Lean Manufacturing : What is Single Piece Flow?
Summary
TLDRThis video explores the difference between traditional batch processing and lean single-piece flow manufacturing. It highlights the inefficiencies of batch processing, such as excess inventory and delayed customer deliveries, while emphasizing the benefits of single-piece flow, including faster delivery, better quality control, and reduced waste. The video also covers the challenges involved in transitioning to single-piece flow, such as layout adjustments, operator training, and addressing core operational issues. By adopting a cellular layout and streamlining production, manufacturers can enhance efficiency, reduce costs, and better meet customer demands.
Takeaways
- 😀 Single-piece flow manufacturing eliminates the need for batch processing, focusing on one item at a time to reduce inventory and improve efficiency.
- 😀 Batch processing, while improving machine utilization, can create inventory build-ups, making it difficult for customers to receive products promptly.
- 😀 A functional layout supports batch processing, while a cellular layout is more suited to single-piece flow, requiring the machines to be arranged in sequence.
- 😀 Implementing a single-piece flow requires identifying losses and inefficiencies, making these problems more apparent through trial runs and adjustments.
- 😀 During a single-piece flow trial, the lean team should observe and document potential improvements, such as reducing machine distances or eliminating trolleys.
- 😀 Resolving key problems like quality issues, machine reliability, and supplier delays is crucial before fully adopting a single-piece flow system.
- 😀 Unlike batch production, where downtime may not affect deliveries due to high inventory, a single-piece flow system means that any machine downtime directly impacts the entire line.
- 😀 In a single-piece flow system, quality issues are detected and addressed immediately, preventing further defects from being produced.
- 😀 One of the main benefits of single-piece flow is the dramatic reduction in Work-in-Progress (WIP) inventory between processes, improving flow and efficiency.
- 😀 Operators in a single-piece flow system need to be cross-trained, as they may handle multiple machines or operations, unlike in batch processing where operators specialize in a single task.
- 😀 The transition to single-piece flow can be challenging and requires careful preparation and discipline to avoid reverting to less efficient methods and avoid inventory buffers that hide inefficiencies.
Q & A
What is single-piece flow in manufacturing?
-Single-piece flow is a production method where products are created one at a time, moving continuously through the manufacturing process without large batches or in-process inventory. This method contrasts with batch processing, which produces products in large groups.
How does batch processing differ from single-piece flow?
-In batch processing, production occurs in large batches with high inventory at each stage, leading to inefficiencies and delayed customer delivery. In contrast, single-piece flow minimizes inventory between processes, enabling quicker product delivery and immediate identification of issues.
What are the benefits of single-piece flow over batch processing?
-Single-piece flow helps reduce inventory levels, enables immediate identification of quality issues, improves machine utilization, and allows for more responsive customer delivery. It leads to a leaner and more efficient manufacturing process overall.
Why does single-piece flow reduce inventory compared to batch processing?
-In single-piece flow, products move continuously from one process to the next, reducing the need to store large quantities of in-process materials. The system operates with minimal work-in-progress (WIP) inventory, unlike batch processing, which often accumulates excess stock.
How does single-piece flow help with quality control?
-In single-piece flow, defective products are identified immediately after they are produced, allowing for quick intervention to stop further production of faulty items. This contrasts with batch production, where defects may not be discovered until many units have been produced.
What challenges arise when implementing single-piece flow in manufacturing?
-Implementing single-piece flow requires addressing key challenges such as machine reliability, resolving quality issues, optimizing layout for efficiency, and ensuring reliable supplier and delivery systems. Without solving these problems, the system may fail or face significant inefficiencies.
What role does machine reliability play in a single-piece flow system?
-Machine reliability is critical in single-piece flow because any breakdowns directly affect the entire production line. Unlike batch production, where inventory can buffer disruptions, single-piece flow requires constant operation without delays or backups.
How does the workforce change in a single-piece flow system?
-In a single-piece flow system, workers may be required to operate multiple machines or perform various tasks across the production line. This is in contrast to batch production, where workers are usually specialized in operating a single machine. Cross-training is essential to maintain flexibility.
What are the risks of transitioning to single-piece flow without proper preparation?
-Without careful preparation, such as solving quality and reliability issues, the transition to single-piece flow can lead to operational failures. The pressure to revert to batch production can also undermine the effectiveness of the system and reduce overall efficiency.
What steps should be taken before implementing single-piece flow in a manufacturing system?
-Before implementing single-piece flow, it's important to resolve quality issues, ensure machine reliability, and streamline the supplier and delivery processes. Additionally, conducting a trial run to identify potential inefficiencies and layout problems is essential for a smooth transition.
Outlines
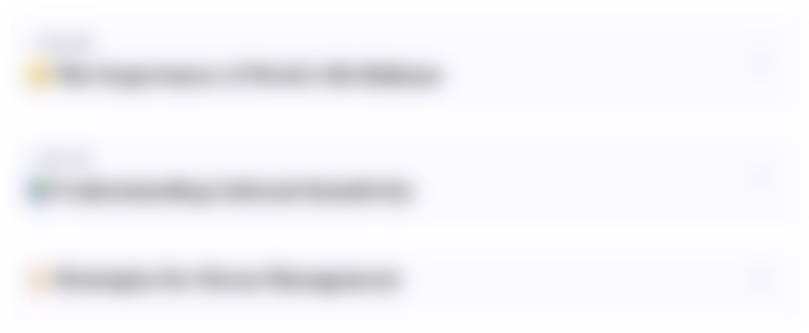
Dieser Bereich ist nur für Premium-Benutzer verfügbar. Bitte führen Sie ein Upgrade durch, um auf diesen Abschnitt zuzugreifen.
Upgrade durchführenMindmap
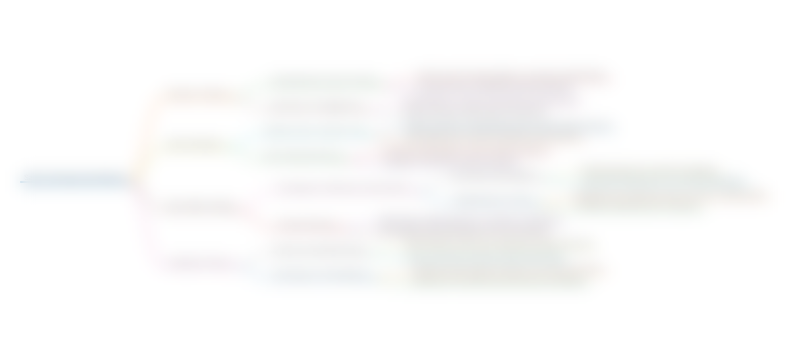
Dieser Bereich ist nur für Premium-Benutzer verfügbar. Bitte führen Sie ein Upgrade durch, um auf diesen Abschnitt zuzugreifen.
Upgrade durchführenKeywords
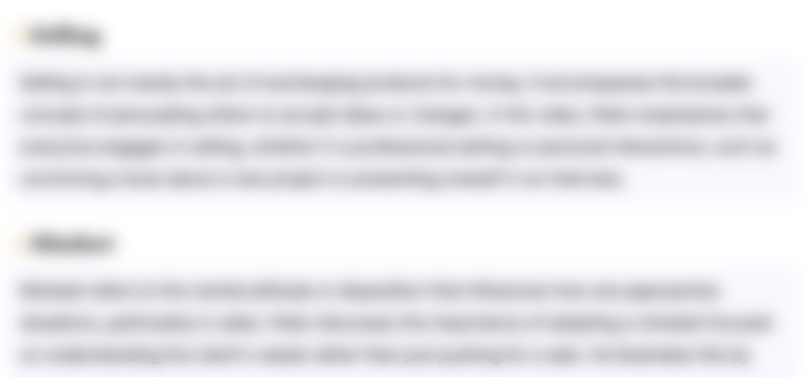
Dieser Bereich ist nur für Premium-Benutzer verfügbar. Bitte führen Sie ein Upgrade durch, um auf diesen Abschnitt zuzugreifen.
Upgrade durchführenHighlights
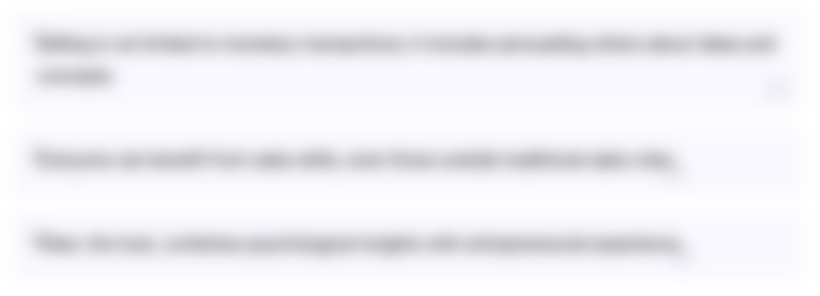
Dieser Bereich ist nur für Premium-Benutzer verfügbar. Bitte führen Sie ein Upgrade durch, um auf diesen Abschnitt zuzugreifen.
Upgrade durchführenTranscripts
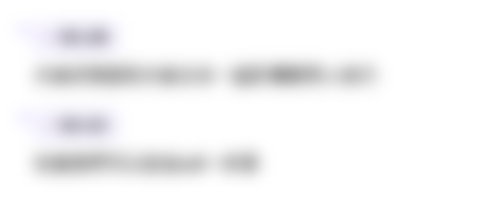
Dieser Bereich ist nur für Premium-Benutzer verfügbar. Bitte führen Sie ein Upgrade durch, um auf diesen Abschnitt zuzugreifen.
Upgrade durchführenWeitere ähnliche Videos ansehen
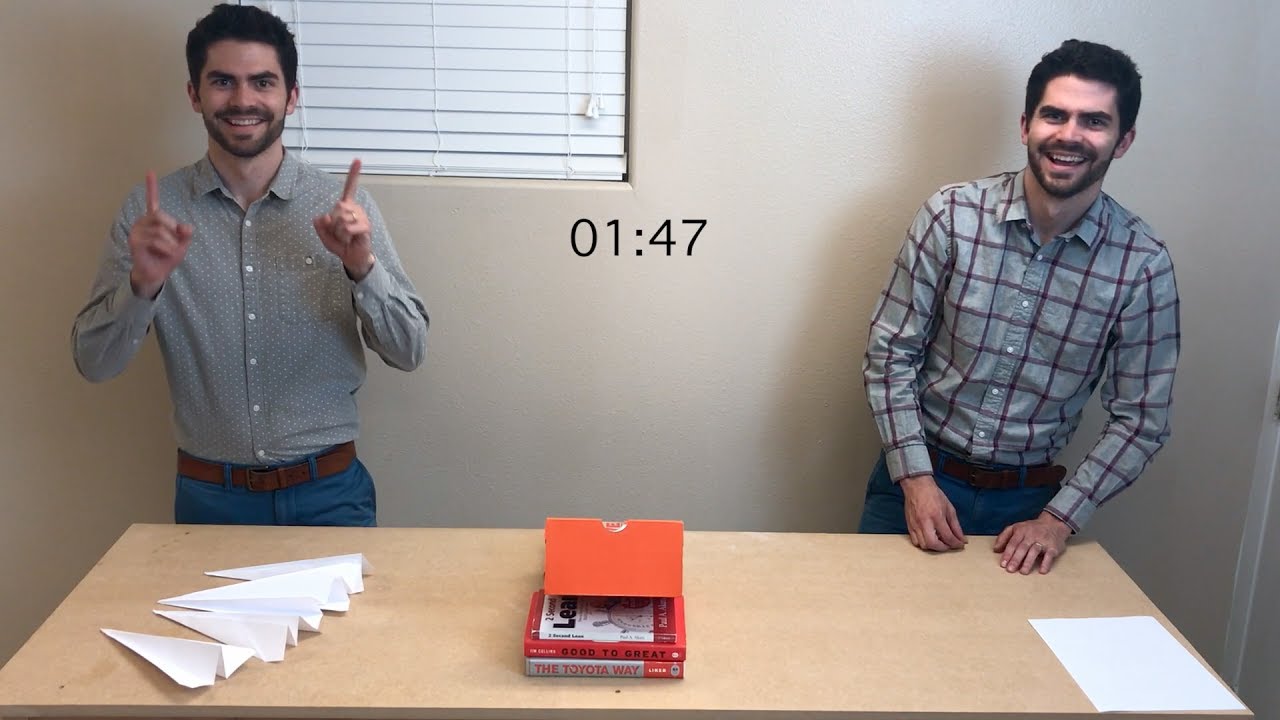
Lean Manufacturing One Piece Flow vs. Mass Production Paper Airplane Simulation (Lean Tip 005)

Cellular Manufacturing: What It Is And Why It Matters
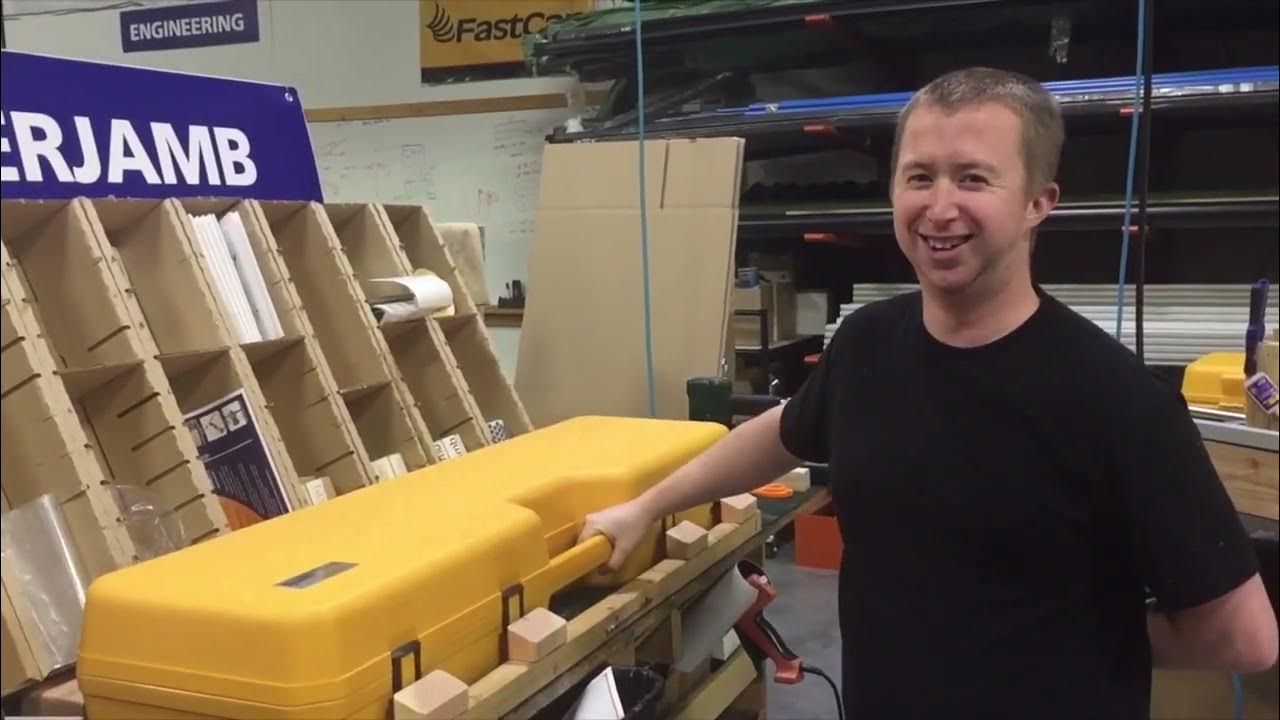
Ch3 - "One Piece Flow" - 2 SECOND LEAN Visual Audiobook
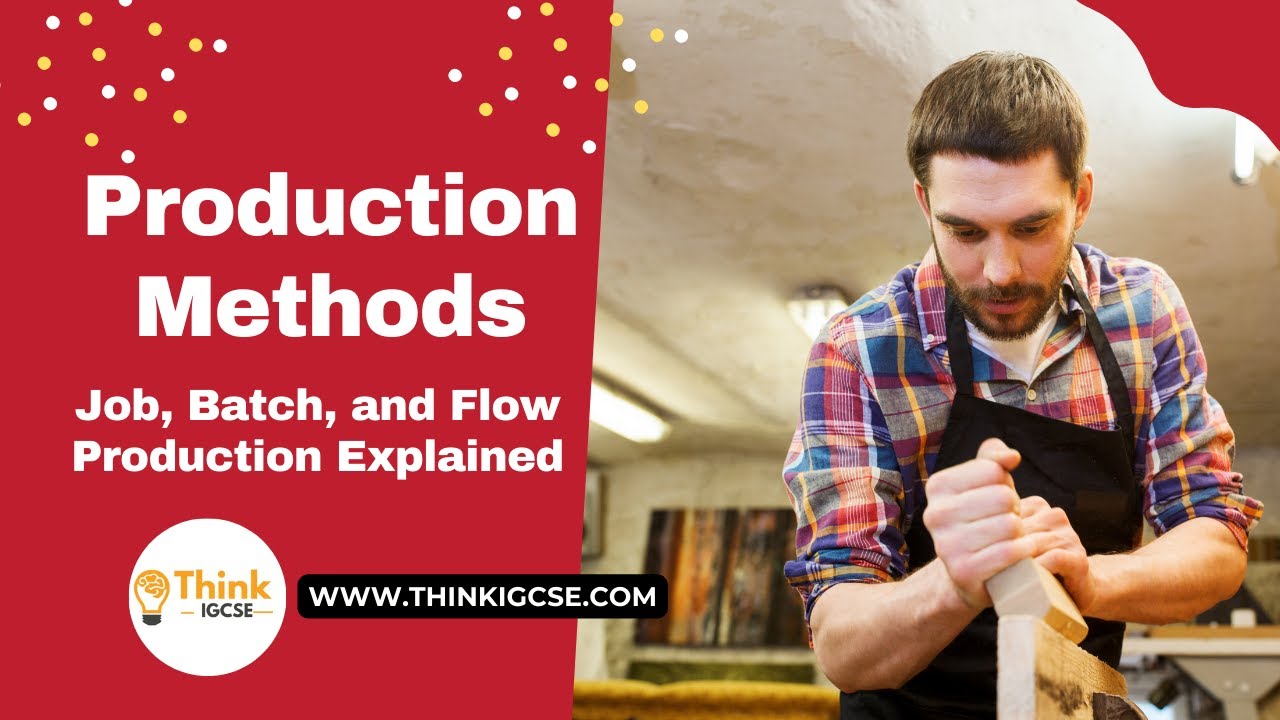
Exploring Production Methods: Job, Batch, and Flow Production Explained | ThinkIGCSE.com
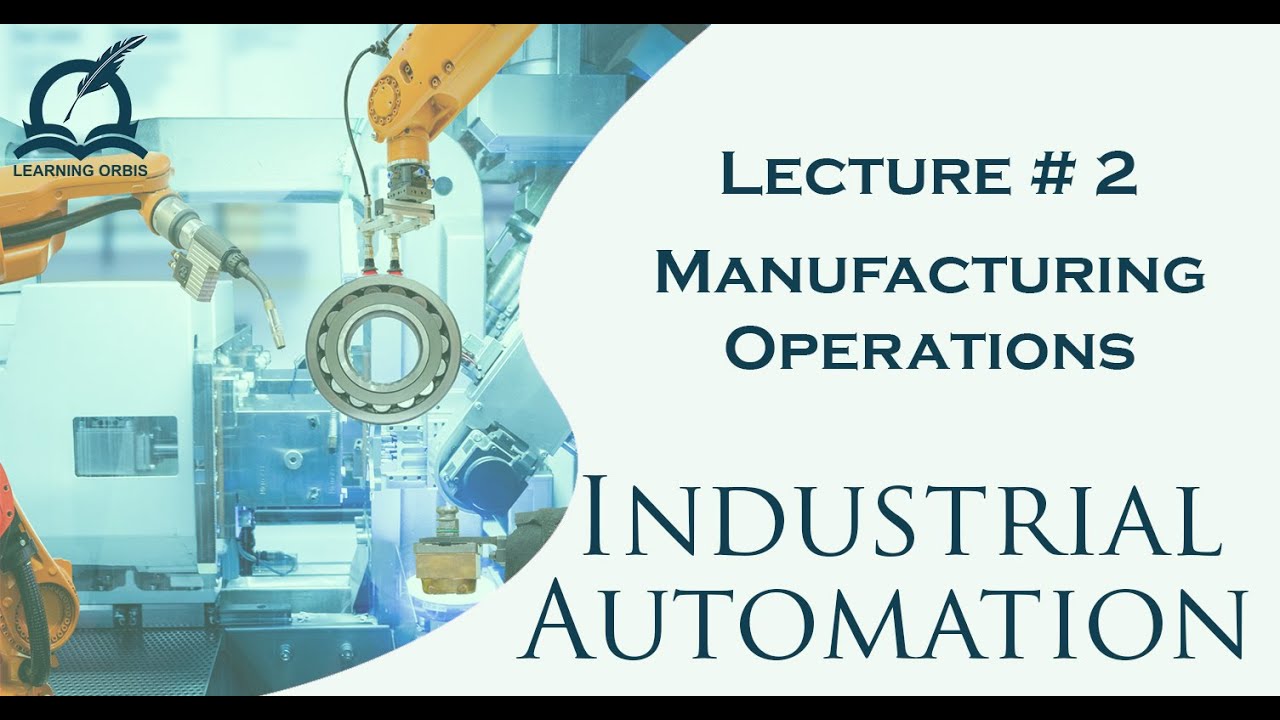
Manufacturing Operations | Industrial Automation

02_06_P1 Three Types of Layouts: Process, Product, and Fixed Position
5.0 / 5 (0 votes)