Sering Lihat Tapi Gak Tau Proses Pembentukannya? Begini Cara Pembuatan Semen Dari Awal Hingga Akhir
Summary
TLDRThis video script explores the surplus production of cement in Indonesia in 2021, highlighting the issue of 45 million tons of unsold cement. It delves into the production process of cement, detailing the extraction of raw materials like limestone and clay, their processing in factories, and the subsequent steps including homogenization, mixing, and calcination. The script also touches on the historical origins of cement, dating back to ancient civilizations, and its evolution into the modern product we know today. The video concludes with a reminder of the importance of cement in various construction projects.
Takeaways
- 🏭 Indonesia's cement industry faced overproduction in 2021, with 45 million tons of cement unsold and left in warehouses.
- 🏗 The main ingredients for cement production are limestone and clay, sourced from natural mines, with Tuban in East Java and Rembang in Central Java being key limestone producers.
- 💥 The extraction of limestone involves the use of explosives, requiring expert handling to prevent accidents and damage.
- 🔨 At the factory, the large limestone is crushed into smaller pieces to facilitate processing, resulting in a homogenized material.
- 🔬 Quality control is a critical step, where the factory assesses the quality of the main materials, which can vary from just clay to more processed forms.
- 🤖 The process is highly mechanized for safety, with limited human access to prevent accidents, such as being hit by limestone spray.
- 🔄 The mixing phase involves a giant machine that blends the materials with additional ingredients like iron ore and sand to achieve the desired structure.
- 🔥 The burning process uses a special type of kiln that can reach temperatures up to 2000 degrees Celsius, which is crucial for cement production.
- 🌱 To reduce CO2 emissions, cement factories often use alternative fuels instead of fossil fuels, such as wood or even waste.
- ♻️ After burning, the material is cooled down to 100 degrees Celsius, which is considered an efficient temperature for the next steps in the process.
- 🔍 The final product undergoes quality control testing, including tests for setting time, strength, and consistency when mixed with water.
Q & A
What was the reported surplus production in the Indonesian cement industry at the end of 2021?
-The reported surplus production in the Indonesian cement industry at the end of 2021 was 116 million tons, of which only 71.72 million tons were sold, leaving approximately 45 million tons unused.
What are the main raw materials used in the production of cement?
-The main raw materials used in the production of cement are limestone and clay, which are obtained from natural quarries such as mountains.
Which regions in Indonesia are known for limestone production?
-In Indonesia, the main regions known for limestone production are Tuban in East Java, and Rembang in Central Java.
How is limestone extracted from the quarry?
-Limestone is extracted from the quarry using explosives in a controlled manner by experts to ensure that the blasting does not cause damage to the mine or result in casualties.
What happens to the limestone once it arrives at the cement factory?
-Upon arrival at the cement factory, the large limestone is crushed into smaller pieces to facilitate further processing.
What is the role of quality control in the cement production process?
-Quality control plays a crucial role in evaluating the quality of the main materials at various stages of the production process, ensuring that the materials meet the factory standards.
What is the purpose of the homogenization process in cement production?
-The homogenization process ensures that the main materials are uniformly mixed, which is essential for maintaining the consistency of the final product.
What is the significance of the silo machine in the cement production process?
-The silo machine is responsible for regulating the chemical and physical properties of the product, ensuring that the properties remain consistent throughout the production.
Why do cement factories use alternative fuels for the calcination process?
-Cement factories use alternative fuels for the calcination process to reduce the use of fossil fuels, which can increase CO2 emissions and are harmful to the environment.
What happens to the cement after it is cooled down from 1000 degrees Celsius to 100 degrees Celsius?
-After the cement is cooled down from 1000 degrees Celsius to 100 degrees Celsius, it undergoes a second mixing process with gypsum and other materials, depending on the type of cement being produced.
How is the quality of cement tested before it is packaged for use?
-The quality of cement is tested by assessing its setting time, compressive strength, and ability to harden when mixed with water. If it does not pass the tests, the cement is re-mixed in the second mixing stage rather than being discarded to avoid loss.
What is the historical origin of cement as a binding material?
-Cement has been known as a binding material since ancient times, including in ancient Greek, Roman, and Egyptian civilizations. It was used in various historical sites such as Borobudur and the Great Wall of China.
Outlines
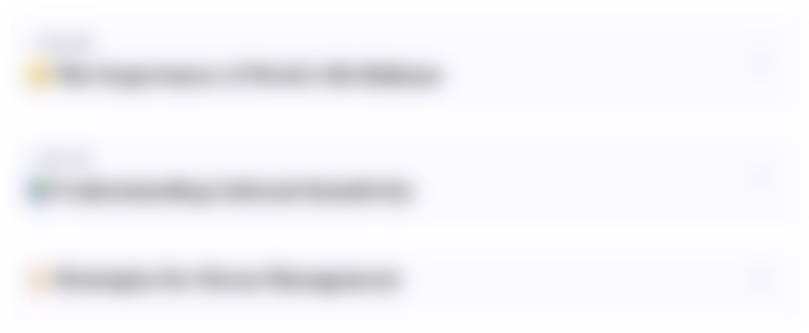
هذا القسم متوفر فقط للمشتركين. يرجى الترقية للوصول إلى هذه الميزة.
قم بالترقية الآنMindmap
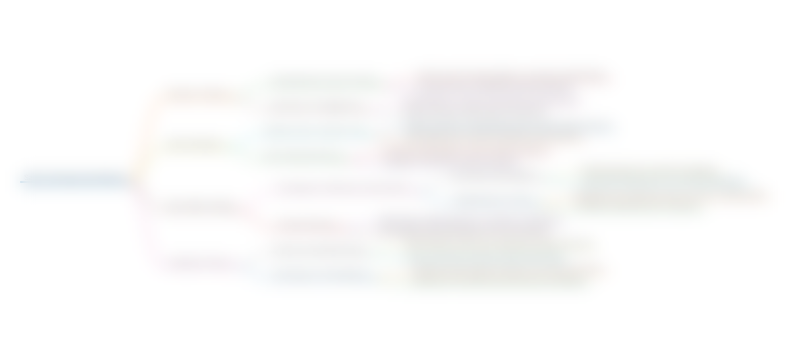
هذا القسم متوفر فقط للمشتركين. يرجى الترقية للوصول إلى هذه الميزة.
قم بالترقية الآنKeywords
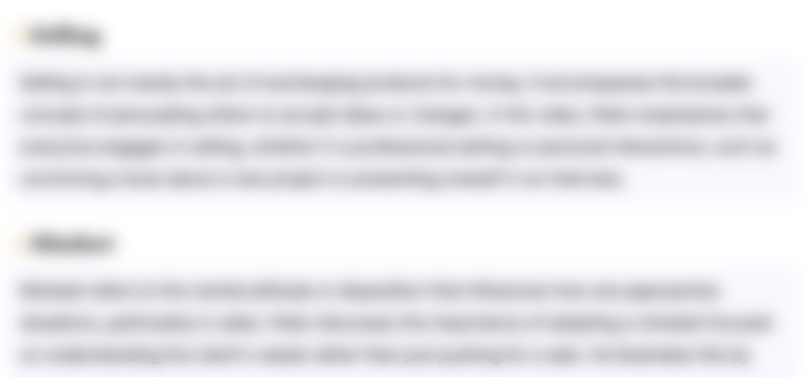
هذا القسم متوفر فقط للمشتركين. يرجى الترقية للوصول إلى هذه الميزة.
قم بالترقية الآنHighlights
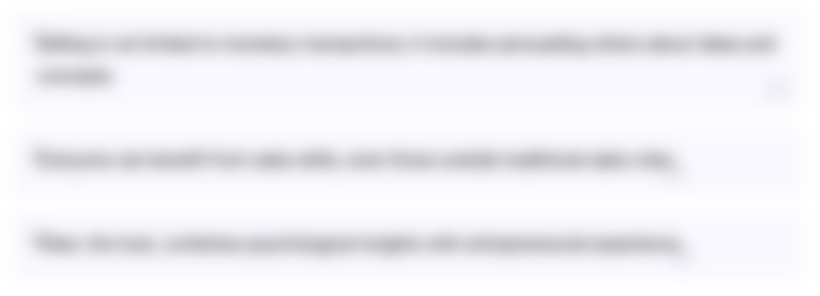
هذا القسم متوفر فقط للمشتركين. يرجى الترقية للوصول إلى هذه الميزة.
قم بالترقية الآنTranscripts
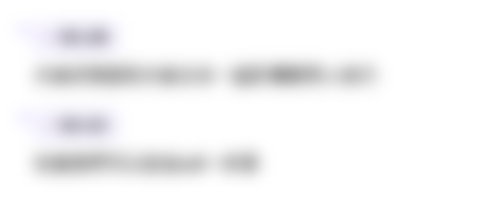
هذا القسم متوفر فقط للمشتركين. يرجى الترقية للوصول إلى هذه الميزة.
قم بالترقية الآنتصفح المزيد من مقاطع الفيديو ذات الصلة

How To Turn Waste Into Electricity
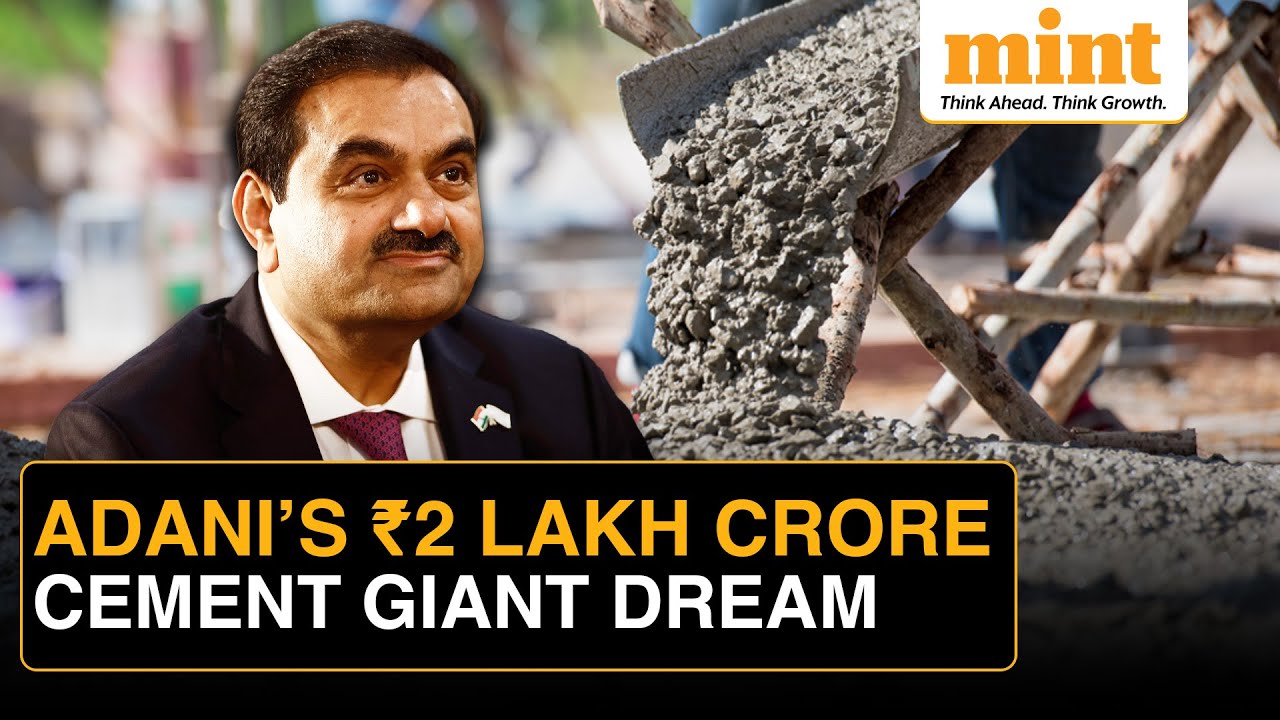
Adani's Mega Cement Merger Plan: Will it be an Industry Gamechanger? | Explained
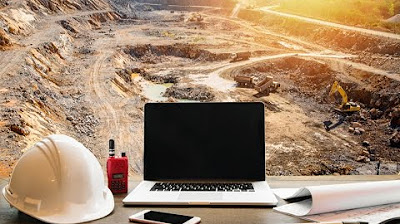
Recycling mining waste – A new business? (Long version)

Penyumbang Emisi Karbon, Mungkinkah Indonesia Memproduksi Semen Hijau?
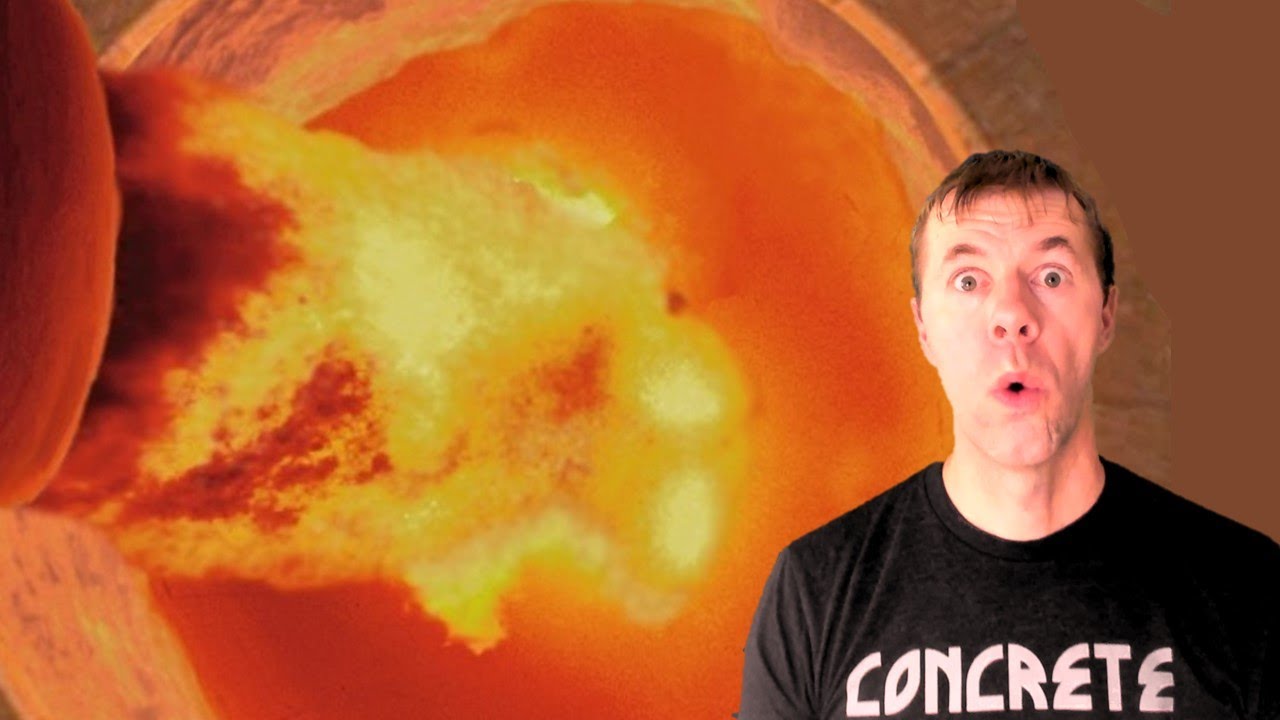
Cement Manufacturing Process with the Portland Cement Association
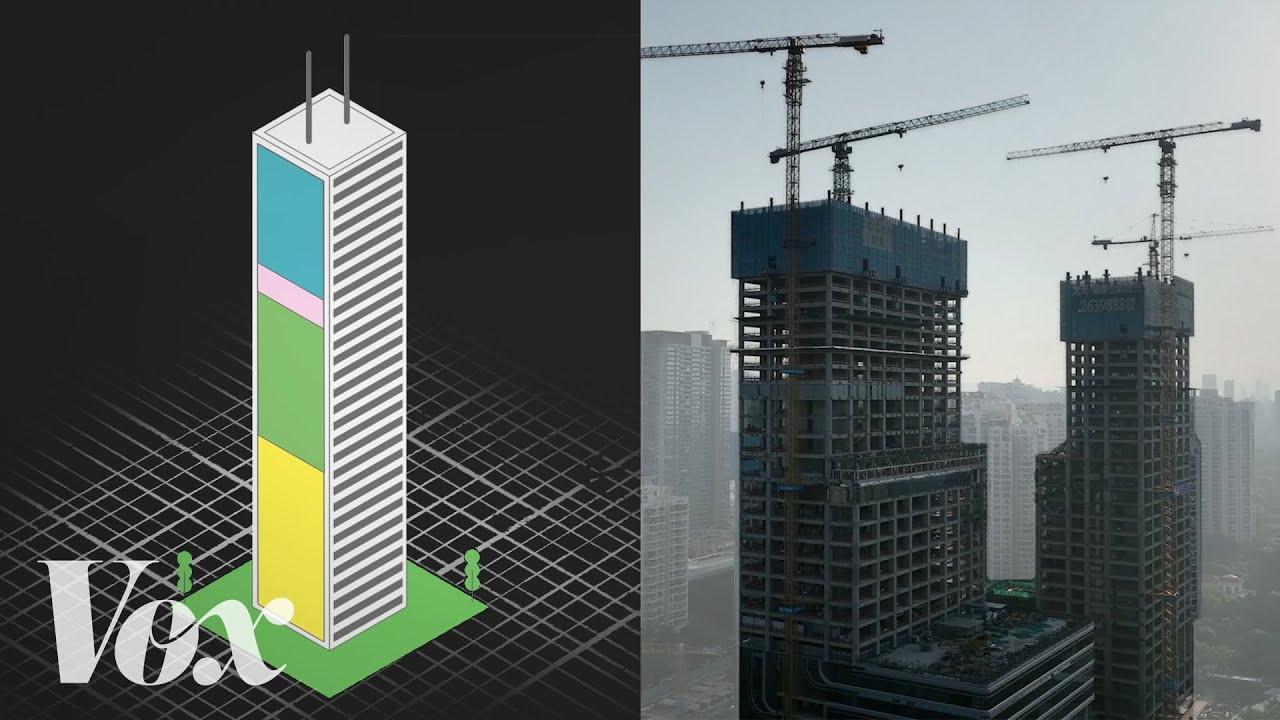
The big problem with cement, and how to fix it
5.0 / 5 (0 votes)