Do you know how an electrical cable is manufactured?
Summary
TLDRThis video provides an in-depth look at the intricate process of manufacturing electrical cables. From the initial copper wire drawing to the application of insulation and protective layers, each step is designed to ensure optimal performance, safety, and durability. The video highlights the high-quality materials used, such as copper and aluminum, and the sophisticated technology behind extrusion, annealing, and voltage testing. Top Cable’s commitment to rigorous quality control and environmental sustainability, along with advanced logistics, guarantees that their cables meet the highest standards for various industrial applications.
Takeaways
- 😀 Top Cable is one of the world's largest manufacturers of electrical cables, focused on producing high-quality cables for various installations.
- 😀 Electrical cables are crucial in everyday tasks like lighting, using lifts, and powering electronics, though they often go unnoticed.
- 😀 The key components of an electrical cable are the conductor, which channels current, and the insulation, which prevents current leakage.
- 😀 Copper is the most commonly used conductor material due to its high conductivity, with aluminum being used in specific cases.
- 😀 The wire drawing process reduces the diameter of copper wire gradually to increase ductility and conductivity, starting from wire rods weighing up to 5 tons.
- 😀 After drawing, copper wire undergoes annealing (heat treatment) to enhance its flexibility and conductivity.
- 😀 The wiring process groups copper wires to create conductors of varying sizes, depending on the cable's intended current capacity.
- 😀 The insulation process involves covering the conductor with materials like PVC, EPR, or XLPE through extrusion at high temperatures.
- 😀 Cables undergo voltage testing to ensure there are no faults in the insulation and that they meet safety standards.
- 😀 In addition to basic insulation, cables may include additional protective layers like electrical screens for signal protection and mechanical armor to guard against damage.
- 😀 Top Cable rigorously tests all cables through quality control systems approved by ISO 9001, ensuring defect-free products before shipment.
Q & A
What are the two main components of an electrical cable?
-The two main components of an electrical cable are the conductor, which channels the current, and the insulation, which maintains the flow of electricity and prevents leakage.
What is the most common material used for the conductor in electrical cables?
-The most frequently used material for the conductor in electrical cables is copper, although aluminum is also used in specific cases.
What is the purpose of the wire drawing process in cable manufacturing?
-The wire drawing process involves reducing the diameter of copper wire gradually to increase its ductility and conductivity, making it suitable for use in electrical cables.
Why is annealing important in the wire drawing process?
-Annealing is a heat treatment applied to the wire to increase its ductility and conductivity, which are essential for the cable's performance.
How are conductors grouped together in the manufacturing process?
-After the wire drawing process, copper wires are grouped together to form conductors in a process known as wiring. This step allows the creation of cables with various cross-sectional sizes.
What materials are commonly used for the insulation of electrical cables?
-Common materials used for insulation in electrical cables include PVC (Polyvinyl Chloride), EPR (Ethylene Propylene Rubber), and XLPE (Cross-Linked Polyethylene), each chosen based on the cable's specific requirements.
What role does insulation play in the functioning of an electrical cable?
-Insulation prevents current leakage and ensures the safety and efficiency of the cable. It also provides protection against external factors such as moisture and physical damage.
What is the purpose of adding an outer sheath to a cable?
-The outer sheath protects the conductor and its insulation from external elements like moisture and mechanical aggression during installation, ensuring the cable remains functional over time.
What is the significance of the voltage test during cable manufacturing?
-The voltage test ensures that the insulation layer of the cable does not have any faults and that the cable can safely handle the intended electrical load.
How does Top Cable ensure the environmental impact of its manufacturing processes is minimized?
-Top Cable ensures minimal environmental impact by recycling all waste produced during the manufacturing process. Scrap cable and other waste are sent to specialized companies for proper disposal and recycling.
Outlines
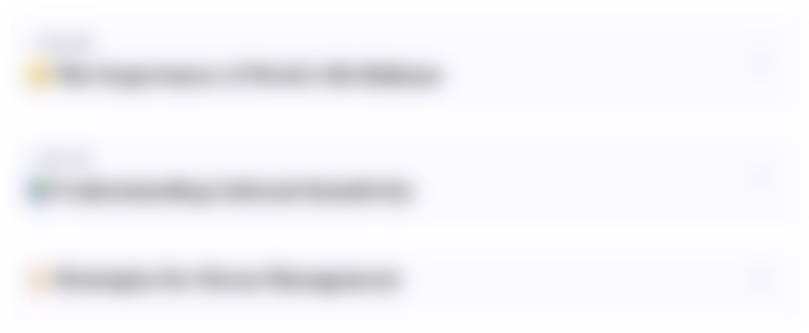
Dieser Bereich ist nur für Premium-Benutzer verfügbar. Bitte führen Sie ein Upgrade durch, um auf diesen Abschnitt zuzugreifen.
Upgrade durchführenMindmap
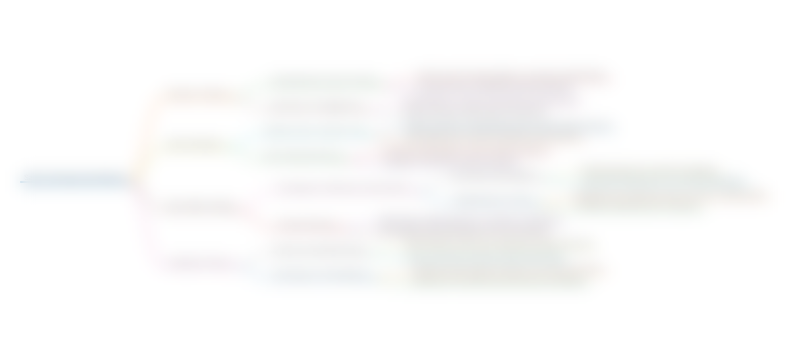
Dieser Bereich ist nur für Premium-Benutzer verfügbar. Bitte führen Sie ein Upgrade durch, um auf diesen Abschnitt zuzugreifen.
Upgrade durchführenKeywords
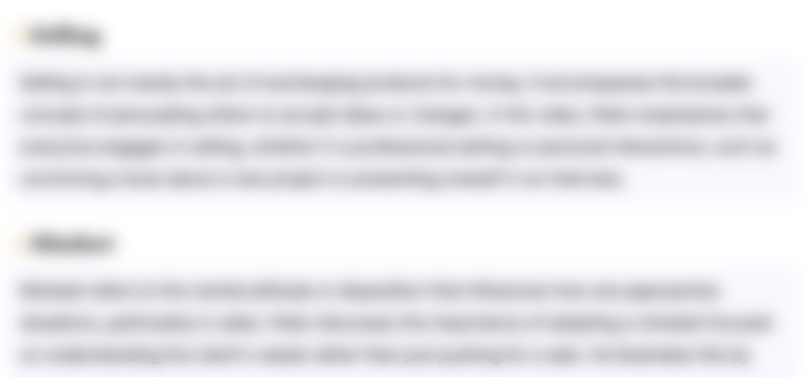
Dieser Bereich ist nur für Premium-Benutzer verfügbar. Bitte führen Sie ein Upgrade durch, um auf diesen Abschnitt zuzugreifen.
Upgrade durchführenHighlights
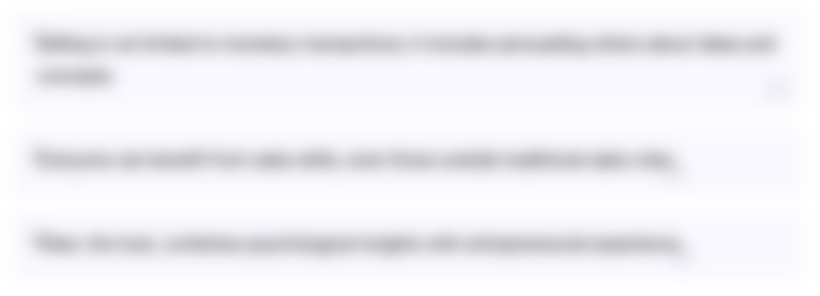
Dieser Bereich ist nur für Premium-Benutzer verfügbar. Bitte führen Sie ein Upgrade durch, um auf diesen Abschnitt zuzugreifen.
Upgrade durchführenTranscripts
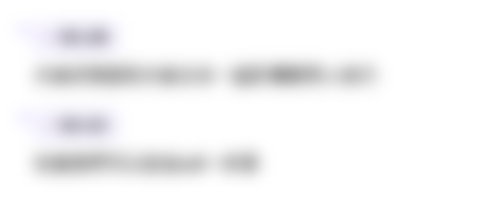
Dieser Bereich ist nur für Premium-Benutzer verfügbar. Bitte führen Sie ein Upgrade durch, um auf diesen Abschnitt zuzugreifen.
Upgrade durchführen5.0 / 5 (0 votes)