How Plastic Products are Made | The Injection Molding Process
Summary
TLDRIn this video, Tristan gives a detailed walkthrough of the injection molding process at Plascon Plastics in Delta, BC. He explains how small plastic pellets are fed into the machine, melted into molten plastic, and then injected into molds using a reciprocating screw. The process includes cooling, product separation, and finishing touches like removing runners from molded items. Tristan also highlights the automated system that transfers finished products to the conveyor belt, offering viewers a closer look at the complex process behind plastic manufacturing. For more information, viewers are encouraged to contact Plascon Plastics.
Takeaways
- 😀 The video introduces the injection molding process at Plascon Plastics, located in Delta, BC.
- 😀 The process begins with small plastic pellets, which are sucked into the hopper to feed into the machine.
- 😀 The plastic pellets resemble grains of rice, and their color corresponds to the final product's color.
- 😀 In some cases, color is added directly in the hopper during the process.
- 😀 The pellets are melted into molten plastic using heat from bands surrounding a reciprocating screw.
- 😀 The screw's turning and friction help melt the plastic as it moves forward along the shaft.
- 😀 Once melted, the molten plastic is forced into the mold by the plunger at the tip of the screw.
- 😀 The mold cavity is filled with molten plastic, and air escapes through small vents in the mold.
- 😀 The molten plastic cools inside the mold with the help of water or coolant before solidifying.
- 😀 A mechanical arm retrieves the molded product and places it on a conveyor belt for further processing.
- 😀 In some cases, multiple smaller products are produced in one mold using interconnected runners, which are later removed from the final product.
Q & A
What is the first step in the injection molding process?
-The first step involves feeding plastic pellets into a tube that carries them to the hopper, which is responsible for feeding the pellets into the reciprocating screw.
What are the plastic pellets made of, and how do they vary?
-The plastic pellets are small, grain-like pieces that vary in color depending on the product. The color of the pellets typically matches the product color, and in some cases, additional color is added at the hopper.
How does the reciprocating screw work in the molding process?
-The reciprocating screw moves the plastic pellets forward through heating bands, melting them due to the heat and friction, turning them into molten plastic. The screw then pushes the molten plastic towards the mold.
What role do the heating bands play in the process?
-The heating bands are responsible for heating the plastic pellets to a high temperature, turning them into molten liquid plastic, which is essential for the molding process.
What happens after the molten plastic reaches the tip of the reciprocating screw?
-Once the molten plastic reaches the tip of the screw, the plunger pulls back and shoots forward, forcing the molten plastic into the mold cavity.
What is the purpose of the mold cavity in the injection molding process?
-The mold cavity is where the molten plastic is injected. It takes the shape of the product being made, and once filled, it cools and hardens to form the final product.
How does the air escape from the mold during the injection process?
-Air escapes through tiny channels called vents in the mold, allowing the molten plastic to fill the cavity completely.
What happens to the plastic after it fills the mold cavity?
-After the molten plastic fills the mold cavity, it cools down with the help of water or coolant, and then it separates from the mold.
How is the finished product removed from the mold?
-A mechanical arm comes down and lifts the finished product out of the mold for further processing or packaging.
What are runners, and what happens to them after the molding process?
-Runners are channels in the mold that connect multiple parts of a product. After the molding process, the runners are cut off and separated from the finished product.
Outlines
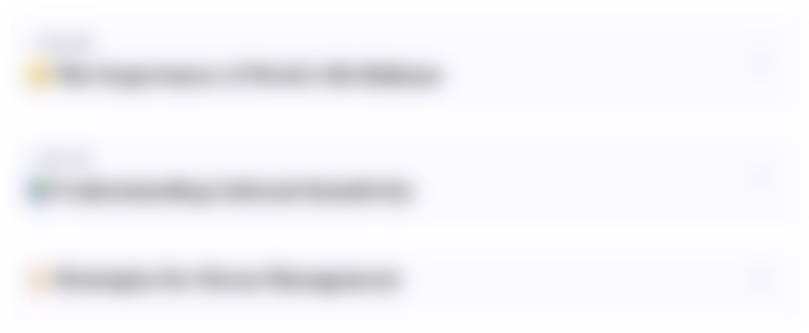
Dieser Bereich ist nur für Premium-Benutzer verfügbar. Bitte führen Sie ein Upgrade durch, um auf diesen Abschnitt zuzugreifen.
Upgrade durchführenMindmap
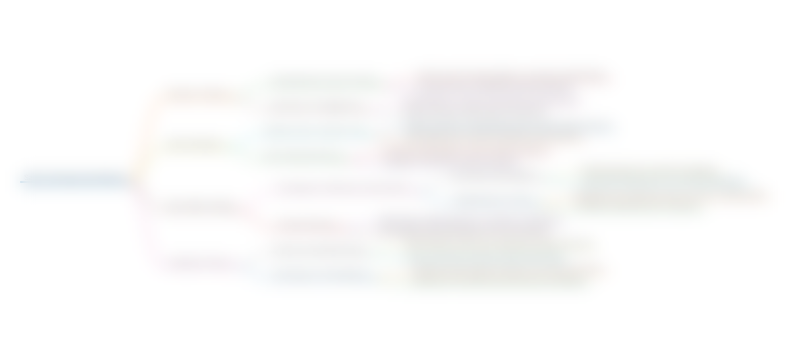
Dieser Bereich ist nur für Premium-Benutzer verfügbar. Bitte führen Sie ein Upgrade durch, um auf diesen Abschnitt zuzugreifen.
Upgrade durchführenKeywords
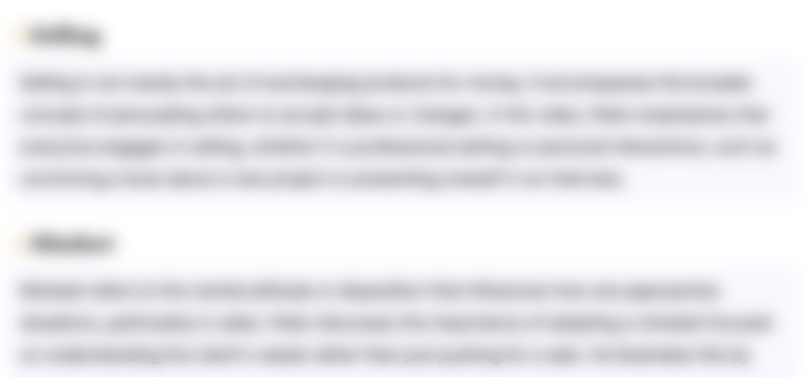
Dieser Bereich ist nur für Premium-Benutzer verfügbar. Bitte führen Sie ein Upgrade durch, um auf diesen Abschnitt zuzugreifen.
Upgrade durchführenHighlights
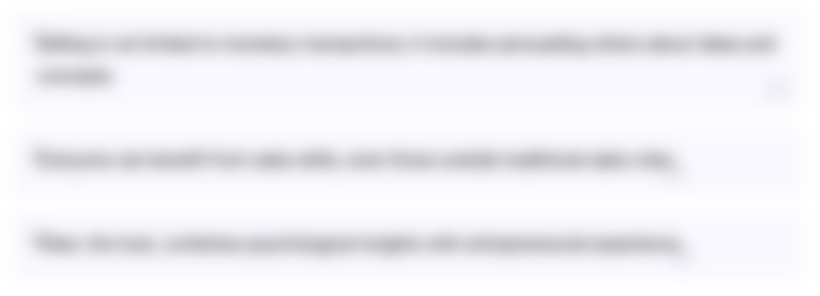
Dieser Bereich ist nur für Premium-Benutzer verfügbar. Bitte führen Sie ein Upgrade durch, um auf diesen Abschnitt zuzugreifen.
Upgrade durchführenTranscripts
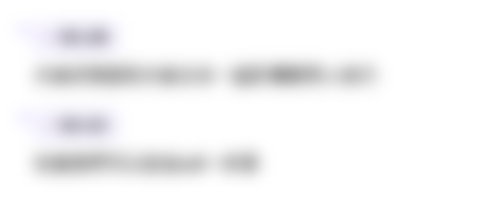
Dieser Bereich ist nur für Premium-Benutzer verfügbar. Bitte führen Sie ein Upgrade durch, um auf diesen Abschnitt zuzugreifen.
Upgrade durchführenWeitere ähnliche Videos ansehen
5.0 / 5 (0 votes)