The Ingenious Design of the Aluminum Beverage Can
Summary
TLDRThe script explores the engineering marvel of the aluminum beverage can, explaining why it's cylindrical, not spherical or cuboid, despite those shapes' theoretical advantages. It details the can's manufacturing process, from blank punching to drawing, redrawing, ironing, and doming, emphasizing the can's efficient material use and rapid production. The script also highlights the can's innovative features, such as the double seam and the stay-on tab, and touches on the importance of recycling, noting that most cans contain a significant amount of recycled material.
Takeaways
- 🔢 Every year, nearly half a trillion cans are manufactured, averaging 15,000 per second.
- 🔍 The can is shaped as a cylinder because it combines the material efficiency of a sphere and the practicality of a cuboid.
- 🛠️ Manufacturing a can involves a process of drawing, redrawing, ironing, and doming to form the can body.
- 🔩 The can's bottom is domed to distribute pressure and reduce the amount of material needed.
- 🏭 The production process is highly automated, with certain steps happening in a fraction of a second.
- ⚙️ The can body is made from a thin aluminum sheet which is punched and shaped into a can.
- 🎨 The can is decorated with a colorful design and has an epoxy lacquer coating on the inside to prevent metallic taste.
- 🌐 The neck of the can is formed through a process called necking, which involves multiple stages to prevent wrinkling.
- 🔗 The double seam is a key feature that ensures a hygienic and secure seal for the can.
- 💨 The internal pressure inside the can strengthens the thin walls, allowing it to support significant weight.
- 🔑 The modern stay-on tab is a result of clever engineering to replace the older pull-tab design, addressing environmental concerns.
Q & A
How many cans are manufactured each year, and how does this rate compare to the speed of production?
-Nearly half a trillion cans are manufactured each year, which is about 15,000 cans per second.
Why are cans shaped like cylinders instead of spheres or cuboids?
-Cans are shaped like cylinders because spheres, while efficient in material use, are impractical to manufacture and unstable when placed on a surface. Cuboids, while efficient in packing, are uncomfortable to hold and drink from, and have weak points that require thicker walls. Cylinders combine the best of both shapes, offering a balance between material use and practicality.
What is the maximum packing factor of a cylinder-shaped can?
-A cylinder-shaped can has a maximum packing factor of about 91%, which is better than a sphere but not as efficient as a cuboid.
How is the initial can shape formed and what is this process called?
-The initial can shape is formed by pressing a blank, which is a disk punched from an aluminum sheet, into a cup using a cylindrical punch and a process called 'drawing.'
What is the purpose of re-drawing and ironing in the can manufacturing process?
-Re-drawing is used to reduce the diameter of the cup to the final can size, while ironing is used to make the walls thinner and the can taller without changing the diameter.
Why is a dome formed at the bottom of the can?
-A dome is formed at the bottom of the can to reduce the amount of metal needed and to distribute some of the vertical load into horizontal forces, allowing the can to withstand greater pressure.
What do the debossed numbers on the dome signify?
-The debossed numbers on the dome signify the production line in the factory and the bodymaker number, which is the machine that performs the redrawing, ironing, and doming processes. These numbers help troubleshoot production problems.
How quickly does the can manufacturing process occur?
-The last three steps of can manufacturing—re-drawing, ironing, and doming—all happen in one continuous stroke and in only a seventh of a second.
What is the purpose of the spray-coated epoxy lacquer applied to the inside of the can?
-The spray-coated epoxy lacquer is applied to the inside of the can to separate the contents from the aluminum walls, preventing the drink from acquiring a metallic taste and keeping acids in the beverage from dissolving the aluminum.
How has the necking process evolved since the 1960s, and what is its significance?
-Since the 1960s, the diameter of the can end has become smaller by 6 mm, from 60 mm to 54 mm today. This reduction saves at least 90 million kilograms of aluminum annually, which is significant in the context of the aluminum can industry's massive production volume.
What is the purpose of the double seam in can manufacturing?
-The double seam is a hygienic and faster method of sealing the can compared to older welding or soldering techniques. It creates an airtight seal that prevents contamination of the can's contents.
Why is the beverage can pressurized?
-The internal pressure in a beverage can creates strength in the thin walls, allowing the can to support weight and maintain its shape without needing additional structural support like corrugations.
What is the function of the tab on the end of the can?
-The tab on the end of the can is used to open the can by venting it and creating an opening for consumption. It has evolved from the pull-tab to the modern stay-on tab to prevent litter and injury from sharp edges.
Outlines
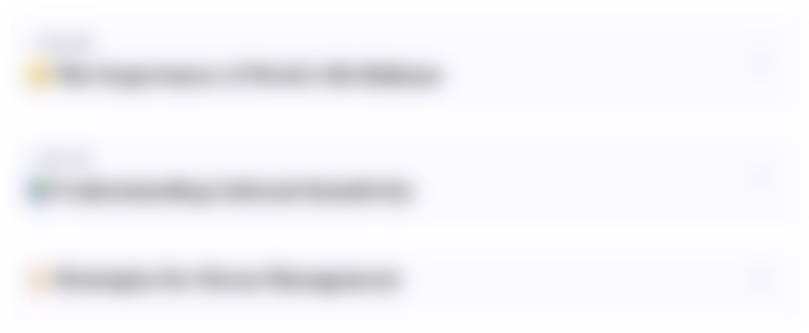
هذا القسم متوفر فقط للمشتركين. يرجى الترقية للوصول إلى هذه الميزة.
قم بالترقية الآنMindmap
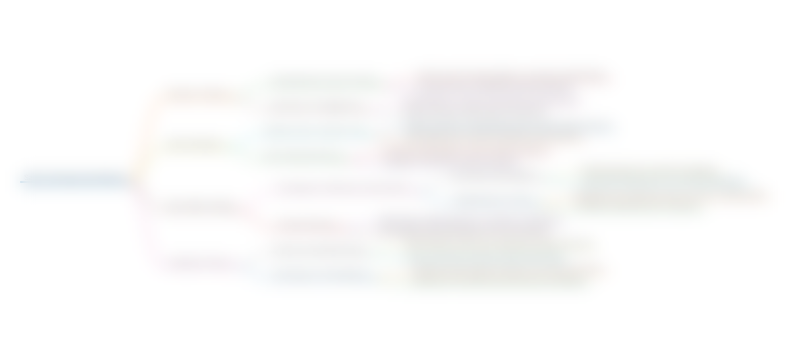
هذا القسم متوفر فقط للمشتركين. يرجى الترقية للوصول إلى هذه الميزة.
قم بالترقية الآنKeywords
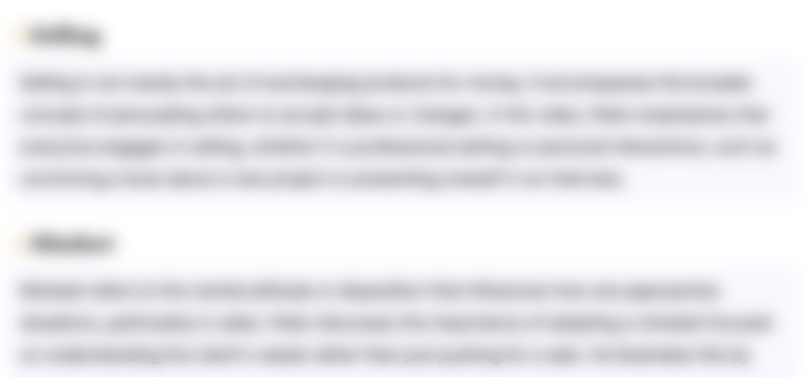
هذا القسم متوفر فقط للمشتركين. يرجى الترقية للوصول إلى هذه الميزة.
قم بالترقية الآنHighlights
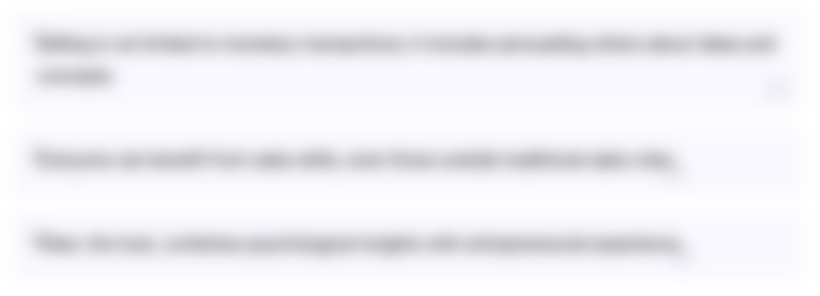
هذا القسم متوفر فقط للمشتركين. يرجى الترقية للوصول إلى هذه الميزة.
قم بالترقية الآنTranscripts
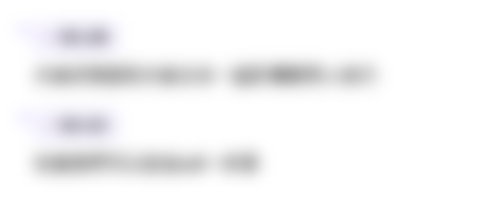
هذا القسم متوفر فقط للمشتركين. يرجى الترقية للوصول إلى هذه الميزة.
قم بالترقية الآنتصفح المزيد من مقاطع الفيديو ذات الصلة
5.0 / 5 (0 votes)