Reliability Block Diagram Explanation | Series, Parallel and Mixed Configuration | RBD Examples
Summary
TLDRThis lecture introduces the concept of reliability block diagrams (RBD) and how reliability is calculated in series and parallel configurations. It explains how the reliability of a system is influenced by the reliability of its individual components, using examples like automobiles and HVAC systems. In series, the failure of any component leads to system failure, and reliabilities are multiplied to find the overall system reliability. In parallel, redundancy ensures that system failure only occurs if all components fail. The video also discusses how reliability is calculated for both configurations and highlights the importance of hot standby in parallel systems.
Takeaways
- 😀 Reliability is a concept applied not only to entire machines but also to their individual components, which collectively determine the overall system reliability.
- 😀 The Reliability Block Diagram (RBD) is used to understand how the reliability of machine components combines to form the system's total reliability.
- 😀 In a **series configuration**, failure of any one component leads to system failure, and the overall reliability is calculated by multiplying the reliabilities of each component.
- 😀 Example of series configuration: In a vehicle, the engine, transmission, and suspension are connected in series. If any one part fails, the entire vehicle fails.
- 😀 In a **parallel configuration**, failure of one component does not result in system failure due to redundancy. Other components take over to keep the system running.
- 😀 Example of parallel configuration: HVAC systems often have redundant compressors. If one compressor fails, the other continues to operate.
- 😀 The reliability of parallel components is calculated using a different formula than series components, often resulting in a higher overall system reliability due to redundancy.
- 😀 For a **hot standby** parallel configuration, the formula for calculating reliability considers redundant components. If both parts are the same, their combined reliability is higher than individual reliabilities.
- 😀 **Cold standby** (to be discussed in later lectures) is another type of parallel configuration, which differs from hot standby in its reliability calculation method.
- 😀 An example calculation for parallel components: Two compressors with 90% reliability in parallel result in a system reliability of 99%.
- 😀 A well-constructed Reliability Block Diagram allows engineers to visualize the system's components in series or parallel, aiding in calculating the overall reliability and identifying potential failure points.
Q & A
What is the purpose of a reliability block diagram (RBD)?
-The purpose of a reliability block diagram (RBD) is to visualize how the reliability of different components in a system combine, allowing for the calculation of the overall reliability of the system based on the configuration of its parts (series or parallel).
How does the reliability of a system in series differ from that in parallel?
-In a series configuration, the reliability of the entire system is the product of the reliabilities of its individual components, meaning if one component fails, the entire system fails. In a parallel configuration, redundancy is introduced, so the system can continue functioning if one component fails, as another will take over, thus increasing the overall reliability.
What is an example of a real-world system with components in series?
-An example of a real-world system with components in series is a vehicle, where the engine, transmission, and suspension are all connected in series. If any one of these components fails, the vehicle cannot operate.
How do you calculate the resultant reliability of a system in series?
-In a series configuration, the resultant reliability of the system is calculated by multiplying the reliabilities of all individual components. For example, if three components have reliabilities of 95%, 90%, and 88%, the overall reliability would be the product: 0.95 × 0.90 × 0.88 = 75.24%.
What does a parallel configuration of components allow in terms of system reliability?
-A parallel configuration allows redundancy, meaning if one component fails, another can take over and keep the system running, thus increasing the overall reliability of the system. The failure of just one component will not lead to system failure.
How do you calculate the reliability of a parallel system with two identical components?
-For two identical components in parallel, the overall reliability can be calculated using the formula: 1 - (1 - R1)(1 - R2), where R1 and R2 are the reliabilities of the components. For example, with each component having a reliability of 90%, the system's reliability is: 1 - (1 - 0.90)(1 - 0.90) = 99%.
What is the difference between hot standby and cold standby in a parallel configuration?
-In a hot standby configuration, the backup component is actively ready to take over immediately if the primary component fails. In a cold standby configuration, the backup component is not active until it is needed, and we will discuss it in more detail in a future lecture.
What is the combined reliability of a system with three components in series, each with reliabilities of 95%, 90%, and 88%?
-The combined reliability of a system with components in series is the product of the reliabilities of all components. For components with reliabilities of 95%, 90%, and 88%, the overall reliability would be: 0.95 × 0.90 × 0.88 = 75.24%.
Why is the reliability of a parallel system greater than that of its individual components?
-The reliability of a parallel system is greater because redundancy is introduced. If one component fails, the parallel backup component can take over, reducing the likelihood of system failure and improving overall reliability.
What role does redundancy play in increasing the reliability of a system?
-Redundancy increases reliability by providing backup components that can take over if a primary component fails, thus preventing the system from failing entirely and improving the chances of continued operation.
Outlines
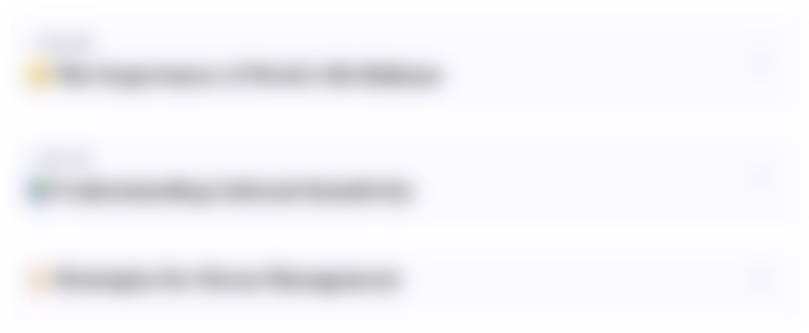
Dieser Bereich ist nur für Premium-Benutzer verfügbar. Bitte führen Sie ein Upgrade durch, um auf diesen Abschnitt zuzugreifen.
Upgrade durchführenMindmap
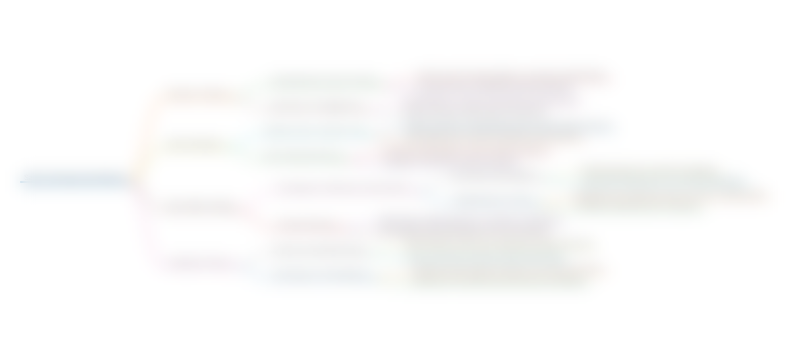
Dieser Bereich ist nur für Premium-Benutzer verfügbar. Bitte führen Sie ein Upgrade durch, um auf diesen Abschnitt zuzugreifen.
Upgrade durchführenKeywords
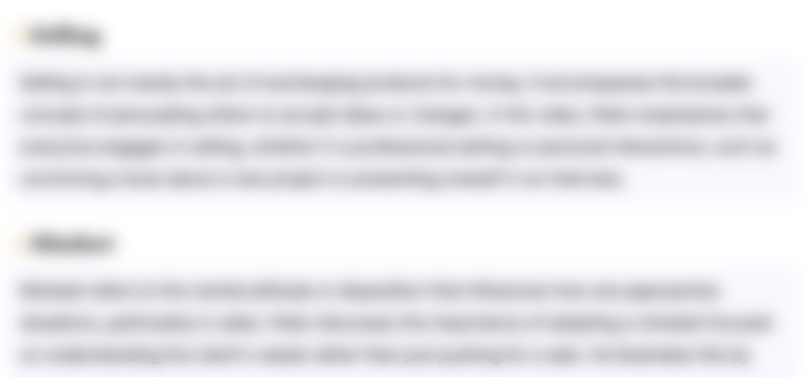
Dieser Bereich ist nur für Premium-Benutzer verfügbar. Bitte führen Sie ein Upgrade durch, um auf diesen Abschnitt zuzugreifen.
Upgrade durchführenHighlights
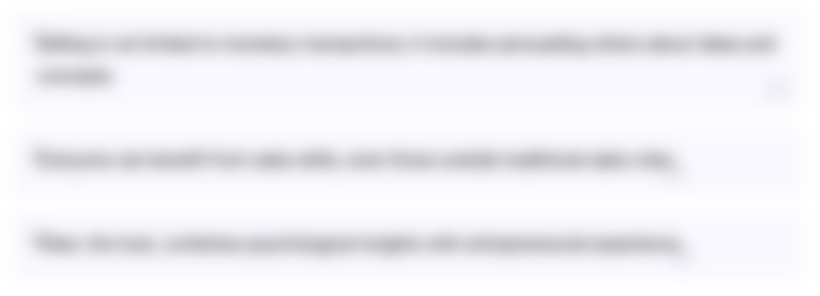
Dieser Bereich ist nur für Premium-Benutzer verfügbar. Bitte führen Sie ein Upgrade durch, um auf diesen Abschnitt zuzugreifen.
Upgrade durchführenTranscripts
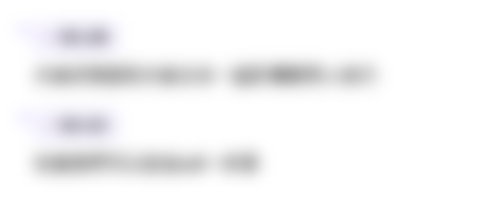
Dieser Bereich ist nur für Premium-Benutzer verfügbar. Bitte führen Sie ein Upgrade durch, um auf diesen Abschnitt zuzugreifen.
Upgrade durchführenWeitere ähnliche Videos ansehen
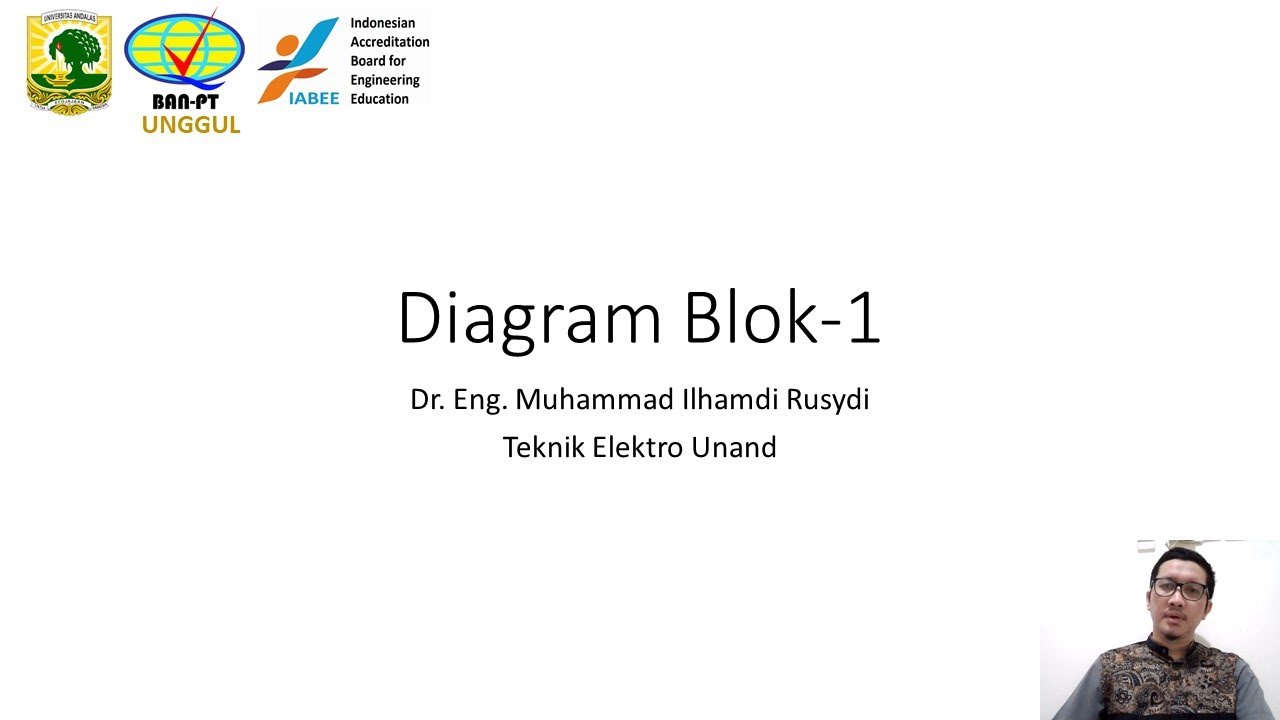
Diagram Blok - 1- Pemodelan dengan diagram blok, komponen utama diagram blok, hubungan antar sistem

What is System Reliability? - Basic Concept & Intuitive Explanation of Equipment Reliability
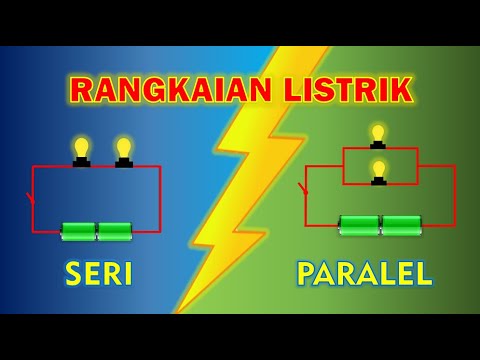
MEDIA PEMBELAJARAN RANGKAIAN LISTRIK SERI DAN PARALEL
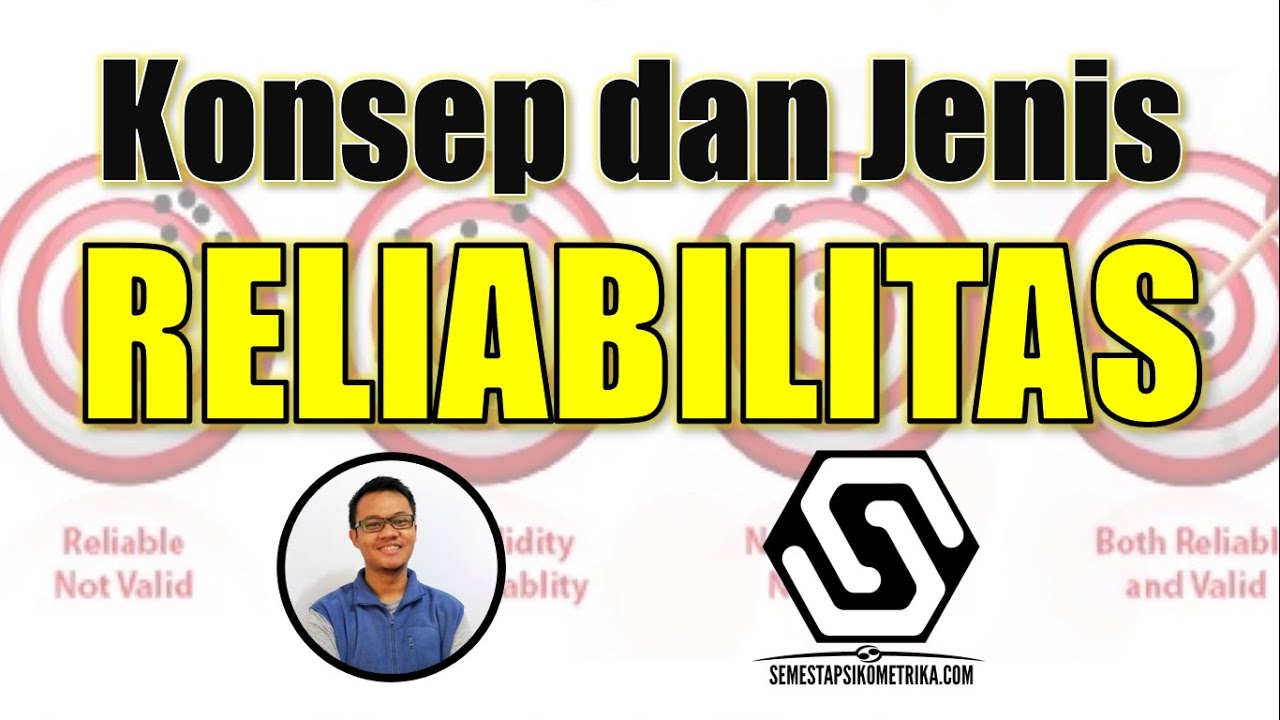
Konsep dan Jenis Reliabilitas

PCSI - video 3 - SLCI cours asservissements - Partie2 : FT et schema blocs

Forms of Reliability in Research and Statistics
5.0 / 5 (0 votes)