THIS IS THE PROCESS OF MAKING A PENCIL FROM RAW MATERIALS TO BECOME THE PRODUCT WE KNOW
Summary
TLDRThis video takes viewers through the fascinating process of pencil manufacturing at Faber-Castell in Germany. It highlights the historical significance of pencils, the use of graphite and clay in their production, and the various stages involved in making a high-quality pencil. From underground mining of graphite to the precision of creating the pencil body, applying paint, and finally, checking for quality, every step is detailed. The video also emphasizes the craftsmanship and expertise behind one of the oldest and largest pencil manufacturers in the world, Faber-Castell, founded in 1761.
Takeaways
- 😀 Pencils have been in use since the 1500s, with significant advancements in the 18th century, particularly the invention of a new type of pencil in 1795 by a French chemist.
- 😀 The core of modern pencils is made from a mixture of graphite and clay, which gives the pencil its writing and drawing properties.
- 😀 Graphite, a soft and slippery form of carbon, allows pencils to mark paper, while the addition of clay makes the core harder and more durable.
- 😀 The proportions of graphite and clay vary to create different pencil hardness levels, ranging from soft (8B) to hard (6H), with HB being a balanced standard.
- 😀 Graphite is mined underground and then mixed with clay at a factory, where it is turned into a paste that is extruded through high-pressure machines.
- 😀 The graphite-clay paste is dried in an electric oven at 120°C for several hours to harden before being subjected to an abrasion test to check its durability.
- 😀 Pencil wood is typically sourced from softwoods like pine, and logs are shaped into slats with grooves to hold the graphite core.
- 😀 Glue is applied to hold the graphite core in place inside the wooden slats, which are then pressed together under high pressure.
- 😀 After drying, the wooden pencil bodies are shaped into different forms (round, hexagonal, or triangular) using a planning machine.
- 😀 The pencils are then painted to hide the wood grain and add color, and are stamped with brand and pencil type information.
- 😀 After painting, the pencils are sharpened quickly using a high-speed grinding drum, and undergo a final quality check before being packaged for shipment worldwide.
- 😀 Faber-Castell, one of the largest pencil manufacturers in the world, produces over 1.8 billion pencils annually and has been in business since 1761.
Q & A
What historical event is mentioned regarding the invention of the pencil?
-The pencil, as we know it today, was invented in the 1790s by a French chemist who created a new type of pencil made from graphite powder and clay.
What is the significance of graphite in pencil manufacturing?
-Graphite is used in pencils because it is a soft and slippery form of carbon that leaves a mark on paper. It also helps in determining the hardness of the pencil based on its proportion mixed with clay.
What are the different types of hardness levels for pencils?
-Pencils have different hardness levels ranging from 8B (softer and darker) to 6HB (harder and lighter). The level of hardness depends on the ratio of graphite to clay in the pencil core.
What does the term 'lite' refer to in the context of pencil manufacturing?
-In the transcript, 'lite' refers to the pencil core, which is made from a mixture of graphite and clay, although the term may be used differently in English, as 'lead' is commonly used to refer to the pencil core.
How is the graphite paste made before being formed into pencil cores?
-The graphite is mixed with clay and water to form a dough-like paste. This mixture is then extruded through a nozzle under high pressure to form the pencil core.
What role does the electric oven play in pencil production?
-The electric oven is used to dry and harden the graphite and clay paste at temperatures of 120°C for 3.5 hours, and then at 100°C for 45 minutes, to make the pencil cores solid enough for use.
What are the testing methods for the pencil's quality during manufacturing?
-The pencil cores are subjected to an abrasion test to check their durability. A hardness scale from 8B to 6HB is used to determine the quality based on the ratio of graphite to clay.
How does the wood used in pencil production contribute to the final product?
-The wood is used to encase the pencil core, providing protection and a comfortable grip. It is specially processed to create grooves where the core is inserted, and it is bonded with elastic glue to minimize the risk of breakage.
What steps are involved in the final stages of pencil production?
-The pencils are painted to cover the wood grain and stamped with brand and grade information. Afterward, they are sharpened using high-speed sandpaper, quality-checked, and packed for distribution.
How many pencils does Faber-Castell produce and sell annually?
-Faber-Castell sells over 1.8 billion pencils annually, making it the largest and oldest wooden pencil manufacturer in the world.
Outlines
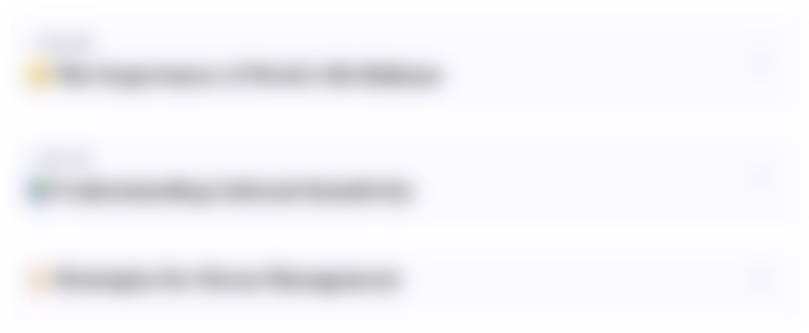
Dieser Bereich ist nur für Premium-Benutzer verfügbar. Bitte führen Sie ein Upgrade durch, um auf diesen Abschnitt zuzugreifen.
Upgrade durchführenMindmap
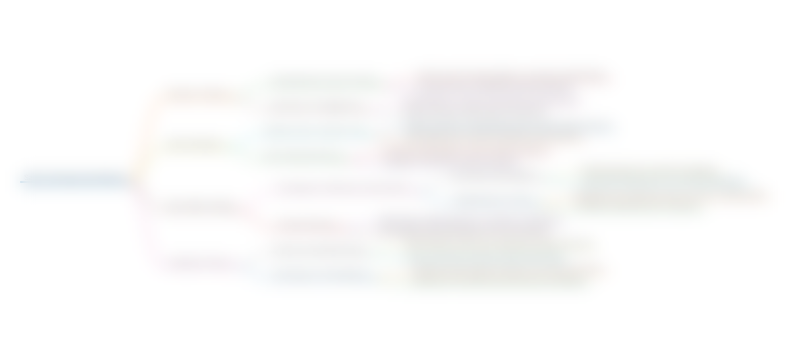
Dieser Bereich ist nur für Premium-Benutzer verfügbar. Bitte führen Sie ein Upgrade durch, um auf diesen Abschnitt zuzugreifen.
Upgrade durchführenKeywords
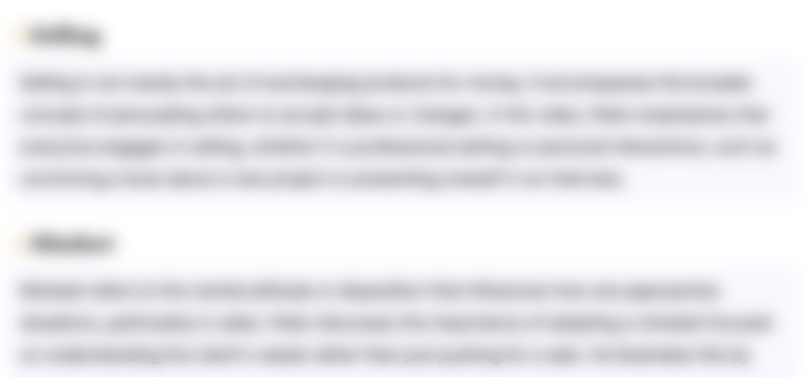
Dieser Bereich ist nur für Premium-Benutzer verfügbar. Bitte führen Sie ein Upgrade durch, um auf diesen Abschnitt zuzugreifen.
Upgrade durchführenHighlights
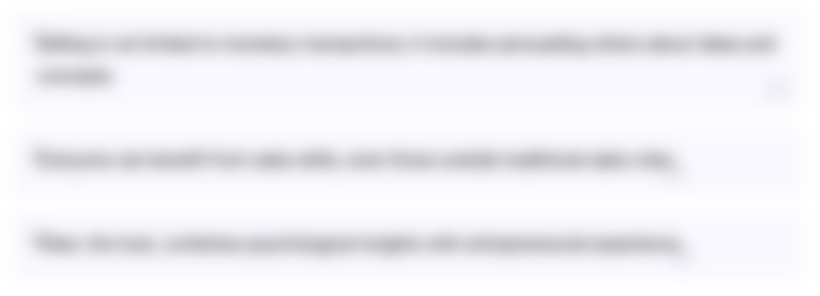
Dieser Bereich ist nur für Premium-Benutzer verfügbar. Bitte führen Sie ein Upgrade durch, um auf diesen Abschnitt zuzugreifen.
Upgrade durchführenTranscripts
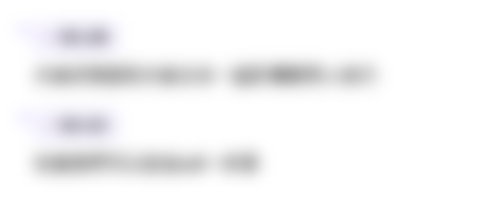
Dieser Bereich ist nur für Premium-Benutzer verfügbar. Bitte führen Sie ein Upgrade durch, um auf diesen Abschnitt zuzugreifen.
Upgrade durchführenWeitere ähnliche Videos ansehen
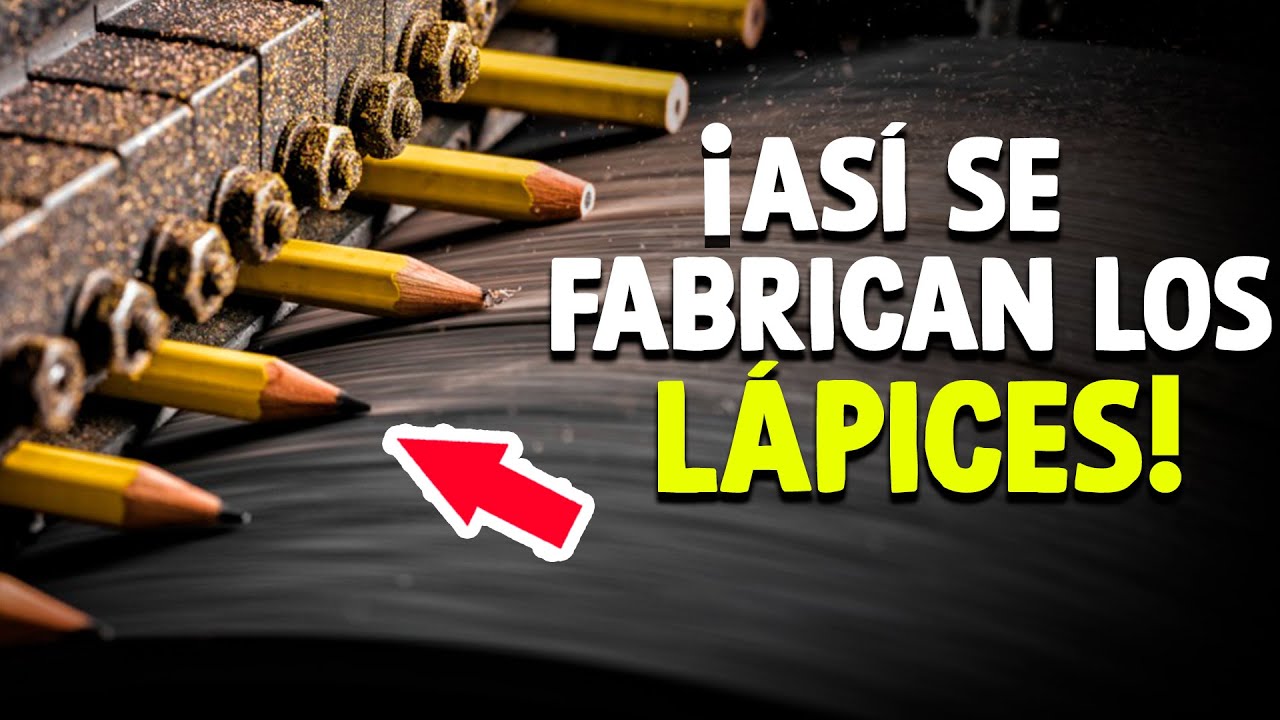
Cómo Se Fabrican Los Lápices? [Proceso En Fábrica]

Como é FABRICADO o PORCELANATO #Boravê 🔵Manual do Mundo
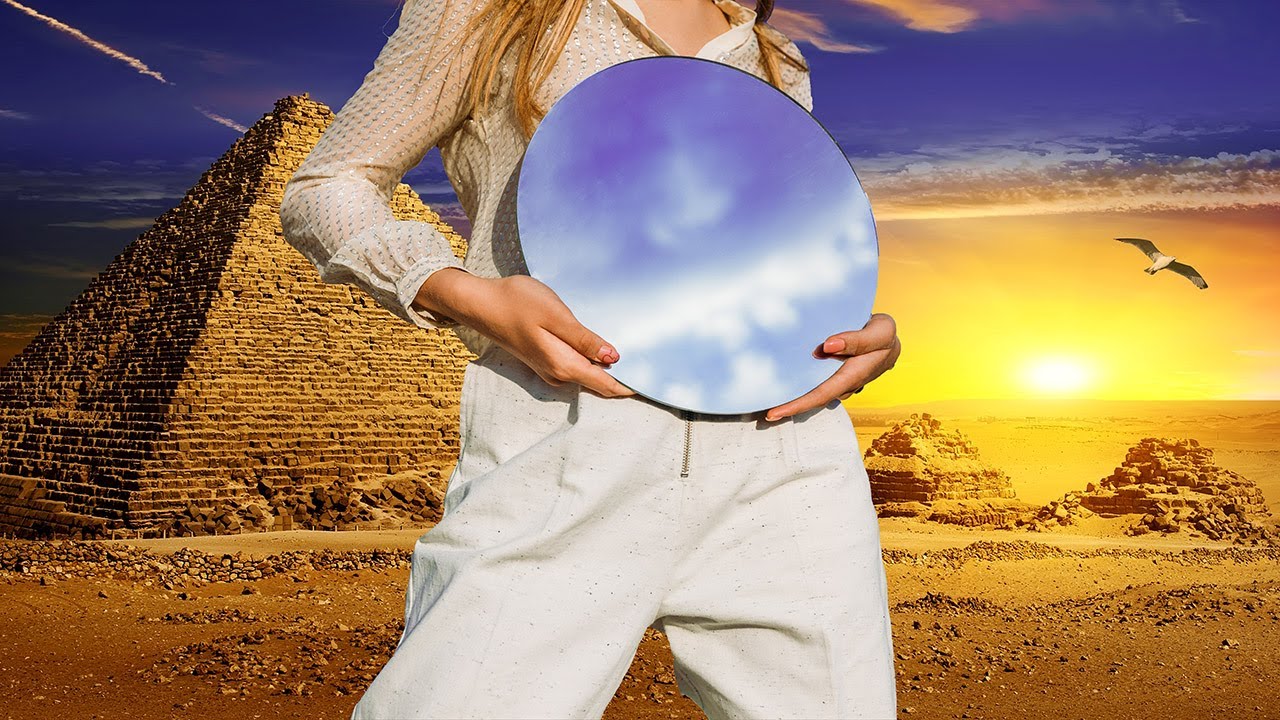
How Mirrors are Made | History of Mirrors from 8,000 BC to Modern Day

How a CPU is made

Perbedaan Pensil Warna Faber Castell Classic dan Watercolour

Faber-Castell: La produccion de los lapices madera (Espanol)
5.0 / 5 (0 votes)