Powder Metallurgy Touches Your Life, Part 2
Summary
TLDRThe video explains the process of powder metallurgy (PM), starting with the production of metal powders and the various methods used to create alloys. The powder is then compacted into parts using highly sophisticated presses before being sintered in a furnace to bond the metal particles. PM offers the advantage of near-net-shape forming, reducing the need for additional processing. The video also highlights the benefits of PM in terms of design flexibility, cost-efficiency, and part performance, encouraging designers to consult PM fabricators for optimal results. PM components are already used in various industries, enhancing performance and reliability.
Takeaways
- 😀 Metal powder is produced through various processes depending on the metal and the desired microstructures and properties.
- 😀 The powder arrives in bulk containers and is processed into alloys using techniques like pre-alloying or diffusion bonding.
- 😀 A small amount of lubricant is added to reduce friction during the process, ensuring smoother operation.
- 😀 The powder is delivered to a press, where it is precisely measured and loaded into a custom-designed die.
- 😀 Compacting presses, with forces ranging from 15 to 1,600 tons, are used to shape the powder into the desired component with high precision.
- 😀 The compacted part has 'green strength', which allows it to be handled before the sintering process.
- 😀 The sintering furnace gradually increases temperature to bond metal particles on an atomic level, achieving desired metallurgical properties.
- 😀 Powder metallurgy (PM) is considered a 'green technology' because it often requires no further processing after sintering.
- 😀 PM parts can undergo additional finishing operations, such as plating, deburring, or heat treatment, to enhance their properties.
- 😀 PM components can be repressed or coined to modify their shape, density, or dimensional control.
- 😀 Close cooperation between part designers and PM fabricators is crucial to ensure design efficiency and avoid unnecessary costs or failures.
Q & A
What is the role of metal powder in powder metallurgy?
-Metal powder serves as the foundational material in powder metallurgy (PM). It is produced through various processes depending on the type of metal and the desired properties, then delivered to the fabricator’s location in bulk containers.
How are alloys created in powder metallurgy?
-Alloys in powder metallurgy are produced using techniques like pre-alloying elements in a molten state, diffusion bonding during the annealing stage, or mixing elements in special devices to achieve homogeneity.
Why is lubricant added to the metal powder?
-A small amount of lubricant is added to the metal powder to reduce frictional forces during the compaction process, ensuring smoother handling and processing of the powder.
What is the function of the dye in the powder metallurgy process?
-The dye, along with other tooling members like punches and core rods, defines the dimensions and shape of the final component by receiving a precisely measured charge of powder that is compacted into it.
What types of presses are used in powder metallurgy?
-Powder metallurgy uses compacting presses that can be mechanical or hydraulic. These presses exert forces ranging from around 15 tonnes to over 1,600 tonnes and are often computer-controlled for precise pressing motions.
What happens to the powder compact after it is pressed?
-After being pressed, the powder compact is ejected from the dye, retaining the appearance of the finished part and its green strength. It can be handled by an automated system or manually, then sent for sintering.
What is the role of the sintering furnace in powder metallurgy?
-The sintering furnace gradually heats the compacted part to remove lubricants and bond metal particles on an atomic level. This process imparts the desired metallurgical properties, such as strength, density, and surface finish.
How does powder metallurgy benefit the environment?
-Powder metallurgy is considered a green technology because it is a net-shaped forming process. In many cases, no further processing steps are needed after sintering, reducing material waste and energy consumption.
What secondary operations can be applied to powder metallurgy components?
-PM components can undergo various secondary operations, such as plating, deburring, furnace brazing, heat treatment, steam treating, and even repressing or coining to refine their properties or improve surface quality.
Why should designers consult with PM fabricators early in the design process?
-Consulting with PM fabricators early ensures that the component is designed to take full advantage of powder metallurgy's strengths, reducing the likelihood of costly mistakes like excessive tooling, product failures, or unnecessary secondary processes.
Outlines
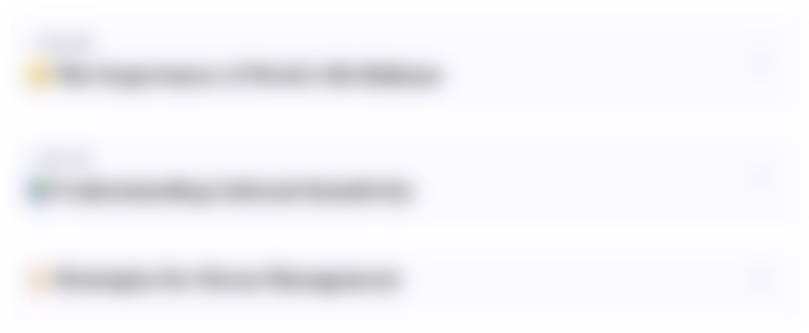
هذا القسم متوفر فقط للمشتركين. يرجى الترقية للوصول إلى هذه الميزة.
قم بالترقية الآنMindmap
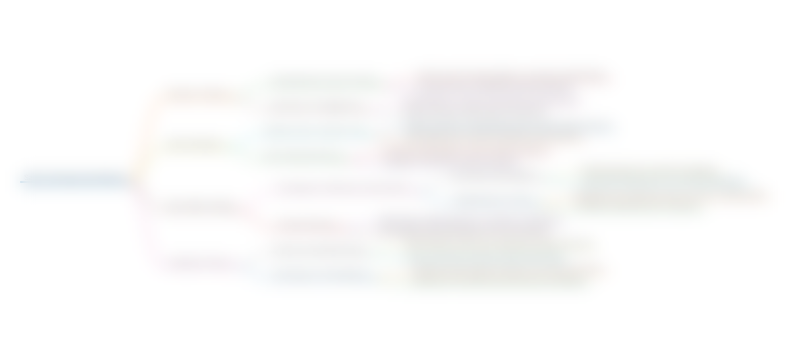
هذا القسم متوفر فقط للمشتركين. يرجى الترقية للوصول إلى هذه الميزة.
قم بالترقية الآنKeywords
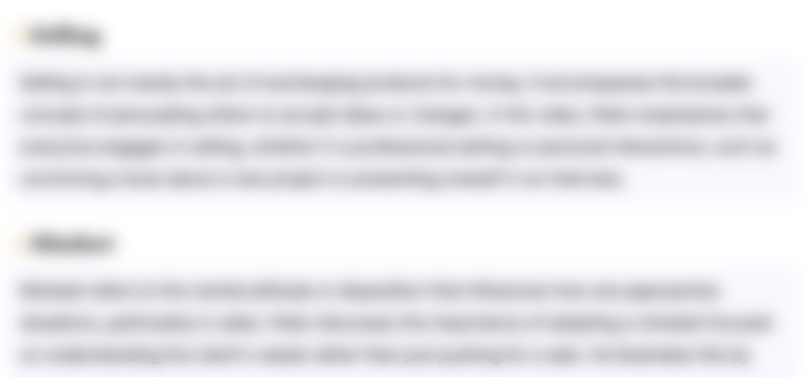
هذا القسم متوفر فقط للمشتركين. يرجى الترقية للوصول إلى هذه الميزة.
قم بالترقية الآنHighlights
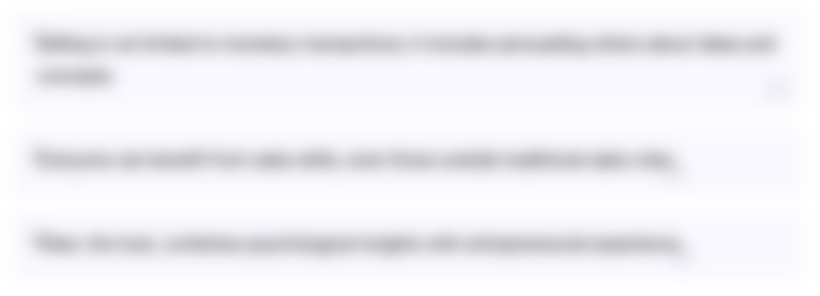
هذا القسم متوفر فقط للمشتركين. يرجى الترقية للوصول إلى هذه الميزة.
قم بالترقية الآنTranscripts
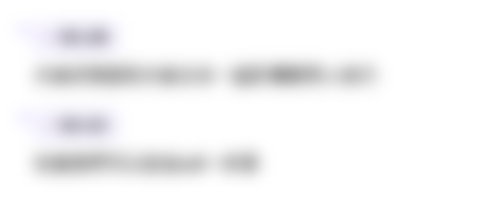
هذا القسم متوفر فقط للمشتركين. يرجى الترقية للوصول إلى هذه الميزة.
قم بالترقية الآن5.0 / 5 (0 votes)