BASF Battery Recycling Presentation - How does hydrometallurgical battery recycling work?
Summary
TLDRThis presentation focuses on the recycling of electric vehicle batteries, emphasizing the need for an efficient and circular economy to reclaim valuable metals like nickel, cobalt, and lithium. BASF's innovative hydrometallurgical process aims to recover battery-grade lithium hydroxide directly, improving recycling efficiency while reducing waste. The presenter highlights the challenges and innovations involved, such as the purification of contaminants like fluoride. With pilot trials concluded and plans for a pilot plant in 2022, BASF aims to advance battery recycling technology, addressing both ecological and economic concerns in the growing electric vehicle market.
Takeaways
- 🔋 Electric vehicles are crucial for a climate-neutral society, and their batteries contain valuable materials like nickel, cobalt, manganese, and lithium.
- ♻️ By 2030, 1.6 million tons of end-of-life electric vehicle batteries are expected, necessitating efficient recycling solutions.
- 🔧 Battery recycling involves disassembling, shredding, and sorting batteries to extract metals like copper, aluminum, and the key active materials in the 'black mass.'
- ⚫ 'Black mass' contains valuable metals like graphite, nickel, cobalt, and lithium, but also has contaminants, requiring further chemical processing.
- 🔥 Pyrometallurgy heats the black mass to 1500°C, melting valuable metals, but lithium ends up in the slag, making it inefficient for lithium recovery.
- 💧 Hydrometallurgy uses sulfuric acid at moderate temperatures to extract nickel, cobalt, copper, and lithium, but is more complex and costly.
- 🧪 BASF's recycling process focuses on hydrometallurgy and aims to selectively extract high-quality battery-grade lithium hydroxide.
- 🌱 BASF's lithium extraction process minimizes carbon footprint and sodium sulfate byproducts, enhancing sustainability.
- 🔍 Removing fluoride and other contaminants from lithium hydroxide is critical for maintaining battery performance and longevity.
- 🏗️ BASF plans to build a pilot plant for this process by 2022 in Schweitzer, Europe, aiming to scale up the technology for global battery recycling.
Q & A
What is the significance of battery recycling in the context of electromobility?
-Battery recycling is crucial for electromobility as it contributes to a circular economy and helps in achieving a climate-neutral society by ensuring the efficient reuse of valuable materials from electric vehicle batteries.
What are the key components of an electric vehicle battery?
-The key components of an electric vehicle battery include two electrodes, an anode made of graphite and a cathode made with materials such as nickel, cobalt, manganese, and lithium, along with a separator to prevent short circuits and an electrolyte for charge exchange.
By what year is it predicted that 1.6 million tons of end-of-life batteries will be generated?
-According to a Bloomberg study, by 2030, it is expected that 1.6 million tons of end-of-life batteries will be generated.
What is the economic importance of recycling battery packs?
-Battery packs contain valuable metals like lithium, nickel, cobalt, and about 160,000 tons of these metals, which is approximately 10 percent of the overall waste amount, making their recycling economically significant.
What is the 'black mass' mentioned in the script?
-The 'black mass' is the product of mechanical processing of used batteries, which contains the active materials of the battery, including carbon or graphite from the anode and valuable materials from the cathode, along with various contaminations.
What are the two primary methods for processing the 'black mass' from used batteries?
-The two primary methods for processing the 'black mass' are pyrometallurgy, which involves heating the material to high temperatures in a smelter, and hydrometallurgy, which takes place at moderate temperatures in an aqueous sulfuric acid solution.
Why is lithium not considered a precious metal in the context of pyrometallurgy?
-Lithium is not considered a precious metal in pyrometallurgy because it ends up in the slag, which is typically sold to the construction industry, making its recovery less economically viable compared to other metals like nickel and cobalt.
What is BASF's approach to improving lithium yield and reducing the carbon footprint in battery recycling?
-BASF's approach involves a hydrometallurgical process that directly extracts lithium hydroxide from the black mass, avoiding the formation of sodium sulfate and additional steps required to convert lithium carbonate into lithium hydroxide, thus reducing the carbon footprint.
What challenges does BASF face in purifying lithium hydroxide to battery-grade quality?
-BASF faces challenges in removing contaminants to a two-digit ppm level from lithium hydroxide to ensure battery quality and performance. Fluoride, in particular, is challenging to remove beyond a certain point as it becomes part of the crystal structure of lithium hydroxide.
What is the current status of BASF's pilot plant for battery recycling, and when is it planned to start?
-As of the presentation, BASF is preparing the pilot plant, which is planned to be commissioned in 2022. The pilot plant will be used to demonstrate the entire process and determine the parameters needed for large-scale production.
How does BASF plan to scale up its battery recycling process from pilot trials to global implementation?
-BASF plans to scale up its battery recycling process by first focusing on Europe, using the pilot plant to demonstrate the process and gather data for large-scale production. The goal is to eventually make battery recycling a global reality.
Outlines
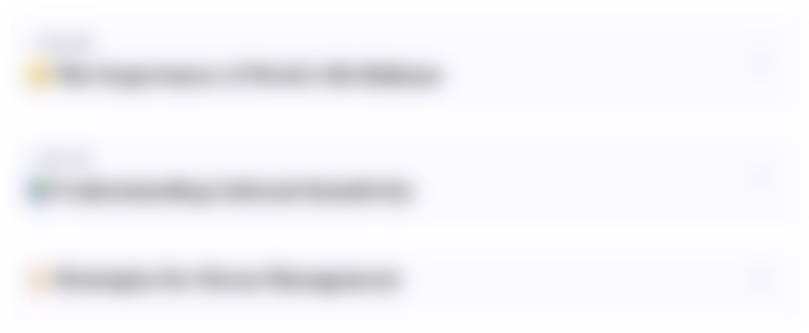
Esta sección está disponible solo para usuarios con suscripción. Por favor, mejora tu plan para acceder a esta parte.
Mejorar ahoraMindmap
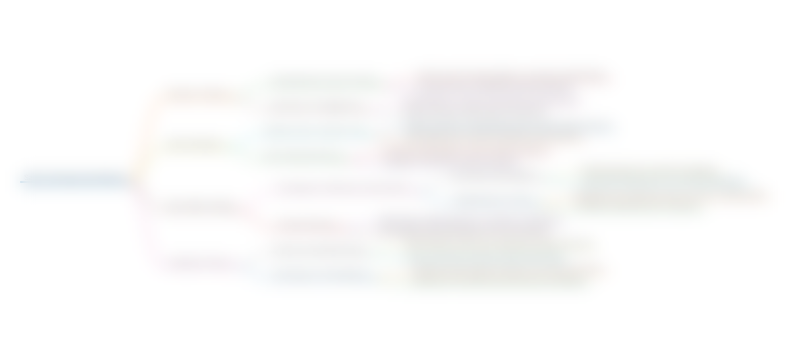
Esta sección está disponible solo para usuarios con suscripción. Por favor, mejora tu plan para acceder a esta parte.
Mejorar ahoraKeywords
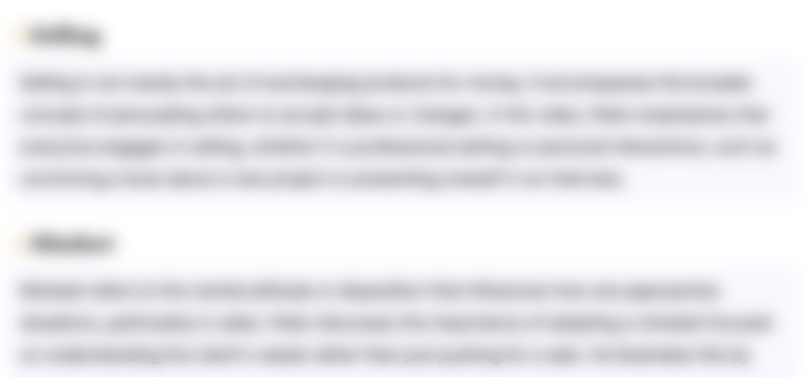
Esta sección está disponible solo para usuarios con suscripción. Por favor, mejora tu plan para acceder a esta parte.
Mejorar ahoraHighlights
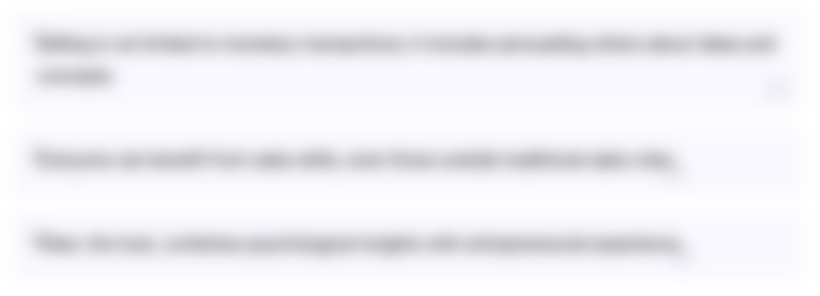
Esta sección está disponible solo para usuarios con suscripción. Por favor, mejora tu plan para acceder a esta parte.
Mejorar ahoraTranscripts
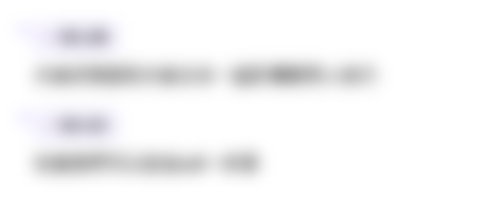
Esta sección está disponible solo para usuarios con suscripción. Por favor, mejora tu plan para acceder a esta parte.
Mejorar ahoraVer Más Videos Relacionados

Was machen wir mit den ganzen E-Auto-Batterien?

Why It's So Hard To Recycle Electric-Car Batteries | World Wide Waste
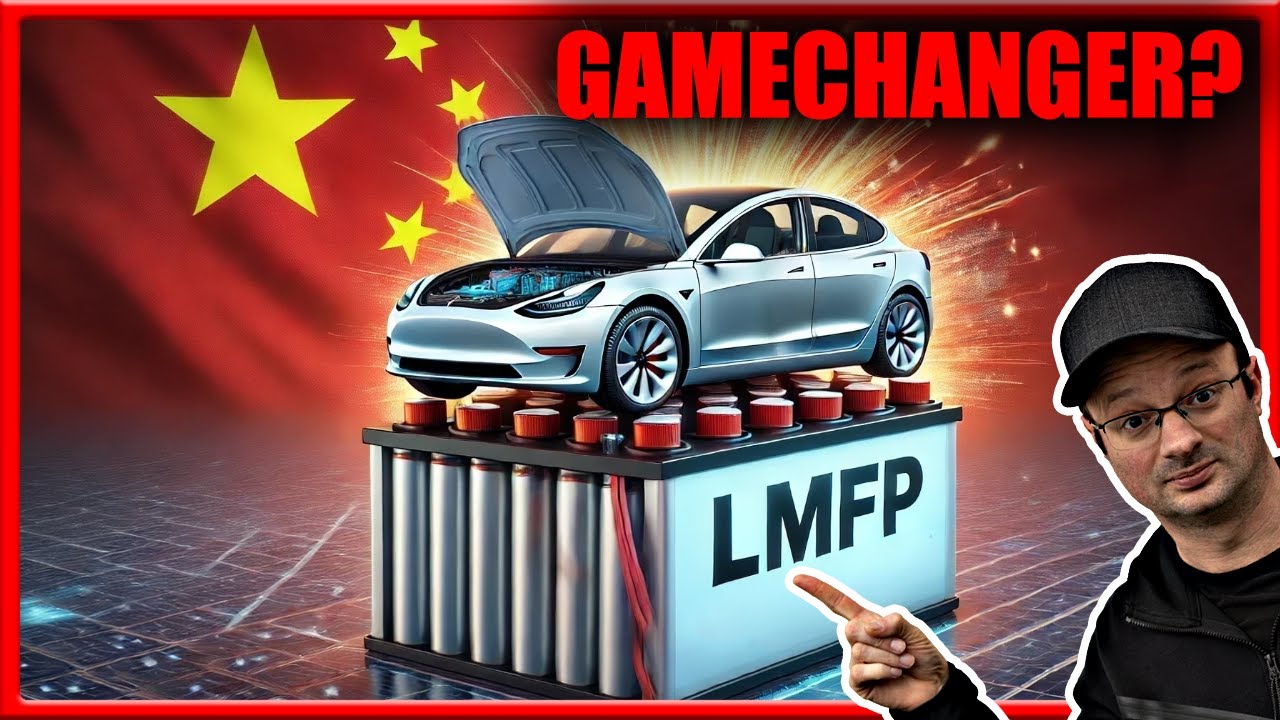
LMFP Akkus - Hat China den Durchbruch geschafft?
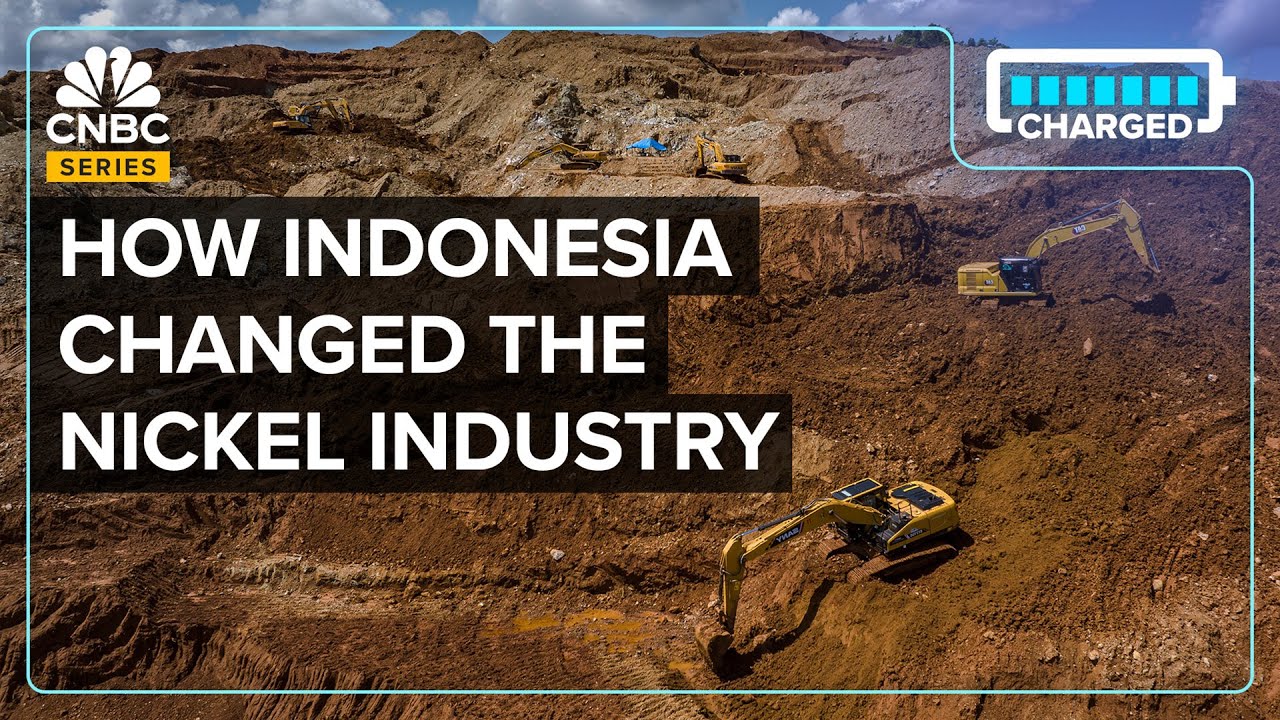
How China Took Over Indonesia’s Nickel Industry To Fuel Its EVs
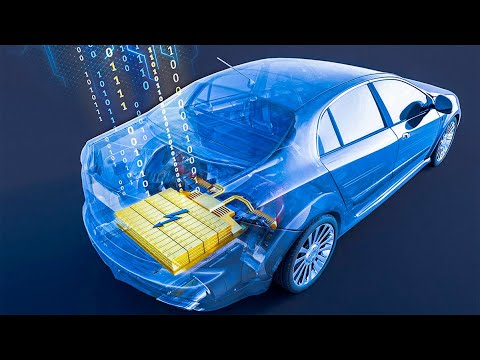
Electric Car Batteries Everything You Need To Know

EV range could skyrocket 20% with new LMFP magnesium doped battery
5.0 / 5 (0 votes)