Four Principles TPM
Summary
TLDRTotal Productive Maintenance (TPM) is a comprehensive approach to enhancing manufacturing efficiency by integrating preventive maintenance, total quality control, and employee involvement. It involves creating a database for equipment maintenance, standardizing processes, and conducting planned maintenance to reduce breakdowns and improve machine performance. TPM ensures a clean and safe work environment, with employees responsible for equipment upkeep. By monitoring key process indicators, TPM promotes continuous improvement, leading to reduced downtime and increased productivity.
Takeaways
- 🔧 TPM stands for Total Productive Maintenance, which is a lean approach to improving the manufacturing process.
- 👷 TPM combines preventive maintenance with total quality control and total employee involvement.
- 🚫 The traditional 'fix it when it breaks' approach can lead to significant downtime and larger problems.
- 📈 TPM focuses on eliminating major equipment-related losses to improve overall efficiency.
- 📚 TPM involves creating a comprehensive database for each piece of equipment to guide maintenance.
- 🛠️ Employees are trained to understand what, when, and how to maintain equipment based on the database.
- 🔄 Standardization of processes is key, including setting key parameters and training on identifying losses.
- 📅 Planned maintenance is scheduled to maintain each part of the machine at recommended intervals.
- 🧹 Keeping equipment clean is part of TPM, helping to detect failures early and avoid breakdowns.
- 🔄 TPM includes a continuous improvement process with key process indicators monitored and managed.
- 💼 TPM leads to reduced breakdowns, improved machine speed, and quality, with efficient systems in place.
Q & A
What is Total Productive Maintenance (TPM)?
-TPM is a lean approach to improving the manufacturing process by combining preventive maintenance with total quality control and total employee involvement.
Why is TPM important for a business?
-TPM is crucial as it helps eliminate major equipment-related losses, reduces breakdowns, improves machine speed and quality, and ensures efficient operations even when issues arise.
What are the four principles of TPM mentioned in the script?
-The script does not explicitly mention four principles but outlines seven pillars for a practical and sustainable TPM approach.
What are the seven pillars of TPM?
-The script does not detail each of the seven pillars but implies they involve equipment history knowledge, standardization, planned maintenance, cleanliness, spare parts analysis, trial standard operating procedures, and continuous improvement.
How does TPM help in maintaining equipment?
-TPM helps by building a database for each piece of equipment, providing employees with the skills to maintain equipment correctly, and scheduling routine maintenance to improve machine performance.
What is the significance of knowing equipment history in TPM?
-Knowing equipment history allows for the creation of a database that eliminates guesswork, ensuring employees know exactly what to maintain, when, and how long it will take.
How does TPM approach the issue of machine cleanliness?
-TPM includes keeping equipment clean as part of its procedure, where each team member is responsible for a clean, safe work environment. Regular cleaning can detect failures early, preventing sudden breakdowns.
What role do spare parts play in TPM?
-TPM involves analyzing spare parts based on consumption and past purchases to ensure that parts that wear out often are always accessible.
How does TPM address machine breakdowns?
-TPM reduces the occurrence of machine breakdowns through planned maintenance and continuous improvement processes, ensuring that when issues do arise, there is minimal downtime and wasted resources.
What is the 'pit-stop approach' mentioned in the script?
-The 'pit-stop approach' refers to a method of trialing standard operating procedures where what works and what doesn't is analyzed, and key process indicators are monitored for continuous improvement.
How does TPM involve total employee involvement?
-TPM involves all employees by assigning responsibility for maintenance and cleanliness, providing training on process measurement and loss identification, and encouraging a culture of continuous improvement.
Outlines
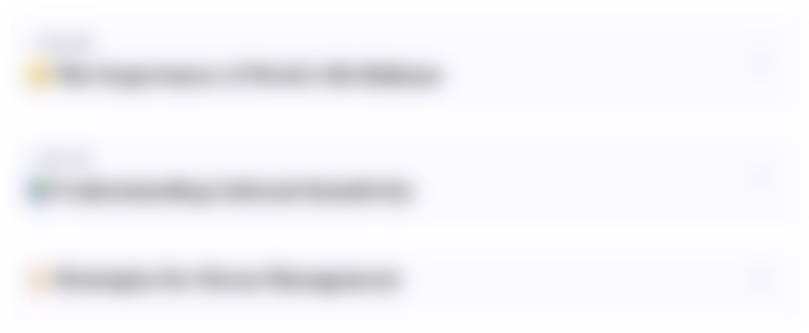
此内容仅限付费用户访问。 请升级后访问。
立即升级Mindmap
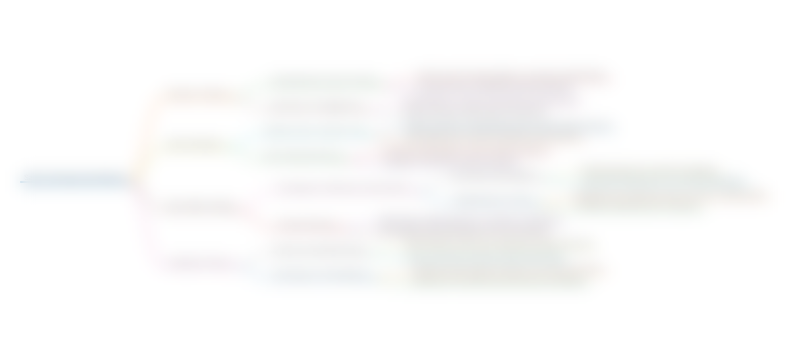
此内容仅限付费用户访问。 请升级后访问。
立即升级Keywords
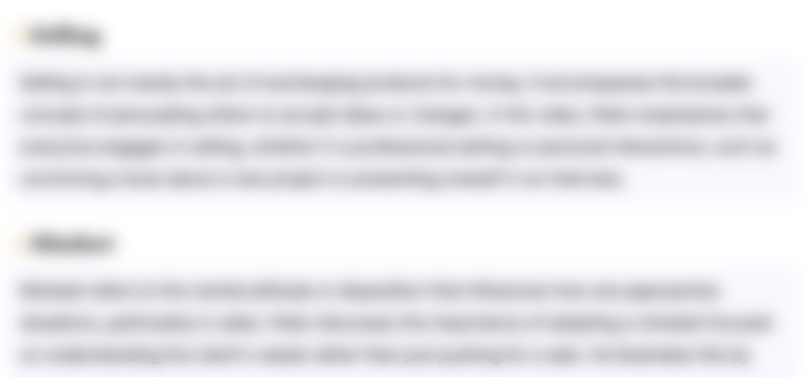
此内容仅限付费用户访问。 请升级后访问。
立即升级Highlights
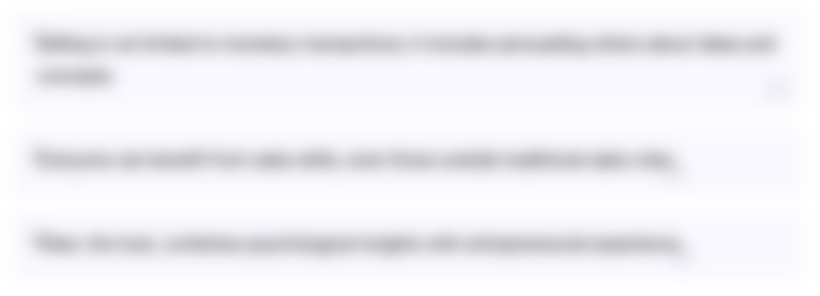
此内容仅限付费用户访问。 请升级后访问。
立即升级Transcripts
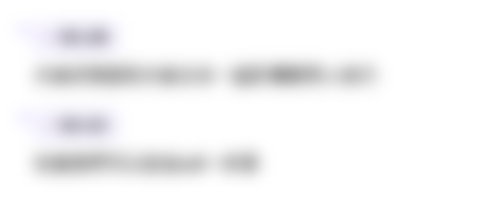
此内容仅限付费用户访问。 请升级后访问。
立即升级浏览更多相关视频

Four Principles – Lean Manufacturing & TPM

What is TPM -Total Productive Maintenance ? | 8 TPM pillars Total Productive Maintenance
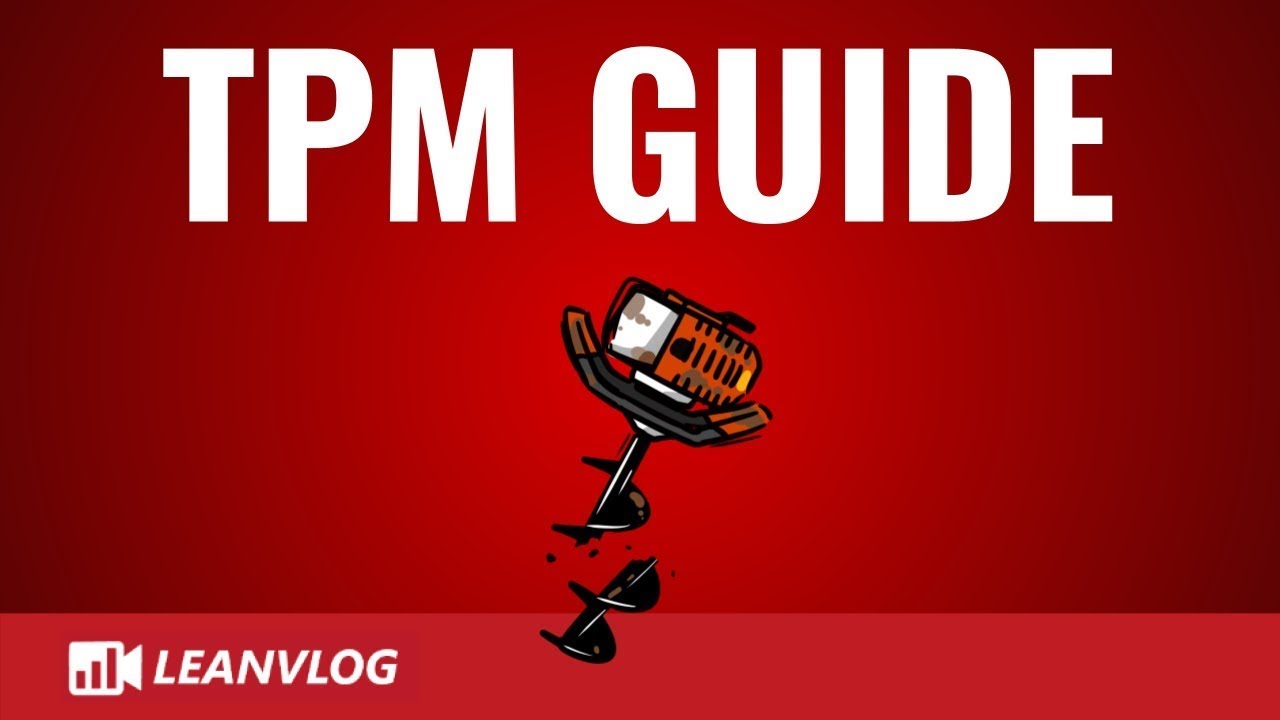
What is Total Productive Maintenance | 8 Pillars of TPM | 6 Big Losses | Type of Maintenance
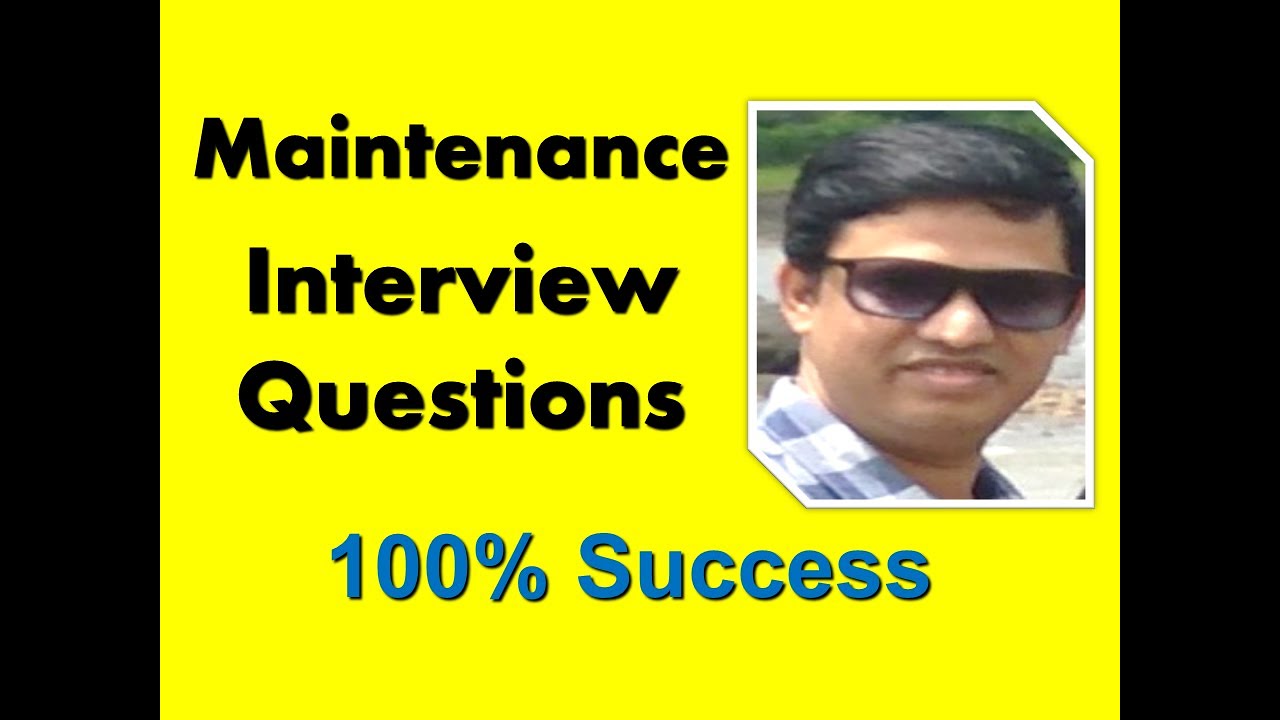
Interview Questions for Maintenance Engineers

How 7 Companies Mastered TPM (Total Productive Maintenance)
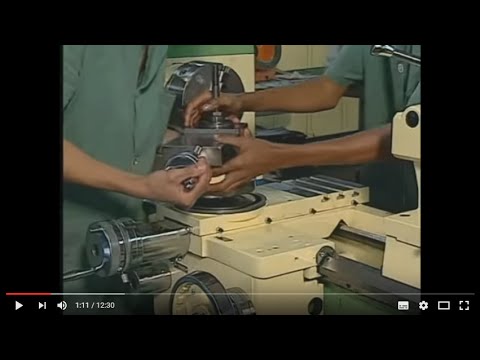
Telecurso 2000 Manutenção 01 Introdução a manutenção
5.0 / 5 (0 votes)