Design Mistakes You Must Avoid on Your New Electronic Product
Summary
TLDRIn this informative video, John Teal of Predictable Designs identifies 10 common mistakes in electronic hardware development, covering both technical and general design issues. He emphasizes the importance of designing for manufacturability, correct wireless circuit design, early cost estimation, and independent design reviews. Teal also addresses specific technical pitfalls such as improper PCB trace width, decoupling capacitor placement, and enclosure manufacturability. His insights aim to help engineers avoid costly errors and streamline the product development process.
Takeaways
- 🛠️ Design for Manufacturability (DFM) is crucial as it can significantly impact the time and cost of bringing a product to market, and should be considered from the early stages of product design.
- 📡 Proper PCB layout for wireless circuits is critical for maximum power transfer. Impedance matching with a 50-ohm transmission line and LC matching circuit is necessary for optimal performance.
- 💰 Estimating manufacturing costs early can prevent costly redesigns later. It's possible to make accurate cost estimates before the final product design is complete.
- 🔌 Ensuring sufficient width for high current PCB traces is important to avoid overheating and to safely carry the required current.
- 🔍 Getting an independent design review can help catch and correct potential mistakes before they become costly in terms of time and money.
- ⚡ Decoupling capacitors should be placed as close as possible to the component pins requiring stable voltage to ensure clean and stable power supply.
- 📦 Product enclosures must be designed with manufacturability in mind, considering the limitations and requirements of production methods like high-pressure injection molding.
- 🔌 Careful design of PCB landing patterns is necessary, especially when components are not included in standard libraries, to ensure compatibility with actual components.
- 🔗 Understanding the use of different types of PCB vias (through, blind, and buried) and their impact on manufacturability and cost is essential for efficient PCB design.
- ⚙️ Correct PCB layout for switching regulators is vital for their efficient operation, and following the layout guidelines provided in data sheets can prevent common mistakes.
- 🔄 The video emphasizes the importance of avoiding common design mistakes to streamline the development process and ensure the success of new electronic hardware products.
Q & A
What are the common design mistakes discussed in the video?
-The video discusses 10 common design mistakes, including failing to design for manufacturing, incorrect design of wireless circuits, waiting too long to estimate manufacturing costs, insufficient width for high current PCB traces, not getting an independent design review, incorrect use of decoupling capacitors, designing the enclosure for manufacturability issues, incorrect PCB landing patterns, designing a PCB with manufacturing or cost issues related to vias, and incorrect PCB layout of switching regulators.
Why is it important to consider manufacturability during the product design process?
-Considering manufacturability is essential because it can significantly affect the time and cost of bringing a product to market. A product that is difficult to manufacture can slow down production and increase costs, which can be detrimental to the product's success.
What is the significance of a transmission line in wireless circuit design?
-A transmission line is crucial for the maximum power transfer between a transceiver and an antenna. It must be designed with the correct impedance to ensure efficient power transfer and optimal wireless functionality.
Why is it a mistake to wait until the final prototype to estimate manufacturing costs?
-Waiting until the final prototype to estimate manufacturing costs can lead to unexpected expenses and redesigns, which can delay product development and increase costs. Estimating costs early allows for adjustments in the design to manage expenses more effectively.
What factors affect the width required for a high current PCB trace?
-The required width of a PCB trace for high current is affected by factors such as the trace's thickness (copper weight), whether the trace is on an internal or external layer, and the permissible temperature rise for that trace.
Why is an independent design review important before prototyping a product?
-An independent design review is important to identify and correct potential mistakes or oversights in the design. It can reduce the number of prototype iterations, save costs, and shorten the time to market.
How should decoupling capacitors be used in PCB design for optimal performance?
-Decoupling capacitors should be placed as close as possible to the pin requiring a stable voltage source. The output capacitor for the power supply regulator should also be placed close to the regulator's output pin to ensure a clean and stable voltage supply.
What are the challenges associated with designing a product enclosure for high volume production?
-High volume production, typically using high-pressure injection molding, requires adherence to strict design rules. Unlike 3D printing, which is forgiving, injection molding does not accommodate complex or intricate designs without significant modifications.
Why is it a mistake to manually draw PCB landing patterns without verifying against actual components?
-Manually drawing PCB landing patterns without verification can lead to errors in pin-to-pin spacing, which can make it impossible to solder parts onto the board. It's essential to verify the landing patterns against actual components to ensure a proper fit.
What are the implications of using through vias, blind vias, and buried vias in PCB design?
-Through vias connect all layers of a PCB, which can increase board size and reduce routing space. Blind and buried vias, while allowing for more compact designs, have strict layer connection rules and can significantly increase the cost of prototype boards. They should be used judiciously and only when necessary.
What are the key considerations for correctly laying out a switching regulator on a PCB?
-For a switching regulator, the PCB layout must follow strict design rules to ensure efficiency and proper operation. Components should not be randomly placed but arranged according to the manufacturer's recommendations, which are typically provided in the data sheet.
Outlines
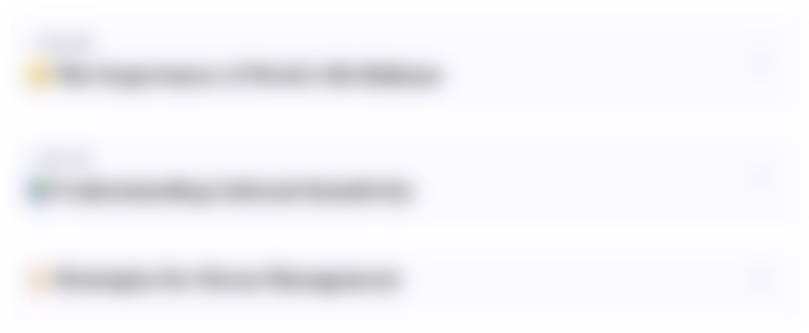
此内容仅限付费用户访问。 请升级后访问。
立即升级Mindmap
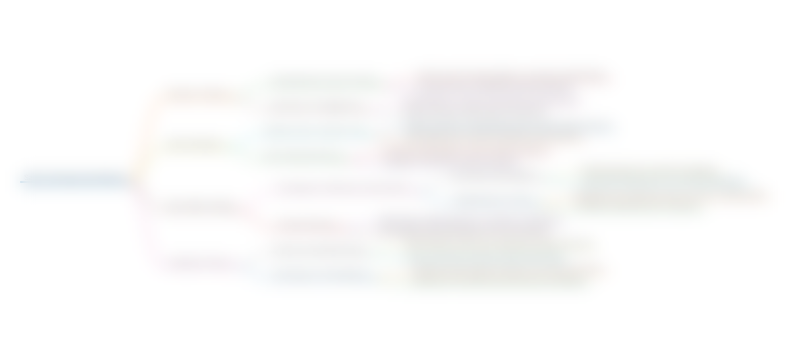
此内容仅限付费用户访问。 请升级后访问。
立即升级Keywords
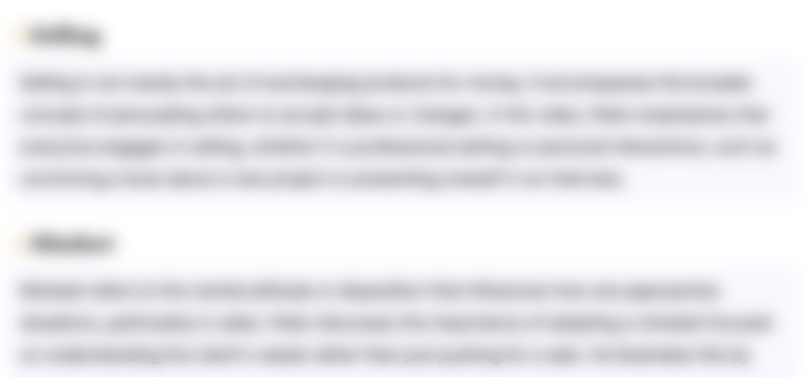
此内容仅限付费用户访问。 请升级后访问。
立即升级Highlights
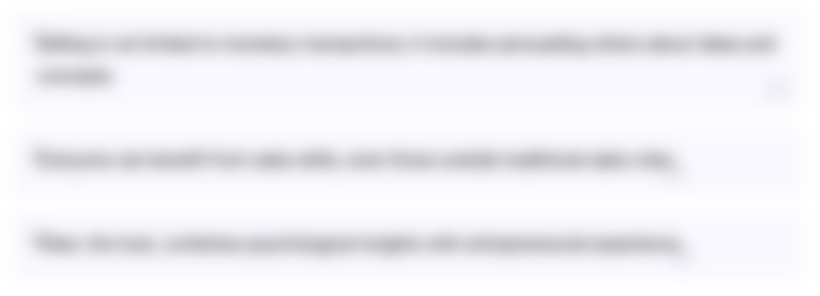
此内容仅限付费用户访问。 请升级后访问。
立即升级Transcripts
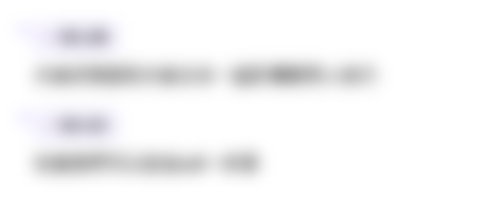
此内容仅限付费用户访问。 请升级后访问。
立即升级5.0 / 5 (0 votes)