Chapter 14. Material Requirements Planning (MRP) and ERP - Part 3
Summary
TLDRThis video explains the process of Material Requirements Planning (MRP), focusing on key concepts like safety stock, gross requirements, net requirements, and lead times. It details how to calculate production and inventory needs, adjust for on-hand inventory and scheduled receipts, and determine the correct timing for orders and production starts. The script also covers the dependencies between components and their parent items, providing a comprehensive overview of how to plan and manage inventory effectively in manufacturing.
Takeaways
- 😀 Safety stock is additional inventory held to buffer against unexpected spikes in demand, ensuring smooth production or sales operations.
- 😀 Gross requirement planning helps forecast the overall demand for materials or products in a specific period, factoring in safety stock.
- 😀 On hand inventory refers to the current stock available. This is subtracted from gross requirements to determine the actual net requirements.
- 😀 Net requirements are the actual quantity needed for production, after considering the on-hand inventory and any safety stock already in place.
- 😀 Schedule planning determines when orders should be placed or produced based on the lead time for the items involved, ensuring timely delivery.
- 😀 Lead time is the time required to procure or produce an item. It is critical for determining the timing of orders and production scheduling.
- 😀 Inventory management often involves complex dependencies between items. For example, component parts like B and C may be required to assemble item A.
- 😀 The relationship between parent and child items must be accounted for in the inventory planning, ensuring that all necessary components are ordered and available when needed.
- 😀 Order release timing is based on net requirements, ensuring that inventory arrives in time to meet demand, factoring in the lead time of each item.
- 😀 Safety stock and lead times should be carefully considered when planning inventory levels. This helps avoid stockouts and ensures sufficient stock for production.
Q & A
What is safety stock, and why is it important in inventory planning?
-Safety stock refers to extra inventory kept on hand to prevent stockouts due to unexpected increases in demand or delays in supply. It acts as a buffer to ensure that production or sales operations continue smoothly, even if demand spikes or supply disruptions occur.
How does safety stock affect gross requirement planning?
-When safety stock is accounted for, it should be added to the gross requirement planning. For example, if the original need is 50 units but there is a safety stock requirement, the total requirement would increase to cover both the planned and safety stock needs.
What is meant by 'Hello Kitty' in the context of inventory scheduling?
-'Hello Kitty' refers to the placement of inventory in the production schedule. It represents the specific items that need to be scheduled for production in future weeks. This concept helps ensure that inventory for upcoming periods is adequately planned and tracked.
What is the significance of low-level codes in Bill of Materials (BOM)?
-Low-level codes are used to indicate the level of components within a Bill of Materials (BOM). A component's low-level code helps determine when it should be scheduled for production based on its position in the BOM hierarchy. Components at level 0 are independent items, while others (e.g., B, C, D) depend on higher-level components.
How do 'on-hand' quantities influence the net requirements calculation?
-The 'on-hand' quantity refers to the stock available at any given time. It is subtracted from the gross requirements to determine the net requirements. If there is stock on hand, the net requirement will be lower, reducing the need for new orders or production.
What is a 'net requirement' in inventory management?
-A net requirement is the actual quantity needed for production after accounting for on-hand stock, scheduled receipts, and safety stock. It is the amount that must be ordered or produced to meet demand, ensuring there are no shortages.
How are order releases scheduled based on net requirements?
-Order releases are scheduled based on the net requirements, taking into account the lead time for production or procurement. For example, if the net requirement for a component is 40 units, and it has a 1-week lead time, the order should be released a week prior to the requirement date to ensure timely availability.
What is the importance of lead time in production planning?
-Lead time is the period between placing an order and receiving the materials. It is critical in determining when to release orders or start production. For example, if a component has a 2-week lead time, orders must be placed 2 weeks before the required delivery date to avoid delays.
How do multiple parents affect the scheduling of components in the BOM?
-When a component has multiple parents, its scheduling can be more complex. For instance, if component B is used by both A and C, the scheduling of B needs to consider the requirements from both A and C. This ensures that the component is available for all of its dependent products in time.
What is the role of 'project on hand' in the inventory planning process?
-'Project on hand' refers to the stock currently available in inventory that has not yet been used or allocated. It helps determine how much stock is available for future production or sales. This figure remains constant each week unless the stock is used or depleted.
Outlines
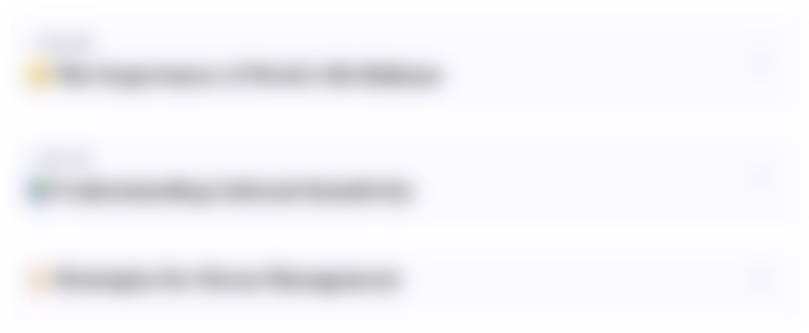
هذا القسم متوفر فقط للمشتركين. يرجى الترقية للوصول إلى هذه الميزة.
قم بالترقية الآنMindmap
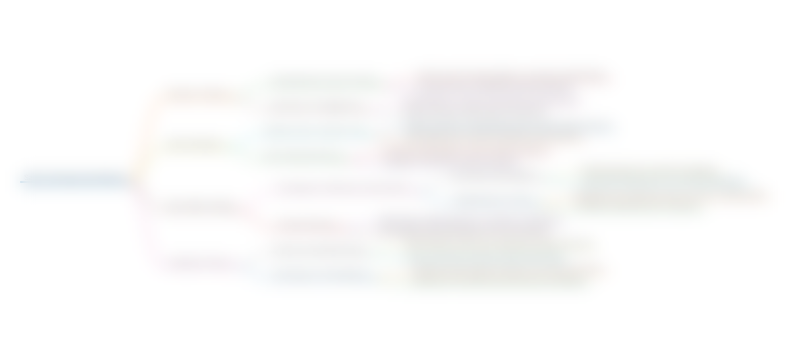
هذا القسم متوفر فقط للمشتركين. يرجى الترقية للوصول إلى هذه الميزة.
قم بالترقية الآنKeywords
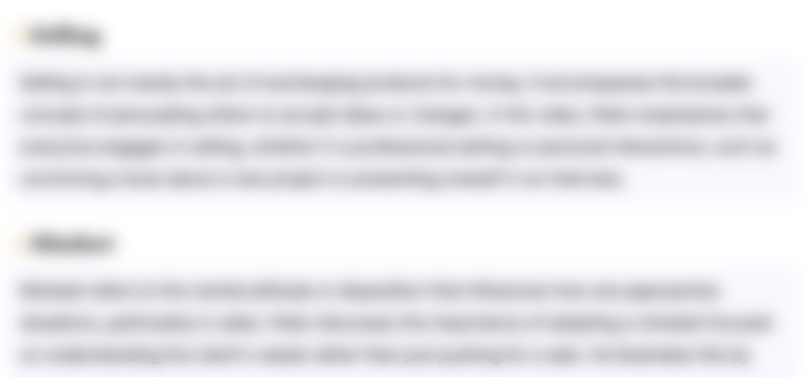
هذا القسم متوفر فقط للمشتركين. يرجى الترقية للوصول إلى هذه الميزة.
قم بالترقية الآنHighlights
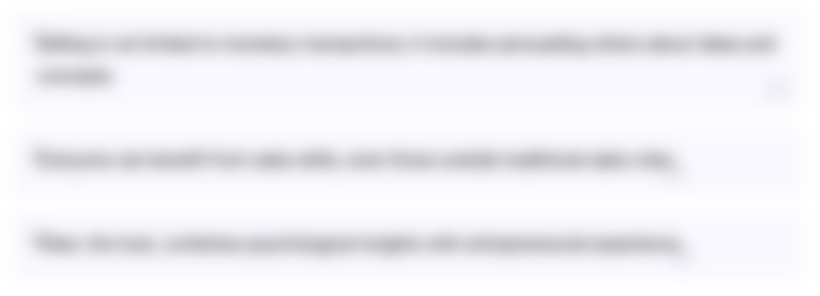
هذا القسم متوفر فقط للمشتركين. يرجى الترقية للوصول إلى هذه الميزة.
قم بالترقية الآنTranscripts
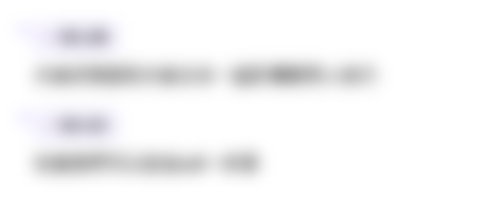
هذا القسم متوفر فقط للمشتركين. يرجى الترقية للوصول إلى هذه الميزة.
قم بالترقية الآنتصفح المزيد من مقاطع الفيديو ذات الصلة
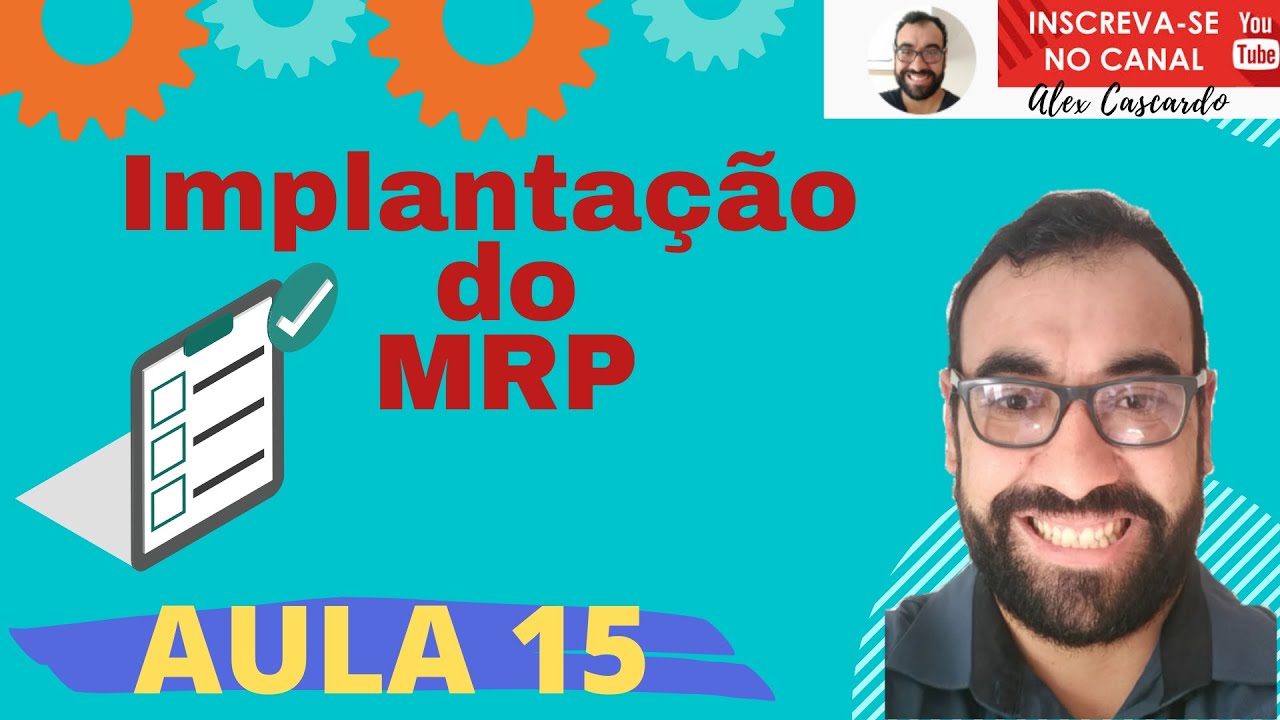
Planejamento e Controle da Produção # 15 – Implantação do MRP
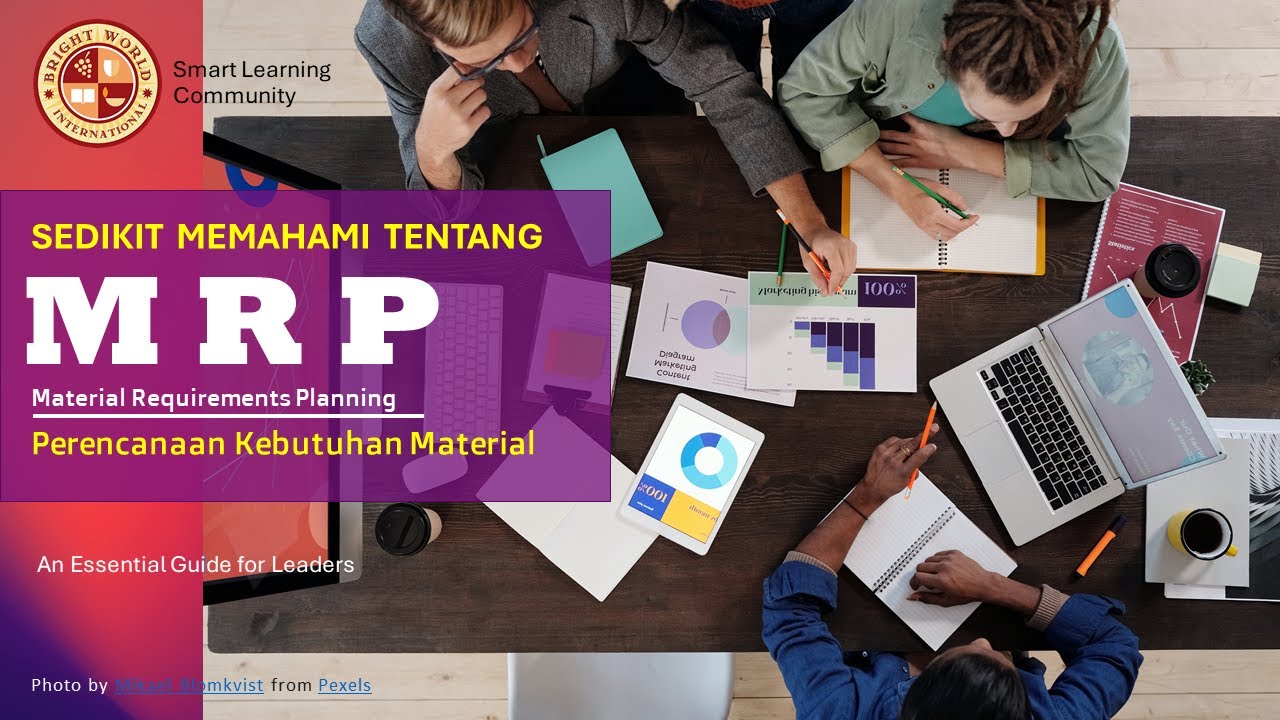
Memahami Perencanaan Kebutuhan Material untuk proses produksi ...
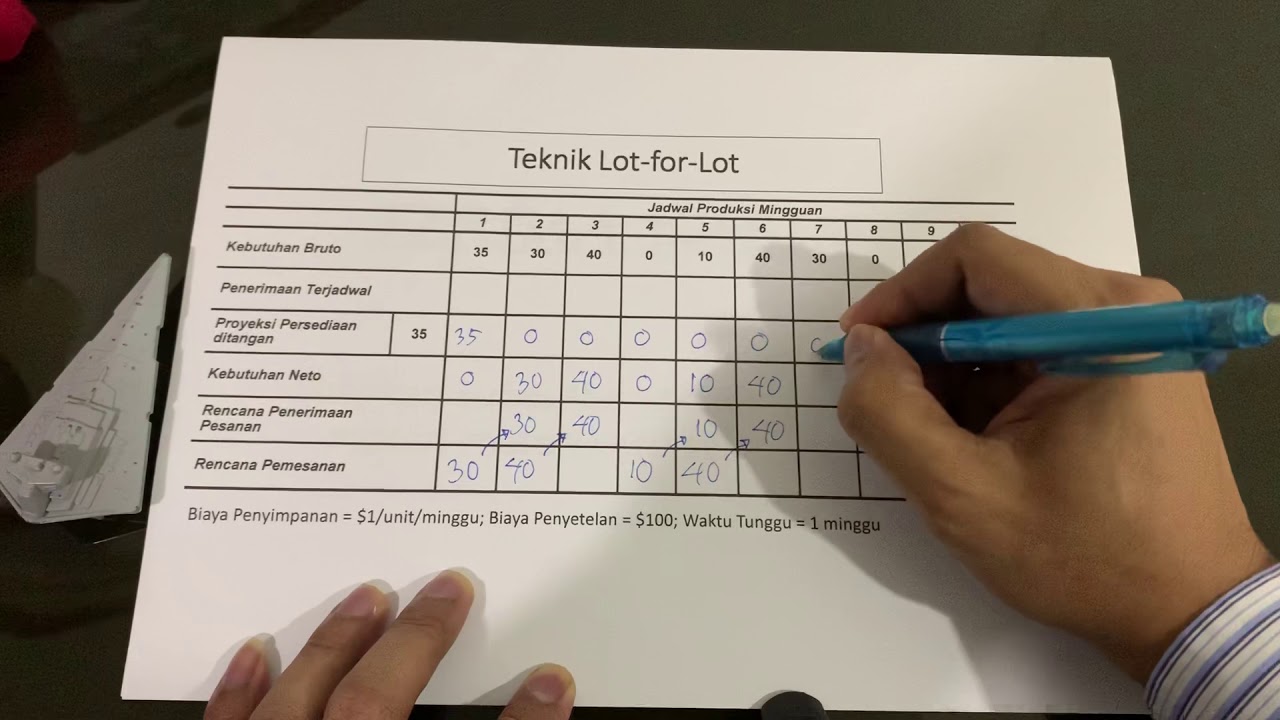
Teknik Lot for Lot pada Lot Sizing (Penentuan Ukuran Lot) dalam Sistem MRP

operasi bisnis week #12 master schedule
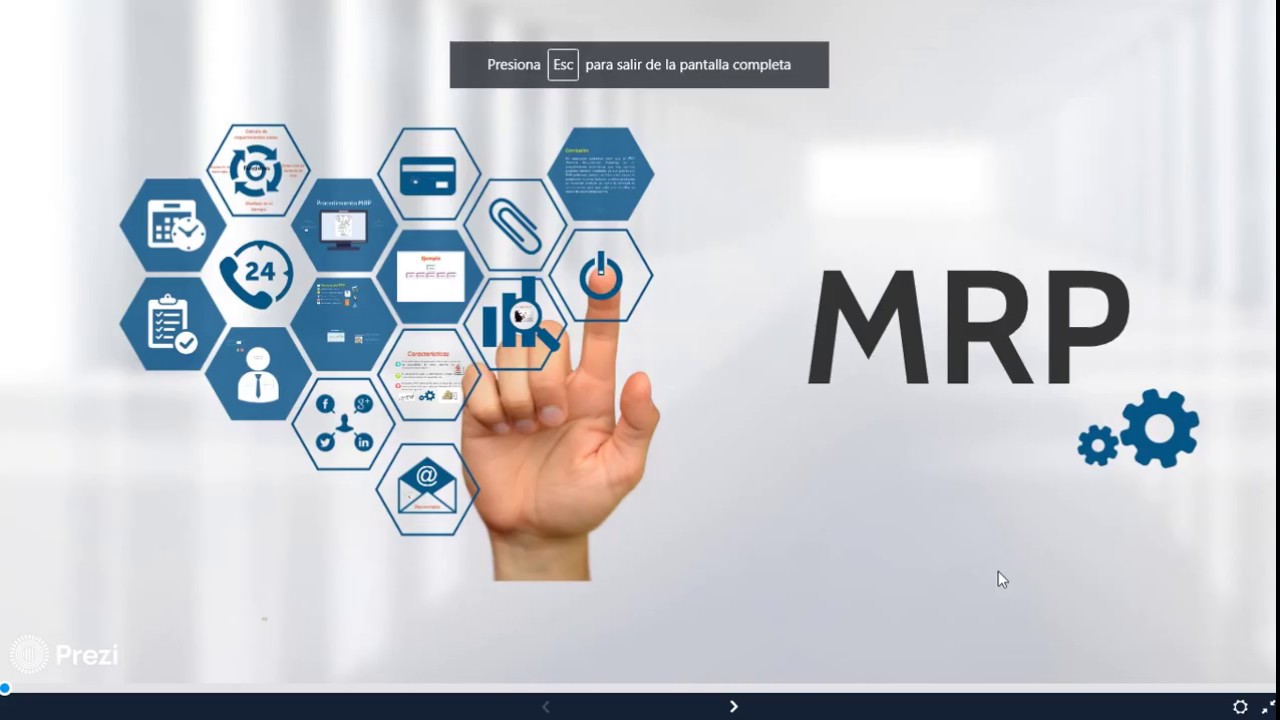
Explicación MRP
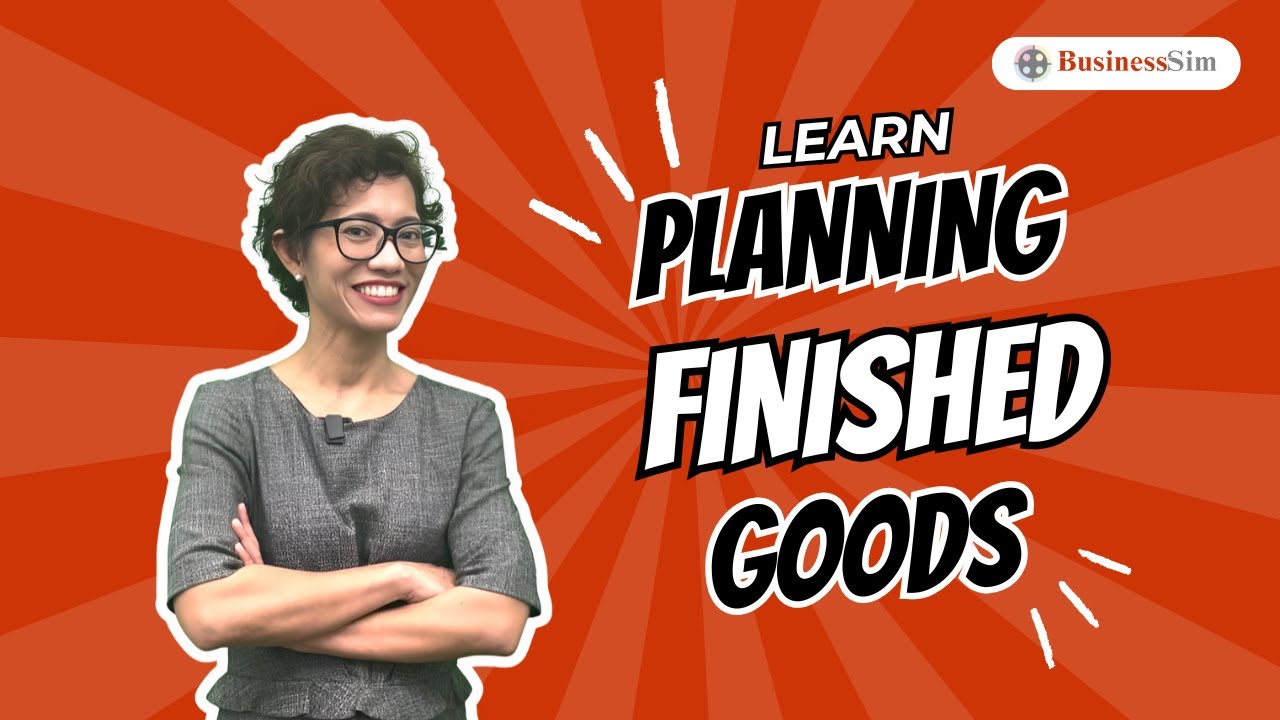
Production | Mastering Finished Goods Planning in Business Simulation
5.0 / 5 (0 votes)