How 7 Companies Mastered TPM (Total Productive Maintenance)
Summary
TLDRThis video highlights the power of Total Productive Maintenance (TPM) as a transformative strategy for manufacturing efficiency. Carlos Amidio explains how TPM empowers employees at all levels, from operators to executives, to actively maintain equipment and prevent issues before they arise. Using examples from Toyota, Nissan, Procter & Gamble, Nestle, 3M, and Unilever, the video demonstrates how TPM boosts productivity, reduces downtime, and slashes maintenance costs. At its core, TPM fosters a culture of ownership and continuous improvement, driving both operational success and employee satisfaction.
Takeaways
- đ TPM (Total Productive Maintenance) is a philosophy, not just a tool or software. It's about getting everyone, from factory workers to executives, involved in improving equipment productivity.
- đ Toyota successfully implemented TPM by empowering operators to perform basic maintenance, reducing equipment breakdowns by 70% and boosting productivity by 30%.
- đ TPM is scalable and can be applied by businesses of all sizes, not just large manufacturers like Toyota and Nissan.
- đ Nissan reduced machine downtime by 50% through preventive maintenance, condition monitoring, and empowering operators to take action on minor issues.
- đ Procter & Gamble (PNG) reduced maintenance costs by 30% by shifting to preventive maintenance, resulting in a 25% increase in equipment uptime.
- đ NestlĂ© implemented TPM to improve their Overall Equipment Effectiveness (OEE), achieving a 15% increase in OEE and a 40% reduction in unscheduled downtime.
- đ 3M reduced production lead times by 20% and improved productivity by 25% by using visual management and standardized work practices as part of their TPM implementation.
- đ Unilever cut maintenance costs by 35% through preventive and condition-based maintenance strategies, while also improving product quality by 20%.
- đ TPM is not just about improving machinery but also about empowering employees, fostering a sense of ownership, and creating a culture of continuous improvement.
- đ TPM can reduce stress, increase efficiency, and make jobs more rewarding by allowing workers to focus on preventing issues before they occur, rather than constantly fixing breakdowns.
Q & A
What is Total Productive Maintenance (TPM)?
-Total Productive Maintenance (TPM) is a philosophy that aims to maximize productivity by involving everyone in the organization, from factory floor workers to top management, in maintaining equipment and preventing breakdowns. It focuses on both preventive maintenance and continuous improvement.
How did Toyota benefit from implementing TPM?
-Toyota reduced equipment breakdowns by 70% and increased productivity by 30% after implementing TPM. By empowering operators to perform basic maintenance and address issues proactively, Toyota achieved significant efficiency gains.
Can TPM be used by small businesses or only large manufacturers?
-TPM is a scalable system that can benefit businesses of all sizes, from small machine shops to large production facilities. It helps improve equipment utilization and boosts overall business efficiency.
How did Nissan apply TPM to improve their operations?
-Nissan focused on reducing machine downtime by implementing preventive maintenance, condition monitoring, and early problem detection. As a result, they cut downtime by 50% and increased production efficiency by 20%.
What role does preventive maintenance play in TPM?
-Preventive maintenance is central to TPM, as it involves identifying potential issues before they occur and taking steps to prevent them. This approach helps maintain equipment health, reduces unplanned downtime, and improves operational efficiency.
How did Procter & Gamble (P&G) use TPM to reduce maintenance costs?
-P&G shifted from reactive maintenance to preventive maintenance with TPM, enabling them to reduce maintenance costs by 30%. By proactively identifying issues before they became major problems, they extended the lifespan of their equipment.
What is Overall Equipment Effectiveness (OEE), and why is it important for Nestlé?
-Overall Equipment Effectiveness (OEE) is a metric used to measure how well equipment is performing, considering factors like availability, performance, and quality. Nestlé aimed to improve OEE as part of their TPM program to enhance productivity and reduce unscheduled downtime.
What improvements did Nestlé see after implementing TPM?
-Nestlé saw a 15% increase in OEE and a 40% reduction in unscheduled downtime. These improvements allowed them to get more value from their equipment and increase production efficiency.
How did 3M use TPM to streamline their production process?
-3M focused on reducing production lead times by implementing visual management and standardized work. These practices helped identify bottlenecks, reduce delays, and ultimately increase productivity by 25%.
What impact did TPM have on employee morale and ownership?
-TPM empowered employees by giving them ownership of their equipment and encouraging them to take proactive steps in maintenance. This increased job satisfaction, reduced stress, and fostered a culture of continuous improvement.
Outlines
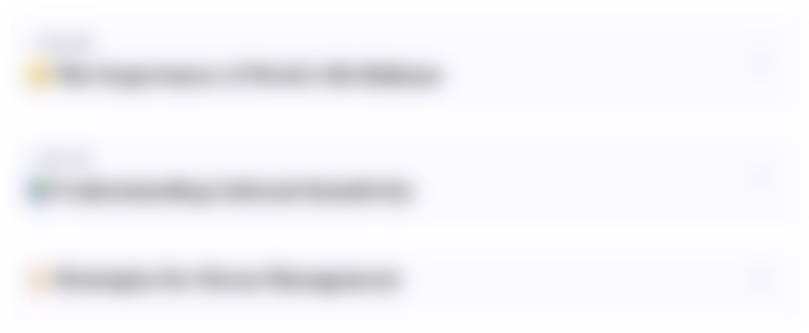
Dieser Bereich ist nur fĂŒr Premium-Benutzer verfĂŒgbar. Bitte fĂŒhren Sie ein Upgrade durch, um auf diesen Abschnitt zuzugreifen.
Upgrade durchfĂŒhrenMindmap
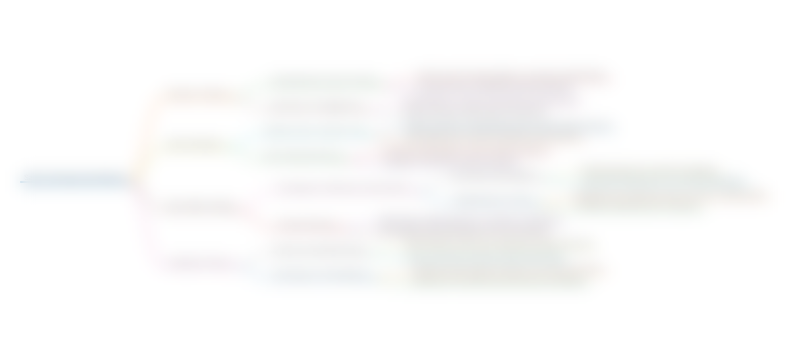
Dieser Bereich ist nur fĂŒr Premium-Benutzer verfĂŒgbar. Bitte fĂŒhren Sie ein Upgrade durch, um auf diesen Abschnitt zuzugreifen.
Upgrade durchfĂŒhrenKeywords
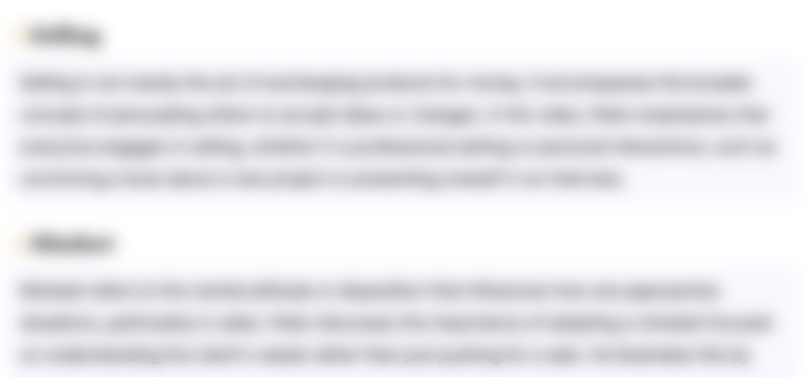
Dieser Bereich ist nur fĂŒr Premium-Benutzer verfĂŒgbar. Bitte fĂŒhren Sie ein Upgrade durch, um auf diesen Abschnitt zuzugreifen.
Upgrade durchfĂŒhrenHighlights
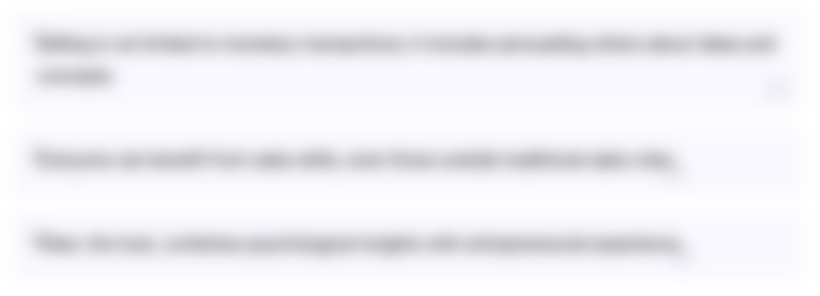
Dieser Bereich ist nur fĂŒr Premium-Benutzer verfĂŒgbar. Bitte fĂŒhren Sie ein Upgrade durch, um auf diesen Abschnitt zuzugreifen.
Upgrade durchfĂŒhrenTranscripts
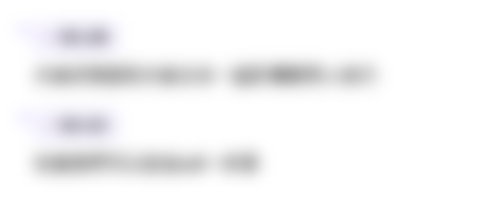
Dieser Bereich ist nur fĂŒr Premium-Benutzer verfĂŒgbar. Bitte fĂŒhren Sie ein Upgrade durch, um auf diesen Abschnitt zuzugreifen.
Upgrade durchfĂŒhrenWeitere Ă€hnliche Videos ansehen

Four Principles â Lean Manufacturing & TPM

What is TPM -Total Productive Maintenance ? | 8 TPM pillars Total Productive Maintenance
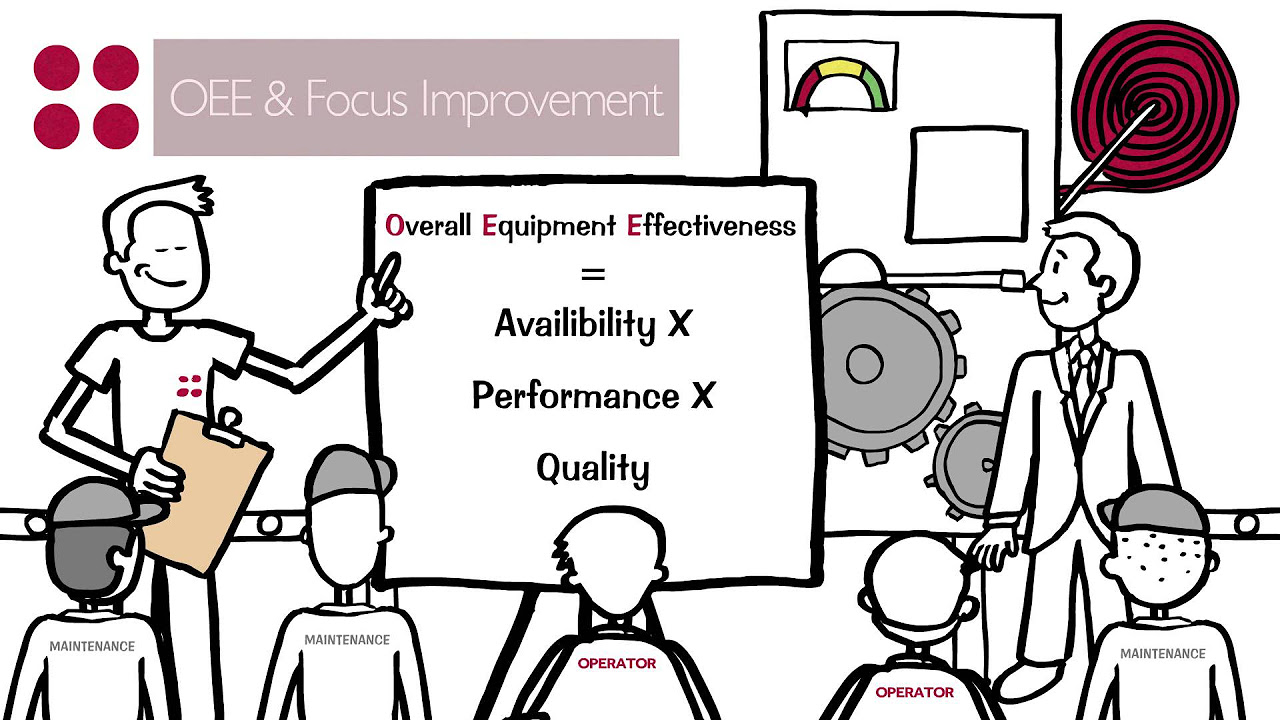
Four Principles TPM
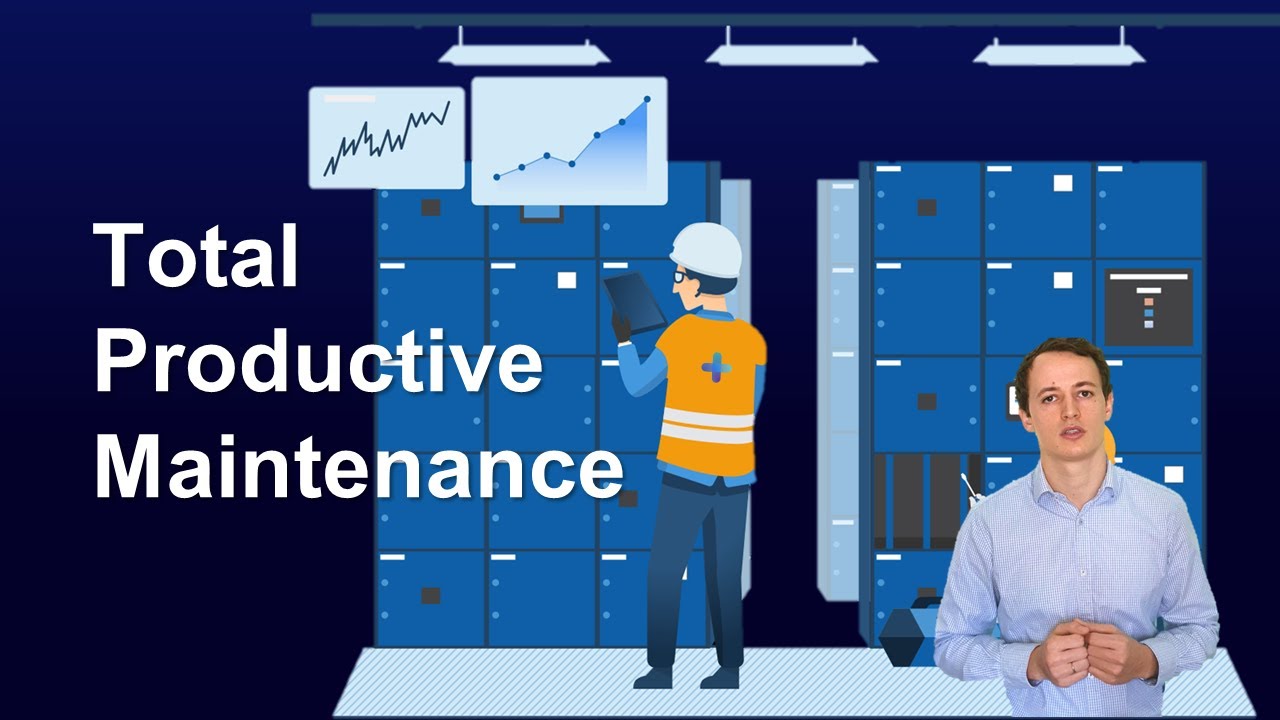
#22 Free Lean Six Sigma Green Belt | Total Productive Maintenance (TPM)
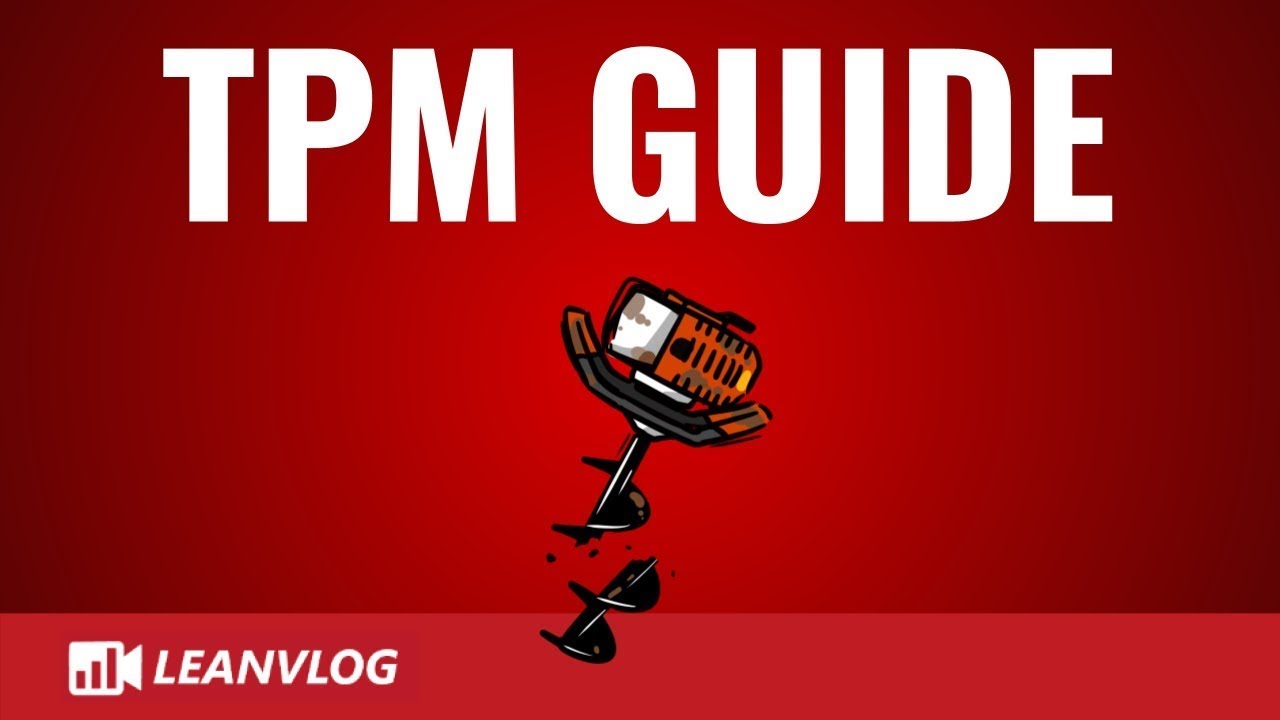
What is Total Productive Maintenance | 8 Pillars of TPM | 6 Big Losses | Type of Maintenance
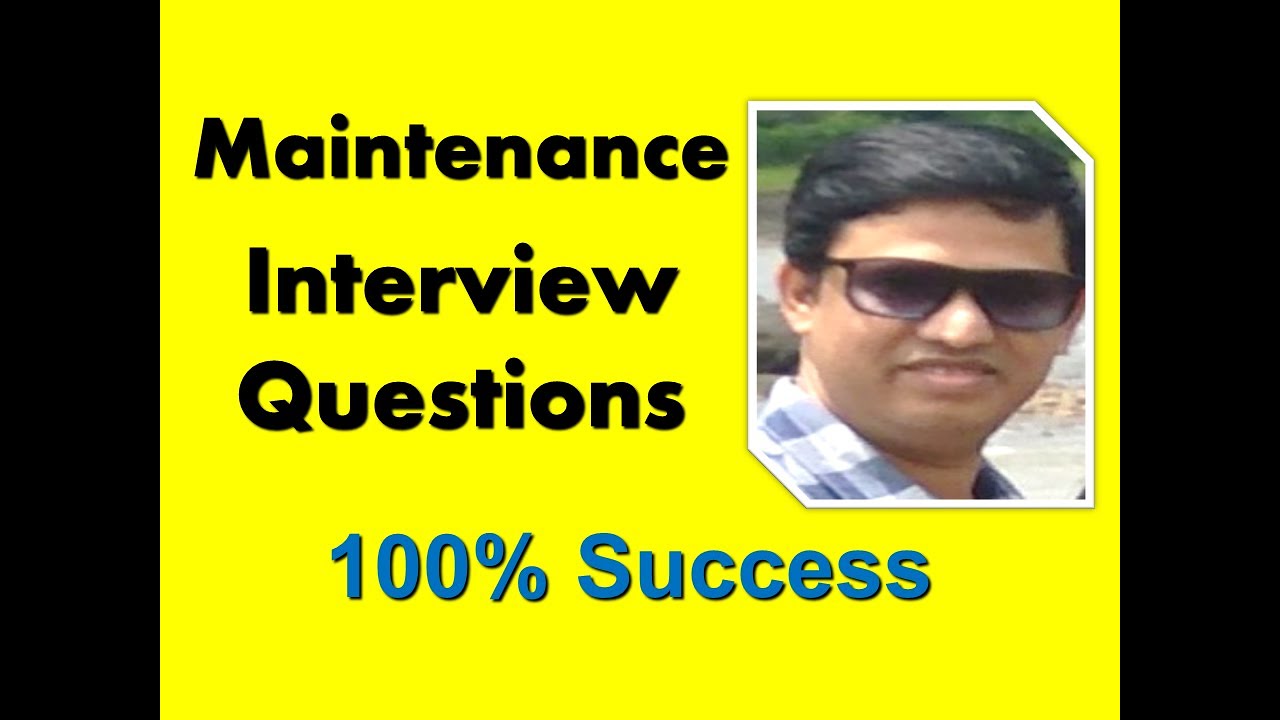
Interview Questions for Maintenance Engineers
5.0 / 5 (0 votes)