Photopolymer plate making for letterpress printing, in-depth walk-through.
Summary
TLDRThis video offers a detailed guide to the photopolymer plate-making process for printing. Michael from Sylvan Printer explains each step, from creating a film positive to developing the plate. He highlights the importance of calibration and equipment, including exposure units, UV light, and washing methods. The video emphasizes trial and error in fine-tuning settings for sharp, high-quality plates. Alongside technical advice, Michael provides tips for ensuring consistent results and encourages viewers to take notes and adjust based on experience. The process may seem complex, but with patience, it becomes manageable.
Takeaways
- 🔧 The photopolymer plate-making process involves multiple steps, but with care and patience, you can achieve crisp results.
- 🖼️ You need to create a film positive before developing the photopolymer plate. The film and plate are exposed to UV light to develop the image.
- 🖨️ A high-quality printer with pigment ink is essential for creating film positives that block UV light effectively. Epson SureColor P9070 is recommended.
- 🖥️ A RIP (raster image processor) like Filmmaker is crucial to manage the printer for even and high-density ink coverage on the film.
- 💡 UV exposure is key to hardening the photopolymer plate. Calibrating the exposure time using tools like a Stouffer gauge is important for consistent results.
- 🧼 Plates can be washed out by hand or using a machine after exposure, with care to ensure even washing without damaging the surface.
- 🔥 Plates must be dried and hardened after washing. Proper drying and UV exposure harden the plates for use in printing, especially for crush printing.
- 📏 Ensuring the plate is at 'type height' is critical for proper inking and consistent printing results. Adhesive film is used to attach the plate to the printing base.
- ♻️ The water used in washing out plates is contaminated and needs to be disposed of according to local regulations.
- 📚 Meticulous calibration and record-keeping for each step of the process are essential to achieving high-quality, consistent photopolymer plates.
Q & A
What is the first step in the photopolymer plate-making process?
-The first step is creating a film positive, which is used to expose the photopolymer plate in the exposure unit.
Why is it important to use a high-quality film positive in the plate-making process?
-A high-quality film positive ensures that the UV light cures the exposed portions of the image while leaving sharp edges, which results in crisp and detailed photopolymer plates.
What equipment is necessary for making a photopolymer plate?
-Key equipment includes a plate-making unit (which may include an exposure table, scrubbing system, and convection heater), a printer for film positives, a UV exposure unit, and adhesive film for mounting the plate onto the base.
Why is calibration essential in the photopolymer plate-making process?
-Calibration ensures that each step of the process is optimized for consistent, high-quality results. This includes calibrating the exposure time, washout time, and drying time to achieve the best final plate.
What is the purpose of a Stouffer gauge in the plate-making process?
-A Stouffer gauge helps calibrate the UV exposure unit by indicating the correct exposure time needed for the photopolymer plate based on the manufacturer’s recommended values.
How does UV light affect the photopolymer plate, and how can this be controlled?
-UV light cures the exposed portions of the photopolymer plate. It's crucial to limit any unintended UV light exposure by controlling the work environment and using appropriate UV light levels during exposure.
What steps are involved after exposing the photopolymer plate to UV light?
-After UV exposure, the unexposed portions of the plate are washed out, the plate is dried, and then given a final exposure to fully harden it for printing.
Why is it necessary to use a special type of adhesive for mounting the photopolymer plate onto the base?
-The adhesive must be able to withstand the pressure during printing without deforming, ensuring that the plate remains at the correct type height for consistent inking.
Can the washout process be done manually without a machine?
-Yes, the washout process can be done manually using a soft brush and lukewarm water, though it may require more effort and practice to achieve consistent results.
What are some common challenges when creating photopolymer plates?
-Common challenges include calibrating the equipment for the desired exposure and washout times, maintaining consistent UV light levels, and ensuring crisp and sharp details on the plate. It may take trial and error to achieve perfect results.
Outlines
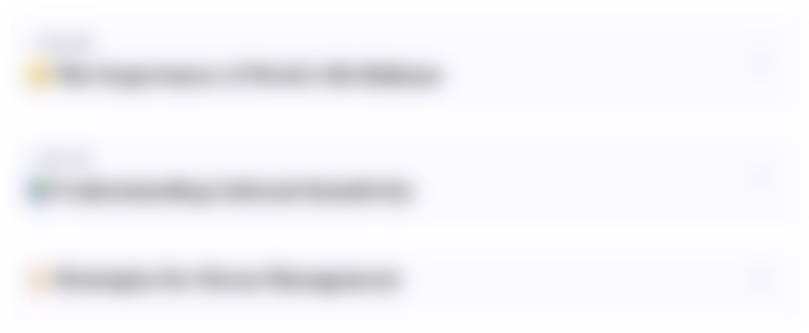
Esta sección está disponible solo para usuarios con suscripción. Por favor, mejora tu plan para acceder a esta parte.
Mejorar ahoraMindmap
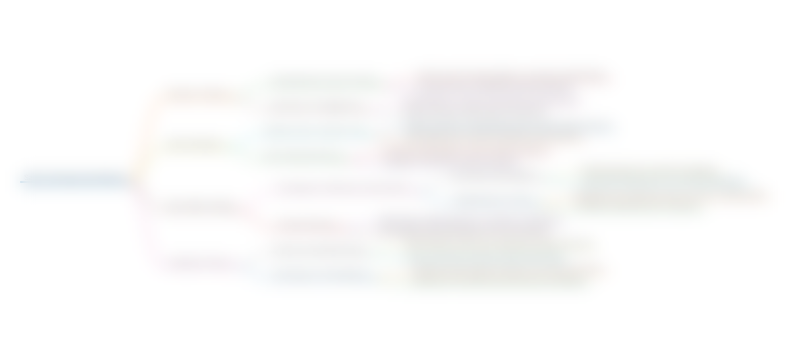
Esta sección está disponible solo para usuarios con suscripción. Por favor, mejora tu plan para acceder a esta parte.
Mejorar ahoraKeywords
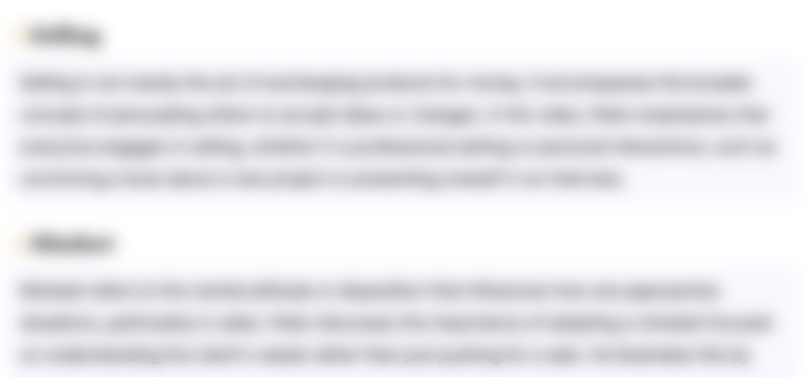
Esta sección está disponible solo para usuarios con suscripción. Por favor, mejora tu plan para acceder a esta parte.
Mejorar ahoraHighlights
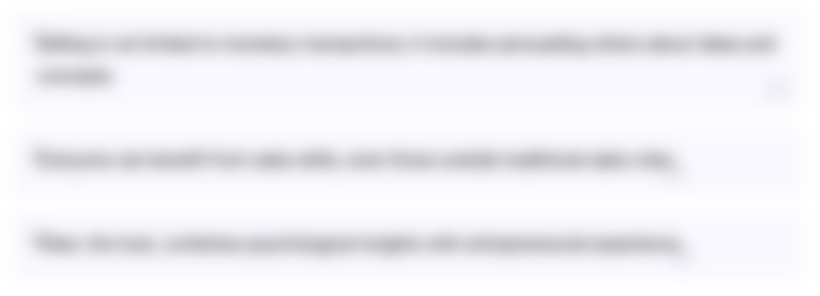
Esta sección está disponible solo para usuarios con suscripción. Por favor, mejora tu plan para acceder a esta parte.
Mejorar ahoraTranscripts
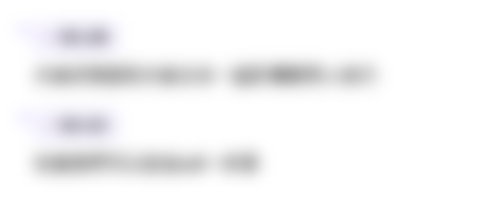
Esta sección está disponible solo para usuarios con suscripción. Por favor, mejora tu plan para acceder a esta parte.
Mejorar ahoraVer Más Videos Relacionados
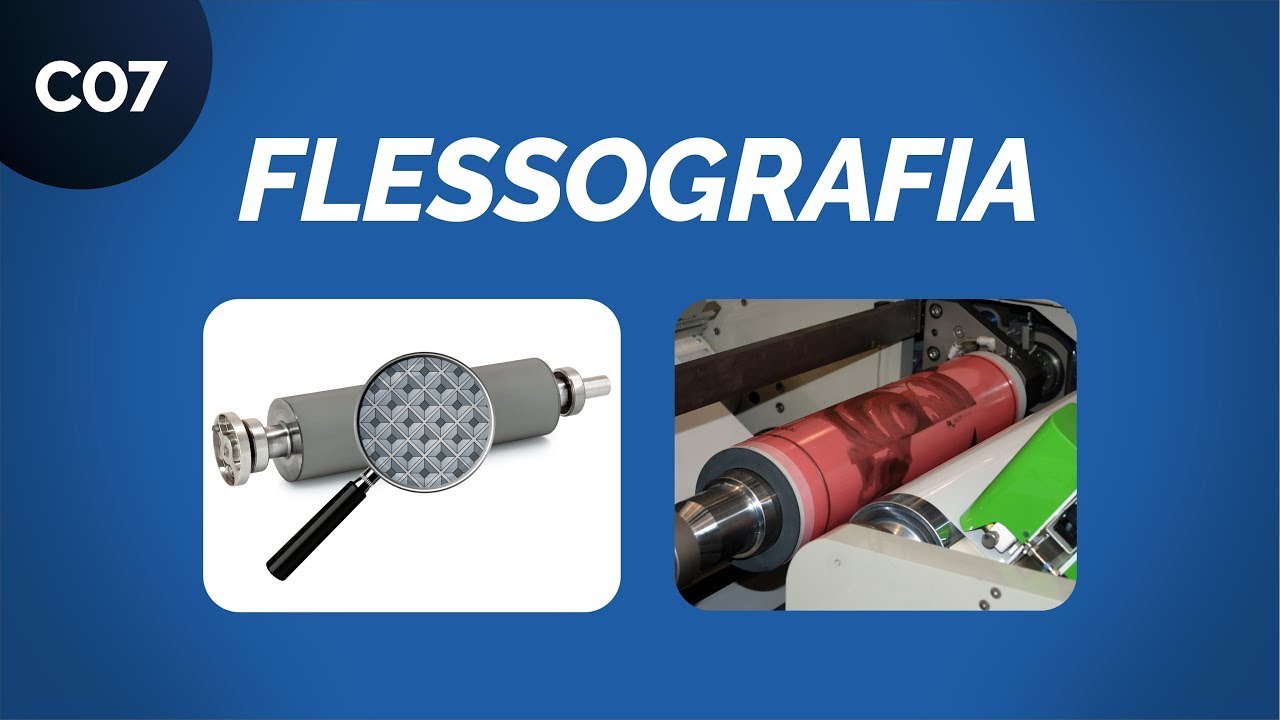
Flessografia: stampa su confezioni e imballi // Daniele Cogo
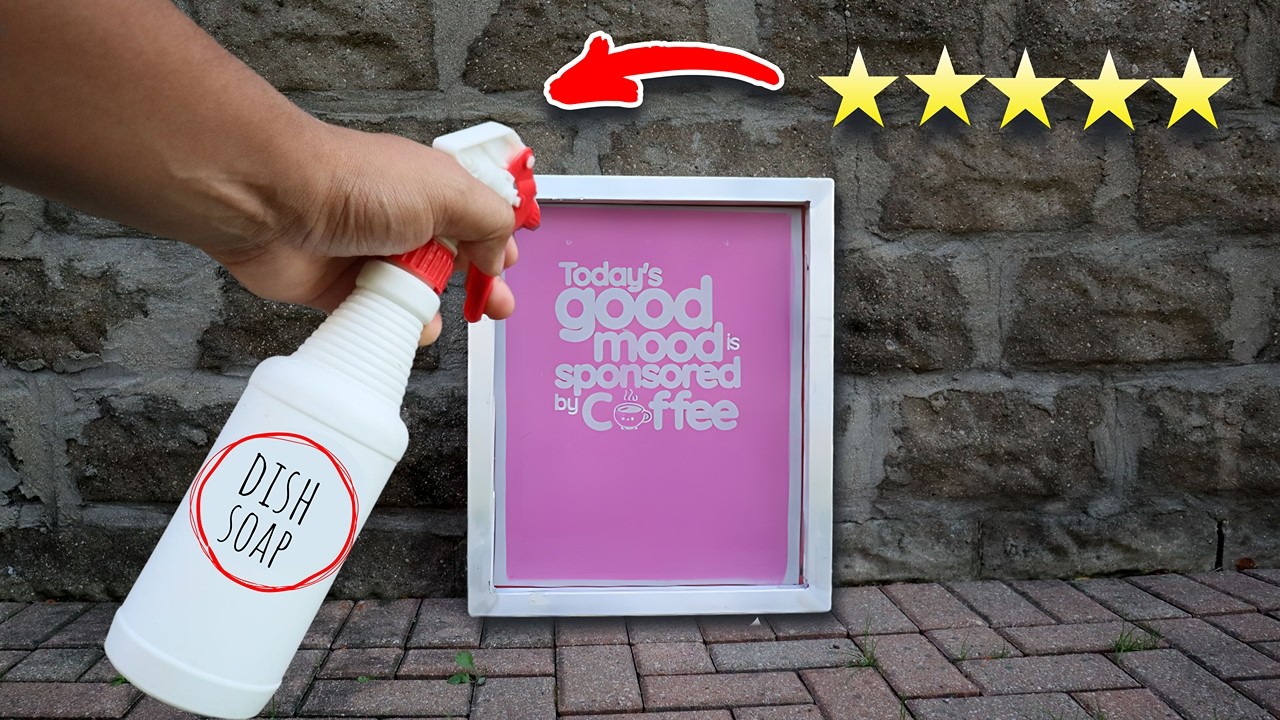
How to Burn Your Own Screens from Home: Screen Print Tutorial

Pergantian plat nomor kendaraan hilang atau rusak di SAMSAT

How To Make Bookmarks | Double Sided 📚✨ procreate tutorial for double sided bookmarks
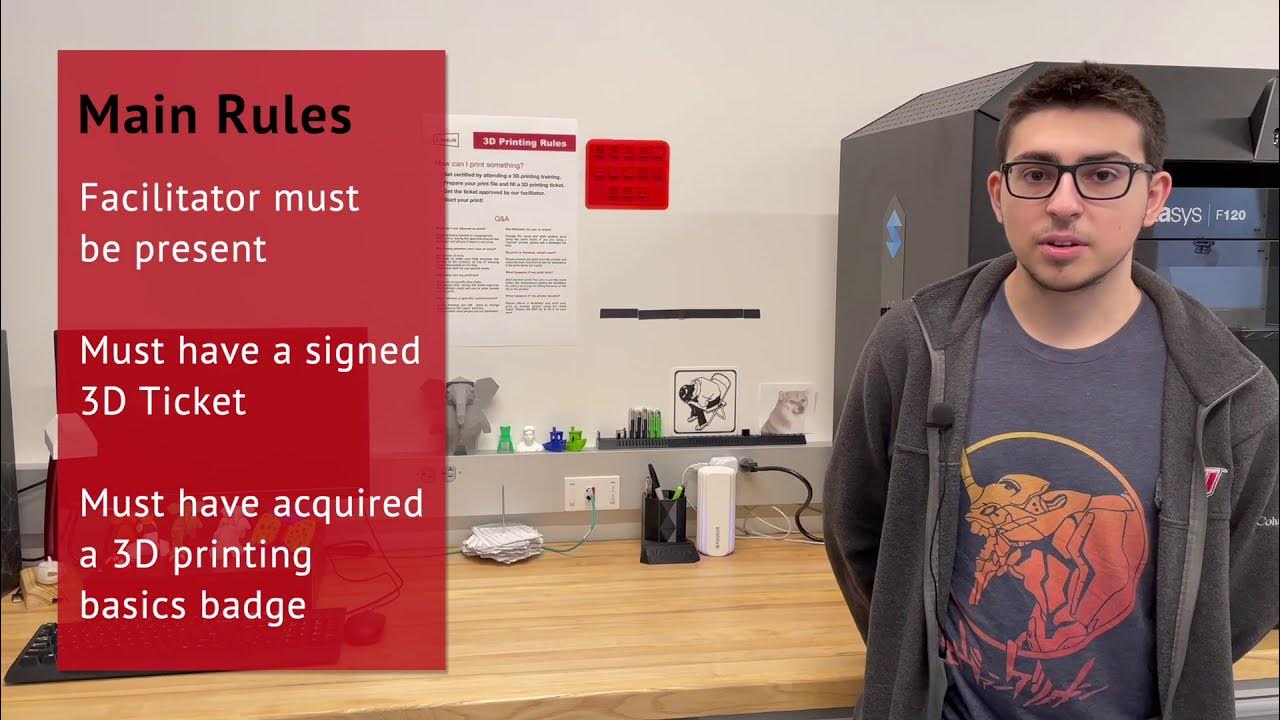
3D Printing Basics Training
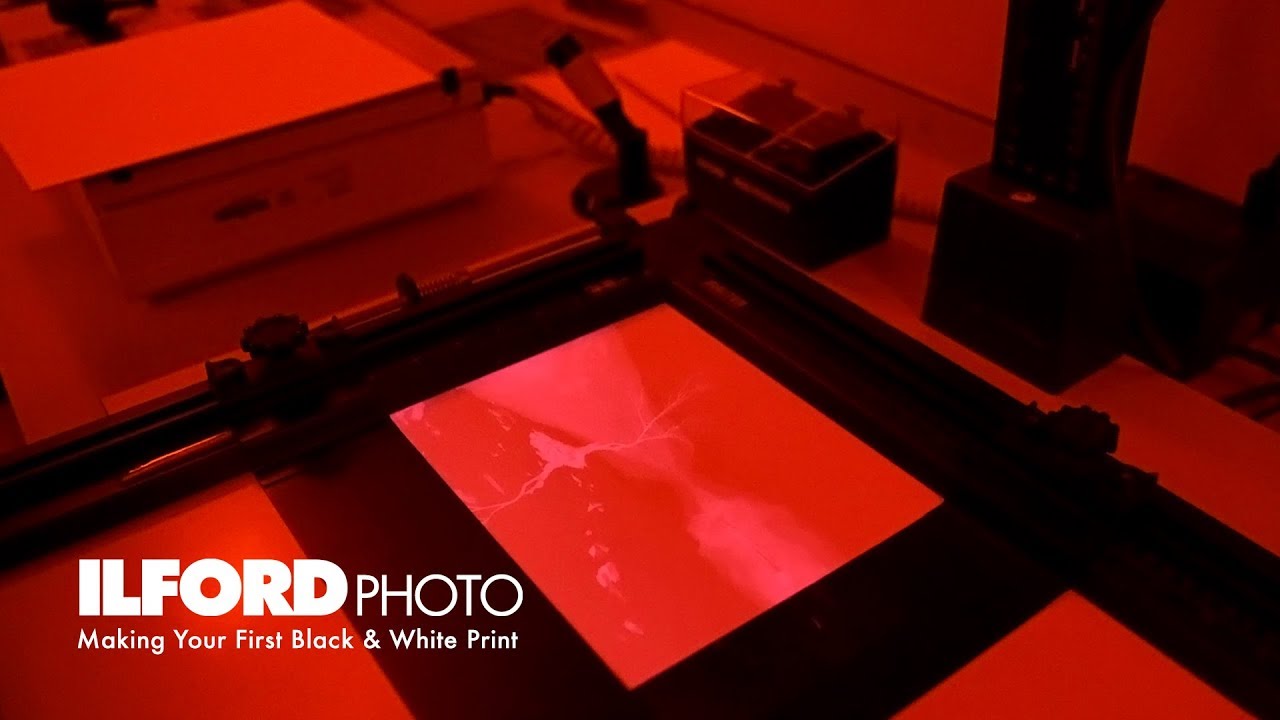
Making Your First Black & White Darkroom Print
5.0 / 5 (0 votes)