Get the Most Aluminum From Melting Cans
Summary
TLDRIn this intriguing video, the host embarks on a project to extract aluminum from soda cans, addressing the common misconceptions about the quality of aluminum from cans. Despite the presence of a plastic liner and the challenges of oxidation during melting, the host demonstrates a method to minimize aluminum loss. Using a crucible, they form a pool of molten aluminum and dunk cans to reduce oxidation. The video also explores the addition of flux to separate impurities and the potential alloying with copper to improve casting and machining properties. The host concludes with tips on enhancing the aluminum's usability and the importance of distinguishing between pure and cast aluminum.
Takeaways
- 🥤 Cans are a common source of aluminum, but the aluminum obtained from them is not of high quality due to the presence of a plastic liner and oxidation issues.
- 🔥 The process of melting cans involves dealing with oxidation that occurs before the aluminum melts, which can reduce the quality of the aluminum obtained.
- 🚮 The plastic liner inside cans prevents the acidic beverage from corroding the aluminum, but it also means that around half the weight of a can is not aluminum.
- 🏺 To minimize loss of aluminum, the process involves creating a pool of liquid aluminum and dunking the cans into it to melt them quickly.
- 🔭 The aluminum from cans is fairly pure but lacks silicon, which is needed to improve its casting and machining properties.
- 🧪 Using a flux, such as Morton's light salt, can help reduce the amount of dross (oxidized aluminum) and improve the purity of the aluminum obtained.
- 🛠️ The video demonstrates a method to purify aluminum from cans by melting them and managing the dross to get a more workable metal.
- 📏 There's a noticeable difference in the appearance and properties between pure aluminum from cans and cast aluminum, with the former being shinier and less dense.
- 🔩 Adding elements like copper to the aluminum can improve its casting and machining properties, making it more suitable for various applications.
- 📊 The video provides a practical demonstration of weighing aluminum and copper to achieve the right proportions for alloying, highlighting the importance of accurate measurements in metallurgy.
- 🎥 The script is from a video that not only instructs on the process but also shares the experimenter's observations and tips for successfully working with aluminum from cans.
Q & A
What is the main issue with using aluminum cans as a source of aluminum?
-The main issue with using aluminum cans as a source of aluminum is that the aluminum obtained from them isn't very good due to the presence of a plastic liner and the fact that it oxidizes before it melts, which results in a significant loss of aluminum.
Why is silicon important when melting aluminum from cans?
-Silicon is important because it helps to improve the casting and machining properties of the aluminum. The aluminum from cans lacks silicon, making it less desirable for certain applications.
What is the purpose of using a flux when melting aluminum cans?
-The purpose of using a flux is to reduce the oxidation of aluminum and to help separate impurities like the plastic liner and dross from the molten aluminum, thus improving the purity and quality of the aluminum obtained.
How does the process of dunking cans into a pool of molten aluminum work?
-The process involves melting a piece of aluminum to form a pool, and then dunking aluminum cans into this pool to melt them. This method helps to minimize oxidation and maximize the amount of aluminum salvaged from the cans.
What is the role of the plastic liner inside the cans during the melting process?
-The plastic liner inside the cans acts as a barrier to prevent the acidic content of the beverage from corroding the aluminum. However, during the melting process, it becomes part of the dross and reduces the overall aluminum yield.
Why does the video suggest adding copper to the aluminum from cans?
-Adding copper to the aluminum from cans is suggested to improve its casting and machining properties. Pure aluminum is soft and not ideal for machining, so copper is added to create an alloy that is stronger and more suitable for these purposes.
How can one determine the percentage of copper to add to the aluminum?
-One can determine the percentage of copper to add by calculating the desired total weight of the alloy and then adding the appropriate amount of copper to achieve 5% to 10% of that total weight.
What is dross and why is it a problem during the melting of aluminum cans?
-Dross is the impure residue that forms on the surface of molten metal due to oxidation and other impurities. It is a problem because it traps aluminum, reducing the yield of pure aluminum and also because it can contaminate the metal.
How does the aluminum from cans compare to cast aluminum in terms of appearance and properties?
-The aluminum from cans is purer and appears shinier compared to cast aluminum, which has a less shiny and dirtier surface. Cast aluminum also exhibits more shrinkage than aluminum from cans.
What is the significance of the non-stick coating burning off in the pan during the pouring process?
-The burning off of the non-stick coating indicates that the temperature of the molten aluminum is high enough to damage the pan's coating, which could contaminate the aluminum and also suggests that special care should be taken when choosing containers for pouring molten aluminum.
What is the final step the presenter takes to ensure the aluminum ingots are properly cast?
-The final step the presenter takes is to tighten the lid of the crucible after it has expanded due to heat, ensuring a tight seal to contain the aluminum as it cools and solidifies into ingots.
Outlines
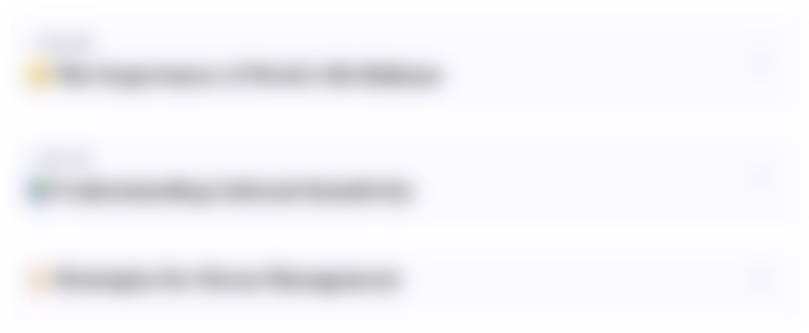
Esta sección está disponible solo para usuarios con suscripción. Por favor, mejora tu plan para acceder a esta parte.
Mejorar ahoraMindmap
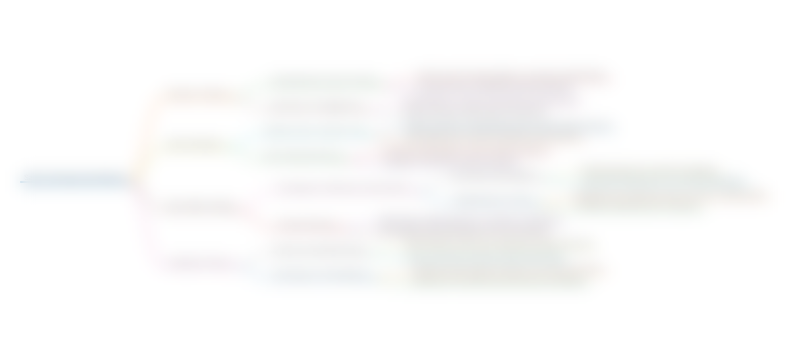
Esta sección está disponible solo para usuarios con suscripción. Por favor, mejora tu plan para acceder a esta parte.
Mejorar ahoraKeywords
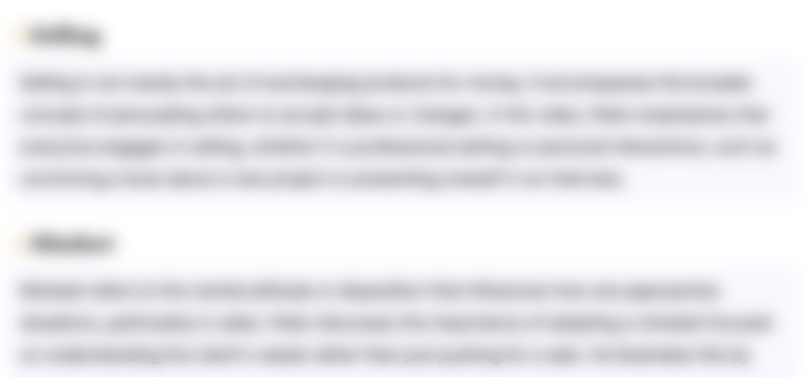
Esta sección está disponible solo para usuarios con suscripción. Por favor, mejora tu plan para acceder a esta parte.
Mejorar ahoraHighlights
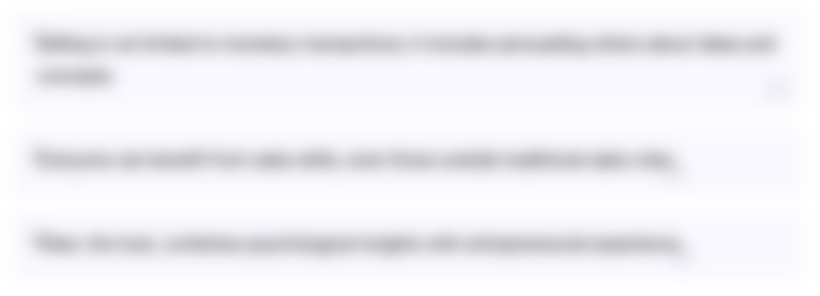
Esta sección está disponible solo para usuarios con suscripción. Por favor, mejora tu plan para acceder a esta parte.
Mejorar ahoraTranscripts
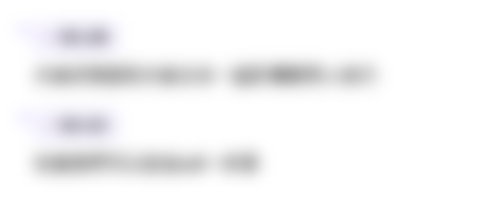
Esta sección está disponible solo para usuarios con suscripción. Por favor, mejora tu plan para acceder a esta parte.
Mejorar ahora5.0 / 5 (0 votes)