Vibration Analysis Focusing on the Spectrum (Remastered)
Summary
TLDR本视频脚本为观众提供了一次关于振动分析的深入讨论。主讲人介绍了振动监测的基本理论,包括如何测量和分析机器的振动信号,以及如何通过振动的频率和幅度来诊断机器的健康状况。通过案例研究,展示了振动分析在监测和预测机械故障方面的实际应用,强调了识别机器故障信号的重要性,并解释了如何利用这些信号来提高设备的可靠性和性能。
Takeaways
- 📈 振动分析是一种监测机器健康状态的有效工具,通过测量振动信号来识别机器中的潜在问题。
- 🔍 机器通过振动信号而非语言与我们沟通,振动监测可以帮助我们理解机器的运行状况。
- 📊 振动监测可以测量信号的高度和持续时间,从而识别机器中具体部件的问题。
- 🔨 机器的振动可能与电气、机械或过程相关,振动监测能够区分这些不同的信号来源。
- 🌡️ 振动测量需要考虑机器的力和运动,包括机器的对齐情况和振动速率。
- 🔄 机器的不同部件,如叶片、螺丝压缩机或齿轮,会产生独特的“心跳”模式,即振动信号。
- 📉 振动信号的波形复杂,但可以通过傅里叶变换等数学方法简化为频率谱,便于分析。
- 📌 频率谱中的峰值可以指示机器问题的性质,如不平衡、轴承损坏或其他机械故障。
- ⚙️ 振动监测不仅关注振动的幅度,更关注幅度的变化趋势,以识别机器状态的变化。
- 🛠️ 通过案例研究,展示了振动监测在实际应用中如何帮助诊断和修复机器故障。
- 🔧 振动分析需要结合专业知识和经验,以正确解释数据并采取适当的维护措施。
Q & A
振动分析是什么,它在机器监测中扮演什么角色?
-振动分析是一种监测和分析机器振动信号的技术,用于评估机器的运行状况和预测潜在故障。在机器监测中,振动分析帮助我们通过测量和分析振动信号来理解机器的“语言”,从而提前发现问题并采取措施。
为什么机器会产生振动信号?
-机器在运行过程中,由于机械、电气或过程等方面的问题,会产生振动。例如,机器的不对中、轴承损坏或者叶片不平衡等问题都会导致振动,这些振动信号可以被传感器捕捉并分析,以确定机器的健康状况。
振动监测中测量的信号有哪些特点?
-振动监测中测量的信号特点包括信号的高度、持续时间以及频率。信号的高度可以反映振动的强度,持续时间可以帮助我们理解每个事件的长短,而频率则可以揭示机器中哪个部件可能存在问题。
什么是机器的“心跳”信号,它如何帮助我们识别问题?
-机器的“心跳”信号是指机器在正常或异常运行状态下产生的特定频率的振动模式。通过分析这些模式,我们可以识别机器的特定部件是否存在问题,例如齿轮的缺陷、轴承的损坏等,从而实现对机器健康状况的跟踪和诊断。
为什么需要考虑机器的对中和运动对振动监测的影响?
-机器的对中和运动直接影响振动信号的特性。如果机器不对中,会导致额外的力和振动,可能会损坏轴和轴承。了解机器的运动和振动速率有助于我们更准确地诊断问题,比如通过分析振动的频率和幅度来确定故障的类型和位置。
在振动分析中,频率分析的作用是什么?
-频率分析是将复杂的时间波形信号转换为频率域,以揭示信号中不同频率成分的强度。这有助于识别和量化机器中的特定问题,如不平衡、轴承损坏等,因为这些问题会在特定的频率上产生特征峰值。
什么是振动信号中的谐波和边带,它们如何帮助诊断问题?
-谐波是基本频率的整数倍频率,而边带是位于中心频率两侧的等间隔的频率峰值。它们通常与机器中的非线性问题或松动部件有关。通过分析谐波和边带的分布和间距,可以提供关于机器故障性质和位置的重要线索。
为什么振动监测需要定期进行,而不仅仅是在机器启动时?
-定期进行振动监测可以追踪机器的运行趋势和健康状况的变化。机器可能在运行过程中逐渐出现问题,如磨损或损坏,这些问题可能不会立即显现,但通过定期监测可以及时发现并采取措施,避免更严重的故障发生。
在实际案例中,振动监测如何帮助识别和解决轴承问题?
-在实际案例中,通过监测轴承的振动信号,可以发现异常的频率峰值,如谐波和边带,这些特征表明轴承可能存在问题。通过进一步分析这些峰值的频率和间距,可以确定故障的具体类型,如内圈、外圈或滚动元件的损坏,并据此进行维修或更换。
振动监测在旋转设备上的应用有哪些局限性?
-虽然振动监测是一种强大的工具,但它也有局限性。例如,它可能无法检测到所有类型的故障,特别是那些不产生显著振动信号的问题。此外,振动监测需要专业知识来正确解释数据,而且可能需要与其他监测技术结合使用,以获得更全面的机器健康状况评估。
Outlines
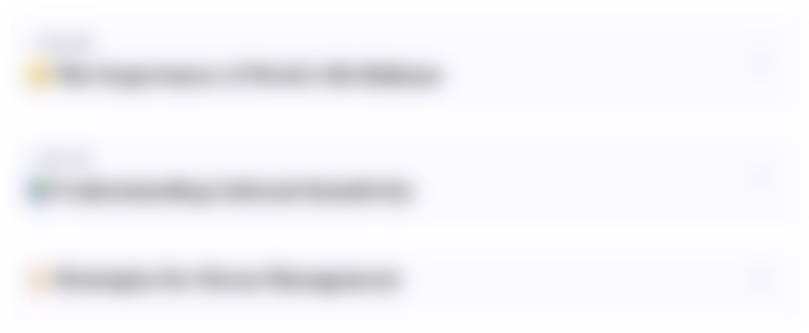
Esta sección está disponible solo para usuarios con suscripción. Por favor, mejora tu plan para acceder a esta parte.
Mejorar ahoraMindmap
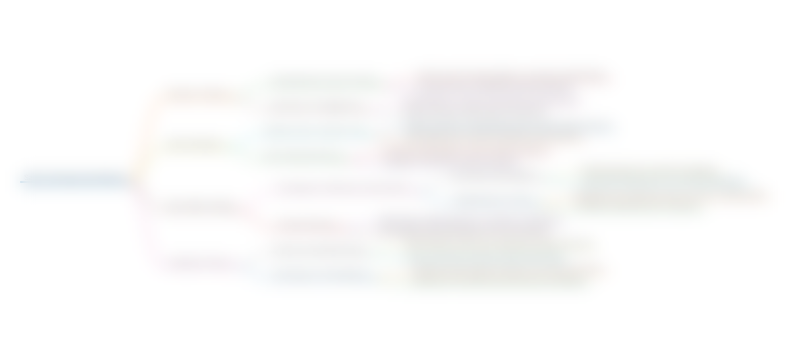
Esta sección está disponible solo para usuarios con suscripción. Por favor, mejora tu plan para acceder a esta parte.
Mejorar ahoraKeywords
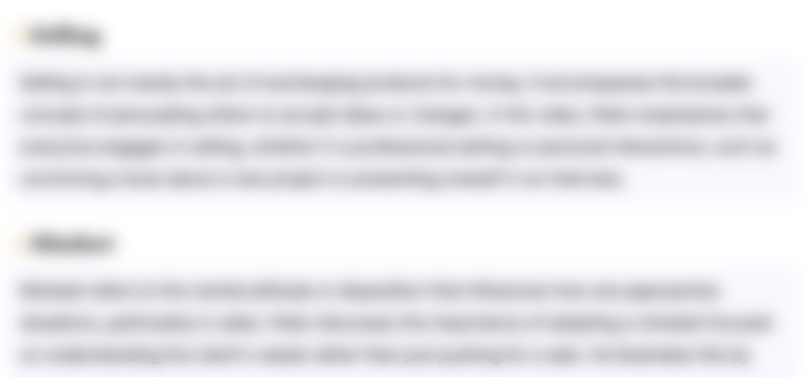
Esta sección está disponible solo para usuarios con suscripción. Por favor, mejora tu plan para acceder a esta parte.
Mejorar ahoraHighlights
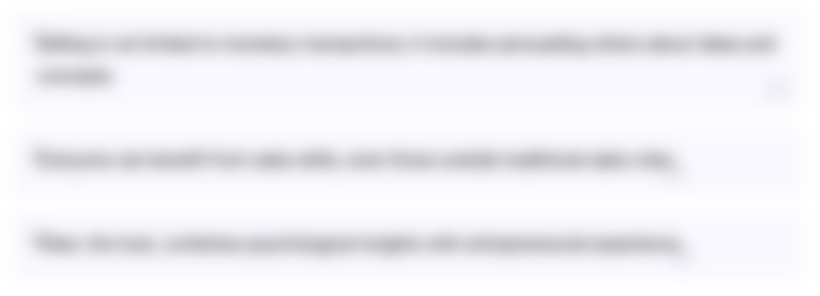
Esta sección está disponible solo para usuarios con suscripción. Por favor, mejora tu plan para acceder a esta parte.
Mejorar ahoraTranscripts
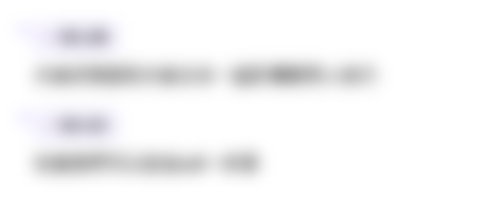
Esta sección está disponible solo para usuarios con suscripción. Por favor, mejora tu plan para acceder a esta parte.
Mejorar ahoraVer Más Videos Relacionados
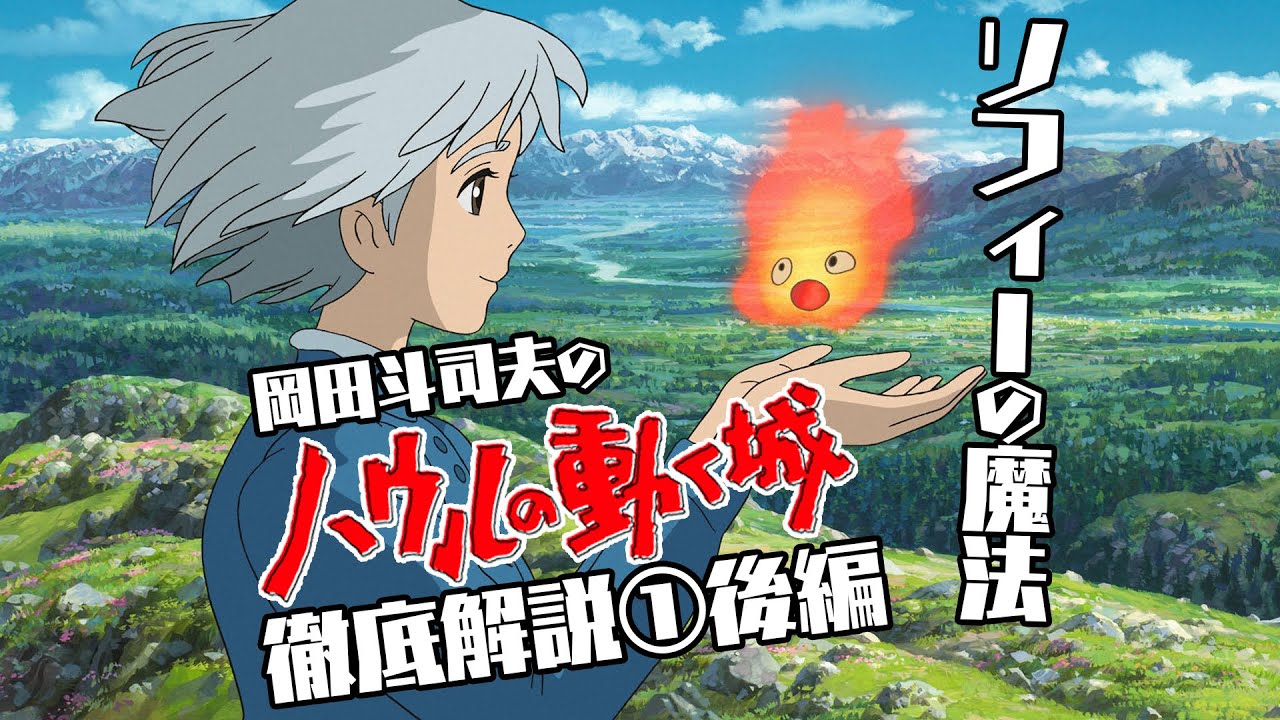
【UG# 243】『ハウルの動く城』徹底解説 第1回後編 ~ ストーリーを裏側から読み解く 4月はジブリ特集④ / OTAKING explains "Howl's Moving Castle"
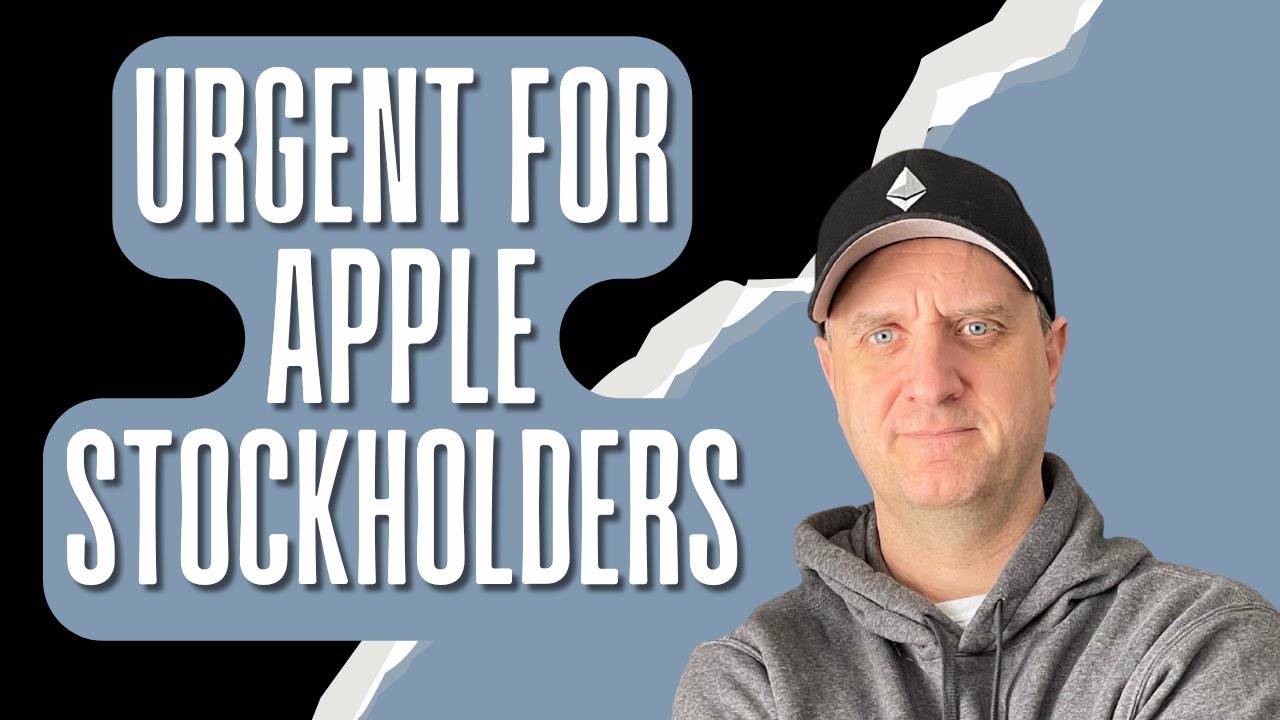
🔥🔥MASSIVE APPLE STOCK PRICE PREDICTION NEWS! YOU NEED TO SEE THIS RIGHT AWAY!
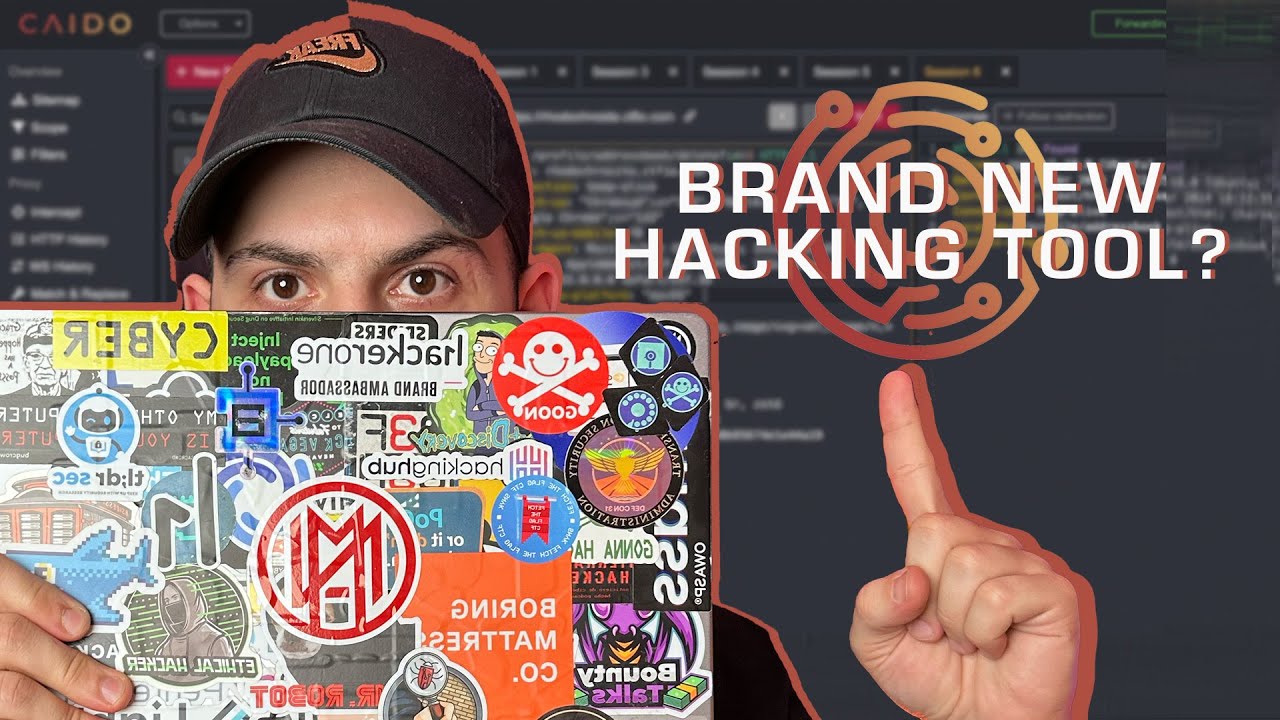
Will This New Hacking Tool Replace BurpSuite?
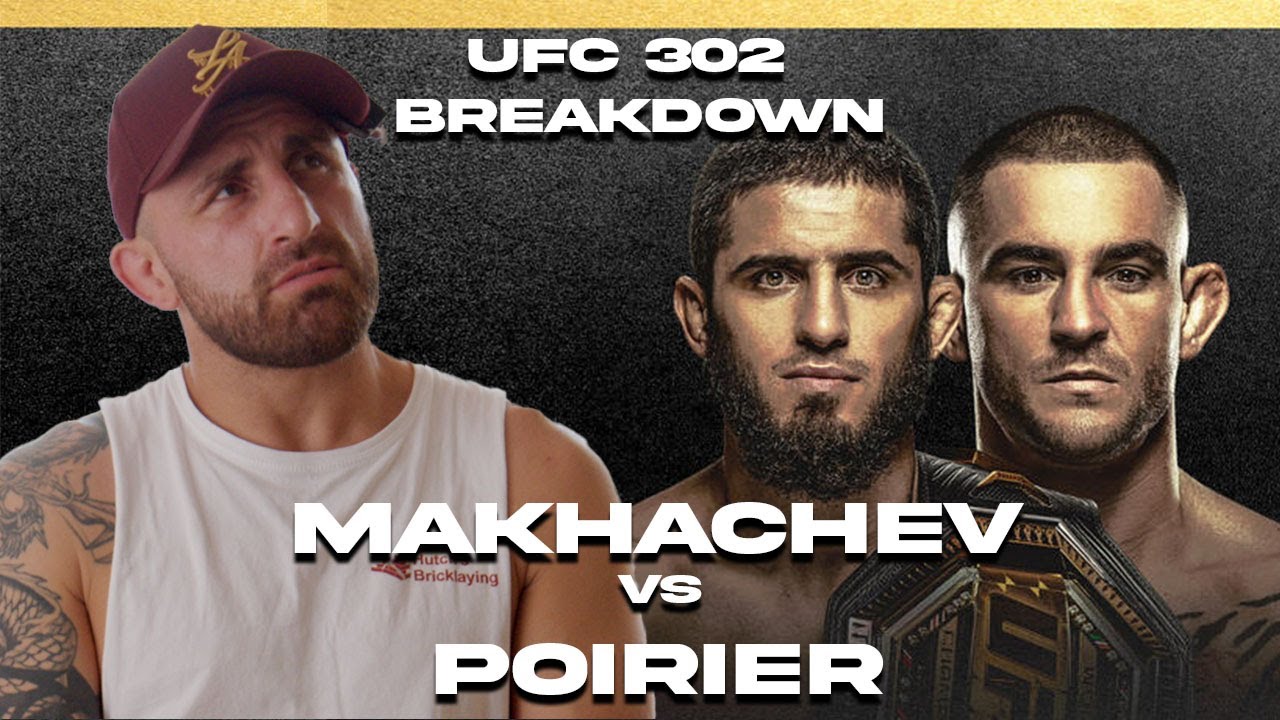
In Depth Breakdown of UFC 302 With Alex Volkanovski

Case Interview: Essential Tips and Tricks (Part 12 of 12) | caseinterview

【原神】結局どのパーティーが1番最強!?七星召喚において多かったこの質問について徹底解説!そして最強デッキも紹介だ!!!
5.0 / 5 (0 votes)