Asset Management Event - Part 2
Summary
TLDRThis video introduces Rockwell Automation's comprehensive asset management and repair services, emphasizing the benefits of their warranty tracking, inventory management, and recertification programs. It highlights how Rockwell helps customers manage repairs, track assets, and save costs through analytics and regular reports. The inventory recertification program addresses issues with suspect inventory by testing and remanufacturing parts to like-new conditions, with a one-year warranty. The program is cost-effective, ensuring that parts are reliable and functional. The video showcases Rockwell's approach to managing spare parts, from initial assessment to final certification.
Takeaways
- 😀 Rockwell Automation offers a 2-year in-service warranty on all products that are repaired.
- 😀 Asset tracking is supported by dedicated personnel who monitor repair progress and provide valuable analytics.
- 😀 Rockwell uses a barcode-like technology to track repairs and help manage inventory efficiently.
- 😀 Reports are generated on a bi-monthly or quarterly basis to provide insights on repair costs, asset status, and potential savings.
- 😀 A long-term partnership with Rockwell Automation includes an embedded person on-site to assist with repair, storage, and lifecycle management.
- 😀 'Suspect inventory' refers to parts that have been in storage for extended periods, often with unknown conditions, such as broken seals or environmental exposure.
- 😀 Rockwell Automation provides an inventory recertification program to test and verify the operational status of suspect inventory.
- 😀 Parts that pass the recertification process are returned with a one-year warranty and are often upgraded to like-new condition, including firmware updates.
- 😀 The recertification program has a flat fee for most items, with different pricing for drives based on their horsepower rating.
- 😀 If parts fail recertification, they can be remanufactured, scrapped, or disposed of, depending on the customer’s preference.
- 😀 The recertification program helps eliminate the uncertainty around stored parts and ensures they are operational when needed.
Q & A
What is the in-service warranty provided by Rockwell for repaired products?
-Rockwell offers a 2-year in-service warranty for all products that have been repaired, ensuring that the repaired items are covered for a longer period after service.
How does Rockwell assist in tracking the status of repairs and assets?
-Rockwell assigns a dedicated Champ person to track the assets, helping customers stay informed about the status of repairs, what’s in storage, and the costs associated with each asset.
What is the purpose of the reports provided by Rockwell on a bimonthly or quarterly basis?
-The reports are designed to help customers track their repair activity, understand their spending, and identify cost savings opportunities. They also offer an overview of asset status and usage.
What kind of inventory management issues are highlighted in the script?
-The script highlights issues like suspect inventory, including parts stored for extended periods, parts exposed to environmental risks, or parts with broken seals, which may not be in optimal working condition.
What is the Inventory Re-certification Program offered by Rockwell?
-The Inventory Re-certification Program allows customers to send suspect inventory to Rockwell for testing. If the parts pass testing, they are re-certified and returned with a 1-year in-service warranty.
What happens to inventory that fails the re-certification process?
-If inventory fails the re-certification, customers have the option to either scrap the item or request remanufacturing, ensuring that even non-functional items can be restored to working condition.
How does Rockwell ensure the re-certification process is fair and transparent?
-The re-certification program is offered at a flat fee for most items. However, drives are priced based on their horsepower. All repaired and re-certified items are returned with a warranty if they pass the re-certification process.
What is the significance of suspect inventory in store rooms?
-Suspect inventory, which consists of parts stored for long periods without proper testing or care, can be a major issue. Such inventory may not be in working condition, leading to potential failures or unplanned downtime.
What can customers do with parts that have been in a store room for an extended period?
-Customers can have these parts sent for re-certification to ensure they are operational and functional. If the parts are not working, they can either be scrapped or remanufactured to restore them to a like-new condition.
What is the main benefit of the Inventory Re-certification Program for businesses?
-The primary benefit is that it helps businesses ensure that their spare parts are operational, avoiding the risk of using faulty or outdated components. Additionally, the re-certified parts come with a warranty, providing added peace of mind.
Outlines
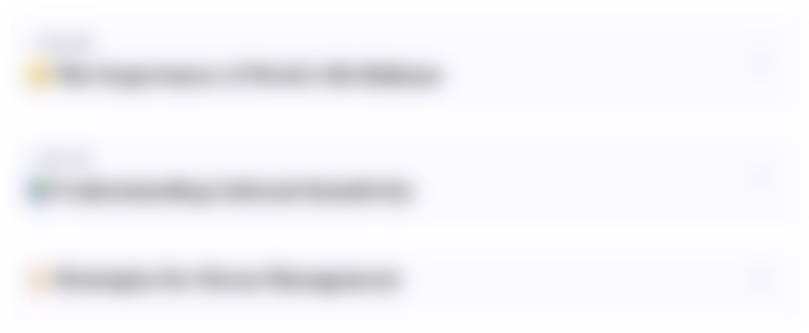
هذا القسم متوفر فقط للمشتركين. يرجى الترقية للوصول إلى هذه الميزة.
قم بالترقية الآنMindmap
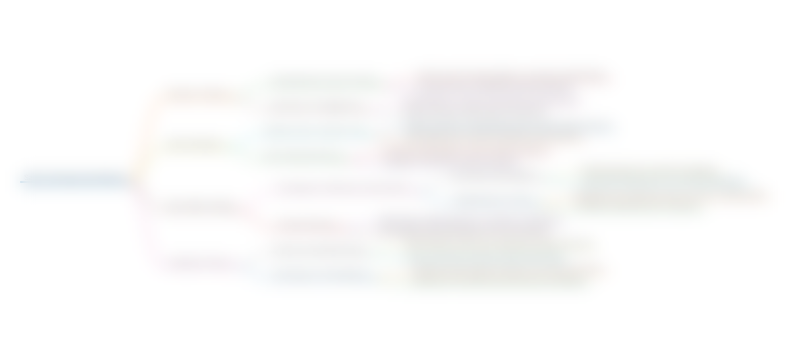
هذا القسم متوفر فقط للمشتركين. يرجى الترقية للوصول إلى هذه الميزة.
قم بالترقية الآنKeywords
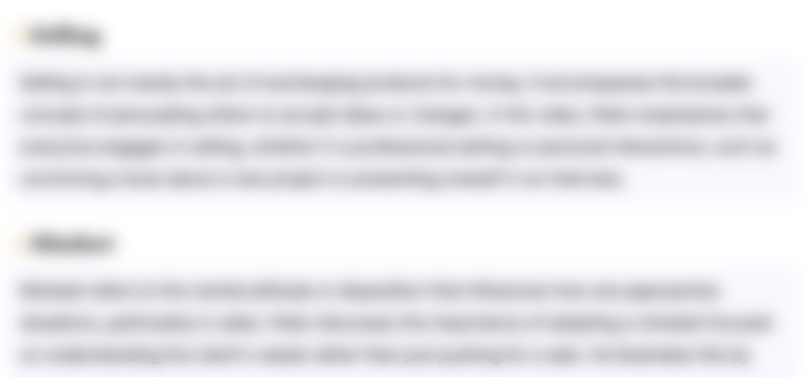
هذا القسم متوفر فقط للمشتركين. يرجى الترقية للوصول إلى هذه الميزة.
قم بالترقية الآنHighlights
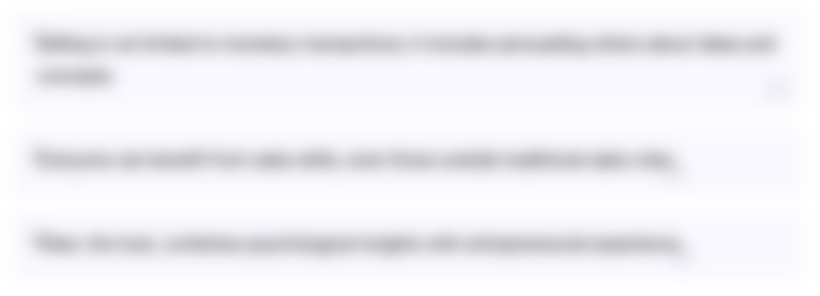
هذا القسم متوفر فقط للمشتركين. يرجى الترقية للوصول إلى هذه الميزة.
قم بالترقية الآنTranscripts
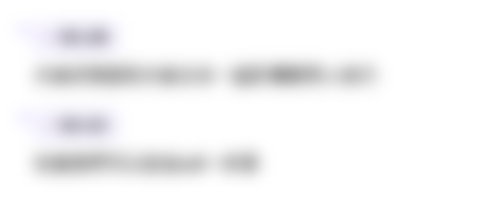
هذا القسم متوفر فقط للمشتركين. يرجى الترقية للوصول إلى هذه الميزة.
قم بالترقية الآنتصفح المزيد من مقاطع الفيديو ذات الصلة

Inventory+

What is Asset management? Importance of Asset management | Asset management softwares.
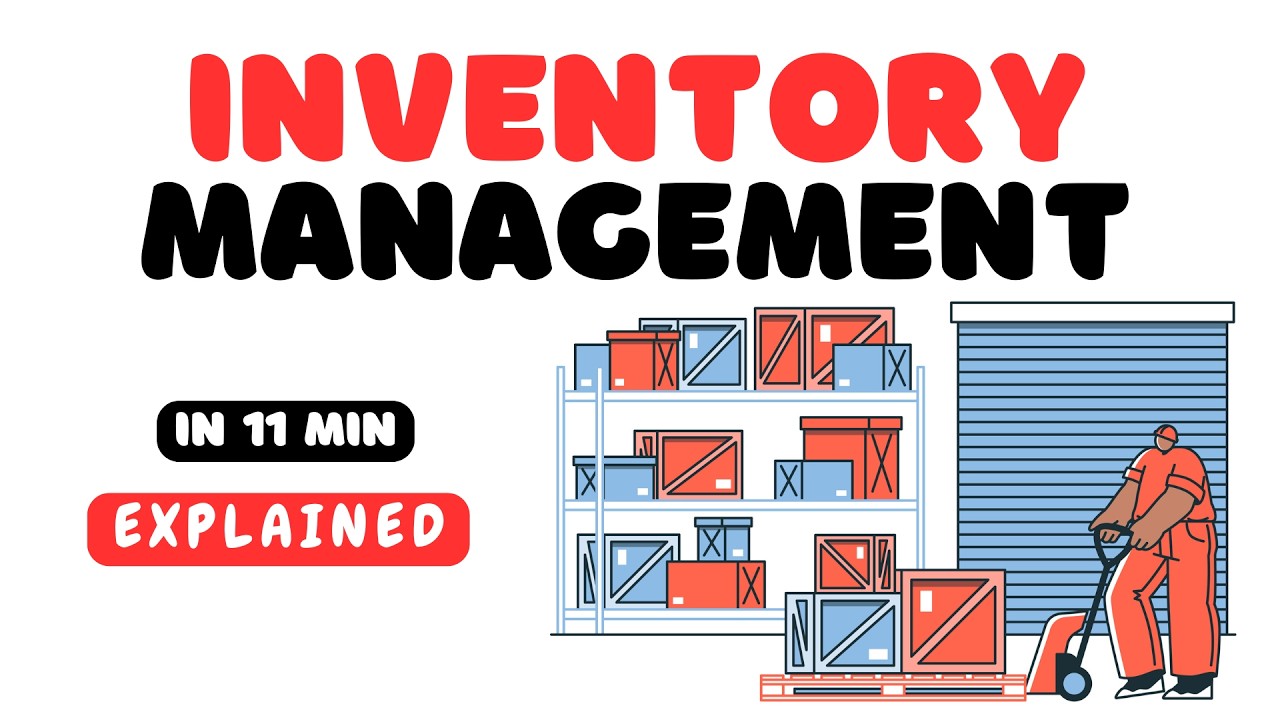
Inventory Management in 11 minutes

WHAT IS A CMMS ? Computerized Maintenance Management System
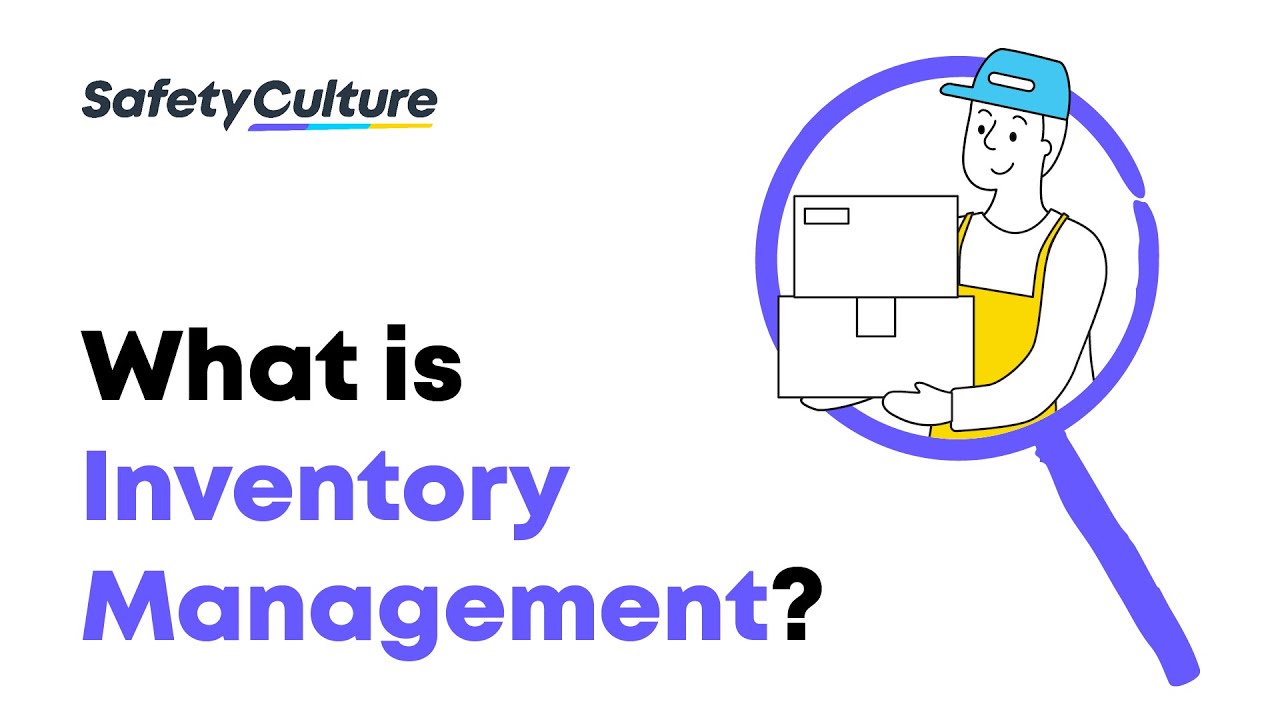
What is Inventory Management? | Inventory Types and Major Challenges | SafetyCulture

Cara Mudah Belajar Housekeeping : Formulir di Room Section
5.0 / 5 (0 votes)