W. Edwards Deming - Part 2
Summary
TLDRالنص يتحدث عن الدكتور ديمينغ وتأثيره الكبير على الشركات اليابانية وتأثيره السلبي على الشركات الأمريكية. يشير النص إلى أن النجاح الأمريكي بعد الحرب كان بسبب الأحداث العسكرية وليس بسبب مهارات الإدارة، وهو ما يشير إلى أن الأرقام ليست كل شيء. يشير النص إلى أن الدكتور ديمينغ كان يرى أن التحسين المستمر هو المفتاح لتحسين الجودة، وهو ما تبعته شركات الصناعة اليابانية بنجاح. وعندما تحول التلفزيون الأمريكي لرؤية الدكتور ديمينغ، بدأت الشركات الأمريكية في الاهتمام ب他的 الأفكار، وبدأت في التركيز على التحسين المستمر. وعندما تحول شركات السيارات الyankee لهذه الطريقة، نجحت في تحسين جودة سياراتها وزيادة حصتها في السوق. ومع ذلك، يشير النص إلى أن التغيير ليس سهل وأنه يتطلب تغيير في التفكير والأسلوب الشخصي، وهو ما كان يعاني منه المديرون الأمريكيون. وأخيرًا، يشير النص إلى أن الدكتور ديمينغ قد وضع 14 نقطة تلخص أفكاره حول الجودة والتحسين المستمر.
Takeaways
- 🏆 W. Edwards Deming was highly respected in Japan, to the extent that an award was named after him, highlighting his influence on Japanese industry's focus on quality and continuous improvement.
- 📈 Japanese companies strive for quality and continuous improvement, which is one of the highest honors they can receive, the Deming Prize.
- 📊 Dr. Deming identified a fallacy in American industry, stating that its success was due to the aftermath of the war, not its own management skills.
- 💡 Deming emphasized the importance of theory over figures, warning against the misuse of quantitative data without understanding the underlying principles.
- 📺 American television brought Dr. Deming to the forefront during the 1980s, leading to a resurgence in his teachings and influence.
- ⏳ Deming's philosophy resonated with business leaders who recognized the fundamental importance of people in his management principles.
- 🚗 Ford's market share recovery was attributed to the quality transformation prompted by Dr. Deming's teachings, particularly in the context of competition from Japanese automakers.
- 🔍 Ford engineers discovered that Japanese transmissions were of higher quality due to tighter tolerances and attention to detail, illustrating the principle of continuous improvement.
- 📈 Ford's success in the 1980s, including overtaking General Motors in market share, was credited to the quality transformation inspired by Dr. Deming.
- 🔄 Deming's teachings emphasize that there is no quick fix for quality management and that it requires a drastic change in thinking and lifestyle.
- 📝 Deming summarized his beliefs in 14 points, which include contentious ideas like the scrapping of performance-related pay and a focus on quality through continuous improvement.
Q & A
德明在日本受到高度尊敬,他们以他的名字命名了一个奖项,这个奖项是什么?
-德明在日本受到高度尊敬,他们以他的名字命名的奖项是戴明奖(Deming Prize),这是日本公司追求质量和持续改进的最高荣誉之一。
德明博士在美国工业中识别出了一个什么谬误?
-德明博士识别出的美国工业的谬误是,其成功是由于战后的余波,而非其自身的管理技能。他认为,会计们认为数字加起来是对的,但德明知道,最重要的商数实际上是无法衡量的。
德明博士的哪个观点在美国电视上引起了关注,导致他的电话响个不停?
-德明博士的观点是,你不能通过制造产品然后将好的与坏的分开来取得进步,因为这样做既浪费人力又浪费时间和材料。这个观点在美国电视上引起了关注,导致他的电话响个不停。
福特公司在1980年代初期与马自达合作,他们制造的是什么类型的车?
-福特公司在1980年代初期与马自达合作,他们制造的是面向美国的第一款前轮驱动汽车。
福特公司在1980年代的市场份额是如何增长的,这与德明博士有什么关联?
-福特公司在1980年代的市场份额增长,这与德明博士提倡的持续改进和质量变革有直接关联。德明博士的理念帮助福特改进了产品质量,特别是在汽车变速箱的制造上,从而提升了市场竞争力。
德明博士的管理原则中,哪个原则是他认为最重要的?
-德明博士的管理原则中,尊重人是他认为最重要的原则。他认为每个人都有固有的价值,并且这一点在他的基本管理原则中反复出现。
德明博士如何描述他对质量的看法?
-德明博士将质量描述为一种思维方式,是一种关于我们如何思考每件事以及我们生活方式的根本性改变。他强调没有快速解决的方法,质量需要时间和持续的努力来实现。
德明博士提出了多少点管理原则?
-德明博士总结了他的管理原则为14点,这比摩西的十诫还要多,显示了他管理哲学的深度和复杂性。
为什么德明博士反对绩效相关的薪酬制度?
-德明博士认为绩效相关的薪酬制度可能会导致短期行为和忽视长期质量,这与他提倡的持续改进和全面质量管理的理念相冲突。
1985年,一家美国公司成为第一个在日本以外获得戴明奖的公司,这家公司位于哪里?
-1985年,一家位于迈阿密的美国公司成为第一个在日本以外获得戴明奖的公司。
德明博士的管理哲学在美国被广泛接受之前,他在美国的知名度如何?
-在德明博士的管理哲学在美国被广泛接受之前,他在美国的知名度并不高。即使他住在离白宫仅五英里的地方,许多美国人,包括白宫的高级顾问,都没有听说过他。
德明博士的管理哲学在美国引起广泛关注的转折点是什么?
-德明博士的管理哲学在美国引起广泛关注的转折点是他在一次电视节目中出现,节目提出了为什么美国正在输给日本的问题,德明博士在节目中仅出现了九分钟,但这足以引起广泛的关注和讨论。
Outlines
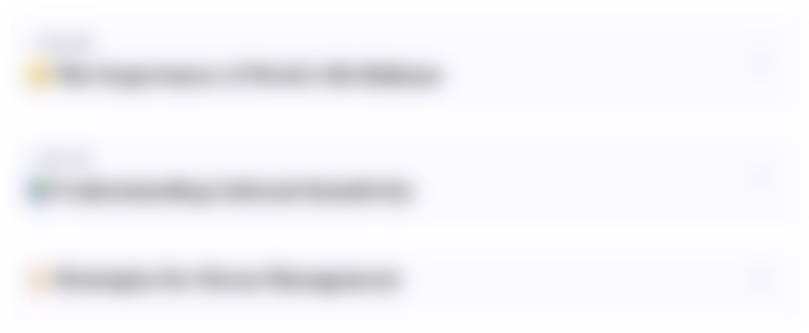
هذا القسم متوفر فقط للمشتركين. يرجى الترقية للوصول إلى هذه الميزة.
قم بالترقية الآنMindmap
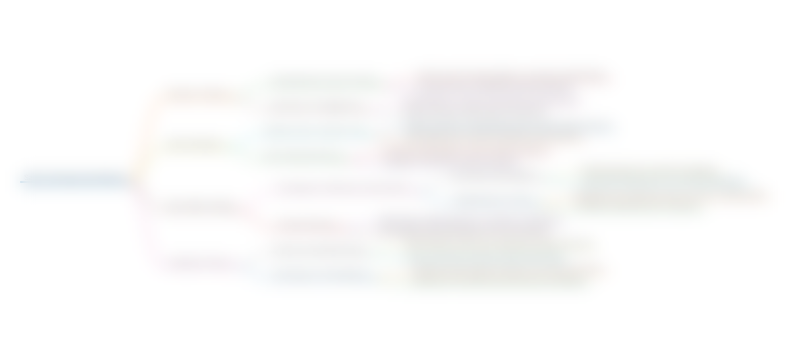
هذا القسم متوفر فقط للمشتركين. يرجى الترقية للوصول إلى هذه الميزة.
قم بالترقية الآنKeywords
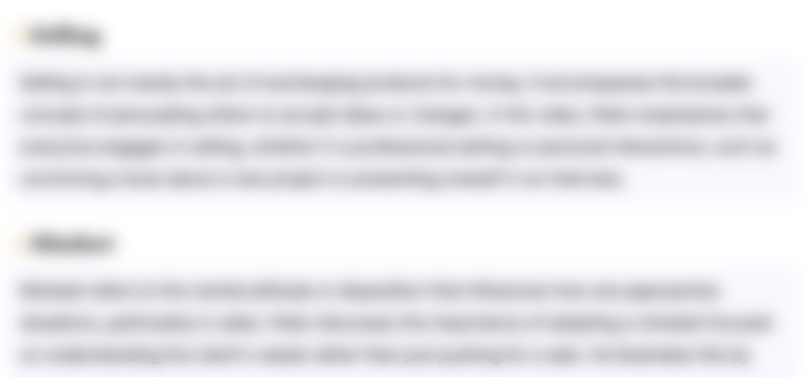
هذا القسم متوفر فقط للمشتركين. يرجى الترقية للوصول إلى هذه الميزة.
قم بالترقية الآنHighlights
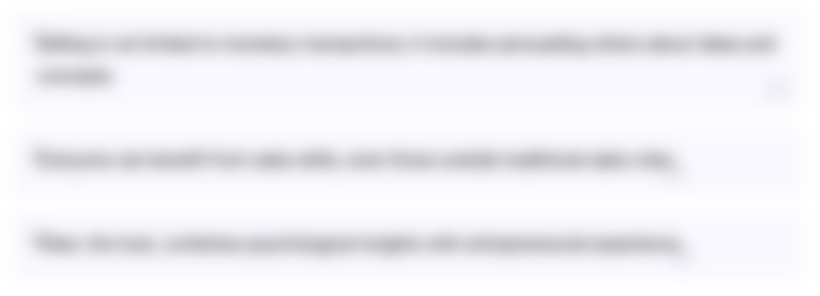
هذا القسم متوفر فقط للمشتركين. يرجى الترقية للوصول إلى هذه الميزة.
قم بالترقية الآنTranscripts
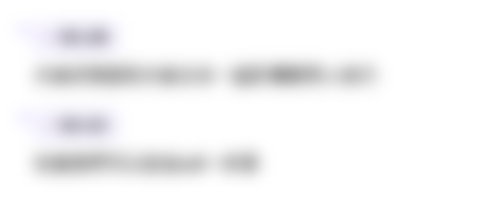
هذا القسم متوفر فقط للمشتركين. يرجى الترقية للوصول إلى هذه الميزة.
قم بالترقية الآنتصفح المزيد من مقاطع الفيديو ذات الصلة

Watch CNBC's full interview with U.S. Trade Representative Jamieson Greer
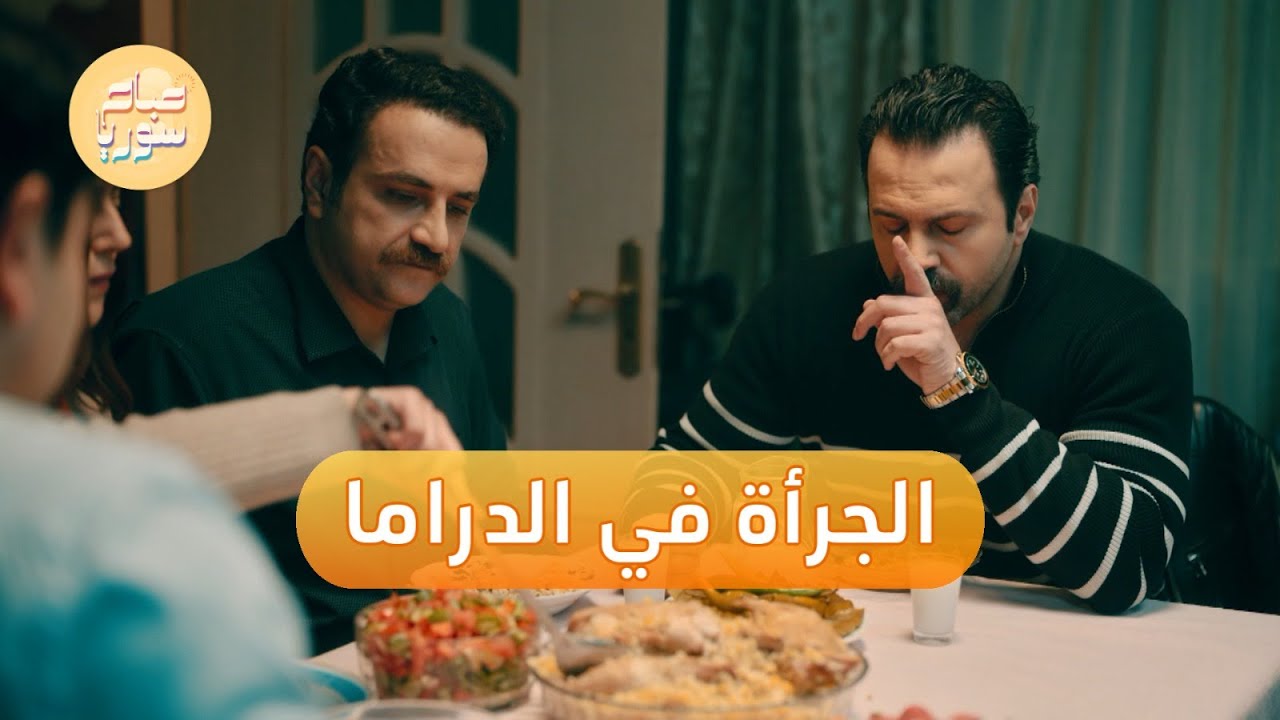
ألفاظ نابية وإيحاءات خفية؟ ما هو سقف الجرأة في الدراما السورية؟ | صباح سوريا

Exchange and Economic Risks in International Operations. CPA Exam Economics.
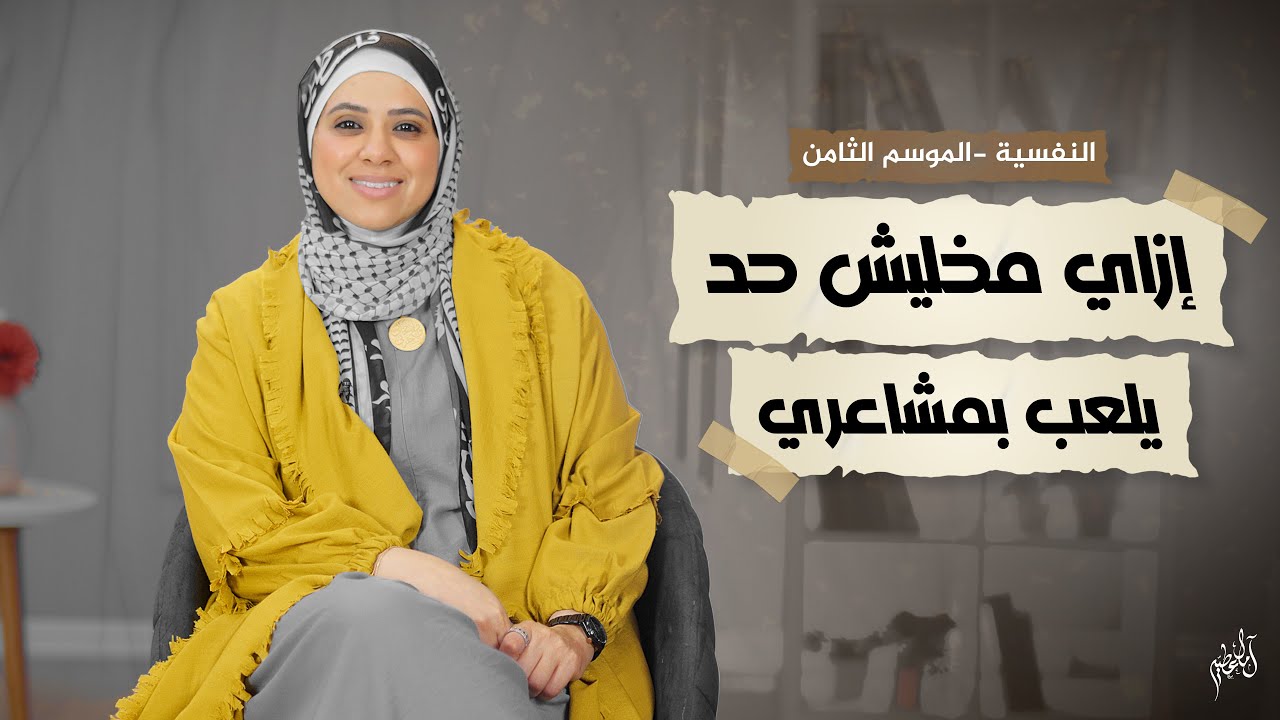
لماذا اصبحت مشاعري لعبة؟/ التلاعب النفسي/ #النفسية #امال_عطيه

خانتني وغدرت بيا في قلب بيتي .. التفاصيل الكاملة لـ خناقة ريم البارودي وريهام سعيد

【前田穂南 日本新記録達成】【official】2024 Osaka Women's Marathon full version/第43回 大阪国際女子マラソン

What Do Digital Marketers & E-commerce Professionals Do? | Google Career Certificates
5.0 / 5 (0 votes)