Hazard Identification - The Safety Inspection
Summary
TLDRThis video outlines the essential steps involved in conducting a safety inspection in the workplace. It emphasizes the importance of identifying hazards, learning about work tasks, and monitoring existing safety controls. Key activities include inspecting equipment like fire extinguishers and forklifts, ensuring proper maintenance and training, and addressing electrical hazards. The script stresses the value of teamwork and clear communication within the Safety Committee, the importance of documenting findings accurately, and prioritizing corrective actions. The goal is to continuously improve workplace safety to prevent injuries and illnesses.
Takeaways
- 😀 Safety inspections are essential for preventing injuries and illnesses in the workplace by identifying hazards and recommending corrective actions.
- 😀 The safety committee should listen to workers and supervisors, learn about job tasks, and identify both existing and potential hazards.
- 😀 Inspections should focus on determining the underlying causes of hazards, monitoring hazard controls, and ensuring corrective actions are taken.
- 😀 A key part of the inspection is identifying out-of-place items, trip hazards, and ensuring exits are clear and signage is in place.
- 😀 Electrical hazards, such as reversed polarity in outlets, should be prioritized during safety inspections.
- 😀 Fire extinguisher checks are vital, ensuring they are unobstructed, in place, and in good condition, with the pressure gauge in the correct range.
- 😀 Forklift safety requires a review of operator checklists, including maintenance checks for brakes, lights, and engine functionality.
- 😀 Machinery must be inspected for proper guarding, correct lockout procedures, and effective communication of hazards using proper signage.
- 😀 Shadow boards should be checked to ensure tools are in good condition and correctly placed, with an updated inventory list.
- 😀 Eye-wash stations must be properly maintained, with plumbed stations being checked for water flow, and portable stations for fluid changes.
- 😀 After completing the inspection, prioritize hazards by urgency, create an action plan for corrective actions, and monitor progress for continuous safety improvement.
Q & A
What is the primary goal of safety inspections in the workplace?
-The primary goal of safety inspections is to identify hazards by examining workplace conditions or practices, allowing for necessary changes to be made to prevent injuries and illnesses.
Why is it important to listen to the concerns of workers and supervisors during a safety inspection?
-Listening to the concerns of workers and supervisors ensures that you gather input from those directly involved in the work, providing valuable insights into potential hazards or issues that might not be immediately apparent.
What should safety committee members look for during their inspection of the workplace?
-Safety committee members should look for existing and potential hazards, monitor hazard controls that are already in place, and recommend corrective actions to address any identified hazards.
What is the significance of identifying the underlying causes of hazards during safety inspections?
-Identifying the underlying causes of hazards helps address the root issues, not just the symptoms, ensuring that corrective actions prevent future occurrences rather than offering temporary fixes.
Why is it necessary to monitor hazard controls such as personal protective equipment and engineering controls?
-Monitoring hazard controls ensures they are functioning properly and continue to protect workers from identified hazards, contributing to the overall effectiveness of the safety program.
What are some common hazards that need to be checked during workplace inspections?
-Common hazards include electrical hazards (like reversed polarity in outlets), fire extinguisher accessibility and condition, forklift operation procedures, machine guarding, and eye-wash station functionality.
How should fire extinguishers be inspected during a safety inspection?
-Fire extinguishers should be inspected for visibility, proper placement, intact locking pins, unbroken tamper seals, operable pressure gauges, and any physical damage or corrosion. The last professional service date should also be verified.
What should be included in the inspection of forklifts in a workplace?
-Forklift inspections should include checking the operator checklist for brakes, steering, seatbelts, lights, and engine maintenance, as well as conducting a walk-around to inspect tires, wheels, hydraulics, and the general condition of the vehicle.
Why is it important to verify that employees working with machinery are properly trained?
-Ensuring that employees are properly trained in machinery operation minimizes the risk of accidents and injuries by ensuring they understand safe usage practices and how to handle potential hazards effectively.
How should safety inspection reports be written and prioritized?
-Safety inspection reports should be detailed, specifying exactly what was found and where, including a priority level (A, B, or C) to indicate the urgency of corrective action. Recommendations for how to fix each hazard should be clearly outlined with deadlines if possible.
Outlines
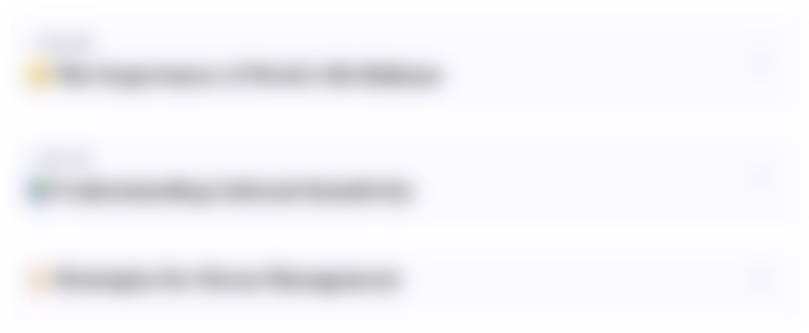
此内容仅限付费用户访问。 请升级后访问。
立即升级Mindmap
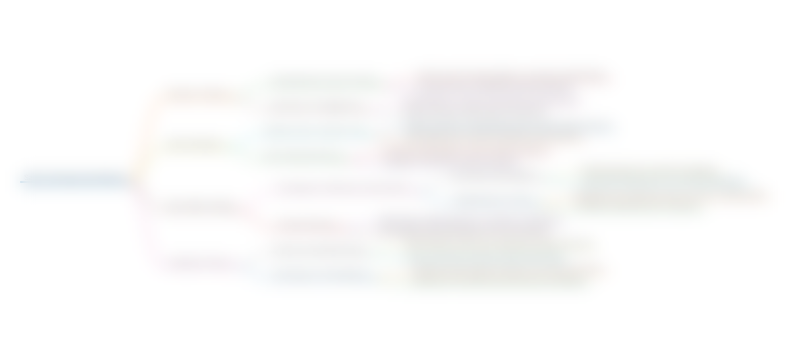
此内容仅限付费用户访问。 请升级后访问。
立即升级Keywords
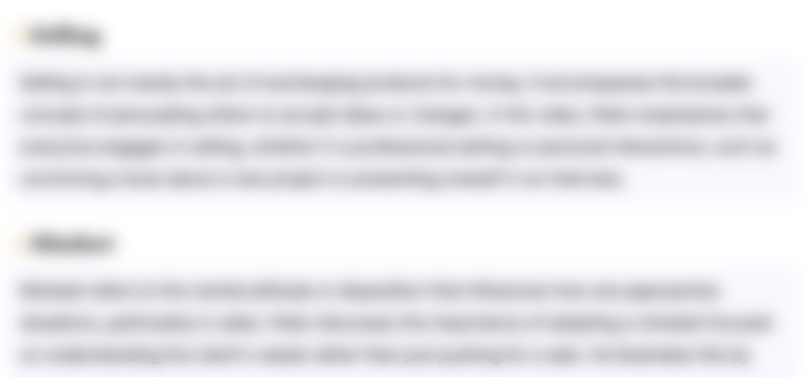
此内容仅限付费用户访问。 请升级后访问。
立即升级Highlights
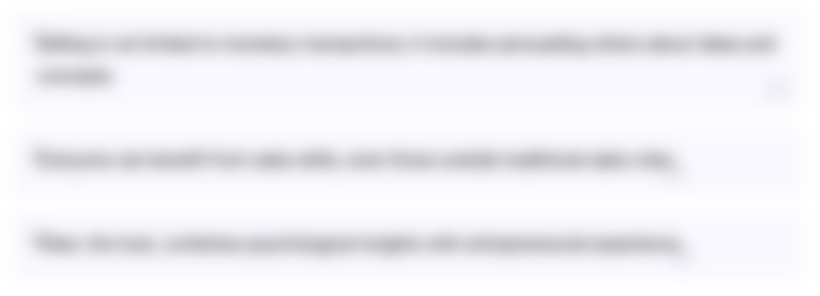
此内容仅限付费用户访问。 请升级后访问。
立即升级Transcripts
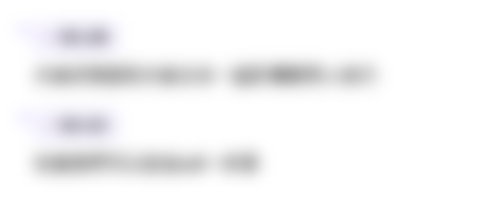
此内容仅限付费用户访问。 请升级后访问。
立即升级5.0 / 5 (0 votes)