What Is Die Casting? Understand the Most Efficiency Metal Casting Process
Summary
TLDRDie casting is a manufacturing process where metal alloys are melted and injected into molds under high pressure to create complex parts. There are two primary methods: hot chamber and cold chamber die casting, each suitable for different material types based on their melting points. The process offers several advantages, including high production rates, long tool life, and the ability to create smooth, textured parts. However, it can be costly for small-scale production due to the high tooling costs. Overall, die casting is ideal for high-volume production, benefiting both manufacturers and consumers by reducing production costs and ensuring uniformity in part design.
Takeaways
- 😀 Die casting is a process that melts metal alloys and forces them into molds under high pressure and speed to create complex parts.
- 😀 There are two types of die-casting processes: hot chamber and cold chamber, each suited for different materials.
- 😀 Hot chamber die casting is ideal for low melting point alloys like zinc, tin, lead, and magnesium.
- 😀 Cold chamber die casting is best for high melting point alloys like aluminum, as it prevents damage to machine components.
- 😀 Die casting tools are made from high-quality steel to withstand extreme thermal and mechanical conditions.
- 😀 Molds for zinc die-casting can last between 500,000 to 2 million cycles, making the process cost-effective for mass production.
- 😀 Die casting allows for the production of large quantities of parts quickly, reducing production costs significantly.
- 😀 The die-casting process typically produces parts with smooth or textured surfaces, making further finishing easier.
- 😀 While die casting is efficient for high-volume production, it can be expensive for small-scale projects due to high tooling costs.
- 😀 Die casting ensures consistency in mass production, with parts adhering to the same design specifications across large quantities.
- 😀 Die casting reduces production costs and impacts the final product's price, benefiting both manufacturers and consumers.
Q & A
What is the die casting process?
-Die casting is a process in which non-ferrous metal alloys are melted and injected into a mold cavity under high pressure and at high speed to quickly manufacture complex metal parts.
What are the two types of die casting processes?
-The two types of die casting processes are hot chamber die casting and cold chamber die casting.
How does the hot chamber die casting process work?
-In hot chamber die casting, the metal is melted and injected into the mold using pressure from a hydraulic system. It is ideal for low-melting-point materials such as zinc, tin, lead, and magnesium alloys.
Why is hot chamber die casting unsuitable for high-melting-point alloys?
-Hot chamber die casting is unsuitable for high-melting-point alloys because they can damage components such as the gooseneck and nozzle due to the high temperatures involved.
How does cold chamber die casting differ from hot chamber die casting?
-Cold chamber die casting involves ladling the melted material from a furnace into a cold chamber through a pouring hole. It works with horizontal partition and does not include a gooseneck, making it suitable for high-melting-point materials like aluminum.
What are the main advantages of die casting?
-Some advantages of die casting include the ability to produce parts quickly with high precision, durability of the molds, and the production of parts with smooth or textured surfaces.
How long do die-casting molds typically last?
-Die-casting molds made from high-quality steel can last between 500,000 and 2 million cycles, depending on the material and the usage.
Why is die casting cost-effective for large-scale production?
-Die casting is cost-effective for large-scale production because it allows for the production of a large number of parts with minimal additional cost per part, significantly reducing production costs.
What are the challenges associated with die casting for small-scale production?
-Die casting can be expensive for small-scale production due to the high tooling costs, making it less cost-effective for producing fewer parts.
How does die casting benefit both manufacturers and consumers?
-Die casting benefits manufacturers by enabling the production of millions of identical parts efficiently, while consumers benefit from lower prices due to reduced production costs.
Outlines
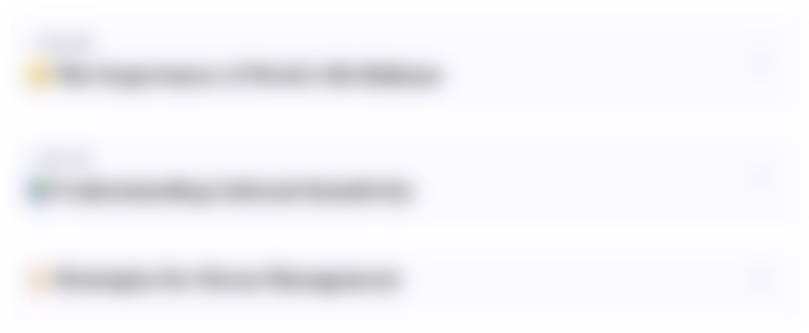
Dieser Bereich ist nur für Premium-Benutzer verfügbar. Bitte führen Sie ein Upgrade durch, um auf diesen Abschnitt zuzugreifen.
Upgrade durchführenMindmap
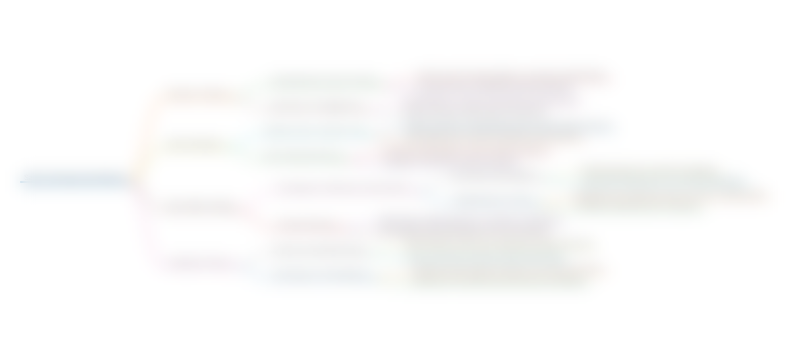
Dieser Bereich ist nur für Premium-Benutzer verfügbar. Bitte führen Sie ein Upgrade durch, um auf diesen Abschnitt zuzugreifen.
Upgrade durchführenKeywords
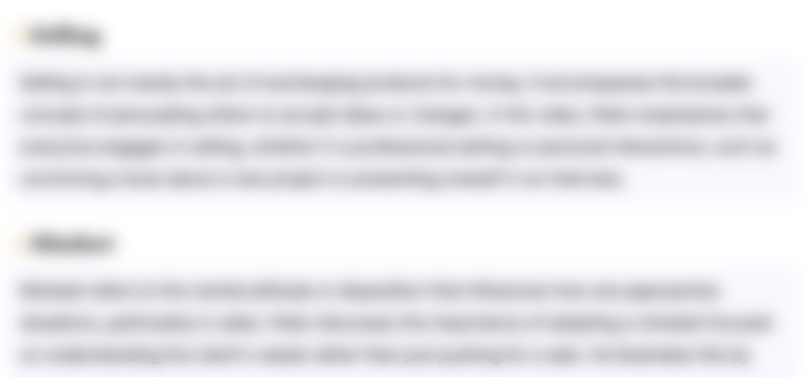
Dieser Bereich ist nur für Premium-Benutzer verfügbar. Bitte führen Sie ein Upgrade durch, um auf diesen Abschnitt zuzugreifen.
Upgrade durchführenHighlights
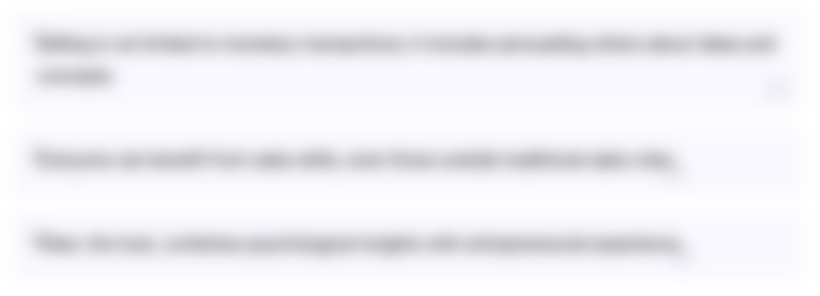
Dieser Bereich ist nur für Premium-Benutzer verfügbar. Bitte führen Sie ein Upgrade durch, um auf diesen Abschnitt zuzugreifen.
Upgrade durchführenTranscripts
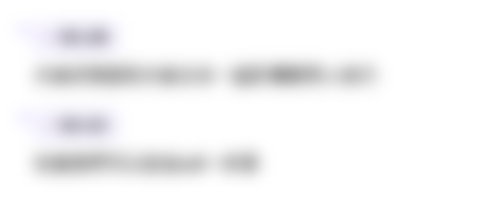
Dieser Bereich ist nur für Premium-Benutzer verfügbar. Bitte führen Sie ein Upgrade durch, um auf diesen Abschnitt zuzugreifen.
Upgrade durchführen5.0 / 5 (0 votes)