Center Drilling, Drilling and Countersinking Video
Summary
TLDRThis video demonstrates the proper technique for drilling a hole. It covers steps like positioning the machine, using a center drill to ensure accuracy, tightening the drill chuck with a chuck key, and setting the appropriate RPM for different tools. The video emphasizes safety, such as removing the chuck key to avoid hazards, and highlights the importance of using a countersink tool to clean up rough edges after drilling. The next video will discuss tapping the hole for threading, providing a well-rounded guide for common machining tasks.
Takeaways
- 🔧 Proper hole drilling starts by positioning the machining table accurately after edge-finding and compensating for the edge finder.
- 📏 The user moves the table 750 thousandths of an inch on both the x and y axes to position the drilling location.
- 🛠️ A center drill is used first because it's short, rigid, and sharpened differently from regular drills, preventing the drill from wandering.
- 🔩 A chuck key is used to tighten the drill chuck after inserting the center drill, and it's crucial to remove the key to avoid safety hazards.
- ⚙️ Center drills run at a high RPM (1000 RPM) and are typically used for precision starting before the main drilling operation.
- 👨🔧 The process involves gently 'pecking' the center drill into the material rather than applying full pressure at once.
- 🚀 Once the center drilling is complete, a quarter-inch drill is inserted into the chuck, and the RPM is adjusted to 1070 for optimal drilling.
- 💧 Coolant, like water-soluble petroleum, is sometimes sprayed when drilling for lubrication, though it may not be necessary for small projects.
- 🔨 After drilling, a countersink tool is used to remove burrs and create a clean, chamfered edge around the hole, typically at 90 degrees.
- 🧰 Drilling is a common operation in many mechanical industries, and the next step in this process would be to tap threads into the drilled hole.
Q & A
What is the first step when preparing to drill a hole?
-The first step is to position the machining table to the desired location and compensate for the edge finder to ensure accurate placement.
Why is it important to start drilling with a center drill?
-A center drill is short and rigid, allowing it to start the hole precisely in the desired location. It avoids the wandering that can occur with a standard drill bit, ensuring accuracy.
What is a chisel point, and why is it problematic for starting a hole?
-The chisel point is where the cutting flutes of a drill bit meet, and it tends to wander when starting a hole, leading to imprecise drilling. That's why it's better to start with a center drill.
What should be done after securing a drill or center drill into the chuck?
-After securing the tool into the drill chuck with a chuck key, it is very important to remove the chuck key to avoid creating a safety hazard as it can fly out when the spindle spins.
At what RPM should standard center drills be run?
-Standard center drills should typically run at around 1000 RPMs.
What is the recommended drilling technique once the center drill is in place?
-It's recommended to use a pecking motion rather than applying full pressure to avoid damaging the tool and to achieve a cleaner start for the hole.
What is the purpose of using a countersink after drilling a hole?
-A countersink is used to remove any burrs or rough edges around the hole by creating a slight bevel or chamfer, resulting in a clean surface.
How should the RPM be adjusted when using a countersink tool?
-When using a countersink, the RPM should be lowered to about 600 RPMs since countersinks generally have a larger diameter than drill bits.
What safety precaution should always be taken before starting the spindle?
-Always ensure that the chuck key is removed from the chuck before starting the spindle to avoid potential injury from the key being dislodged while the spindle spins.
Why is coolant sometimes applied during the drilling process?
-Coolant is applied to prevent overheating, particularly during large or extended drilling tasks. However, for smaller projects, it may not be necessary.
Outlines
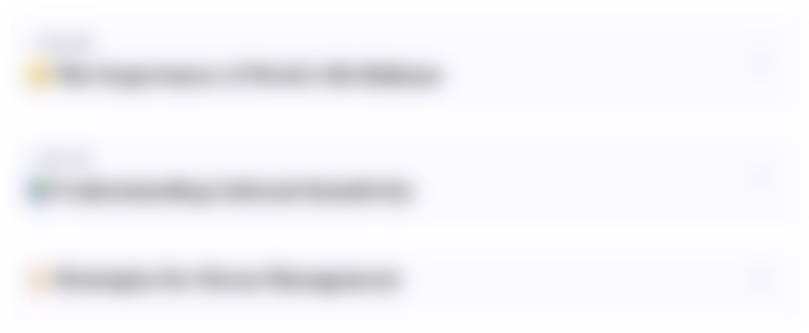
Dieser Bereich ist nur für Premium-Benutzer verfügbar. Bitte führen Sie ein Upgrade durch, um auf diesen Abschnitt zuzugreifen.
Upgrade durchführenMindmap
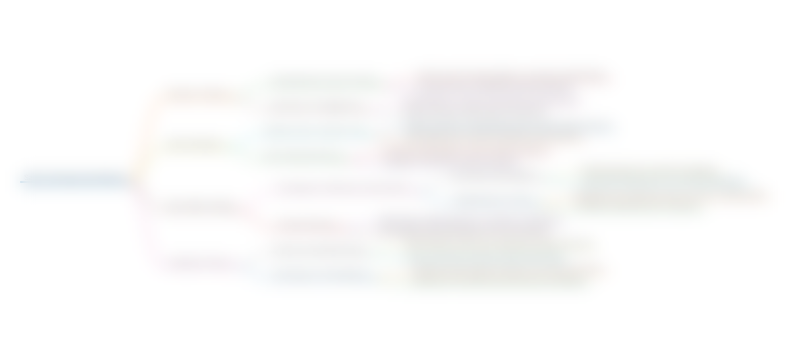
Dieser Bereich ist nur für Premium-Benutzer verfügbar. Bitte führen Sie ein Upgrade durch, um auf diesen Abschnitt zuzugreifen.
Upgrade durchführenKeywords
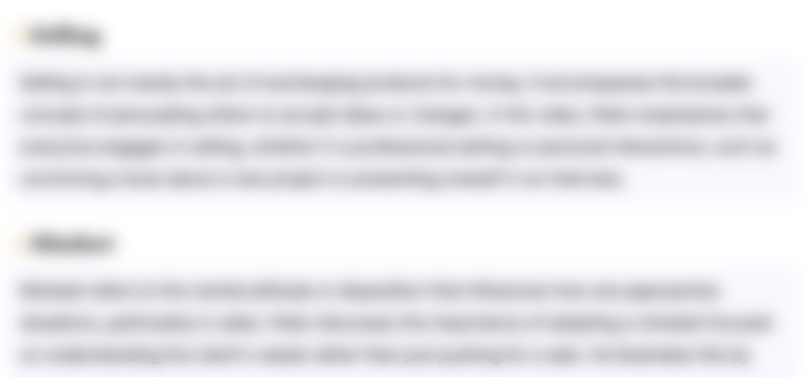
Dieser Bereich ist nur für Premium-Benutzer verfügbar. Bitte führen Sie ein Upgrade durch, um auf diesen Abschnitt zuzugreifen.
Upgrade durchführenHighlights
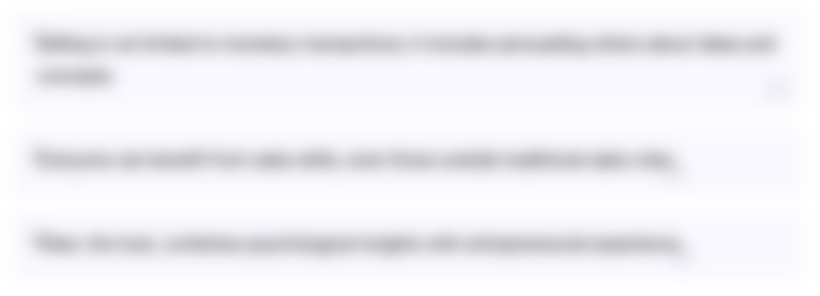
Dieser Bereich ist nur für Premium-Benutzer verfügbar. Bitte führen Sie ein Upgrade durch, um auf diesen Abschnitt zuzugreifen.
Upgrade durchführenTranscripts
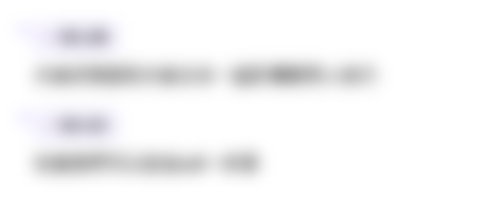
Dieser Bereich ist nur für Premium-Benutzer verfügbar. Bitte führen Sie ein Upgrade durch, um auf diesen Abschnitt zuzugreifen.
Upgrade durchführen5.0 / 5 (0 votes)