Lean Manufacturing Changeover | How to Optimize Quick Changeover Times
Summary
TLDRThe video explains the changeover process in manufacturing, focusing on the transition from producing one product to another. It highlights the importance of reducing changeover time to enhance productivity and efficiency. The technique known as Single-Minute Exchange of Die (SMED) is introduced, which categorizes setup activities into internal (performed when the machine is stopped) and external (performed while running). By minimizing internal setup time, companies can increase external setup opportunities, ultimately reducing overall changeover time. This approach is essential for streamlining production processes and maximizing output.
Takeaways
- 🔄 Changeover is the process of switching from one product or part number to another on machines.
- ⏳ The goal of changeover is to reduce downtime and increase efficiency in the production process.
- 📏 Changeover time is measured from the last piece of the current run to the first good piece produced after the changeover.
- 🕒 Changeover time can vary from a few minutes to several hours, depending on production complexity.
- 📈 Reducing changeover time is essential for boosting productivity in manufacturing.
- ⚙️ One technique for reducing changeover time is Single Minute Exchange of Die (SMED).
- 🛠️ SMED is a lean manufacturing tool aimed at reducing changeover time to less than 10 minutes.
- 📊 SMED categorizes changeover activities into internal and external setups.
- 🔧 Internal setup activities can only be performed while the machine is stopped.
- 🔄 External setup activities can be done while the machine is still running, maximizing efficiency.
Q & A
What is the primary goal of the changeover process in manufacturing?
-The primary goal of the changeover process is to reduce downtime and increase efficiency in the production process.
How is changeover time measured in the manufacturing industry?
-Changeover time is measured as the duration between the last piece of the current production run and the first good piece produced after the changeover.
What factors influence the duration of changeover time?
-The duration of changeover time can range from a few minutes to several hours, depending on the complexity of the production process.
Why is reducing changeover time essential for productivity?
-Reducing changeover time is essential for increasing productivity because it minimizes the periods when production is halted, allowing for more efficient operation.
What is SMED and what does it stand for?
-SMED stands for Single Minute Exchange of Die, which is a lean manufacturing tool aimed at reducing changeover time to less than 10 minutes.
How does SMED categorize the changeover process?
-SMED categorizes the changeover process into two types of setup: internal setup, which can only be done while the machine is stopped, and external setup, which can be performed while the machine is still running.
What is the significance of internal and external setup in the changeover process?
-The significance of internal and external setup lies in the ability to optimize the overall changeover time; by reducing internal setup time, more time can be allocated to external setup, thus enhancing efficiency.
What impact does effective changeover have on manufacturing companies?
-Effective changeover allows manufacturing companies to switch production efficiently, leading to increased productivity and improved operational efficiency.
Can changeover time vary widely among different manufacturing processes?
-Yes, changeover time can vary widely among different manufacturing processes due to factors such as product complexity and the types of machines involved.
What are some potential benefits of implementing SMED in a manufacturing setting?
-Implementing SMED can lead to significant reductions in changeover time, increased machine availability, enhanced production flexibility, and overall improvements in productivity.
Outlines
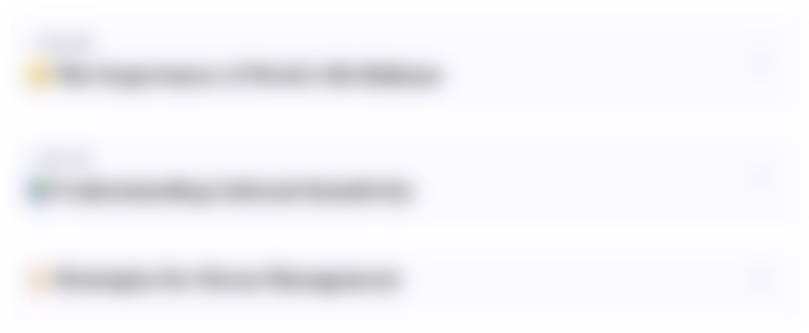
Dieser Bereich ist nur für Premium-Benutzer verfügbar. Bitte führen Sie ein Upgrade durch, um auf diesen Abschnitt zuzugreifen.
Upgrade durchführenMindmap
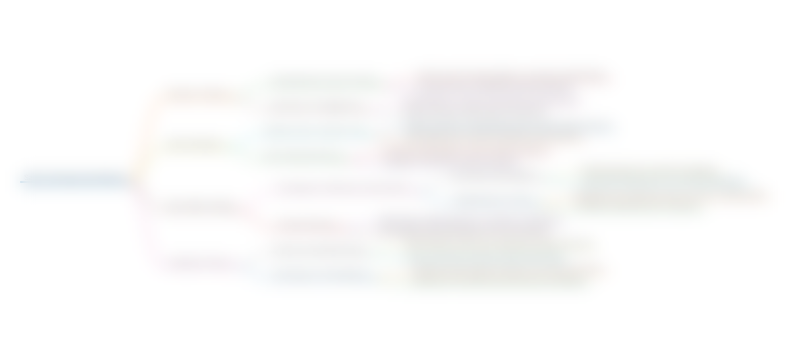
Dieser Bereich ist nur für Premium-Benutzer verfügbar. Bitte führen Sie ein Upgrade durch, um auf diesen Abschnitt zuzugreifen.
Upgrade durchführenKeywords
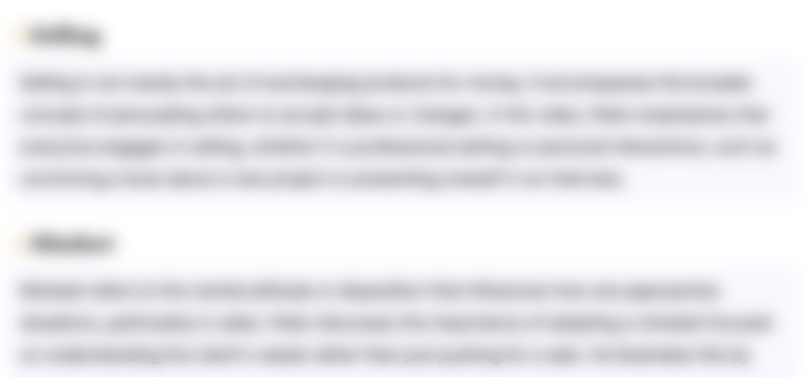
Dieser Bereich ist nur für Premium-Benutzer verfügbar. Bitte führen Sie ein Upgrade durch, um auf diesen Abschnitt zuzugreifen.
Upgrade durchführenHighlights
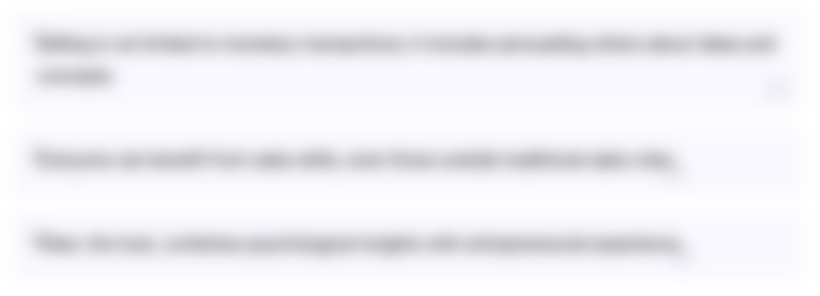
Dieser Bereich ist nur für Premium-Benutzer verfügbar. Bitte führen Sie ein Upgrade durch, um auf diesen Abschnitt zuzugreifen.
Upgrade durchführenTranscripts
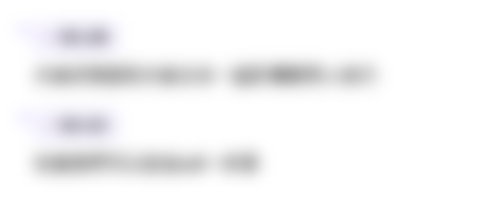
Dieser Bereich ist nur für Premium-Benutzer verfügbar. Bitte führen Sie ein Upgrade durch, um auf diesen Abschnitt zuzugreifen.
Upgrade durchführen5.0 / 5 (0 votes)