Sinter plant
Summary
TLDREste video en 3D ofrece una visión detallada del proceso de sinterización en una planta de Indonesia, explicando su importancia en la fabricación de hierro. La planta procesa materiales finos de hierro, inferiores a 10 milímetros, para transformarlos en un mineral adecuado para hornos de fundición. Se detalla la disposición de la planta, que incluye áreas para el manejo de materiales, la producción de sinter y la trituración, así como sistemas de control de polvo. El proceso comienza con la mezcla de mineral de hierro, auxiliares y combustibles, seguido de la granulación y la sinterización en un sinterizador. Posteriormente, el sinter se enfría y se clasifica antes de ser utilizado en el proceso de fundición.
Takeaways
- 🏭 La planta de sinterización es el primer paso en el proceso de fabricación del hierro y es crucial para crear mineral de hierro que se puede usar en un alto horno.
- 📏 La granularidad adecuada del mineral de hierro requerida para un alto horno es superior a 10 milímetros, y la planta de sinterización procesa materiales finos inferiores a 10 milímetros.
- 🏗️ La planta se divide en tres instalaciones principales: manejo de materiales, sinterización y trituración, además de sistemas de control de polvo.
- ♻️ El proceso de sinterización comienza con el mineral de hierro como material principal, y utiliza serpentina, sílice, cal y mineral de sinterización devueltos como materiales auxiliares.
- 🔥 El carbón y el coque se utilizan como combustibles, siendo procesados en equipos de trituración de combustible antes de ser utilizados en la sinterización.
- 🔄 La mezcla de materiales y combustibles en una proporción adecuada es esencial para producir el mineral de sinterización requerido para el alto horno.
- 🌀 El triturador de re-rodaje granula los materiales, agregando la cantidad adecuada de humedad y mejorando la permeabilidad necesaria para el proceso de sinterización.
- 🔥 La superficie de los materiales mezclados se ignita en un horno de encendido, y luego se queman desde la parte superior hacia abajo por la presión de succión del fondo de la bandeja.
- ⏱️ El proceso de sinterización es continuo, con la bandeja moviendo los materiales hacia adelante y permitiendo la operación continua.
- 🌡️ La temperatura del gas de escape se monitorea en el centro de control, y cuando más del 70% del proceso de sinterización ha progresado, la temperatura del gas de escape aumenta rápidamente, indicando que todo el humedad en los materiales se ha evaporado.
- 🔧 Una vez que el mineral de sinterización ha sido quemado, se enfriará y se triturará para ser fácilmente transferido, y luego se clasificará y se almacenará para su uso en el alto horno.
Q & A
¿Cuál es el propósito principal de la planta de sinterización en la industria del acero?
-El propósito principal de la planta de sinterización es procesar materiales de origen fino, inferiores a 10 milímetros, en un mineral de hierro grueso listo para ser cargado en un alto horno.
¿Qué es el tamaño de grano adecuado del mineral de hierro requerido para un alto horno?
-El tamaño de grano adecuado del mineral de hierro para un alto horno es superior a 10 milímetros.
¿Cuáles son las tres instalaciones principales en la planta de sinterización?
-Las tres instalaciones principales en la planta de sinterización son: la instalación de manejo de materiales, la instalación de sinterización y la instalación de trituración.
¿Qué es la función de la instalación de manejo de materiales en la planta de sinterización?
-La instalación de manejo de materiales almacena y descarga los materiales transferidos desde el patio de materiales.
¿Cuál es la función de la instalación de sinterización en la planta?
-La instalación de sinterización produce el mineral de hierro sinterizado real.
¿Qué hace la instalación de trituración en la planta de sinterización?
-La instalación de trituración tritura, tamiza y transporta el mineral de hierro sinterizado producido.
¿Cuál es el papel de los electrostaticos de precipitación (ESP) en la planta de sinterización?
-Los electrostaticos de precipitación recolectan el polvo generado en el proceso de sinterización, en la cribado y en la trituración de equipos, y en el equipo de trituración de combustible.
¿Qué materiales se utilizan como combustible en la planta de sinterización?
-El antracita y el coque se utilizan como combustibles en la planta de sinterización, especialmente el antracita y el coque que no están disponibles para un alto horno y una planta de coque debido a su tamaño de grano pequeño.
¿Cómo se mezclan los materiales en la planta de sinterización para producir el mineral de hierro requerido para el alto horno?
-Se mezclan los materiales y cada material auxiliar en una proporción adecuada en un tambor de mezcla para producir el mineral de hierro requerido para el alto horno.
¿Qué es el proceso de granulación y por qué es importante en la planta de sinterización?
-El proceso de granulación es cuando el coque, los materiales auxiliares, etc., se combinan con el mineral de hierro como centro, rotando en el tambor de re-rodaje. Este proceso es importante para obtener la permeabilidad necesaria para el proceso de sinterización.
¿Cuál es la función de la capa de tierra en el proceso de sinterización?
-La capa de tierra se extiende 100 milímetros de espesor en la parte inferior del tablero y los materiales mezclados se cargan sobre las capas de tierra. Esto previene que el mineral de hierro sinterizado se derrita y se pegue a la superficie del tablero durante el proceso de sinterización.
Outlines
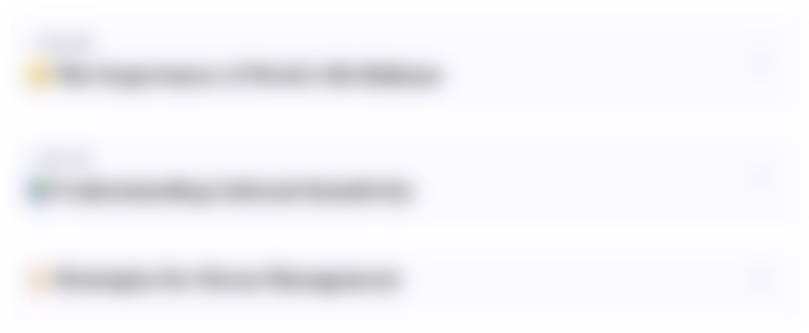
Dieser Bereich ist nur für Premium-Benutzer verfügbar. Bitte führen Sie ein Upgrade durch, um auf diesen Abschnitt zuzugreifen.
Upgrade durchführenMindmap
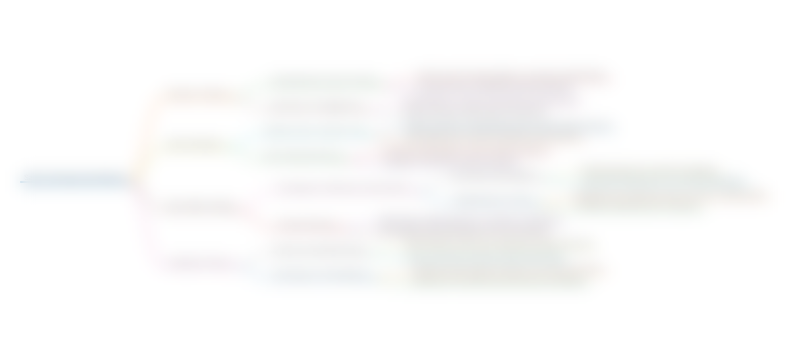
Dieser Bereich ist nur für Premium-Benutzer verfügbar. Bitte führen Sie ein Upgrade durch, um auf diesen Abschnitt zuzugreifen.
Upgrade durchführenKeywords
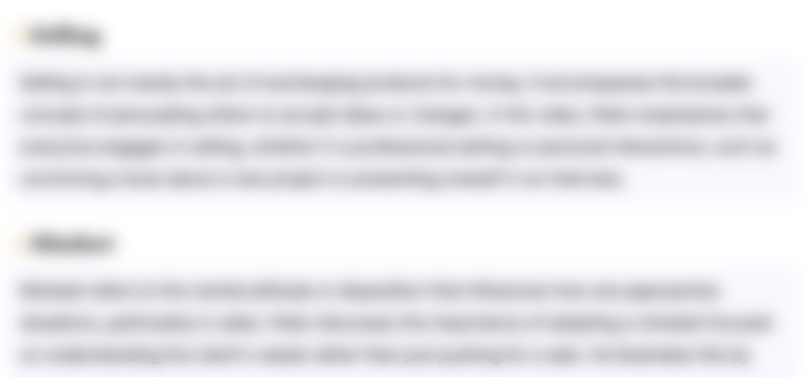
Dieser Bereich ist nur für Premium-Benutzer verfügbar. Bitte führen Sie ein Upgrade durch, um auf diesen Abschnitt zuzugreifen.
Upgrade durchführenHighlights
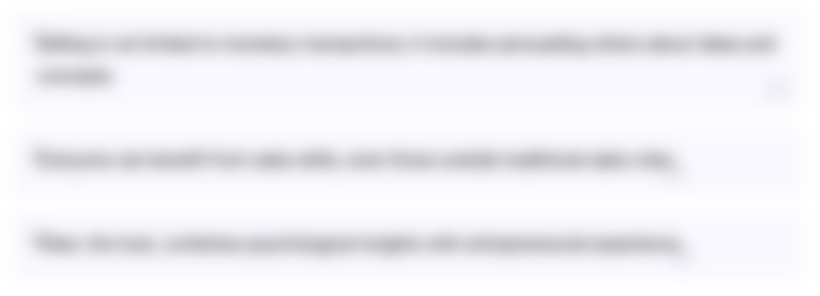
Dieser Bereich ist nur für Premium-Benutzer verfügbar. Bitte führen Sie ein Upgrade durch, um auf diesen Abschnitt zuzugreifen.
Upgrade durchführenTranscripts
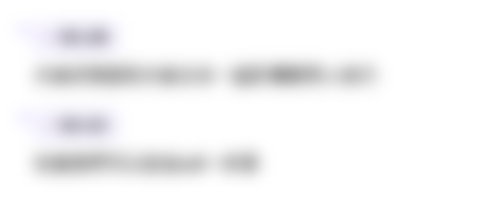
Dieser Bereich ist nur für Premium-Benutzer verfügbar. Bitte führen Sie ein Upgrade durch, um auf diesen Abschnitt zuzugreifen.
Upgrade durchführenWeitere ähnliche Videos ansehen

Construcción de un transformador eléctrico - Build a electric transformer
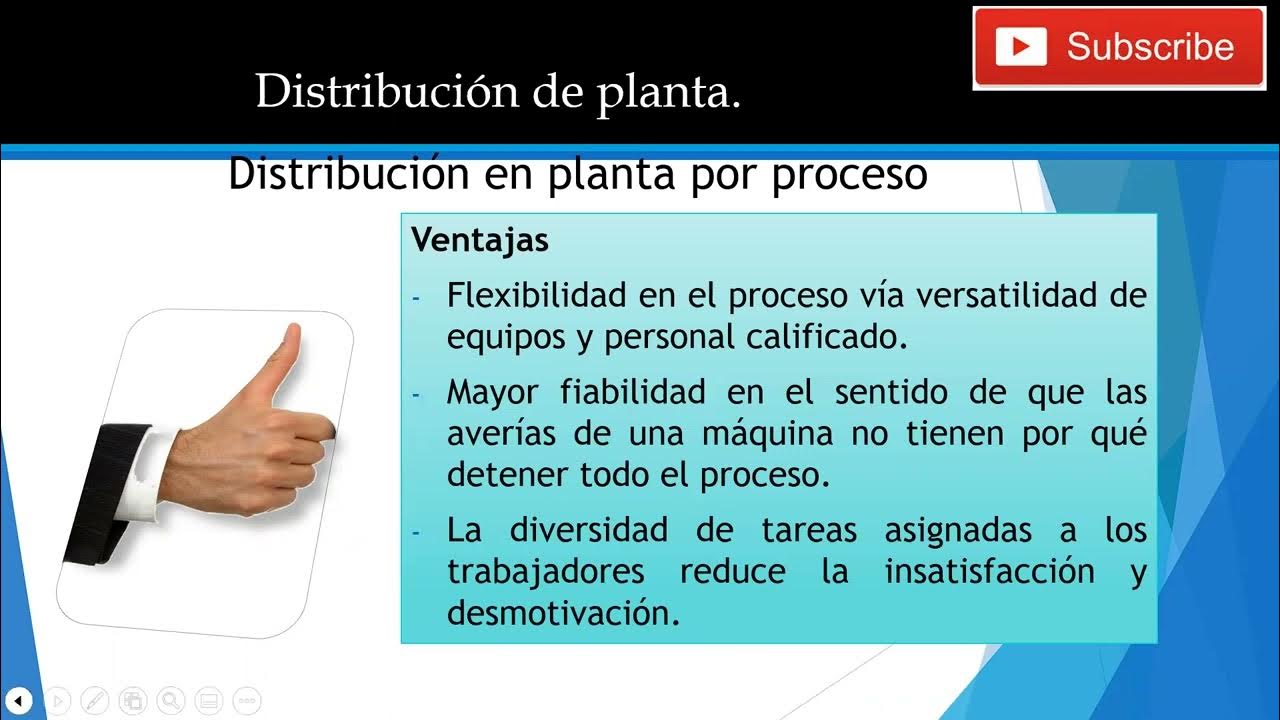
Definición del layout tipos de distribución de planta- Gestión de operaciones

Cómo se hacen los antibióticos - Laboratorios Bagó
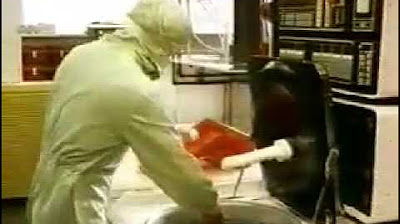
Tecnología y Producción de Circuitos Integrados (en español)

Copia de Proceso del Acero AHMSA Español

Procesos AHMSA 2022
5.0 / 5 (0 votes)