Takt Time, Cycle Time, Lead Time
Summary
TLDRThis video script teaches the concepts of TAC time, cycle time, and lead time in operational excellence. It explains how TAC time represents the theoretical demand rate, cycle time is the actual production rate, and lead time measures the duration from production to completion. The script uses a scenario of a company producing colored circles to illustrate these concepts, showing how to calculate TAC time, improve cycle time, and reduce lead time to meet customer demands and improve process efficiency.
Takeaways
- 🕒 **Takt Time (TAC Time)**: It's the rate at which you need to produce to meet customer demand, calculated by dividing available production time by the number of units needed.
- ⏱️ **Cycle Time**: It's the actual rate of production, measured from the completion of one unit to the next, indicating process stability and reliability.
- 📏 **Lead Time**: It's the total time taken for a unit to move from start to finish in the production process, impacting customer wait times and inventory levels.
- 🔍 **Process Understanding**: Understanding these times helps in designing processes to better meet customer demands and expectations.
- 🔧 **Process Improvement**: By measuring and analyzing TAC, cycle, and lead times, you can identify inefficiencies and areas for improvement in your operations.
- 📉 **Inventory Management**: A long lead time relative to the production effort suggests excess inventory, which can be reduced to improve efficiency.
- 🛠️ **Operational Flexibility**: Having multiple options to adjust production (like adding more workers or combining steps) allows meeting varying customer demands.
- 📈 **Customer Demand Adaptation**: The ability to adapt production rates to changing customer demands is crucial for operational excellence.
- 🔄 **Balancing Workload**: Combining certain steps or using multiple cells can balance workload and improve overall cycle times.
- 📋 **Value Stream Mapping**: This tool can help visualize and reduce inventory delays, improving lead times to meet customer service level agreements (SLAs).
Q & A
What is TAC time and how is it calculated?
-TAC time, or Takt Time, is a calculated value that represents the theoretical demand rate of a customer. It is the rate at which you need to produce to meet their demand. It is calculated by dividing the available production time by the number of units the customer needs.
What is the purpose of calculating TAC time?
-Calculating TAC time helps to understand the production rate required to meet customer demand. It provides a gauge on what is actually needed to satisfy customer requirements.
Why might a company choose to run faster than their TAC time?
-A company might choose to run faster than their TAC time to allow for potential downtime due to issues that may arise, especially early in the learning curve of a process.
What is Cycle Time and how is it measured?
-Cycle Time is the rate at which an operation is actually producing a unit. It is measured as the frequency of units produced, typically from the output of one unit to the next.
What does a consistent and predictable Cycle Time indicate about a process?
-A consistent and predictable Cycle Time indicates a stable process. It allows for the quick identification of abnormalities in the production process.
How is Lead Time measured and what does it represent?
-Lead Time is measured by observing how long it takes for one unit to move through the entire operation from start to finish. It represents the total time a customer has to wait for their product to be completed.
How can Lead Time be used to gauge inventory levels in a process?
-If the Lead Time is significantly longer than the time it takes to produce a unit, it suggests that there is a lot of inventory between process steps, which could be delaying the output.
What is the scenario presented in the script and what is the company producing?
-The scenario involves a small company that produces colored circles on white paper. The operation requires three work steps: tracing, cutting, and adhering.
How does the company calculate TAC time with the given scenario?
-In the given scenario, the company calculates TAC time by dividing the available production time (540,000 seconds per month) by the number of units ordered (36,000 units), resulting in a TAC time of 15 seconds per unit.
What are some potential improvements to the process discussed in the script?
-Potential improvements include combining the first and last steps to balance the work content, adding a second cutter to speed up the process, or running two cells to increase staffing flexibility and meet increased demand.
How does the script suggest measuring and improving Lead Time?
-The script suggests measuring Lead Time by following a unit through the entire process and stopping the clock when it is completed. If the Lead Time exceeds customer requirements, value stream mapping can be used to identify and eliminate inventory delays.
Outlines
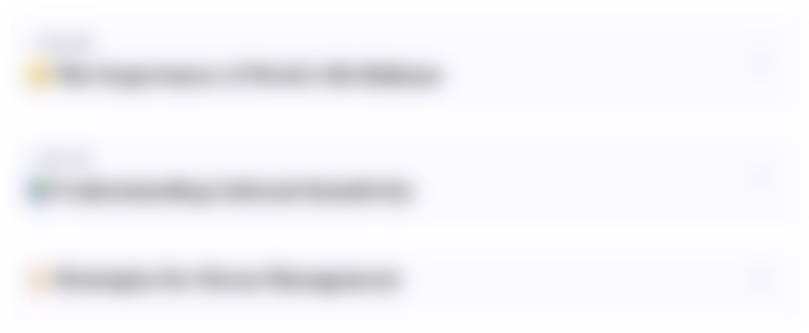
هذا القسم متوفر فقط للمشتركين. يرجى الترقية للوصول إلى هذه الميزة.
قم بالترقية الآنMindmap
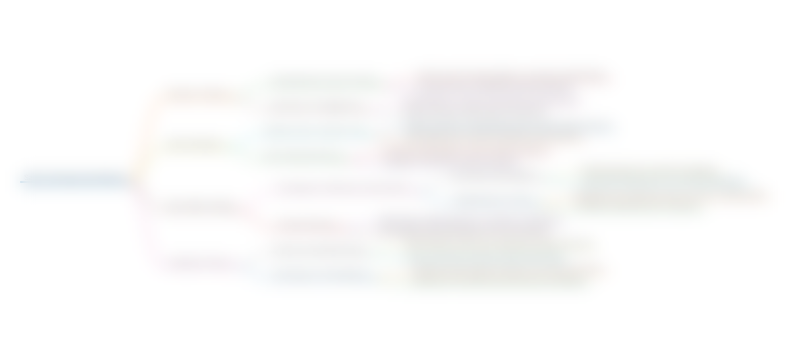
هذا القسم متوفر فقط للمشتركين. يرجى الترقية للوصول إلى هذه الميزة.
قم بالترقية الآنKeywords
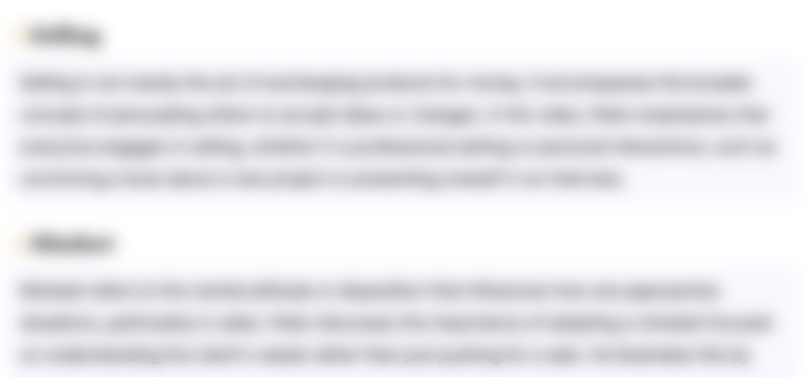
هذا القسم متوفر فقط للمشتركين. يرجى الترقية للوصول إلى هذه الميزة.
قم بالترقية الآنHighlights
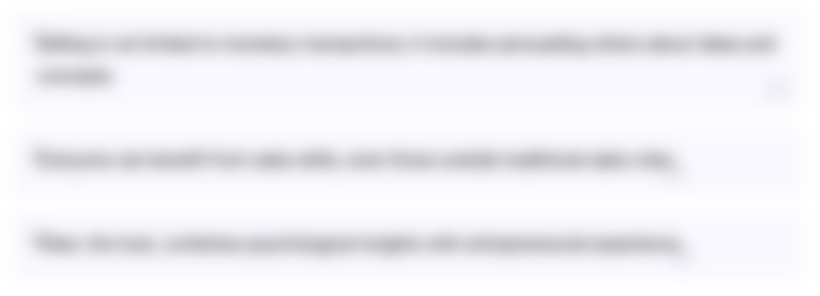
هذا القسم متوفر فقط للمشتركين. يرجى الترقية للوصول إلى هذه الميزة.
قم بالترقية الآنTranscripts
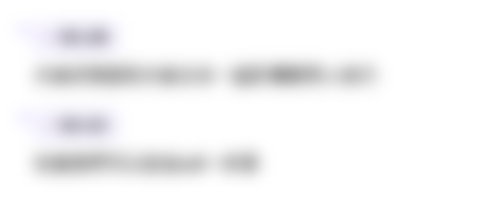
هذا القسم متوفر فقط للمشتركين. يرجى الترقية للوصول إلى هذه الميزة.
قم بالترقية الآنتصفح المزيد من مقاطع الفيديو ذات الصلة
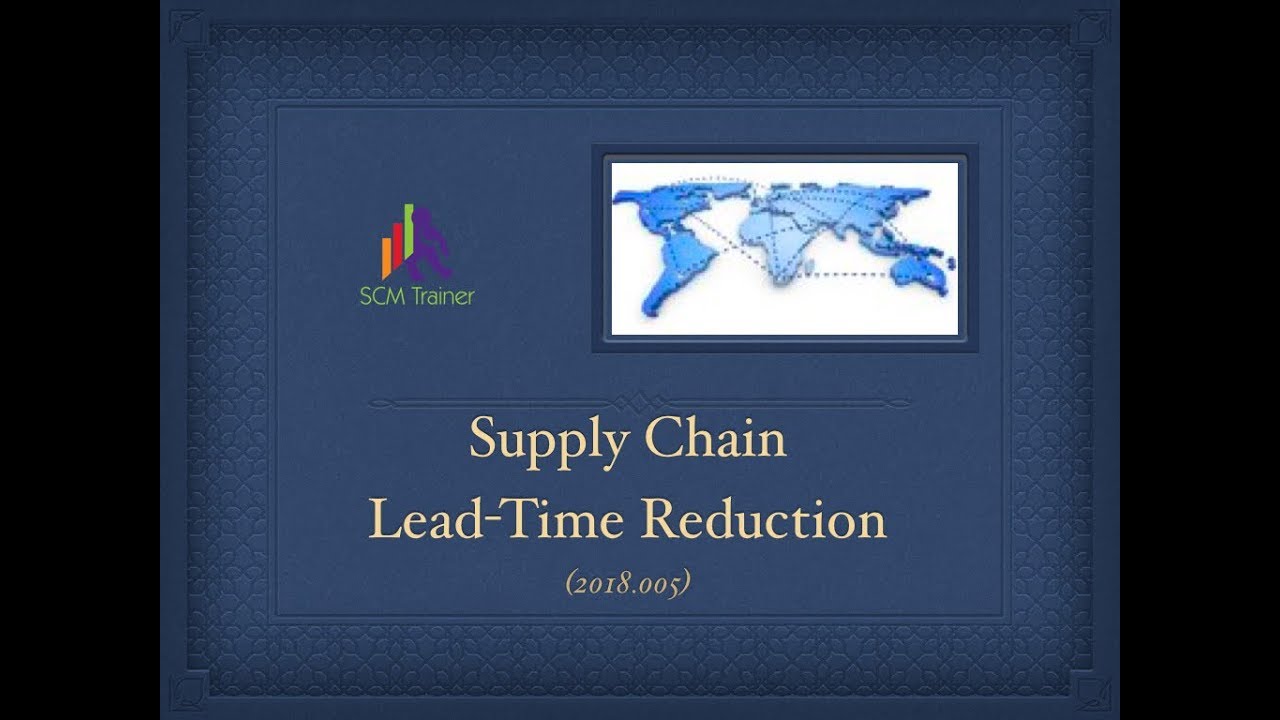
2018.005: Supply Chain Lead Time Reduction Tips

QUAL A DIFERENÇA ENTRE LEAD TIME & TAKT TIME?

What Is Lead Time and How to Reduce It?

Lezione 4B - CREAZIONE VSM - Parte 2 di 4 - Lean Thinking e Toyota Producition System - Zero sprechi
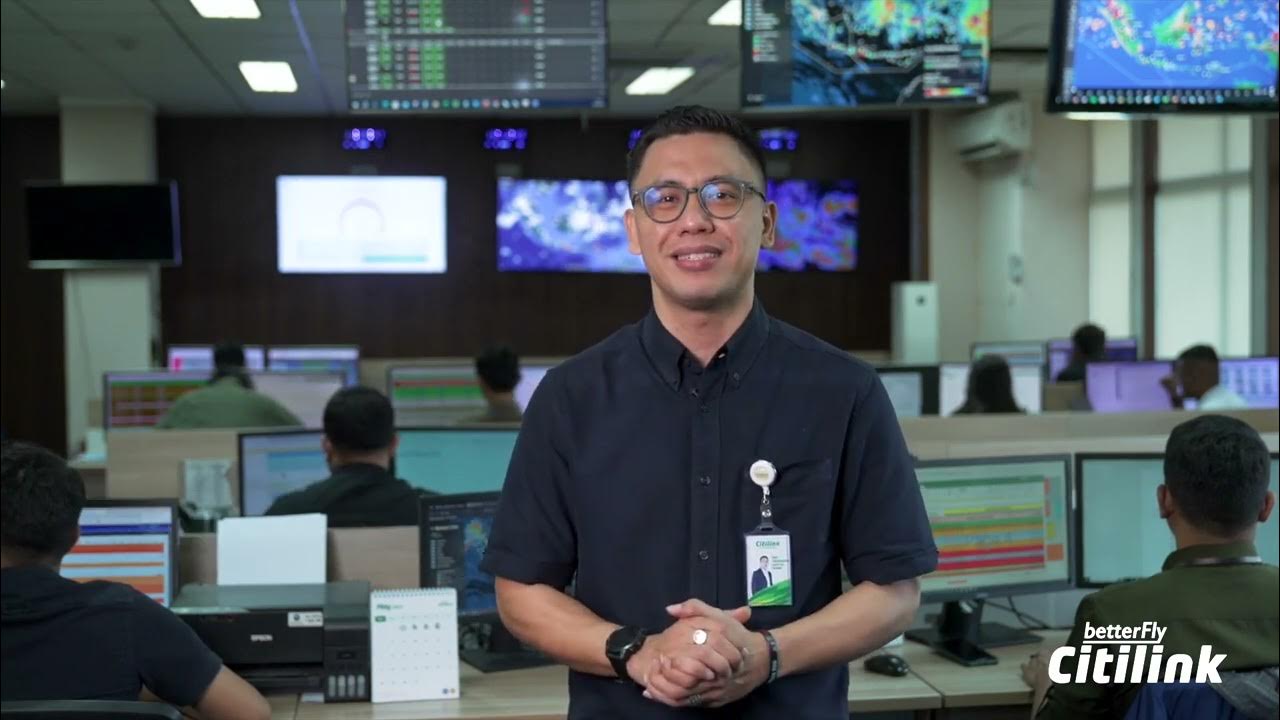
#BikinLebih Dekat dengan Operation Control Centre
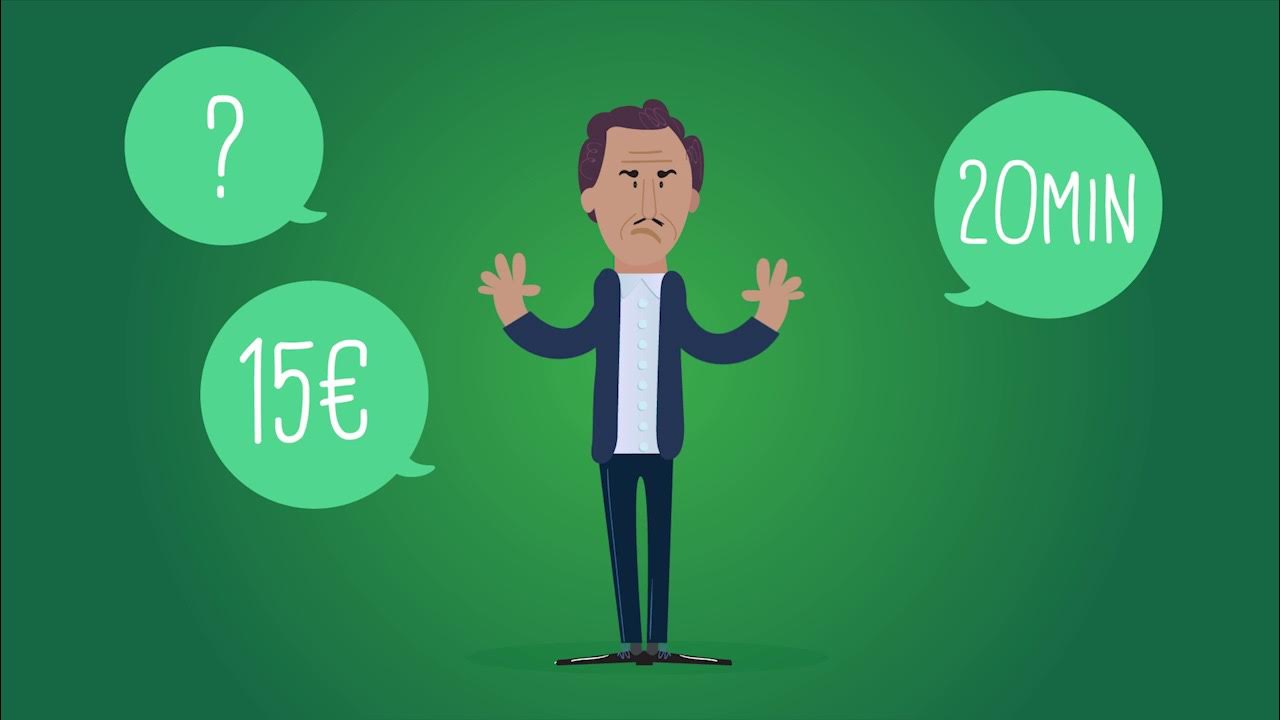
Learn About Lean by Eating Pizza
5.0 / 5 (0 votes)