Flow-Tech: Industrial Control Valve Basics
Summary
TLDRThis video explains the workings of control valve actuators, which regulate fluid flow by varying the orifice size in a valve. The control valve has two main components: the valve body, which houses the fluid connections and restrictor, and the valve actuator, which moves the restrictor to adjust flow. Three types of actuators are discussed: spring and diaphragm, solenoid, and motor-based. Each method controls the valve differently, using pneumatic signals, magnetic fields, or motorized movements, to manage fluid flow for various applications, including both on/off and proportional control modes.
Takeaways
- 🔧 Control valve actuators regulate fluid flow in a pipe by varying the orifice size.
- 🏗️ Control valves have two major components: the valve body and the valve actuator.
- 💧 The valve body contains the fluid connections and the movable restrictor that controls fluid flow.
- ⚙️ The valve actuator moves the restrictor to adjust the flow of fluid.
- 🔩 There are three types of actuators used in control valves: spring and diaphragm, solenoid, and motor.
- 🌬️ Spring and diaphragm actuators use a pneumatic signal to exert pressure on the diaphragm, which moves the restrictor.
- 📏 The 3-15 psi pneumatic signal controls the restrictor’s position and the flow rate through the valve.
- ⚡ Solenoid actuators use current to generate a magnetic field, moving the valve to fully open or fully closed positions.
- 🔄 Motor actuators provide proportional control using a gear motor and a servo amplifier to adjust the valve's position.
- 🔙 Feedback mechanisms, like wiper arms, help the motor actuator maintain precise positioning by monitoring signals.
Q & A
What are the two main components of a control valve?
-The two main components of a control valve are the valve body and the valve actuator.
What role does the valve body play in a control valve?
-The valve body provides the fluid connections and houses a movable restrictor, consisting of a valve stem and plug, that varies the flow of fluid.
How does the valve actuator affect fluid flow in a control valve?
-The valve actuator physically moves the restrictor, adjusting the orifice size to control the flow of fluid through the valve.
What are the three types of actuators used in control valves?
-The three types of actuators used in control valves are spring and diaphragm, solenoid, and motor actuators.
How does the spring and diaphragm actuator operate?
-A spring and diaphragm actuator uses a 15 psi pneumatic signal to apply pressure on the diaphragm, which exerts a downward force on the spring, moving the valve stem and plug to adjust fluid flow.
What happens in a spring and diaphragm actuator when no air pressure is applied?
-With no air pressure, the spring pushes the restrictor upward, causing the valve to act as a normally open control valve.
What is the purpose of a current-to-pressure transducer in a spring and diaphragm actuator?
-A current-to-pressure transducer is used to provide a 3 to 15 psi signal to the diaphragm, allowing for proportional control of the valve's flow based on the applied pressure.
How does a solenoid actuator control the valve?
-A solenoid actuator uses a magnetic field generated by current applied to a coil, which moves the plunger to open or close the valve for on/off control.
How is variable valve positioning achieved using a motor actuator?
-Variable valve positioning is achieved using a motor actuator by utilizing a gear motor and a servo amplifier. The servo amplifier provides a DC control signal to adjust the valve position, with feedback from a wiper arm that monitors the valve's position.
What is the role of the servo amplifier in motor-operated valves?
-The servo amplifier drives the motor until the control signal is equal to the feedback signal from the valve position, ensuring precise positioning.
Outlines
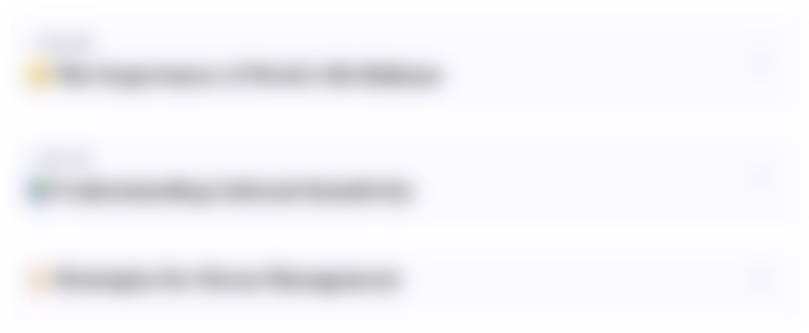
هذا القسم متوفر فقط للمشتركين. يرجى الترقية للوصول إلى هذه الميزة.
قم بالترقية الآنMindmap
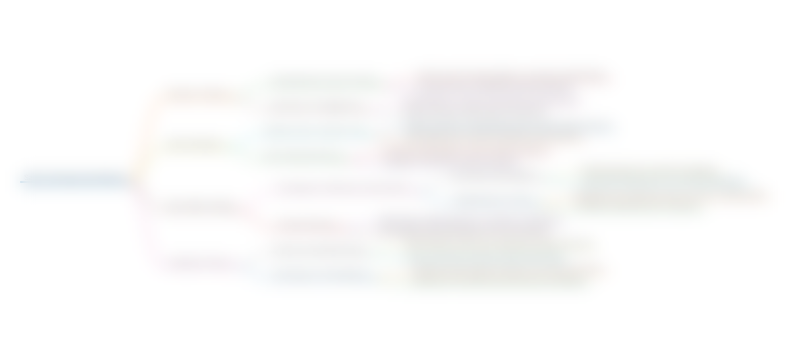
هذا القسم متوفر فقط للمشتركين. يرجى الترقية للوصول إلى هذه الميزة.
قم بالترقية الآنKeywords
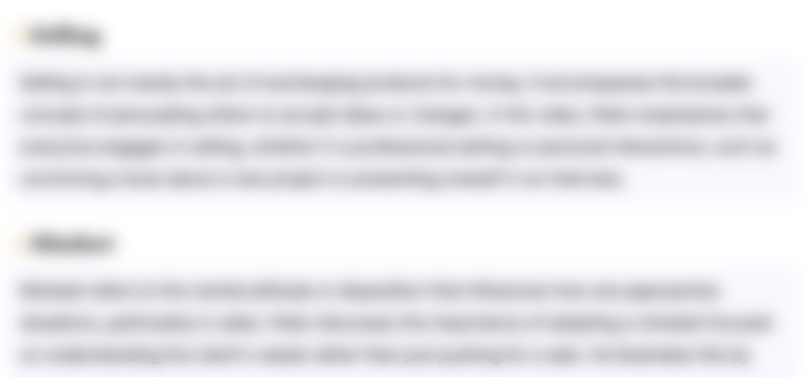
هذا القسم متوفر فقط للمشتركين. يرجى الترقية للوصول إلى هذه الميزة.
قم بالترقية الآنHighlights
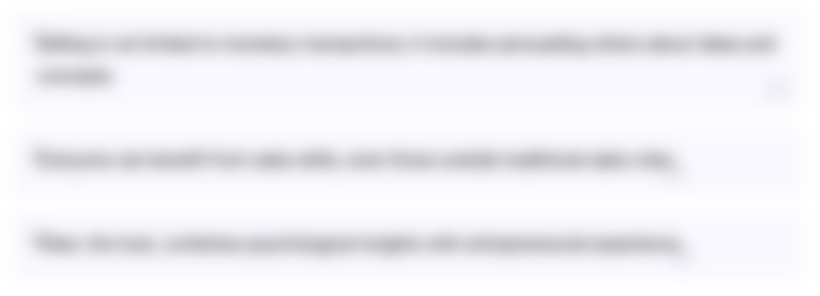
هذا القسم متوفر فقط للمشتركين. يرجى الترقية للوصول إلى هذه الميزة.
قم بالترقية الآنTranscripts
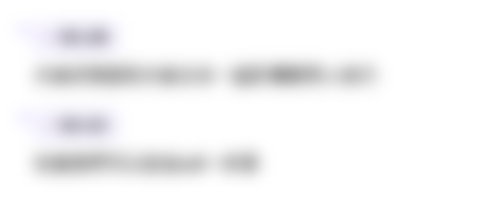
هذا القسم متوفر فقط للمشتركين. يرجى الترقية للوصول إلى هذه الميزة.
قم بالترقية الآنتصفح المزيد من مقاطع الفيديو ذات الصلة

How Do Control Valve Actuators Work?
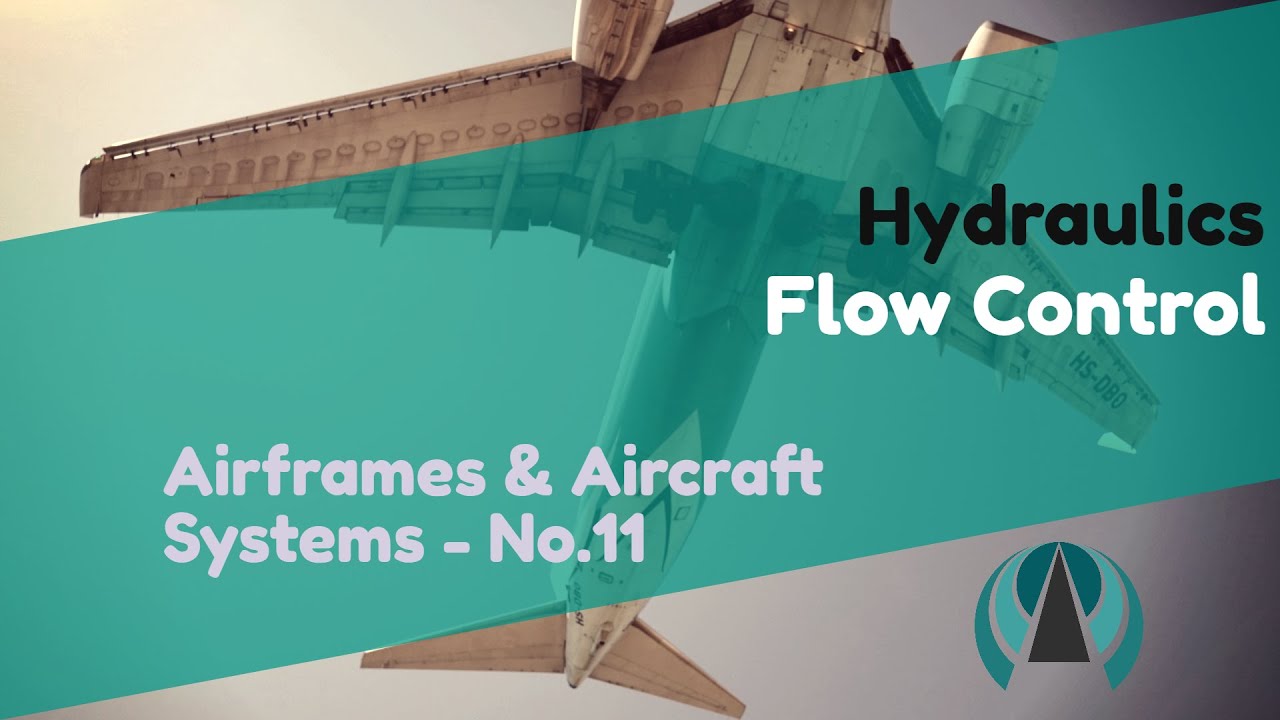
Flow Control - Hydraulics - Airframes & Aircraft Systems #11

EMS Part 3, Macam macam Aktuator Engine Management system #ems #enginemanagementsystem
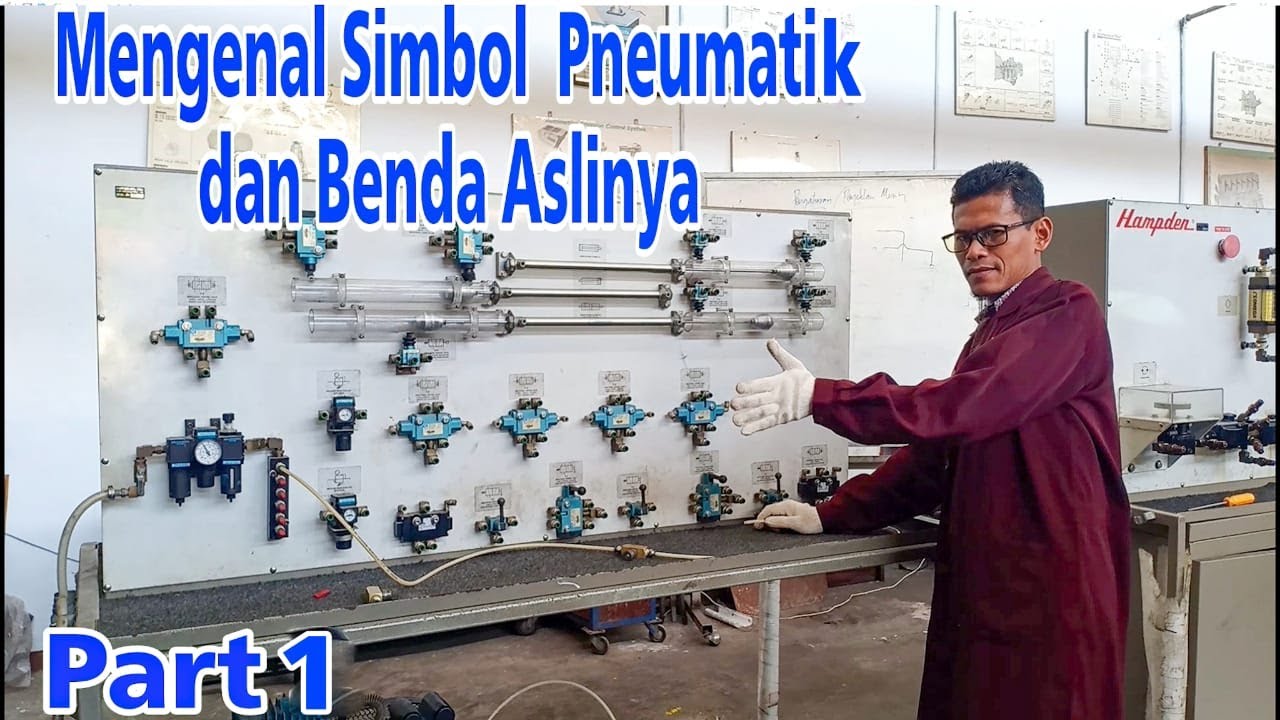
Mengenal Simbol Pneumatik dan Benda Aslinya #waginothok
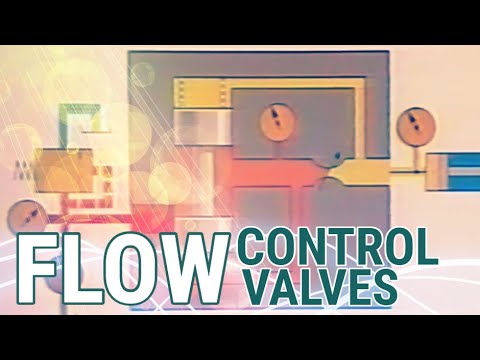
Hydraulic Training Series - Chapter 6 - Flow Control Valves

How an Automated Manual Transmission Works
5.0 / 5 (0 votes)