What Is The Last Planner System?
Summary
TLDRThe video explains the Last Planner System, a collaborative planning method used in construction to ensure reliable scheduling and execution. The system involves foremen and superintendents—known as 'last planners'—working together to create short-interval schedules and remove roadblocks. Key components include the master schedule, pull plans, look-ahead schedules, weekly work plans, and daily huddles. By fostering commitment from the team, this system improves project efficiency and ensures that tasks are completed on time. Viewers are encouraged to implement these steps and utilize resources like 'The Lean Builder' to learn more.
Takeaways
- 🔧 The Last Planner System is a collaborative planning system that involves foremen and superintendents (last planners) to ensure reliable short-interval scheduling.
- 👷 The 'last planner' refers to the last person in the planning cycle, often the foreman or superintendent, who leads a team on the ground.
- 📅 The system uses several schedule formats: master schedule, pull plan, look-ahead, weekly work plan, and daily plan, designed to improve workflow coordination and communication.
- 🎯 The master schedule outlines the overall project duration and milestones, while pull plans ensure activities are done in the correct sequence.
- 🗓️ A six-week look-ahead helps teams identify potential roadblocks by checking if activities are 'ready' based on manpower, materials, tools, and equipment availability.
- ✅ The weekly work plan requires trades to commit to specific activities for the week, ensuring alignment and commitment across the team.
- 📊 Teams track progress with the Percent Planned Complete (PPC) metric, which measures how many tasks were completed on time, with a goal of achieving over 80% PPC.
- 👥 Collaborative meetings, such as weekly work planning and daily huddles, are essential for maintaining team alignment and addressing roadblocks.
- 🧠 Psychological safety and buy-in are key to the success of the Last Planner System. Tradespeople are more likely to commit if they feel heard and involved in the planning process.
- 📖 Additional resources, such as 'The Lean Builder' book and blog, provide further insights and guidance on implementing the Last Planner System.
Q & A
What is the Last Planner System (LPS)?
-The Last Planner System is a collaborative planning system where 'last planners'—usually foremen or superintendents—collaborate to create reliable short-interval scheduling. It focuses on commitment, communication, and accountability in planning construction projects.
Who are the 'last planners' in the Last Planner System?
-The 'last planners' are typically the foremen or superintendents—the people on the ground leading crews. They are the last individuals in the planning cycle and are responsible for adding wisdom and validity to the project plans.
Why was the Last Planner System created?
-The Last Planner System was created to foster collaboration, improve communication, and create a culture where a construction team works as an integrated unit. It helps ensure more reliable promises in scheduling and project execution.
What is the role of the master schedule in LPS?
-The master schedule identifies the total project duration and key milestones. It serves as a high-level plan, and there are two common methods for creating it: CPM (Critical Path Method) and tact planning. The presenter prefers tact planning.
What is 'pull planning' in LPS?
-Pull planning is a collaborative process where the team, especially the last planners, work backward from a milestone to create a proper sequence of activities. This ensures that each activity is ready and follows the correct order.
What is the 'six-week make-ready look-ahead' in LPS?
-The six-week make-ready look-ahead is a planning tool where the team looks six weeks into the future to ensure that upcoming tasks have the necessary manpower, materials, tools, and equipment. It helps to identify and remove roadblocks.
What is a weekly work plan in LPS?
-The weekly work plan is a one-week schedule where all trades commit to completing specific tasks. It focuses on 100% commitment from all parties and ensures activities are properly coordinated.
What does PPC stand for in LPS?
-PPC stands for Percent Planned Complete or Percent Promises Complete. It measures how many planned activities were completed as promised. A PPC score over 80% generally correlates with projects being on or under budget and schedule.
Why is it important for the last planners to 'weigh in and buy in' to the plan?
-If last planners are actively involved in planning and feel like their input is valued, they are more likely to commit to the schedule. This makes the plan more realistic and improves the chances of successfully executing the work.
What are the four steps to implementing LPS?
-The four steps to implementing LPS are: (1) Start holding daily huddles with foremen to discuss the day's plan, (2) Use visual planning formats to make the plan visible to the team, (3) Focus meetings on identifying and removing roadblocks, and (4) Implement the entire LPS system and track progress using Percent Plan Complete (PPC).
Outlines
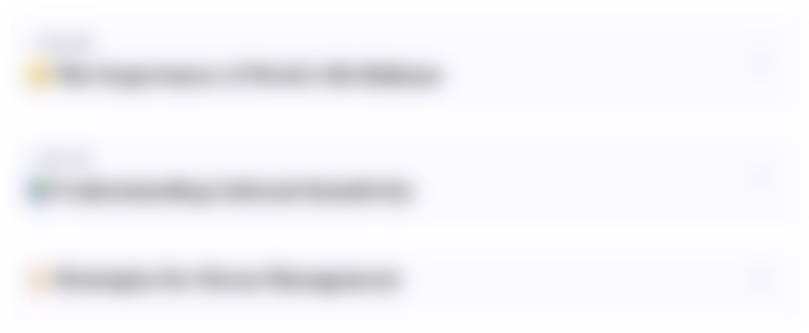
此内容仅限付费用户访问。 请升级后访问。
立即升级Mindmap
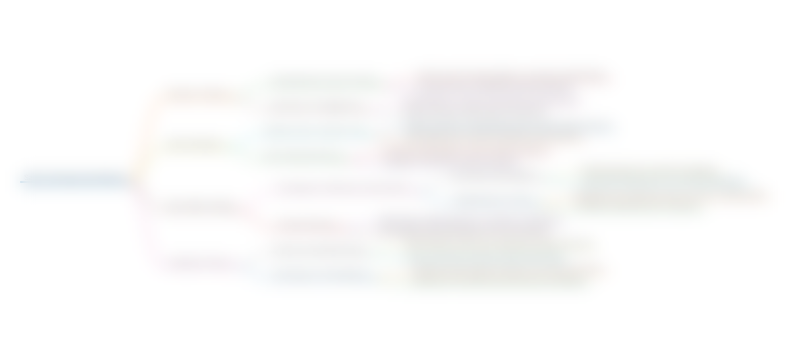
此内容仅限付费用户访问。 请升级后访问。
立即升级Keywords
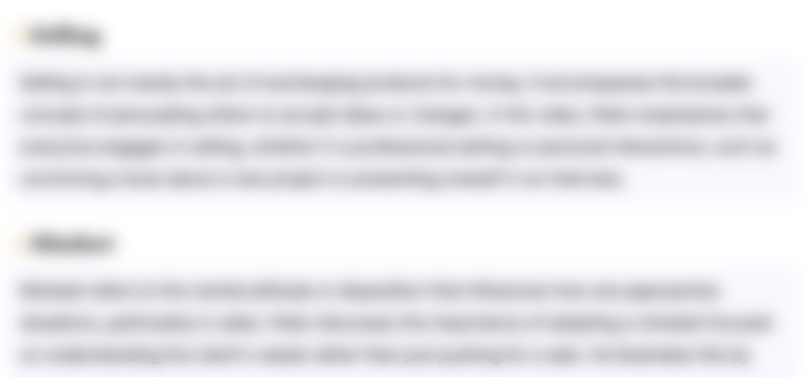
此内容仅限付费用户访问。 请升级后访问。
立即升级Highlights
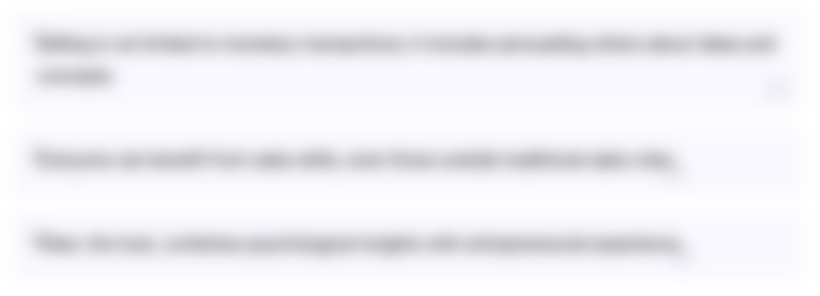
此内容仅限付费用户访问。 请升级后访问。
立即升级Transcripts
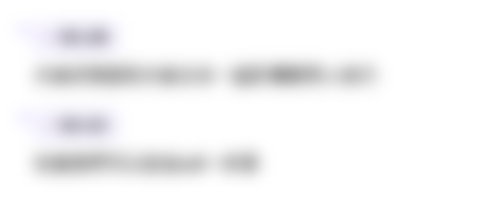
此内容仅限付费用户访问。 请升级后访问。
立即升级浏览更多相关视频
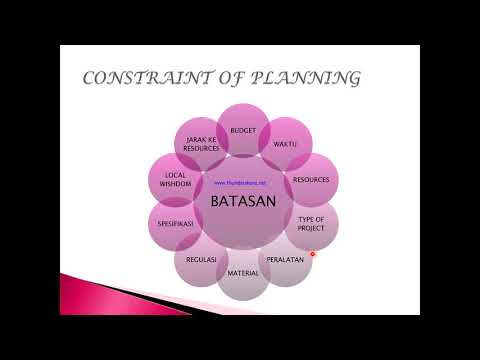
01 Penjadwalan Proyek

ILMU UKUR TANAH PEKERJAAN UITZET DAN BOUWPLANK
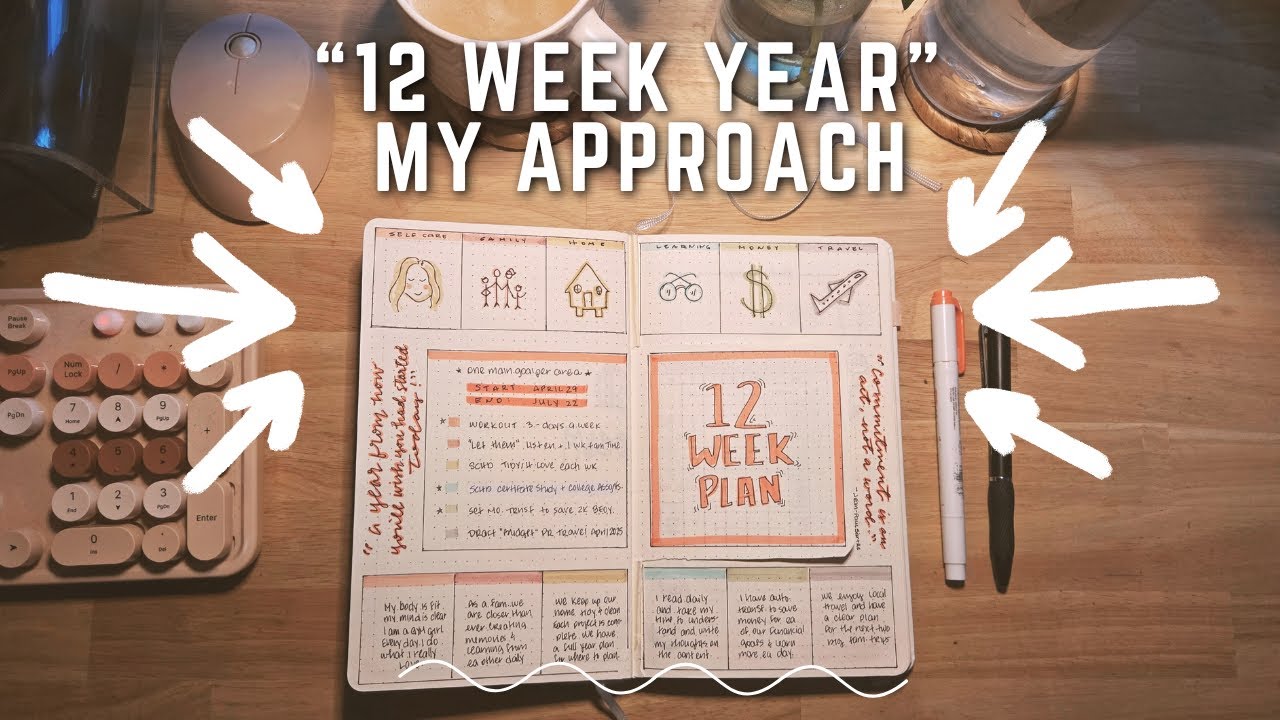
Achieve your goals in just 12 weeks | My 12 Week Year Approach
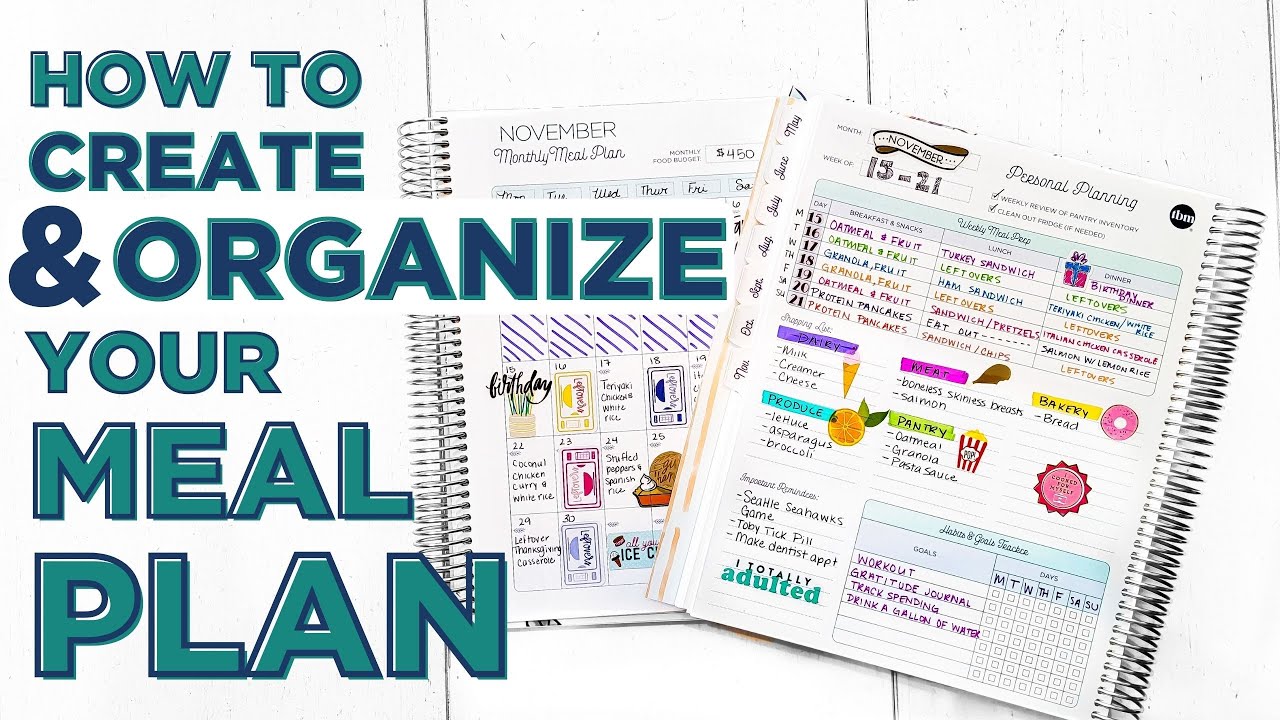
Creating & Organizing Your Meal Plan | Organization Tips + Meal Plan

The Most Successful Idea in Computer Science

Project Scheduling Levels & Scheduling Engineer Responsibilities
5.0 / 5 (0 votes)