#MH004 Plant Layout, Principles of plant layout & Types of layout.
Summary
TLDRThis video from Academic Gain Tutorials provides an in-depth understanding of plant layout, covering key principles such as minimum movement, space utilization, flexibility, and safety. It also explains the four main types of layouts—process, product, combination, and fixed position—detailing their advantages and disadvantages. The video is part of a course on materials handling and maintenance engineering, and aims to make academic studies easier by exploring topics like production efficiency and layout design. Future videos will address material flow patterns and the relationship between plant layout and material handling.
Takeaways
- 🌿 **Plant Layout Definition**: Optimum arrangement of facilities including personnel, equipment, storage, and services within a plant structure.
- 🔄 **Principle of Minimum Movement**: Materials and labor should be moved over the shortest distances to save on transportation and handling costs.
- 🏠 **Principle of Space Utilization**: Effective use of all available space, both horizontally and vertically, to maximize efficiency.
- 🔧 **Principle of Flexibility**: The layout should adapt to changes due to expansion or technological advancements.
- 🔗 **Principle of Interdependence**: Operations that depend on each other should be located close together to minimize product travel.
- 🔐 **Principle of Overall Integration**: All plant facilities should be integrated into a single operating unit to reduce production costs.
- 🛡️ **Principle of Safety**: The layout should ensure the comfort and safety of workers.
- ⚙️ **Principle of Smooth Flow**: The layout should be designed to reduce work bottlenecks and ensure continuous workflow.
- 💰 **Principle of Economy**: The layout should aim for economic efficiency in terms of fixed asset investment.
- 👀 **Principle of Supervision**: Effective layout facilitates supervision over workers.
- 😃 **Principle of Satisfaction**: A good layout boosts employee morale and work satisfaction.
- 🛠️ **Process Layout**: Machines performing similar operations are grouped together, such as all lathes or milling machines in one area.
- 🏭 **Product Layout**: Machines are arranged in the sequence of product operations, typically producing one type of product.
- 🔄 **Combination Layout**: A mix of process and product layouts, suitable for complex products like refrigerators.
- 🚧 **Fixed Position Layout**: Materials or major components remain fixed, and all tools, machinery, and materials are brought to them, as seen in bridge or airplane construction.
Q & A
What is plant layout?
-Plant layout refers to the optimum arrangement of facilities, including personnel, operating equipment, storage space, material handling equipment, and all other supporting services, along with the design of the best structure to contain all these facilities.
What are the general principles of plant layout?
-The general principles of plant layout include minimum movement, space utilization, flexibility, interdependence, overall integration, safety, smooth flow, economy, supervision, and satisfaction.
How does the principle of minimum movement contribute to plant layout?
-The principle of minimum movement ensures that materials and labor are moved over the shortest distances, saving on transportation and material handling costs and time.
What is the significance of the principle of flexibility in plant layout?
-The principle of flexibility allows the plant layout to adapt to changes required by expansion or technological development, ensuring the layout can evolve with the production needs.
Can you explain the concept of interdependence in plant layout?
-The principle of interdependence suggests that operations and processes that depend on each other should be located close to each other to minimize the travel of products and improve efficiency.
What is a process layout or functional layout?
-In a process layout, machines that perform similar types of operations are grouped together. This layout is suitable for workshops where a variety of operations are performed on different products.
How does a product layout or line layout differ from a process layout?
-A product layout arranges all the processing equipment and machines according to the sequence of operations of the product, typically used when producing one type of product in an operating area.
What is a combination layout and when is it used?
-A combination layout, also known as a hybrid or mixed type of layout, combines process layout for various operations and product layout for final assembly. It is used in manufacturing processes that require both types of layouts, such as refrigerator manufacturing.
What are the advantages of a fixed position layout?
-Fixed position layout involves the least movement of materials, provides maximum flexibility for changes in product and process, and allows for the handling of large or immovable products like bridges, ships, or large machinery.
What are the disadvantages of using a process layout?
-Disadvantages of a process layout include backtracking and long movements of materials, reduced material handling efficiency, difficulty in production planning and control, and the need for more space.
How does a product layout improve material handling efficiency?
-A product layout improves material handling efficiency by arranging machines in a straight flow according to the sequence of operations, which simplifies material handling systems and reduces material handling costs.
Outlines
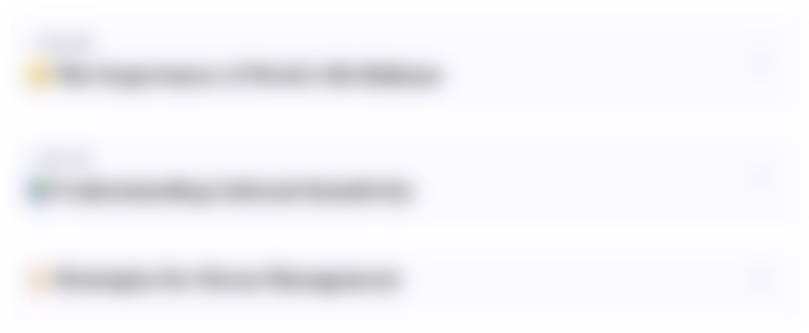
Dieser Bereich ist nur für Premium-Benutzer verfügbar. Bitte führen Sie ein Upgrade durch, um auf diesen Abschnitt zuzugreifen.
Upgrade durchführenMindmap
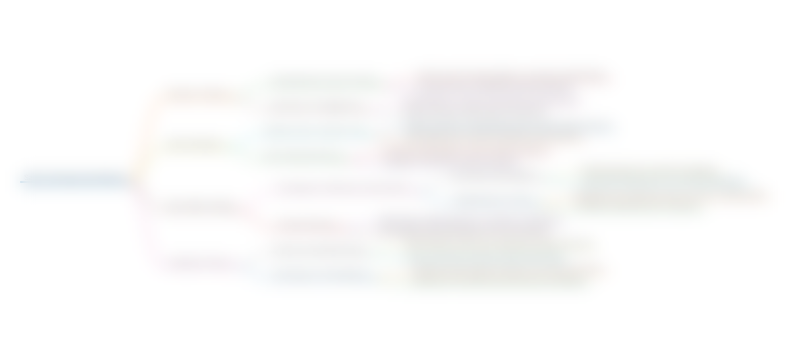
Dieser Bereich ist nur für Premium-Benutzer verfügbar. Bitte führen Sie ein Upgrade durch, um auf diesen Abschnitt zuzugreifen.
Upgrade durchführenKeywords
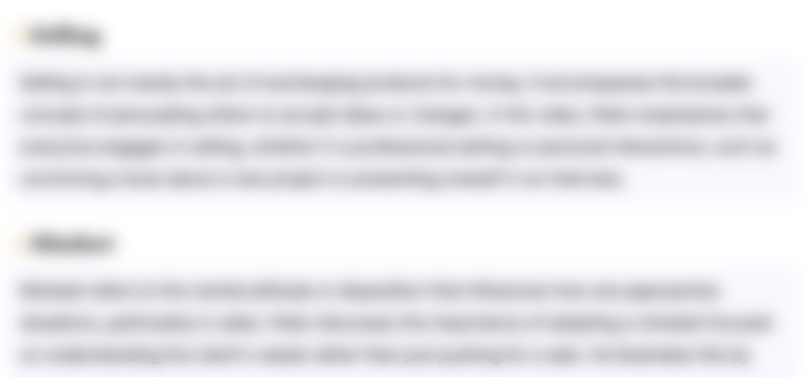
Dieser Bereich ist nur für Premium-Benutzer verfügbar. Bitte führen Sie ein Upgrade durch, um auf diesen Abschnitt zuzugreifen.
Upgrade durchführenHighlights
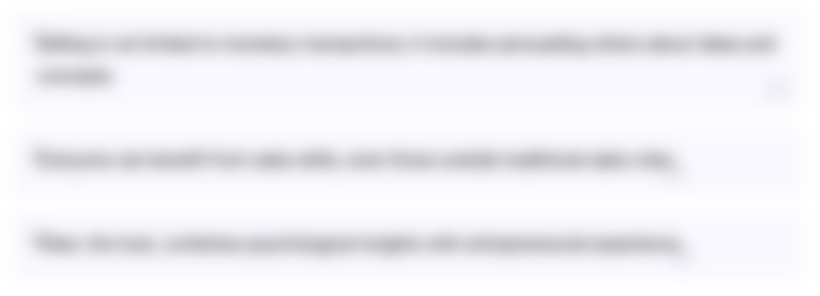
Dieser Bereich ist nur für Premium-Benutzer verfügbar. Bitte führen Sie ein Upgrade durch, um auf diesen Abschnitt zuzugreifen.
Upgrade durchführenTranscripts
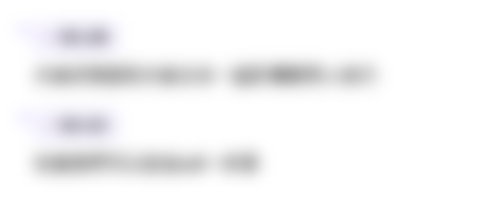
Dieser Bereich ist nur für Premium-Benutzer verfügbar. Bitte führen Sie ein Upgrade durch, um auf diesen Abschnitt zuzugreifen.
Upgrade durchführenWeitere ähnliche Videos ansehen
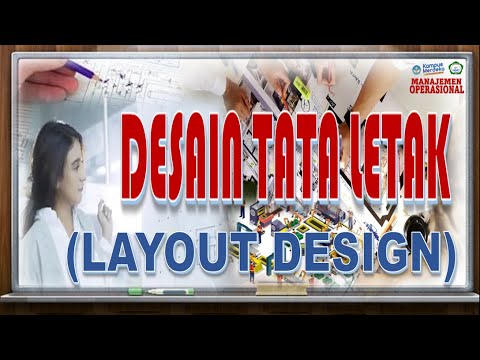
DESAIN TATA LETAK (LAYOUT DESIGN)

Manajemen Kantor - Layout Kantor
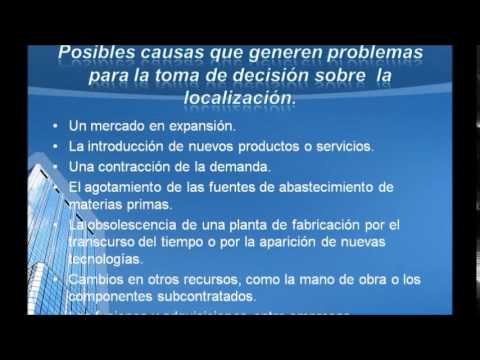
Distribución Y Localización De Planta

Lecture#0 Introduction to KiboCUBE Academy (KiboCUBE Academy)

Klasifikasi Virus / pengelompokan Virus . Bab.virus biologi Sma kelas 10
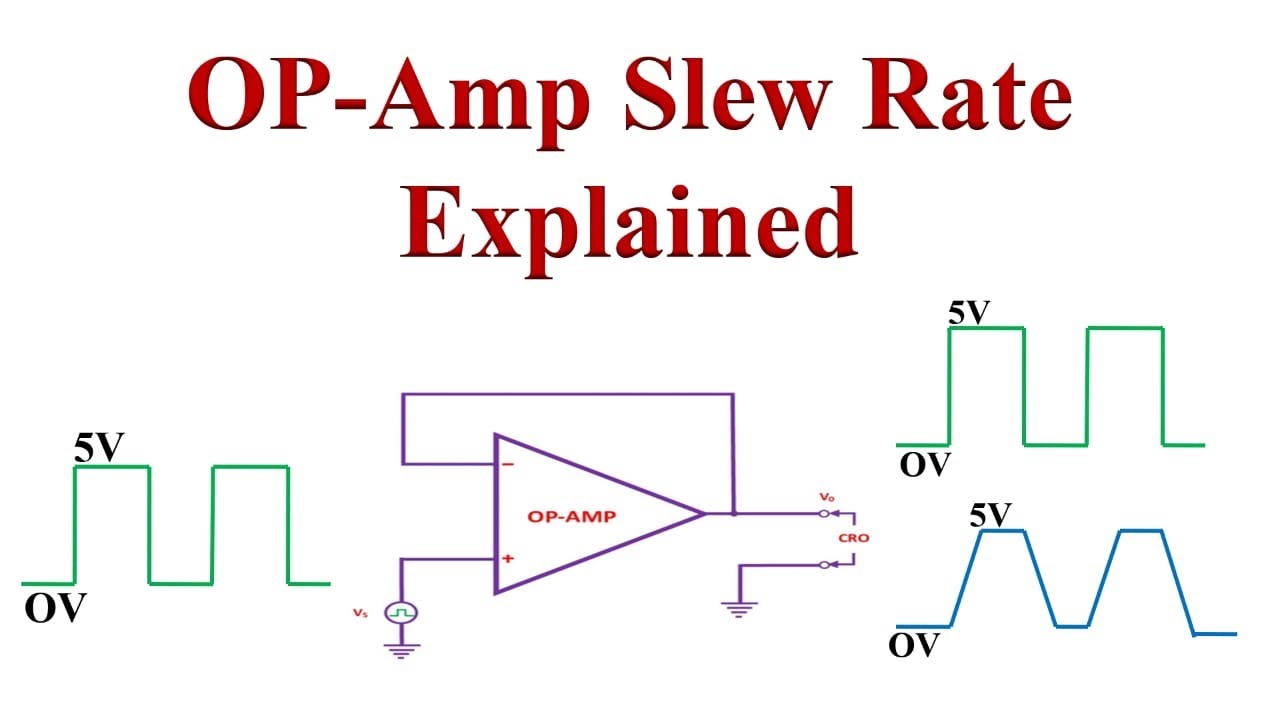
OP-Amp Slew Rate With Examples and Solutions (Operational Amplifier)
5.0 / 5 (0 votes)