CFD Simulation Workflow — Lesson 2
Summary
TLDRThis video provides a comprehensive overview of the CFD (Computational Fluid Dynamics) process using Ansys Fluent. It covers the key stages, from defining project goals before starting the software to problem identification, domain selection, geometry creation, mesh generation, solver setup, and solution computation. Emphasis is placed on the importance of clear objectives, appropriate physical models, mesh resolution, and ensuring that results are converged. The video concludes by stressing the need for careful post-processing and verification to ensure the accuracy and relevance of simulation results, ultimately leading to meaningful engineering insights.
Takeaways
- 😀 Clearly define project goals before starting any CFD simulation to ensure a focused and efficient process.
- 😀 Pre-processing involves defining the project scope, selecting the computational domain, and determining boundary conditions.
- 😀 Simulate only the most relevant part of the system to save computational time and resources.
- 😀 Use simplifications like quasi-2D or axisymmetric models when appropriate to reduce complexity and simulation time.
- 😀 The geometry for the CFD model should represent the fluid region and exclude unnecessary features that complicate the mesh.
- 😀 Meshing should be done carefully to ensure the grid captures regions with high flow gradients while considering available resources.
- 😀 Set up the solver by defining material properties, selecting physical models, and providing boundary conditions and initial values.
- 😀 Convergence is achieved when solution variables no longer change with iterations, and residuals decrease to a set target level.
- 😀 Post-processing involves visualizing the flow patterns and extracting numerical data to verify the simulation results.
- 😀 Always verify the accuracy of the results by questioning the assumptions, models, and boundary conditions used in the simulation.
- 😀 Mesh independence and numerical checks are essential to ensure the solution is valid and free from computational errors.
Q & A
What is the first stage of the CFD process?
-The first stage of the CFD process is problem identification, which occurs before any software is opened. It involves defining the project goals, considering modeling options, and determining if CFD is an appropriate tool for the problem.
Why is it important to define project goals before starting a CFD simulation?
-Defining project goals is crucial because it ensures clarity on what information the simulation should provide, such as pressure drop or mass flow rate. It also helps in determining the necessary modeling options and level of accuracy required.
What factors should be considered when selecting the boundaries of the computational domain?
-When selecting boundaries, it is important to consider where enough information is available to define boundary conditions. Boundaries should be placed where flow data is known, and if uncertain, they might be placed further upstream. It's also essential to consider simplifications, such as quasi-2D or axi-symmetric models.
How does symmetry or periodicity affect the CFD model?
-If symmetry or periodicity exists in the flow or geometry, it allows for smaller models and faster computation times. However, it's essential to ensure that not just the geometry, but also boundary conditions and flow, exhibit symmetry or periodicity.
What is the role of geometry simplifications in CFD modeling?
-Simplifying geometry, such as removing unnecessary features like bolts or fillets, can help reduce the complexity of the model, lower the number of control volumes, and decrease calculation times. These simplifications should preserve the essential flow characteristics.
Why is mesh creation an important step in pre-processing?
-Mesh creation is critical because the mesh resolution impacts the accuracy of the simulation. A finer mesh is needed in regions with high gradients in flow or temperature fields, but it must also be balanced with computational resources to avoid excessive memory use.
What are the key considerations when setting up the CFD solver?
-When setting up the solver, key considerations include defining material properties, selecting the appropriate physical models (e.g., turbulence or combustion models), setting boundary conditions, providing initial values, and adjusting solver control settings to suit the problem.
How is convergence checked during the CFD solution process?
-Convergence is checked by monitoring residuals, which indicate how close the solution is to satisfying the conservation equations. Additional checks include monitoring quantities of interest, like drag or pressure drop, to ensure they stabilize over iterations.
What should be done if the solution has converged but may not be accurate?
-After achieving a converged solution, it's important to verify the assumptions and models used in the simulation. Revising the model to test these assumptions can help ensure that the results are valid and that potential issues, such as incorrect boundary conditions or turbulence models, are addressed.
What is the significance of post-processing in CFD simulations?
-Post-processing involves analyzing the results through solution visualization (such as contour plots or vector plots) and extracting numerical data (such as forces, moments, and heat transfer coefficients). It helps verify the accuracy of the solution and understand key flow features.
Outlines
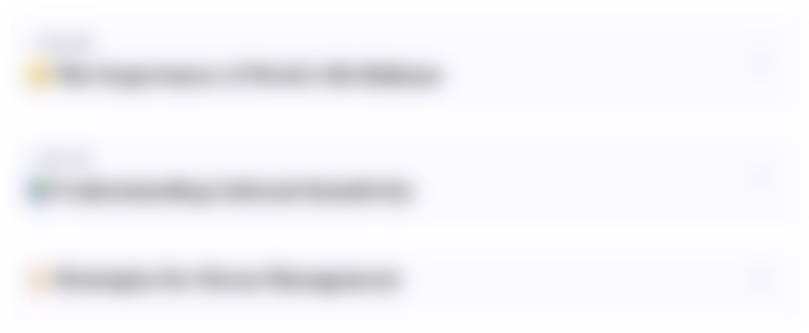
此内容仅限付费用户访问。 请升级后访问。
立即升级Mindmap
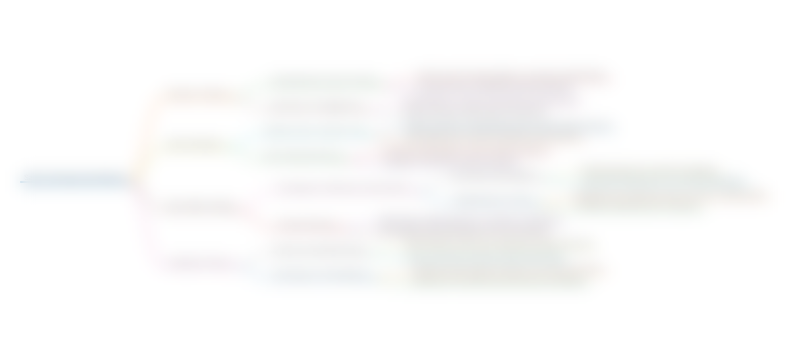
此内容仅限付费用户访问。 请升级后访问。
立即升级Keywords
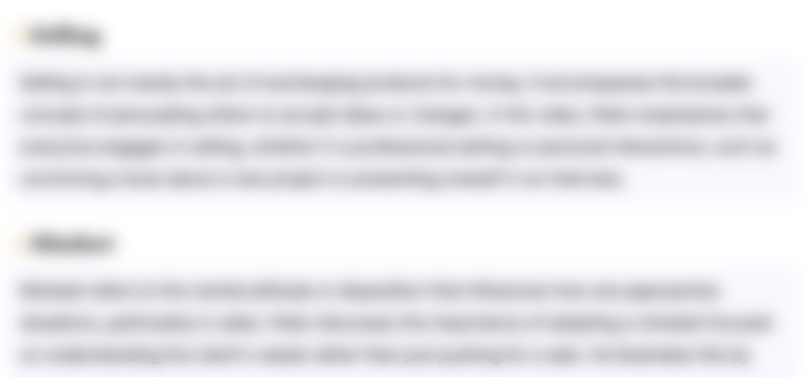
此内容仅限付费用户访问。 请升级后访问。
立即升级Highlights
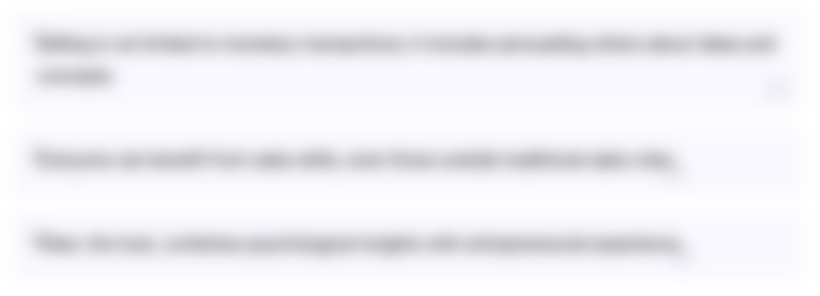
此内容仅限付费用户访问。 请升级后访问。
立即升级Transcripts
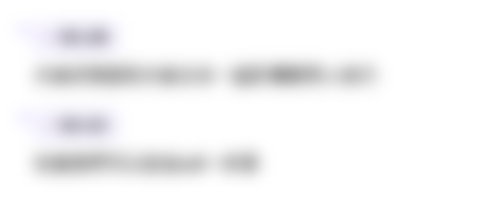
此内容仅限付费用户访问。 请升级后访问。
立即升级浏览更多相关视频
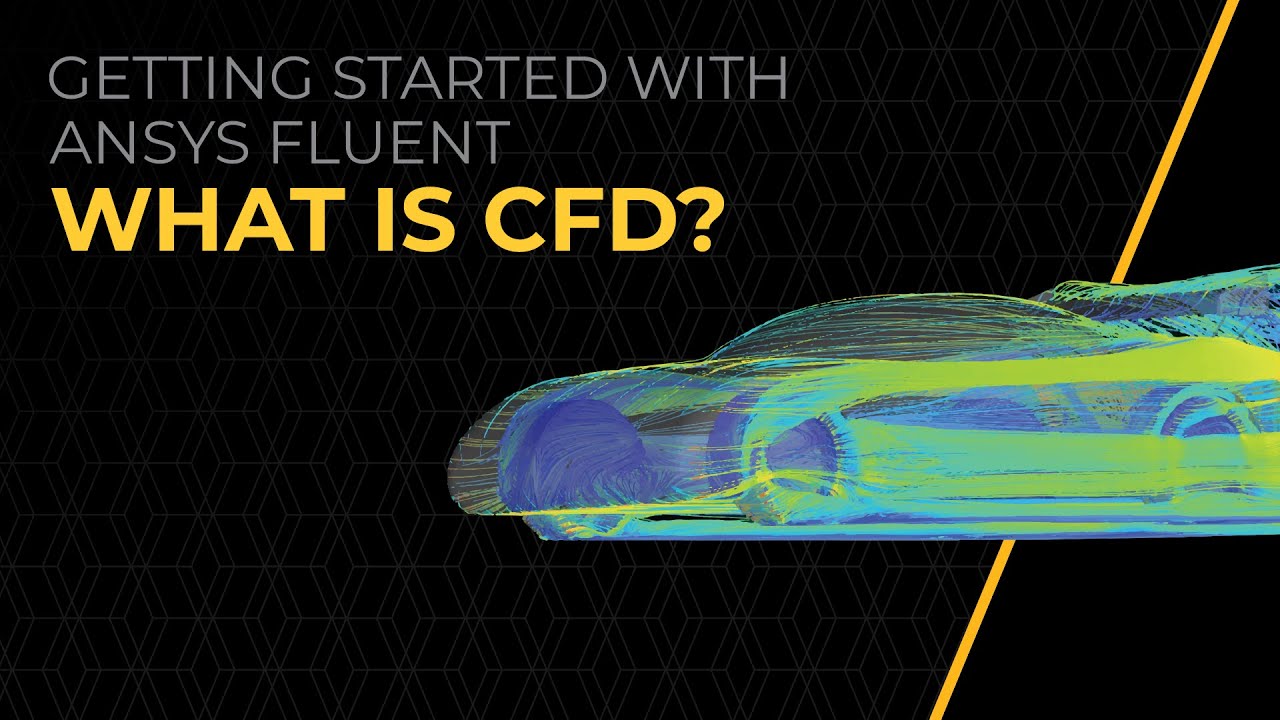
What is CFD? — Lesson 1

How to Specify Materials in Ansys Fluent — Lesson 4
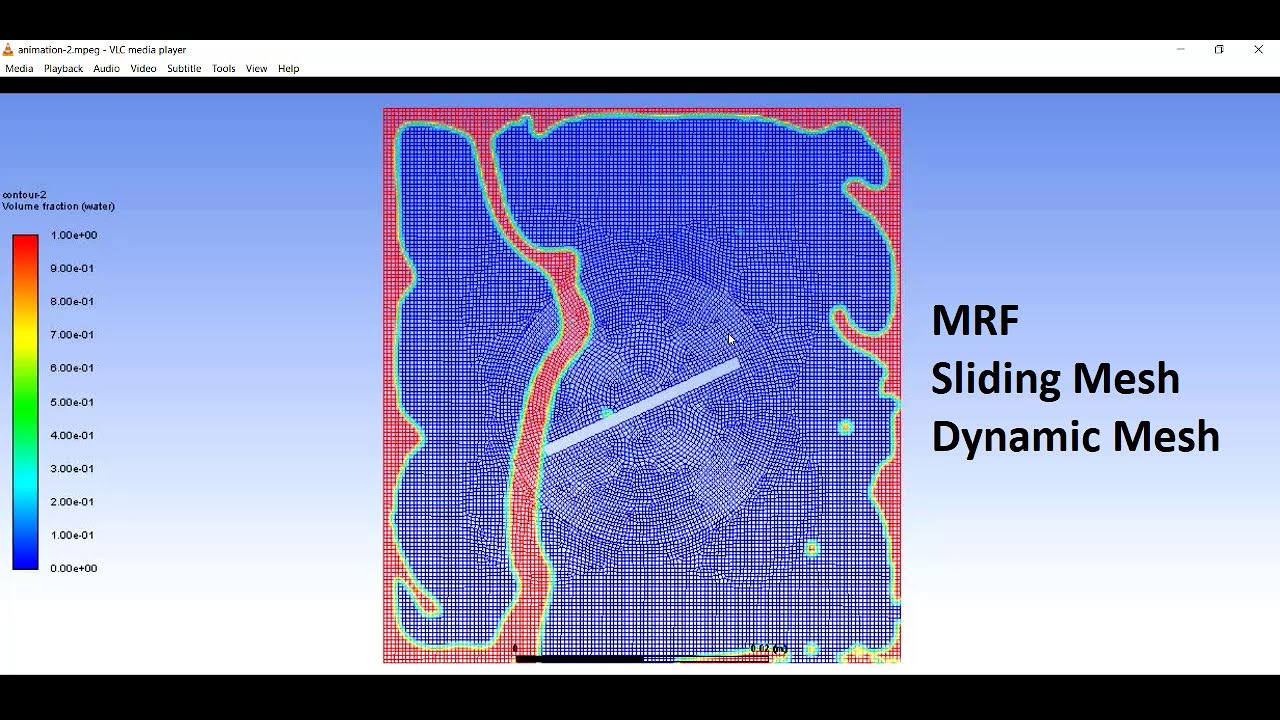
MRF,Sliding Mesh and Dynamic Mesh|| Differences With Simulations for better understanding

How to Mesh with Watertight Geometry Workflow – User Interface – Ansys Fluent Meshing
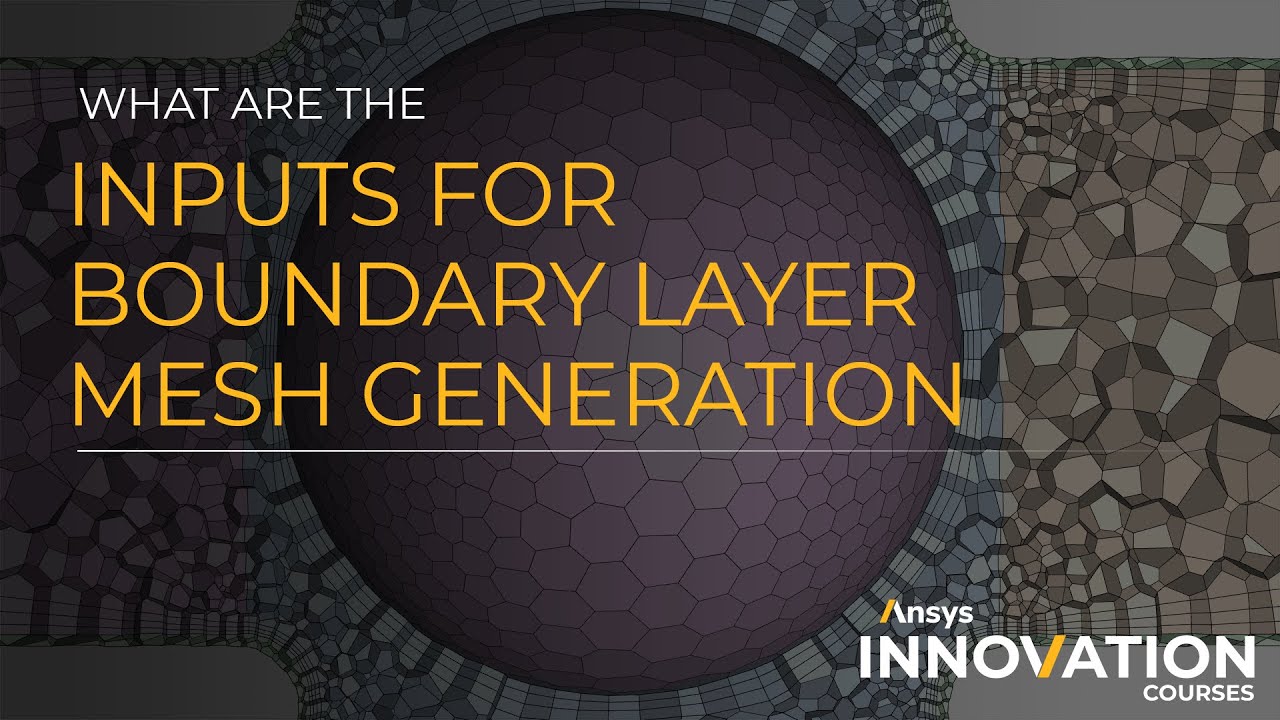
Inputs for Boundary Layer Mesh Generation in Ansys Fluent Meshing Watertight Geometry Workflow
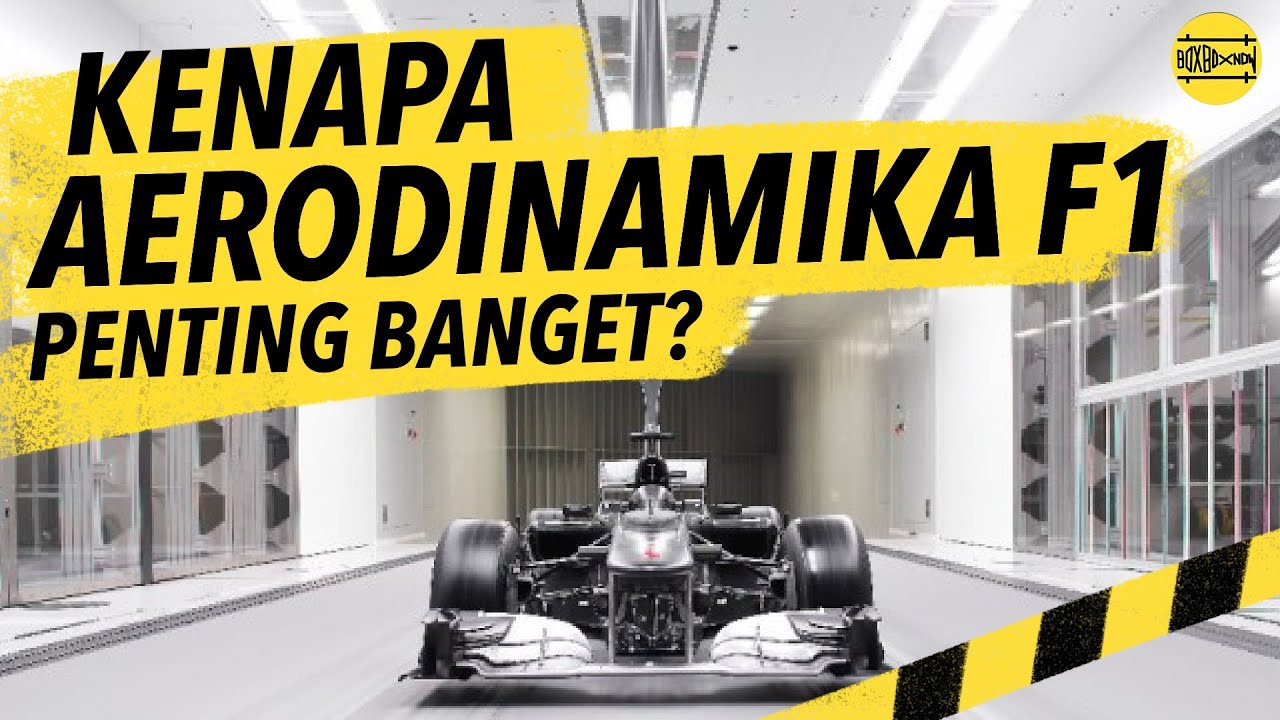
Semua yang lu perlu tahu soal aerodinamika di F1
5.0 / 5 (0 votes)