Distribución por Proceso
Summary
TLDREn este video se aborda la distribución por proceso en el diseño de sistemas productivos, un enfoque ideal para empresas con baja demanda pero muchas referencias. Se explican conceptos clave como la agrupación de operaciones según su función, el uso de matrices de flujo y relaciones entre departamentos, y la importancia de optimizar las rutas de los pedidos dentro de la planta. Además, se muestra cómo calcular las necesidades de espacio y evaluar diferentes opciones de distribución para reducir la distancia recorrida por los productos. Finalmente, se destaca el uso de software para comparar y elegir la mejor distribución.
Takeaways
- 😀 La distribución por proceso agrupa las operaciones similares en función de los procesos que realizan, lo que facilita la producción cuando hay poco volumen pero muchas referencias.
- 😀 En una distribución por proceso, los pedidos pueden seguir rutas diferentes a través de la planta, dependiendo de las necesidades de cada producción.
- 😀 Esta distribución es ideal cuando se manejan varias referencias de productos pero no se tiene una alta demanda por cada uno.
- 😀 Un ejemplo práctico de distribución por proceso se presenta con una empresa metalmecánica que tiene seis departamentos: taladro y rectificación, equipos NC, embarque y recepción, tornos y taladros, depósito de herramientas e inspección.
- 😀 Para ubicar los departamentos correctamente, se deben conocer los requisitos de área de cada uno y la cantidad de unidades que se trasladarán entre ellos.
- 😀 La matriz de relaciones determina la proximidad de los departamentos entre sí, basándose en factores como la supervisión, el manejo de materiales y la salud de los empleados.
- 😀 El método heurístico de ingeniería se utiliza para encontrar una distribución ideal, pero con espacio para considerar limitaciones prácticas como el presupuesto o restricciones de espacio.
- 😀 La propuesta de distribución implica evaluar las distancias rectilíneas entre departamentos y calcular el costo de las distancias en función de las unidades que se mueven.
- 😀 A través de comparaciones entre la distribución actual y las propuestas alternativas, se puede determinar cuál es la más eficiente en términos de recorrido y carga entre departamentos.
- 😀 El uso de software de optimización es crucial para manejar todas las posibles alternativas y hacer una comparación más precisa, considerando múltiples factores y limitaciones de la planta.
Q & A
¿Qué es la distribución por proceso y cómo se aplica en los sistemas productivos?
-La distribución por proceso, también conocida como distribución por función, agrupa las máquinas y operaciones según su tipo o función. Este tipo de distribución es más adecuada para entornos con bajo volumen de producción pero una alta variedad de productos, donde cada producto sigue rutas diferentes a través de las distintas áreas de la planta.
¿Cuáles son los beneficios de usar distribución por proceso en una planta productiva?
-La distribución por proceso permite una mejor organización de las operaciones, especialmente en plantas con alta variabilidad en la producción. Facilita la agrupación de equipos similares y la optimización de las rutas que siguen los pedidos, lo que resulta en una mayor flexibilidad y eficiencia en la gestión de pedidos diversos.
¿Cómo se determina la cantidad de espacio requerido para cada departamento en una distribución por proceso?
-El espacio requerido para cada departamento se determina considerando las necesidades de cada área, como el equipo necesario y el tipo de procesos a realizar. En el ejemplo dado, se indicaron áreas específicas para cada departamento, como 1000 m² para el departamento de taladros y 950 m² para el equipo NC.
¿Qué es la matriz de movimiento y por qué es importante en la distribución por proceso?
-La matriz de movimiento describe cómo se moverán los productos entre los distintos departamentos, especificando la cantidad de unidades que deben transferirse entre ellos. Es crucial para optimizar el flujo de materiales y la disposición de los departamentos, garantizando que las rutas de transporte sean eficientes y minimicen los tiempos de desplazamiento.
¿Qué diferencia hay entre la matriz de relaciones y la matriz de movimiento?
-La matriz de relaciones define qué tan cerca o lejos deben estar los departamentos entre sí, basándose en factores como la seguridad y la eficiencia operativa. En contraste, la matriz de movimiento describe las cantidades de productos que se mueven entre los departamentos, ayudando a calcular las distancias y a organizar el flujo de trabajo.
¿Qué rol juega el método heurístico en la distribución por proceso?
-El método heurístico ayuda a identificar una distribución óptima de los departamentos dentro de la planta, considerando tanto las idealizaciones del diseño como las limitaciones prácticas, como el presupuesto y la infraestructura existente. Este enfoque permite encontrar soluciones satisfactorias sin necesidad de una optimización matemática exhaustiva.
¿Por qué se utiliza software para comparar alternativas de distribución por proceso?
-El uso de software permite evaluar múltiples alternativas de distribución de manera rápida y precisa, considerando diferentes variables como las distancias y el volumen de material en movimiento. Esto facilita la identificación de la opción más eficiente sin depender de cálculos manuales tediosos.
En el ejemplo dado, ¿cómo se calcula la eficiencia de una distribución propuesta?
-La eficiencia de una distribución se evalúa calculando la distancia total que deben recorrer los productos, multiplicada por las unidades de cada tipo de producto que se mueven entre los departamentos. La propuesta de distribución que minimize la distancia total de movimiento es considerada más eficiente.
¿Cuál fue el resultado de la comparación entre la distribución actual y la propuesta?
-La distribución propuesta resultó ser más eficiente que la distribución actual. La suma total de distancias en la distribución actual fue de 785, mientras que en la propuesta fue de 400, lo que demuestra que la nueva distribución reduce significativamente el recorrido de los productos.
¿Qué factores deben considerarse al determinar las ubicaciones de los departamentos en la planta?
-Los factores a considerar incluyen la cantidad de espacio necesario, las relaciones de proximidad entre departamentos, la optimización de los recorridos de material, la seguridad de los trabajadores, y las restricciones prácticas como el costo y la infraestructura disponible. Es importante balancear todos estos aspectos para lograr una distribución eficiente y segura.
Outlines
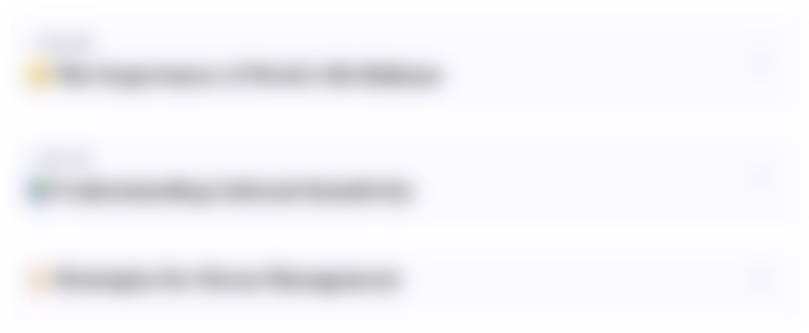
Esta sección está disponible solo para usuarios con suscripción. Por favor, mejora tu plan para acceder a esta parte.
Mejorar ahoraMindmap
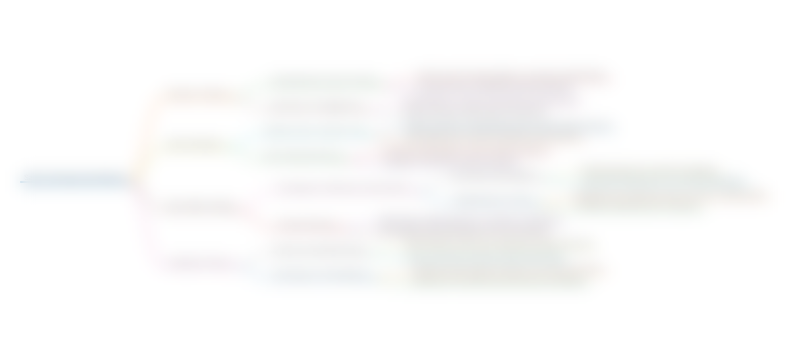
Esta sección está disponible solo para usuarios con suscripción. Por favor, mejora tu plan para acceder a esta parte.
Mejorar ahoraKeywords
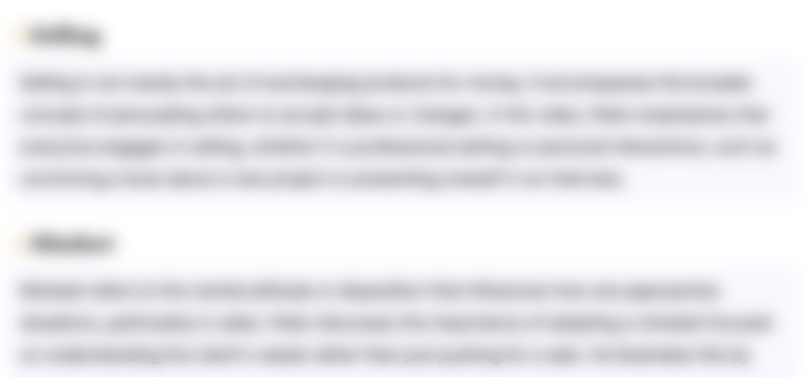
Esta sección está disponible solo para usuarios con suscripción. Por favor, mejora tu plan para acceder a esta parte.
Mejorar ahoraHighlights
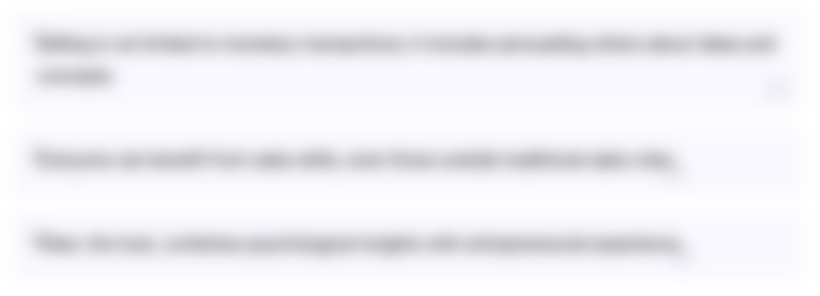
Esta sección está disponible solo para usuarios con suscripción. Por favor, mejora tu plan para acceder a esta parte.
Mejorar ahoraTranscripts
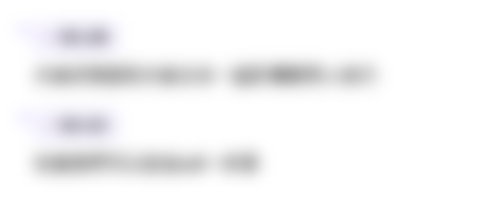
Esta sección está disponible solo para usuarios con suscripción. Por favor, mejora tu plan para acceder a esta parte.
Mejorar ahoraVer Más Videos Relacionados
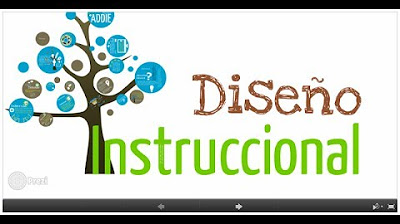
Soy Docente: DISEÑO INSTRUCCIONAL
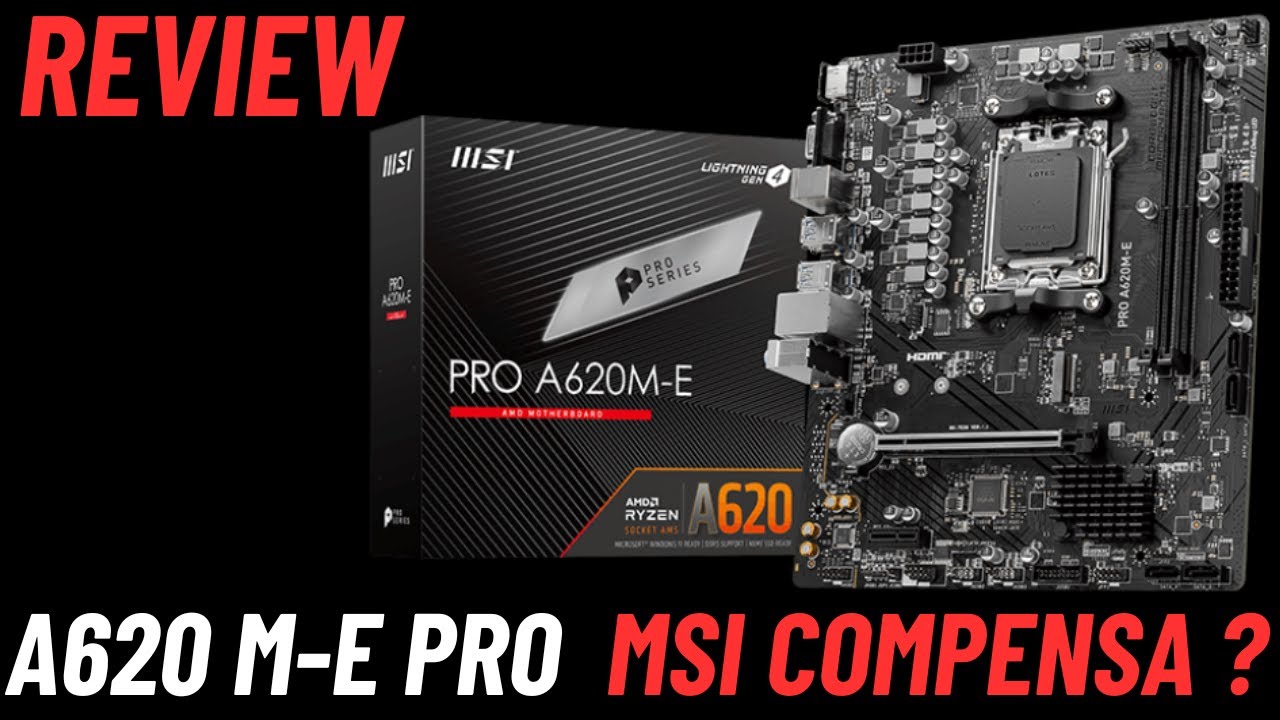
PRO A620 M-E MSI REVIEW - VRM INFERIOR A520 A-PRO MSI AM4 ? Caparam a placa AM5 ? Water Rise ?

Teoría de Restricciones
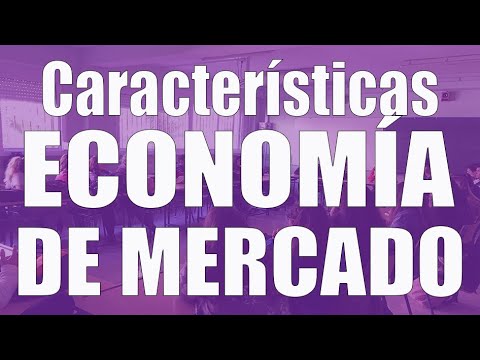
Características de la economía de mercado: cómo resuelve los problemas económicos básicos
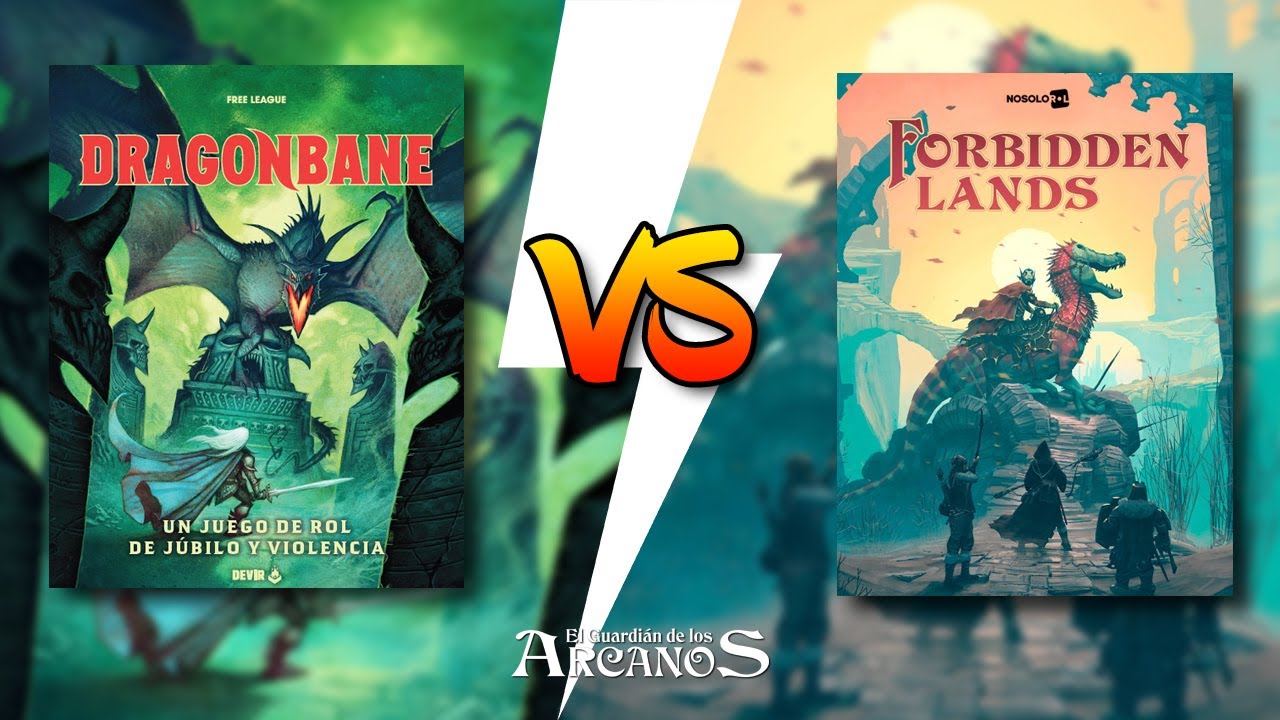
Dragonbane VS Forbidden Lands
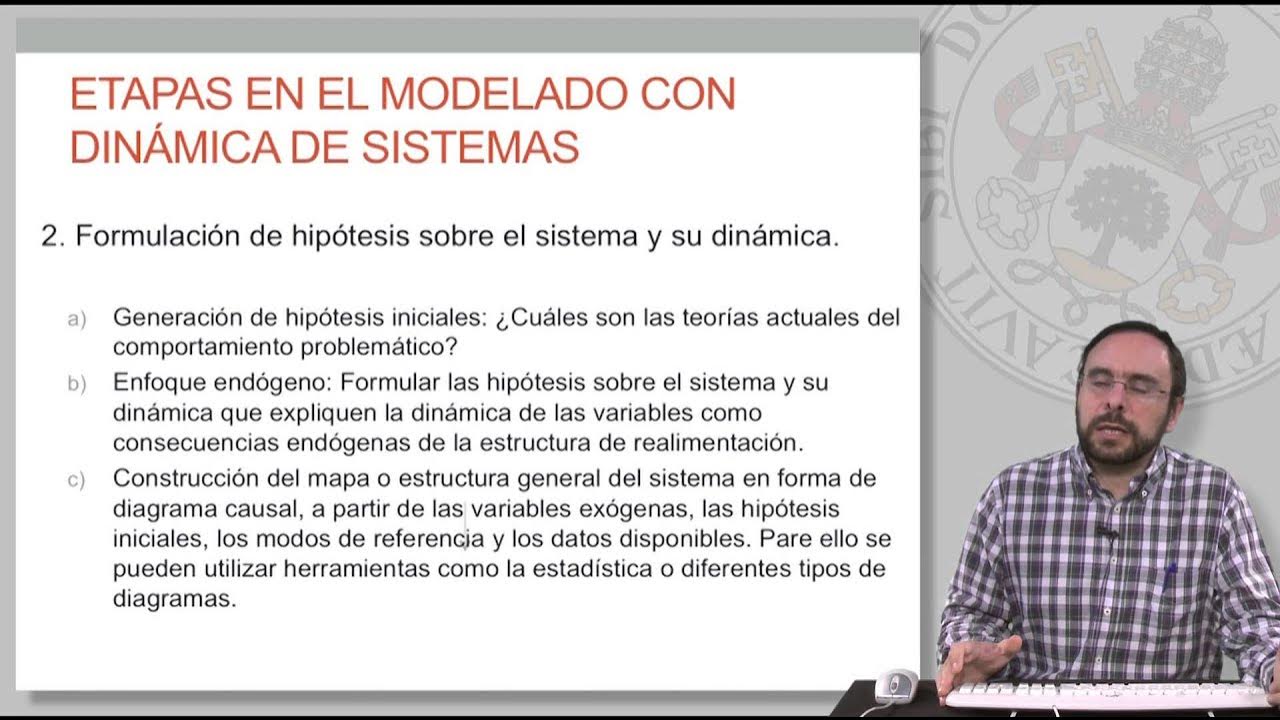
3. MODELADO CON DINÁMICA DE SISTEMAS
5.0 / 5 (0 votes)