ABB - Reliability-Centered Maintenance
Summary
TLDRThis video introduces Reliability-Centered Maintenance (RCM), a world-class maintenance approach for optimizing assets in industries like manufacturing and process automation. It covers three key topics: equipment criticality analysis, failure modes and effects analysis (FMEA), and how to implement RCM. The presenter, Dave Bureaus from ABB, highlights the balance between preventive, reactive, and proactive maintenance, emphasizing the importance of maintaining equipment efficiently without inducing failure. Safety, production impact, and cost are central to the criticality analysis. ABB's tools, like Service Pro and advanced services, are showcased as essential for successful RCM implementation.
Takeaways
- 🔧 Reliability-centered maintenance (RCM) is a high-level strategy designed to optimize all assets in a facility by using a variety of maintenance approaches.
- 🏭 RCM is considered the world-class maintenance approach for industries such as manufacturing and process industries.
- 📉 Preventive maintenance can reduce unplanned repairs and lower overall maintenance costs but doing too much can also induce failures or increase costs.
- ⚙️ Before RCM, common strategies included reactive maintenance (fix after failure), preventive maintenance (regular maintenance), proactive maintenance (easy-to-maintain designs), and predictive maintenance (using technology to predict failures).
- 🎯 RCM only selects the appropriate maintenance strategy for each piece of equipment, and sometimes it may not require any maintenance if the equipment is low-cost or redundant.
- 🛠️ The three key steps in RCM are: preserving equipment functionality by determining criticality, identifying and prioritizing failure modes, and implementing the correct maintenance strategy.
- 🚨 Criticality analysis must always prioritize safety, followed by environmental, production, maintenance costs, and the effect on other systems.
- 📊 Failure Modes and Effects Analysis (FMEA) identifies potential failures and the causes, ranking them based on likelihood and impact, and recommends actions to prevent or address them.
- 👥 Successful RCM implementation requires a cross-functional team from various departments, including mechanical maintenance, process control, operations, and engineering.
- 💻 Tools like ABB’s ServicePro and ServicePort help analyze maintenance data, identify critical equipment, and assist in benchmarking performance to improve reliability-centered maintenance practices.
Q & A
What is Reliability-Centered Maintenance (RCM)?
-Reliability-Centered Maintenance (RCM) is a high-level maintenance strategy designed to optimize the performance of all assets in a facility. It integrates various maintenance approaches to create a system-specific strategy that ensures efficient plant operation.
Why is RCM considered the world-class maintenance approach?
-RCM is regarded as world-class because it balances preventive, reactive, and predictive maintenance strategies. It ensures that maintenance efforts are efficient and cost-effective while minimizing unplanned downtime and costly failures.
What are the three main steps in effective RCM implementation?
-The three main steps are: 1) Preserve equipment functionality by establishing equipment criticality levels. 2) Identify and prioritize failure modes for each piece of equipment. 3) Implement RCM by selecting the right maintenance approaches based on equipment criticality and failure analysis.
What is the importance of finding a 'sweet spot' in preventive maintenance?
-The 'sweet spot' in preventive maintenance refers to doing just the right amount of maintenance. Too little maintenance can result in unplanned repairs, while too much can lead to induced failures or unnecessary costs.
What are the key factors to consider when determining equipment criticality?
-The key factors include: 1) Safety risks, 2) Environmental impact, 3) Production stoppages, 4) Maintenance expenses, 5) System-wide effects, and 6) Redundancy within the system.
How does Failure Modes and Effects Analysis (FMEA) contribute to RCM?
-FMEA helps identify potential failure modes for each component, understand the underlying causes, and determine the likelihood and impact of those failures. This analysis guides the selection of appropriate maintenance strategies for each piece of equipment.
What is the difference between reactive, preventive, and predictive maintenance?
-Reactive maintenance involves fixing equipment after it breaks. Preventive maintenance schedules regular checks to avoid breakdowns. Predictive maintenance uses technology to monitor equipment performance in real-time and detect issues before they cause failures.
Why is safety the top priority in equipment criticality analysis?
-Safety is prioritized because equipment failures can lead to severe consequences, including loss of life or serious injuries. Ensuring safe operations prevents catastrophic incidents and maintains a safe working environment.
What role does ABB’s Service Pro play in supporting RCM?
-ABB's Service Pro helps customers manage their maintenance processes by providing a computerized maintenance management system (CMMS). It includes preventive maintenance routines, criticality analysis, and benchmarking tools to optimize asset management.
How does ABB's advanced services powered by Service Port assist in RCM?
-ABB’s advanced services use real-time data from systems like Harmony control and quality control systems to identify and prioritize maintenance needs. This data-driven approach supports reliability-centered maintenance by enabling proactive decision-making.
Outlines
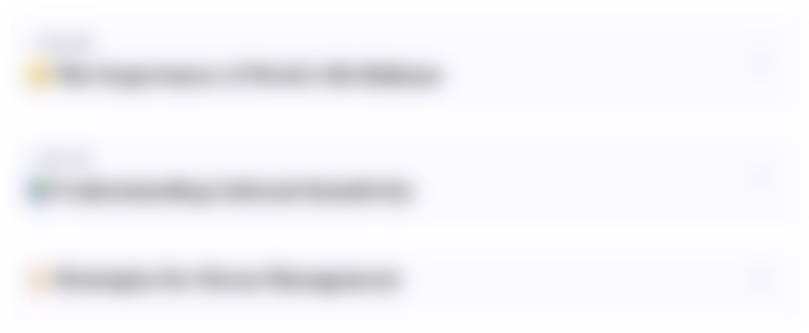
Esta sección está disponible solo para usuarios con suscripción. Por favor, mejora tu plan para acceder a esta parte.
Mejorar ahoraMindmap
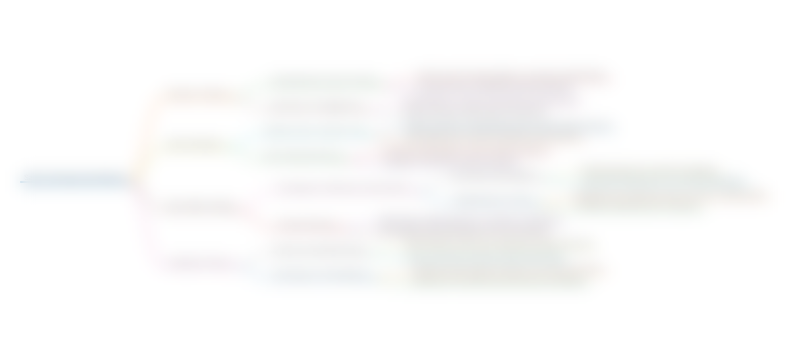
Esta sección está disponible solo para usuarios con suscripción. Por favor, mejora tu plan para acceder a esta parte.
Mejorar ahoraKeywords
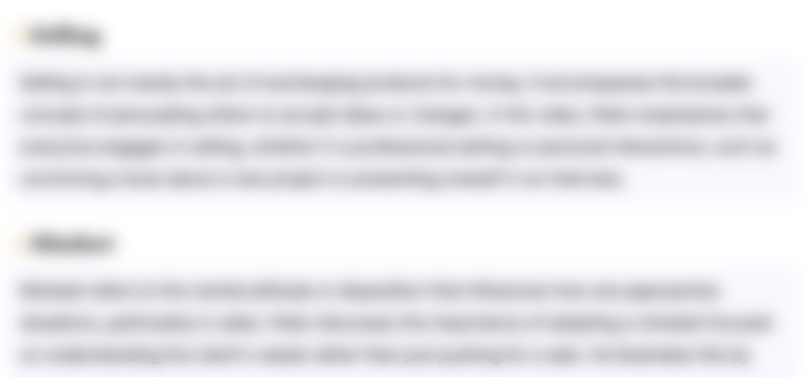
Esta sección está disponible solo para usuarios con suscripción. Por favor, mejora tu plan para acceder a esta parte.
Mejorar ahoraHighlights
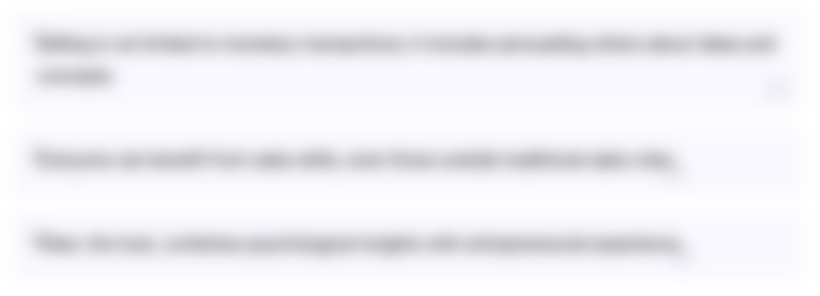
Esta sección está disponible solo para usuarios con suscripción. Por favor, mejora tu plan para acceder a esta parte.
Mejorar ahoraTranscripts
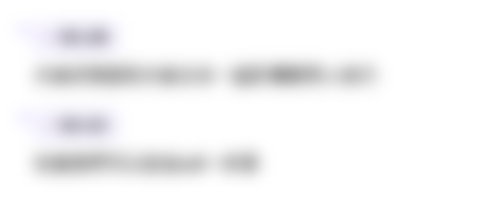
Esta sección está disponible solo para usuarios con suscripción. Por favor, mejora tu plan para acceder a esta parte.
Mejorar ahoraVer Más Videos Relacionados
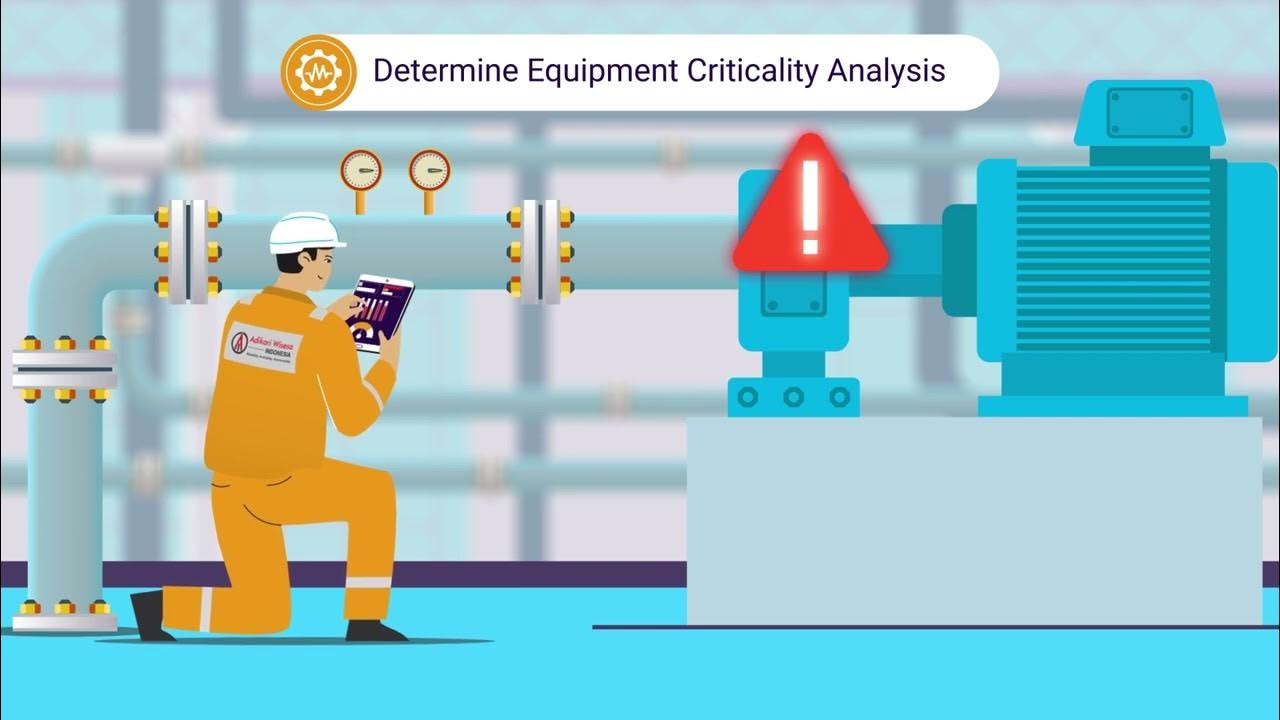
Reliability Center Maintenance by Adikari Wisesa Indonesia
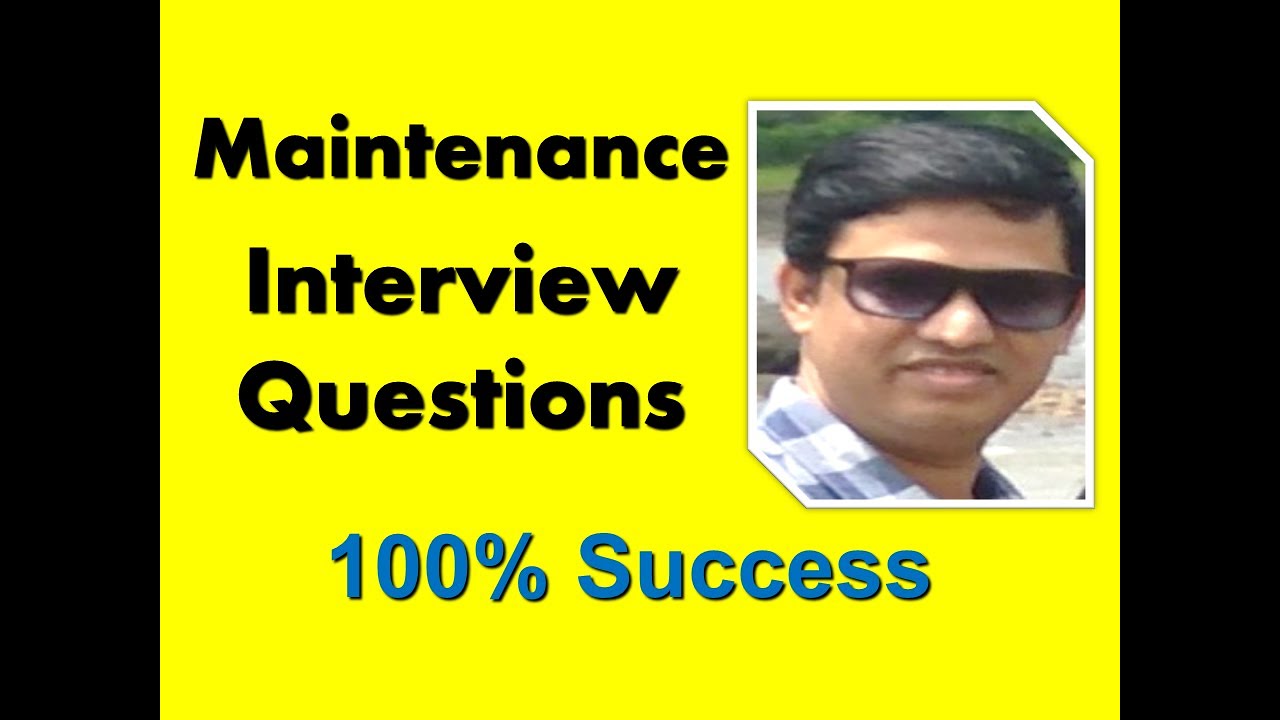
Interview Questions for Maintenance Engineers

WHAT IS A CMMS ? Computerized Maintenance Management System

What is TPM -Total Productive Maintenance ? | 8 TPM pillars Total Productive Maintenance

Exploring Different Types of Machine Sensors in Manufacturing: Uses, Pros & Cons
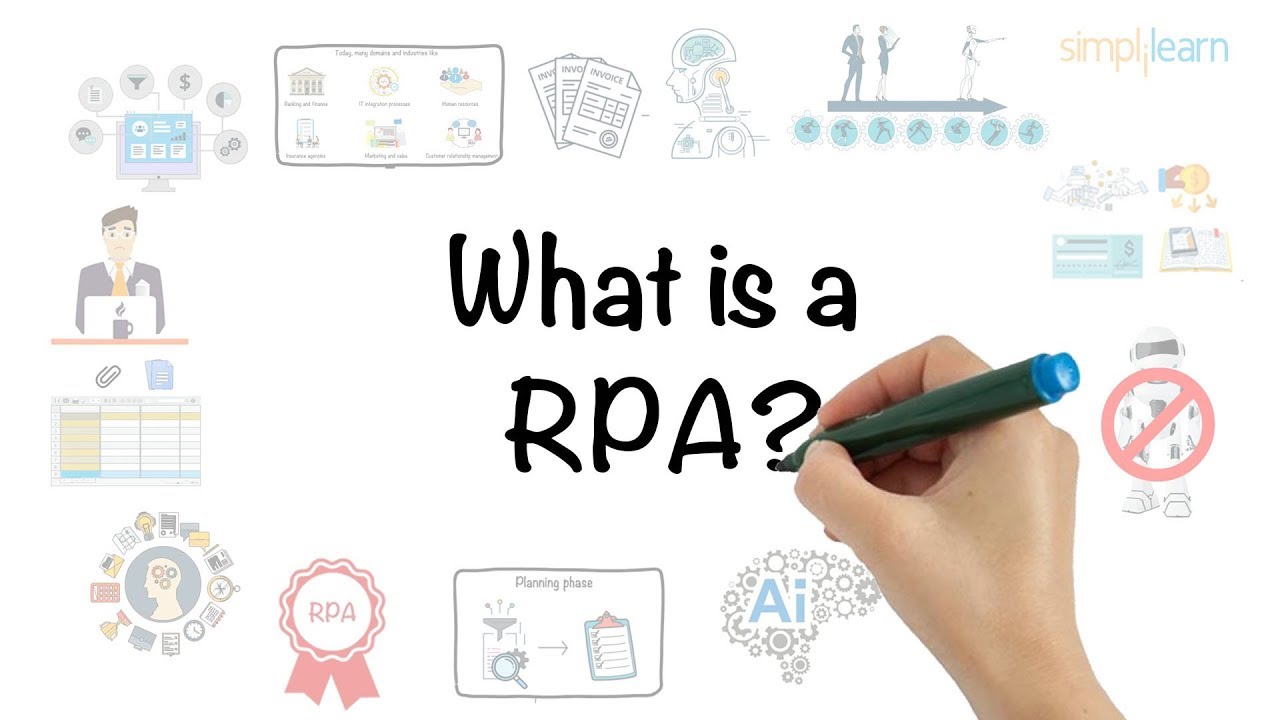
RPA In 5 Minutes | What Is RPA - Robotic Process Automation? | RPA Explained | Simplilearn
5.0 / 5 (0 votes)