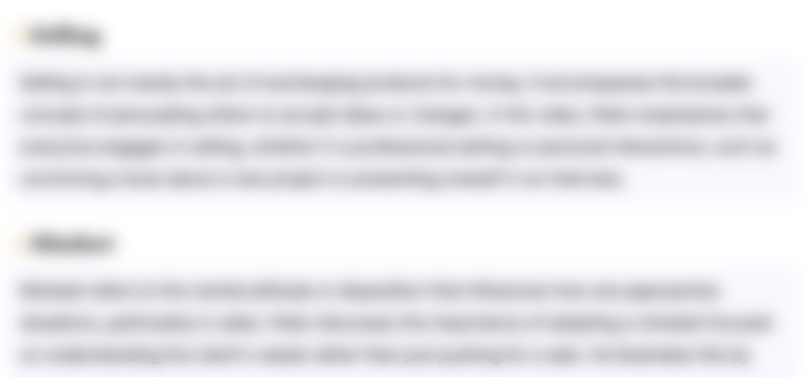
Esta sección está disponible solo para usuarios con suscripción. Por favor, mejora tu plan para acceder a esta parte.
Mejorar ahoraHighlights
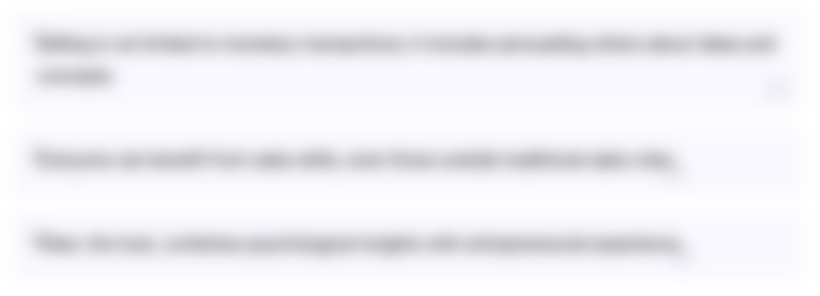
Esta sección está disponible solo para usuarios con suscripción. Por favor, mejora tu plan para acceder a esta parte.
Mejorar ahoraTranscripts
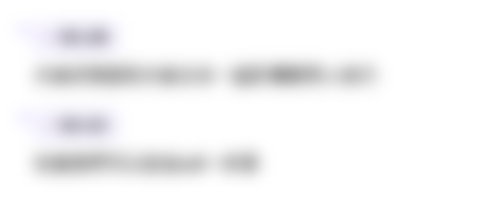
Esta sección está disponible solo para usuarios con suscripción. Por favor, mejora tu plan para acceder a esta parte.
Mejorar ahoraVer Más Videos Relacionados

Telecurso 2000 - Processos de Fabricação - 65 Metalurgia do pó

Conventional Press-and-Sinter Powder Metallurgy
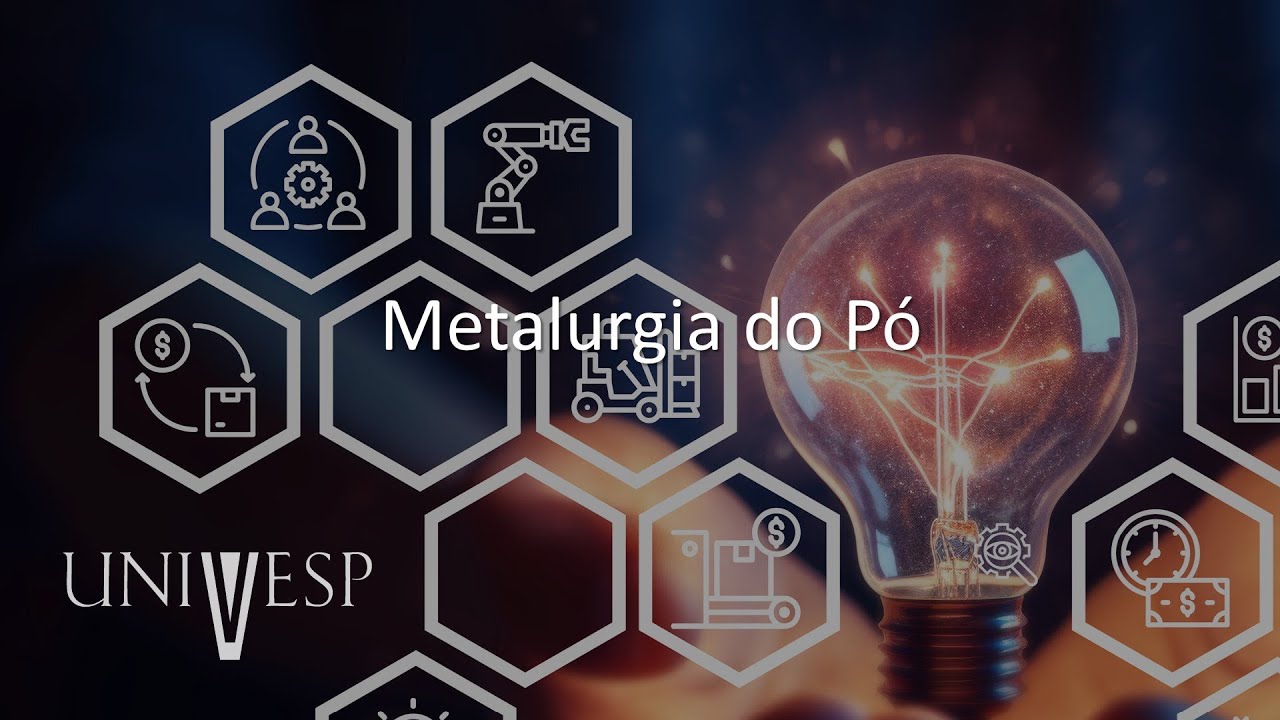
Materiais e Processos de Fabricação para Engenharia de Produção - Metalurgia do Pó

Powder Metallurgy Process

Materiais e Processos de Fabricação para Engenharia de Produção - Princípios de soldagem
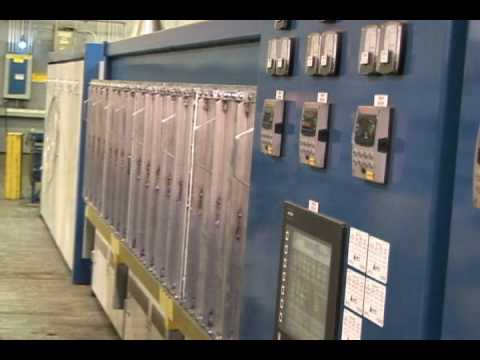
Powder Metallurgy Touches Your Life, Part 2
5.0 / 5 (0 votes)