ANODIZING PROCESS - Proses Pelapisan Teknik Anodising
Summary
TLDRThe video explains the process of anodizing, a technique to enhance the natural protective layer on metals, particularly aluminum, through electrochemical reactions. It covers the benefits such as increased corrosion resistance, durability, and aesthetic appeal. The presentation discusses various types of anodizing, including AC and DC anodizing, along with their applications in different industries like aerospace and architecture. Detailed steps in the anodizing process, including surface preparation, electrolysis, and sealing, are explained, followed by insights into the reactions, coloring methods, and sealing techniques used to improve the metal's properties.
Takeaways
- 🔍 Anodizing is a process designed to thicken or strengthen the natural protective layer on metals, creating a more durable surface.
- 💡 The process also enhances the decorative appearance of metals, making them more resistant to corrosion.
- 🏗️ Anodized surfaces are resistant to ultraviolet rays, ensuring color stability and easier maintenance.
- ⚡ There are two types of anodizing based on the current: AC anodizing (slower) and DC anodizing (faster).
- 🔧 Three common types of anodizing include chromic acid (thin, high corrosion resistance), sulfuric acid (most common, up to 25 microns), and hard anodizing (tougher, for high abrasion and heat resistance).
- 🛠️ Anodizing process steps include degreasing, etching, anodizing in an electrolyte solution, and sealing to enhance surface protection.
- 🧪 Reactions during anodizing involve the breakdown of sulfuric acid into ions, leading to the formation of aluminum oxide layers.
- 🎨 Coloring can be done using organic dyes or mineral pigments, enhancing both aesthetics and durability of the metal surface.
- 💧 Sealing is critical after anodizing to prevent physical and chemical damage to the anodized layer, often done with hot water or special solutions.
- 🔄 Anodizing is widely used in everyday products for decoration, corrosion resistance, and long-term durability.
Q & A
What is the purpose of the anodizing process?
-The purpose of the anodizing process is to thicken or strengthen the natural protective layer on metal surfaces, making the metal more durable and resistant to corrosion.
What are the main advantages of anodized surfaces?
-Anodized surfaces have a longer lifespan, offer better corrosion resistance, maintain color stability even under ultraviolet light, and are easy to clean using soap and water. They also provide good aesthetic value, with a glossy finish and various color options.
What are the differences between AC anodizing and DC anodizing?
-AC anodizing uses alternating current, leading to slower oxide formation, while DC anodizing uses direct current, resulting in faster oxide layer formation.
What are the most common types of anodizing?
-The most common types of anodizing are chromic acid anodizing (Type 1), sulfuric acid anodizing (Type 2), and hard anodizing (Type 3). Type 1 produces thin, flexible layers, Type 2 offers thicker layers that are suitable for coloring, and Type 3 produces a tough, abrasion-resistant layer.
What is the primary electrolyte used in sulfuric acid anodizing?
-Sulfuric acid is the primary electrolyte used in Type 2 sulfuric acid anodizing, which allows the formation of a protective oxide layer up to 25 microns thick.
What are the basic steps in the anodizing process?
-The basic steps include degreasing the metal, rinsing with water, etching for surface preparation, anodizing using electric current in an electrolyte solution, rinsing again, and then sealing the anodized layer to close the pores.
How is the anodized layer colored?
-Anodized layers can be colored either by using organic dyes or through mineral pigmentation. The dyes or pigments are deposited into the pores of the anodized layer during the coloring stage.
What are the key factors that affect the thickness of the anodized oxide layer?
-Key factors include the type of electrolyte used, current density, anodizing duration, and temperature during the process.
What is the purpose of sealing the anodized layer?
-Sealing the anodized layer is essential to close the pores of the oxide layer, enhancing its corrosion resistance and preventing external factors from affecting the metal underneath.
What applications commonly use anodizing?
-Anodizing is commonly used in various industries for decorative and protective purposes, such as in architecture, aerospace, automotive, electronics, and everyday consumer products.
Outlines
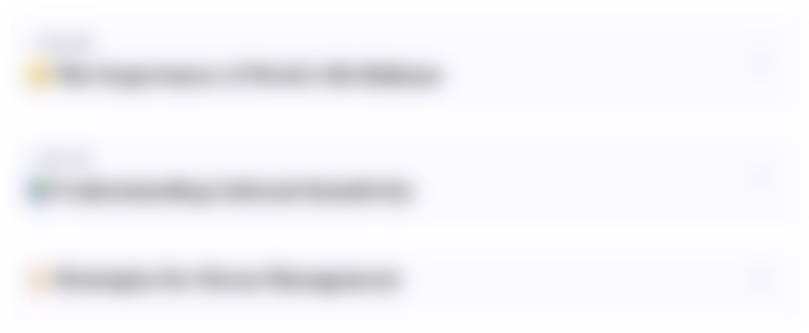
Dieser Bereich ist nur für Premium-Benutzer verfügbar. Bitte führen Sie ein Upgrade durch, um auf diesen Abschnitt zuzugreifen.
Upgrade durchführenMindmap
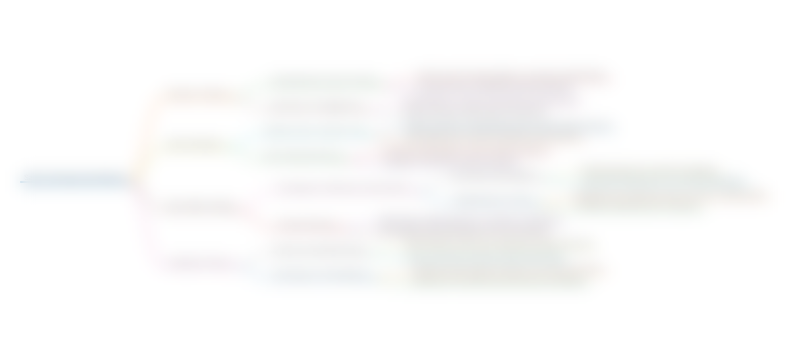
Dieser Bereich ist nur für Premium-Benutzer verfügbar. Bitte führen Sie ein Upgrade durch, um auf diesen Abschnitt zuzugreifen.
Upgrade durchführenKeywords
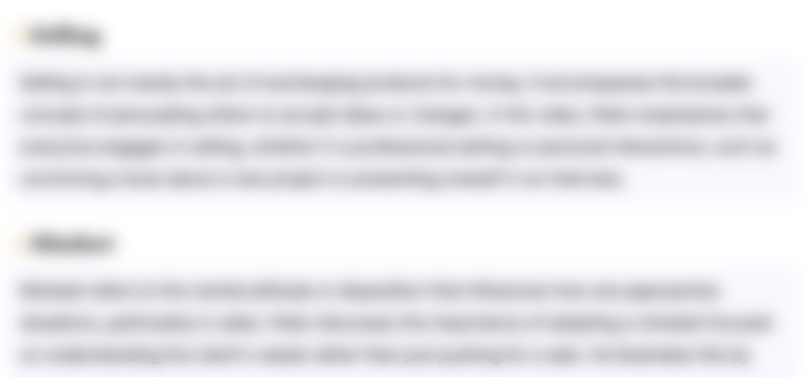
Dieser Bereich ist nur für Premium-Benutzer verfügbar. Bitte führen Sie ein Upgrade durch, um auf diesen Abschnitt zuzugreifen.
Upgrade durchführenHighlights
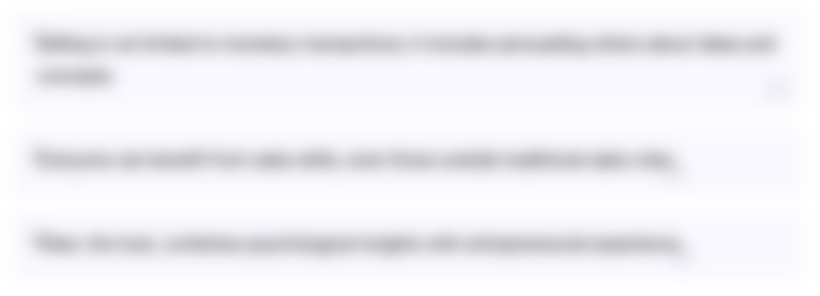
Dieser Bereich ist nur für Premium-Benutzer verfügbar. Bitte führen Sie ein Upgrade durch, um auf diesen Abschnitt zuzugreifen.
Upgrade durchführenTranscripts
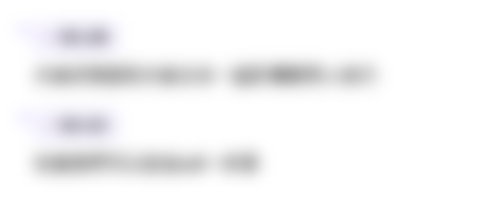
Dieser Bereich ist nur für Premium-Benutzer verfügbar. Bitte führen Sie ein Upgrade durch, um auf diesen Abschnitt zuzugreifen.
Upgrade durchführenWeitere ähnliche Videos ansehen
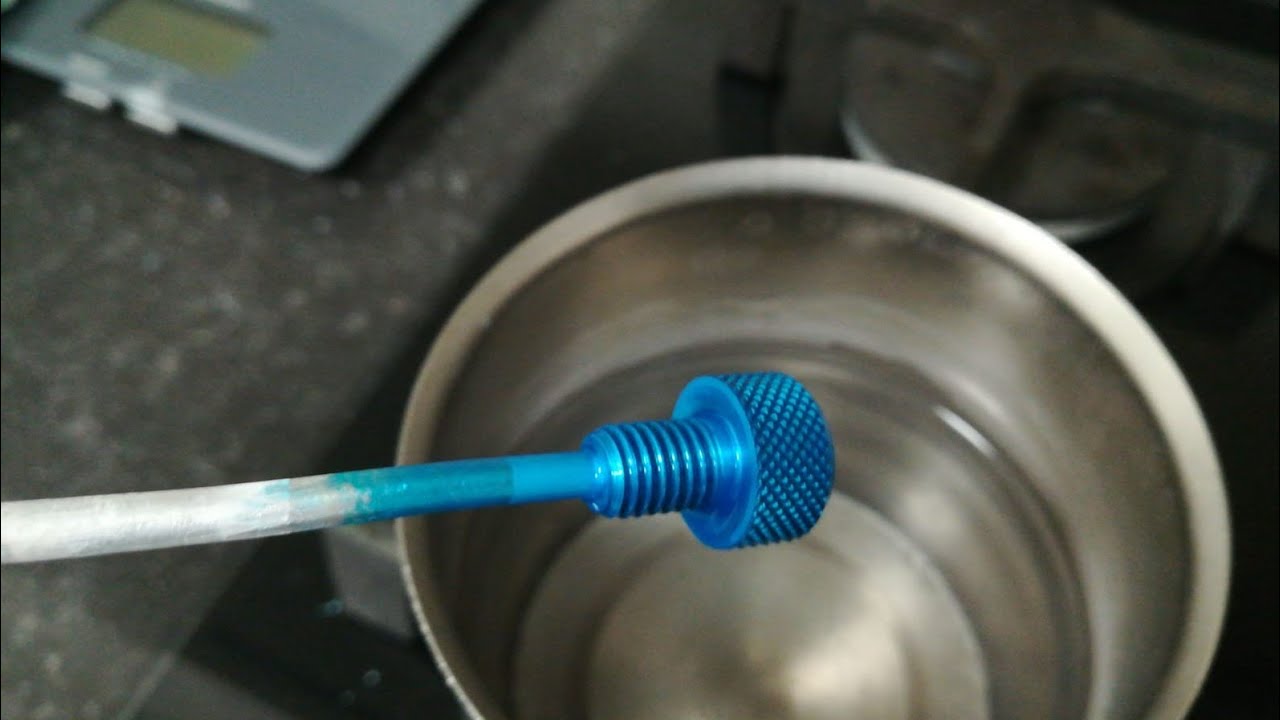
#234 ANODIZZARE ALLUMINIO COLORATO FAI DA TE - How to ANODIZE and COLOR ALUMINIUM DIY [SUB ENG]

Anodisasi

What is Electrochemical Impedance Spectroscopy (EIS) and How Does it Work?

Corrosion : Electrochemical Cell or Corrosion Cell (Chapter 3) (Animation)
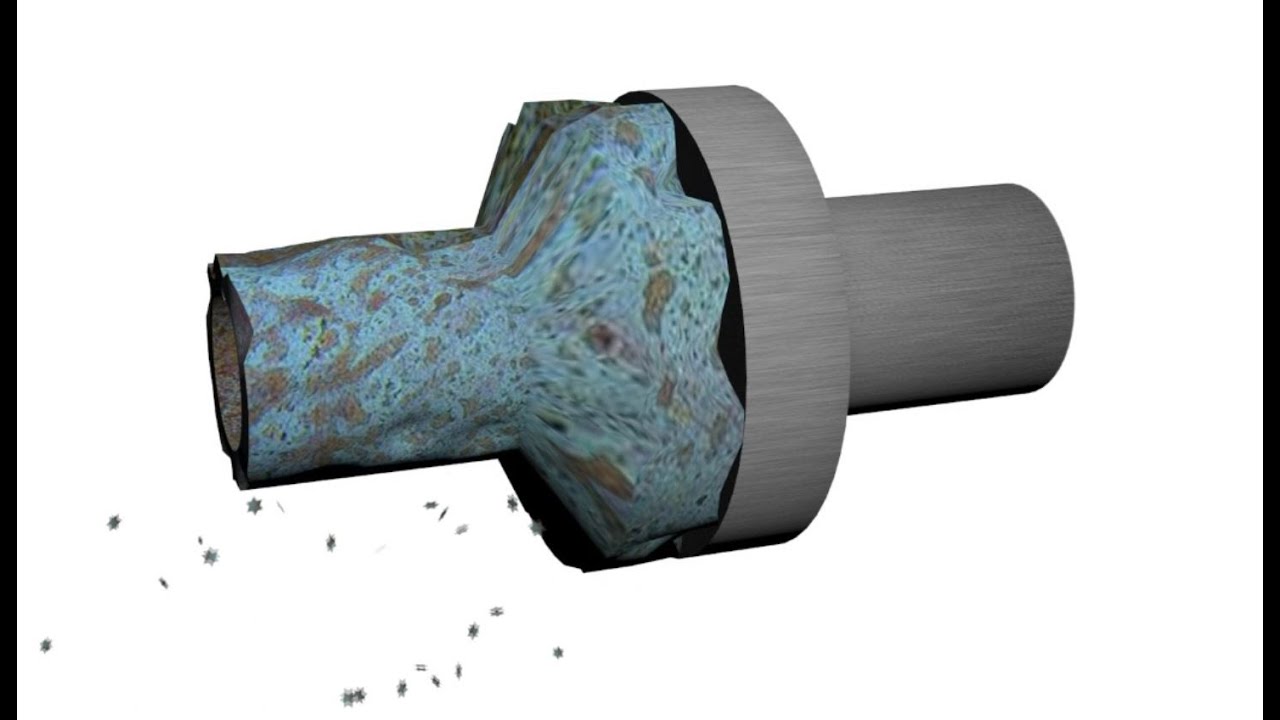
Galvanic Corrosion | Forms of Corrosion

Korosi | Kimia SMA
5.0 / 5 (0 votes)