Marking Tuner Positions, Headstock Veneer and Logo Inlay - A week in the Unquendor Guitars Workshop
Summary
TLDRIn this workshop video, Daniel takes viewers through the process of crafting two guitar necks, focusing on the intricate details of headstock veneer selection, tuner hole positioning, and inlay work. He discusses design decisions, such as choosing between light and dark veneers, and shares tips for precise work, like ensuring correct string pull alignment and avoiding tear-out during drilling. Daniel demonstrates his step-by-step method, from gluing and sanding veneers to drilling tuner holes and creating a custom logo inlay. The video culminates with the necks nearing completion, ready for attachment to guitar bodies in the next project stage.
Takeaways
- 😀 Daniel introduces his guitar workshop, showcasing his work on two necks and headstocks in the video.
- 😀 He discusses the process of choosing the right headstock veneer, experimenting with different thicknesses and colors of black limba wood.
- 😀 The decision-making process for selecting the headstock veneer is highlighted, with Daniel opting for a darker one for its pattern despite concerns about the contrast with black hardware.
- 😀 Daniel explains the importance of sanding by hand for the final pass to avoid creating dents, despite using a spindle sander for the majority of the sanding work.
- 😀 He demonstrates how to mark and measure the placement of tuner holes on the headstock, using both a full-size drawing template and hand measurements to ensure accuracy.
- 😀 The difficulty of working with black limba wood is highlighted, as pencil markings are hard to see, leading Daniel to use light lines and a protractor for better accuracy.
- 😀 Tuner hole placement is explained in detail, including offset measurements and ensuring equal spacing, with considerations for both straight and curved headstocks.
- 😀 Daniel ensures that the tuner positions are mirrored on both sides of the headstock to avoid trademark issues with other guitar brands.
- 😀 When drilling the tuner holes, Daniel emphasizes the use of a drill press, sharp drill bits, and backing material to prevent tear-out and ensure precision.
- 😀 Daniel shares his method for creating inlays for the headstock logo and mentions that the process will take several evenings, though sped up for the video audience.
- 😀 The video concludes with Daniel wrapping up his work on the necks, mentioning that the next step will be attaching them to guitar bodies in future videos.
Q & A
Why does Daniel prefer to use a combination of a full-size drawing and drawing on the headstock itself when determining the tuner hole positions?
-Daniel combines both methods to ensure that the string pull is as straight as possible, while also confirming that the tuner hole positions align with his template for accurate placement.
What challenge does Daniel face when using black limba for the headstock veneer?
-The main challenge with black limba is that pencil lines are difficult to see clearly on the material, which can make marking precise measurements challenging.
Why does Daniel prefer to sand the headstock veneer by hand after using the spindle sander?
-Daniel prefers to do the final pass by hand to avoid creating dents, which can occur if the spindle sander is left in one spot for too long, even with fine grit sanding.
How does Daniel ensure that the tuner holes are accurately spaced and aligned?
-Daniel measures the distances carefully, first determining the position of the first tuner hole, then uses a 26mm spacing for the remaining holes, ensuring the holes are aligned with the string positions.
What type of drill bit does Daniel recommend for drilling tuner holes and why?
-Daniel recommends using brad point drill bits because they provide a cutting action, which helps reduce tear-out compared to regular drill bits that use a scraping action.
Why does Daniel use a drill press rather than drilling by hand?
-Daniel prefers a drill press because it offers greater accuracy and minimizes tear-out, particularly when drilling through delicate areas like the headstock.
What precaution does Daniel take to prevent tear-out when drilling through the headstock?
-Daniel uses a backing material under the headstock, which helps prevent tear-out and ensures cleaner holes, especially when using masking tape and super glue to secure the backing.
How does Daniel decide on the thickness of the headstock veneer?
-Daniel adjusts the thickness of the headstock veneer based on the clamping range of the tuners, ensuring that the veneer is thick enough for a secure bond but not overly bulky.
Why does Daniel take the time to ensure the tuner holes are positioned carefully, even when they are less visible?
-Daniel emphasizes the importance of accuracy with the tuner hole positions because they directly affect the tuning stability and appearance of the guitar, and he wants to avoid any mistakes, even if the holes are not highly visible.
What is the purpose of the headstock logo inlay, and how does Daniel approach this task?
-The headstock logo inlay adds a personalized touch to the guitar. Daniel mentions he has done many inlays before and will speed up the process in the video using time-lapse footage, taking two to three evenings to complete.
Outlines
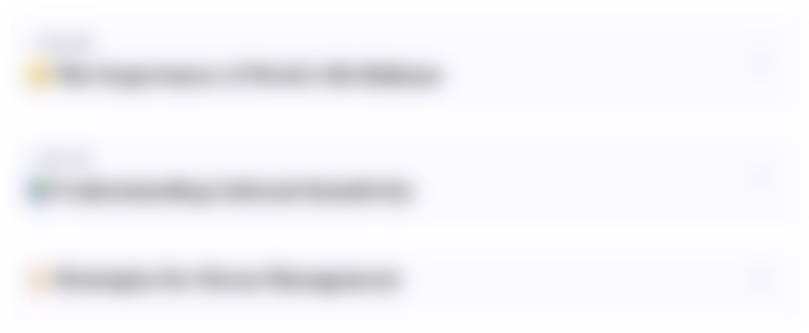
此内容仅限付费用户访问。 请升级后访问。
立即升级Mindmap
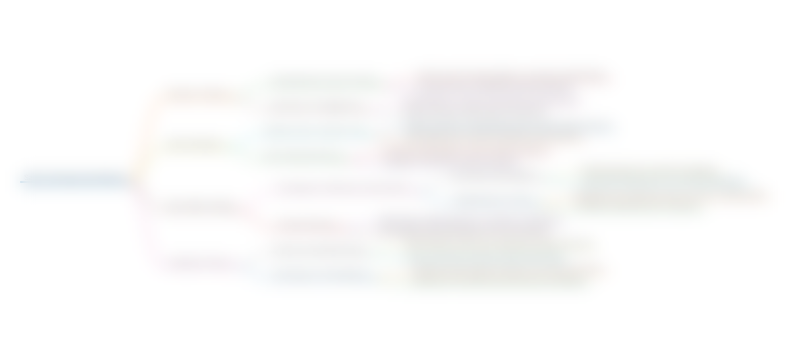
此内容仅限付费用户访问。 请升级后访问。
立即升级Keywords
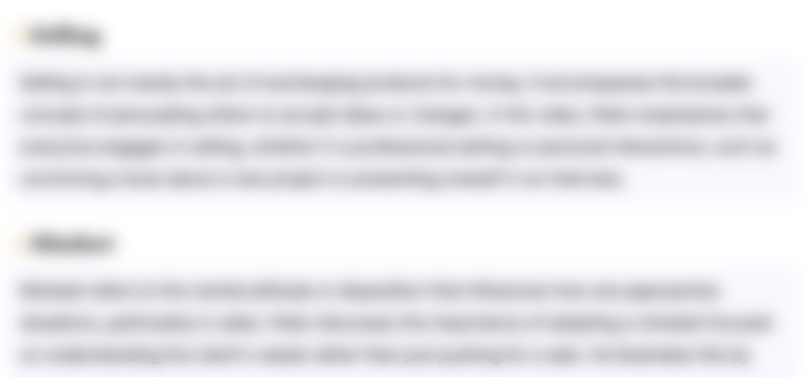
此内容仅限付费用户访问。 请升级后访问。
立即升级Highlights
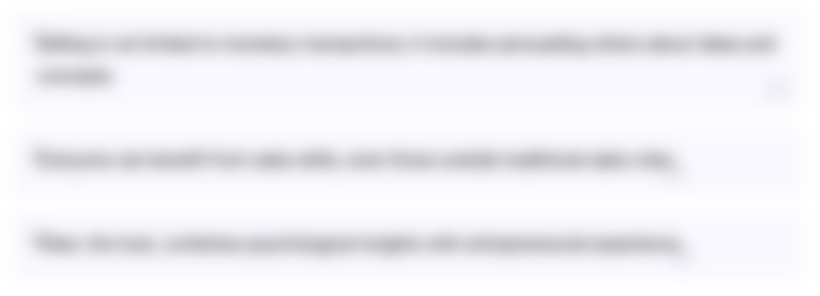
此内容仅限付费用户访问。 请升级后访问。
立即升级Transcripts
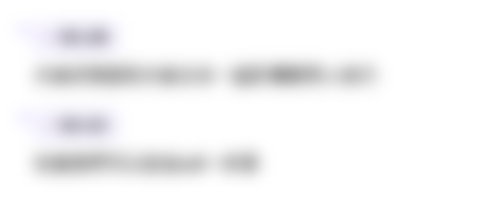
此内容仅限付费用户访问。 请升级后访问。
立即升级浏览更多相关视频

HASIL HUTAN YANG DIOLAH MENJADI KARYA SENI YG INDAH,TAS ROTAN

3rd Grade - Week 7 Homework
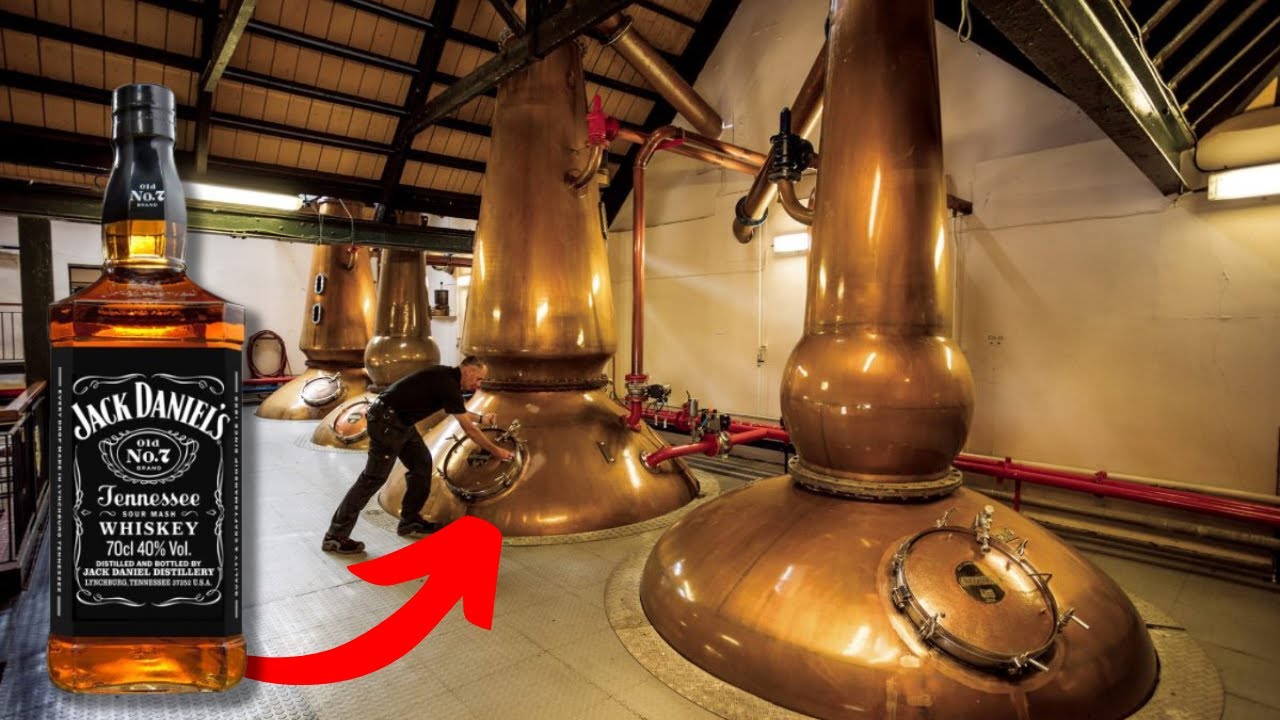
Como o WHISKY é feito - Processo Industrial

今更聞けない「カスタム」「スタンダード」の違い。色の違いだけじゃない、レスポールのバリエーションについて解説【ギターバイヤー増田】

Der Erzgießer von Nürnberg | Der Letzte seines Standes

How to make a creative cardboard mini marble track - DIY tutorial
5.0 / 5 (0 votes)