Grounding Video – Chance® (Temporary Protective Grounding)
Summary
TLDRThis script emphasizes the critical importance of safety and proper temporary grounding practices for line maintenance workers, whether on live or de-energized lines. It discusses the risks of fault currents due to various causes, the role of temporary grounding in protecting workers, and the significance of creating an equipotential zone to minimize voltage drop across the worker's body. It also highlights the need for adequate grounding equipment, its correct installation, and the potential hazards faced by both overhead and ground-based line workers, advocating for adherence to industry standards and individual responsibility in ensuring safety.
Takeaways
- 🔐 Safety is paramount in line maintenance, whether on live or de-energized lines, with the goal being the safe return of all workers at the end of the day.
- ⚠️ De-energized lines are not inherently safer; accidents can still occur due to inadequate temporary grounding practices.
- 👷♂️ The responsibility for safety lies with the individual lineman, who must choose to follow rules and take personal responsibility for their safety.
- 🌩️ Fault currents can occur for various reasons, including human error, lightning, backfeed, accidental contact with energized circuits, and induced voltage.
- 🛡️ Temporary grounding is essential for protecting the lives of linemen, providing an equipotential zone and a low impedance path to ground to clear faults quickly.
- 🔧 Hubbell Power Systems tests temporary grounding equipment to industry standards to ensure it can handle specified fault current levels and prevent failures in the field.
- ⚡ The amount of current that can harm a lineman is minimal compared to the total fault current, emphasizing the importance of minimizing current flow through the body.
- 🔄 Current flow through a lineman's body is reduced by minimizing potential differences across the body, achieved by reducing resistance in the grounding equipment.
- 🛠️ Proper maintenance and installation of temporary grounding equipment are crucial to prevent accidents and ensure the equipment functions correctly during a fault.
- ⚙️ Selecting adequate ground sets involves understanding the maximum available fault current, its duration, and the asymmetrical factor (x over r ratio).
- 📏 The length and size of the grounding cable are important; shorter and larger cables reduce resistance and the potential current passing through the lineman.
Q & A
Why is safety emphasized for both live and de-energized line maintenance?
-Safety is emphasized for both live and de-energized line maintenance because accidents can happen in both scenarios, and lives have been lost due to inadequate safety practices, such as improper temporary grounding.
What is the primary goal regarding safety for line workers?
-The primary goal is for all line workers to return home alive and well at the end of their workday, which underscores the importance of following industry standards, company policies, and work rules.
What is the purpose of temporary grounding during de-energized maintenance?
-The purpose of temporary grounding during de-energized maintenance is to protect the lives of line workers by providing protection against fault currents that can occur unexpectedly.
What are some reasons why fault currents can occur?
-Fault currents can occur due to human error, lightning, backfeed from sources like solar panels or generators, accidental contact between de-energized and energized circuits, and induced voltage from nearby energized lines.
Why is it important to create an equipotential zone with temporary grounding?
-Creating an equipotential zone with temporary grounding is important to minimize the voltage drop across the worker, reducing the current that could flow through them in the event of a fault.
What are the two essential components of proper temporary grounding?
-The two essential components are creating an equipotential zone to minimize voltage drop across the worker and providing a low impedance path to ground to engage system protection devices quickly and clear the fault.
What role does Hubbell Power Systems play in ensuring temporary grounding equipment safety?
-Hubbell Power Systems is a manufacturer of temporary grounding equipment that performs tests against industry standards to ensure their grounding equipment complies with specified ratings and can handle the forces associated with fault currents.
Why is it crucial to select the appropriate type of clamp for temporary grounding?
-Selecting the appropriate type of clamp is crucial because different clamps are designed for specific applications and surfaces. Using the wrong clamp type can result in a poor connection, increasing the risk of equipment failure and worker injury during a fault current.
How can the current flowing through a lineman be minimized during a fault?
-The current flowing through a lineman can be minimized by reducing the resistance of the temporary grounding equipment in parallel with the lineman, which in turn minimizes the potential difference across the lineman's body.
What are some key considerations for proper temporary grounding to minimize the current passing through the lineman?
-Key considerations include using adequately rated grounding equipment, maintaining and taking care of the equipment, installing it properly in an equipotential configuration, and ensuring the equipment is clean and tightened to the manufacturer's recommended torque value.
What is the significance of maintaining a safe distance or using protective equipment for line workers on the ground?
-Maintaining a safe distance or using protective equipment is significant for ground workers to avoid step potential and touch potential hazards, which can result in serious injury or death due to the flow of fault current through their bodies.
What is the role of an Equi-Mat in protecting ground workers during line maintenance?
-An Equi-Mat helps protect ground workers by creating an equipotential surface that eliminates potential differences between the worker's feet, thus preventing current flow through their body in the event of a fault.
Outlines
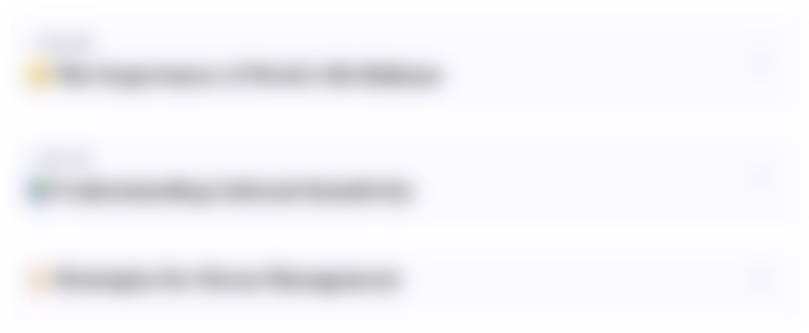
This section is available to paid users only. Please upgrade to access this part.
Upgrade NowMindmap
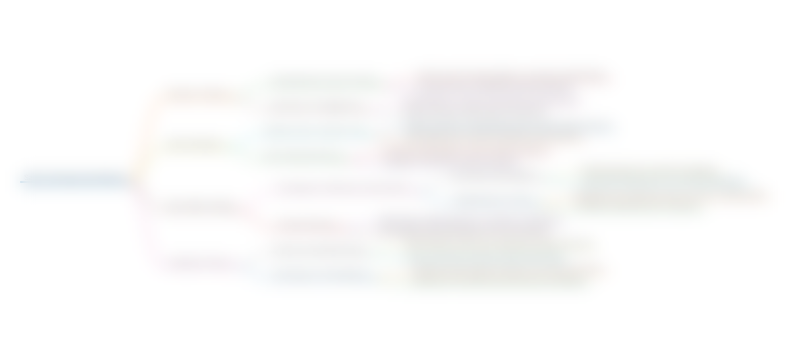
This section is available to paid users only. Please upgrade to access this part.
Upgrade NowKeywords
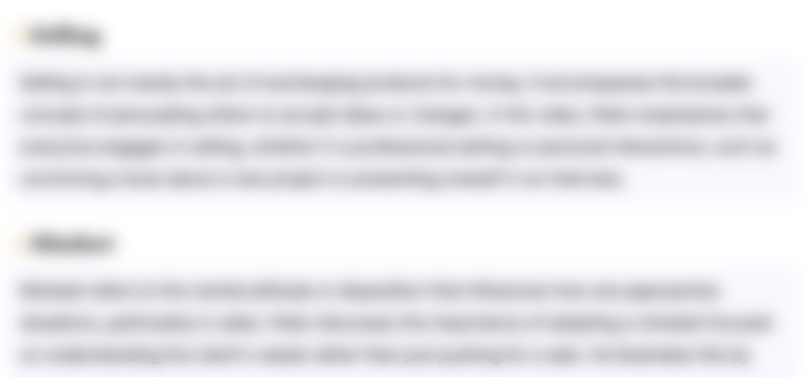
This section is available to paid users only. Please upgrade to access this part.
Upgrade NowHighlights
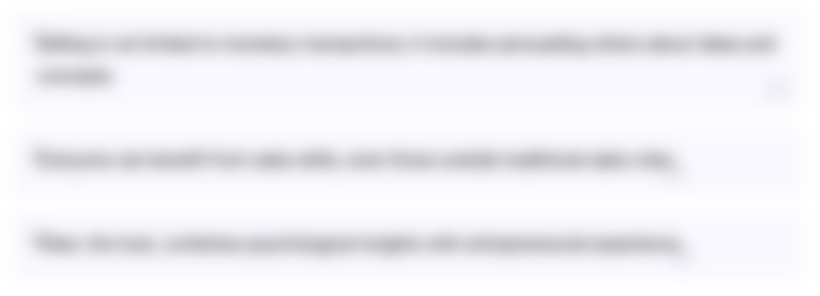
This section is available to paid users only. Please upgrade to access this part.
Upgrade NowTranscripts
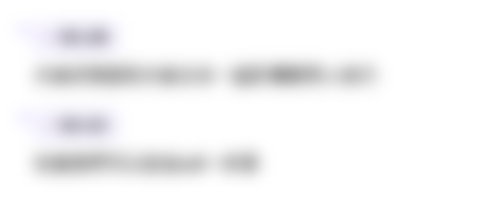
This section is available to paid users only. Please upgrade to access this part.
Upgrade NowBrowse More Related Video

Construction Safety: Electrical Safety

Electrical Safety (2018)

2 Minute Toolbox Talk: Electrical Safety - Electrical Isolation: LOTO Policy
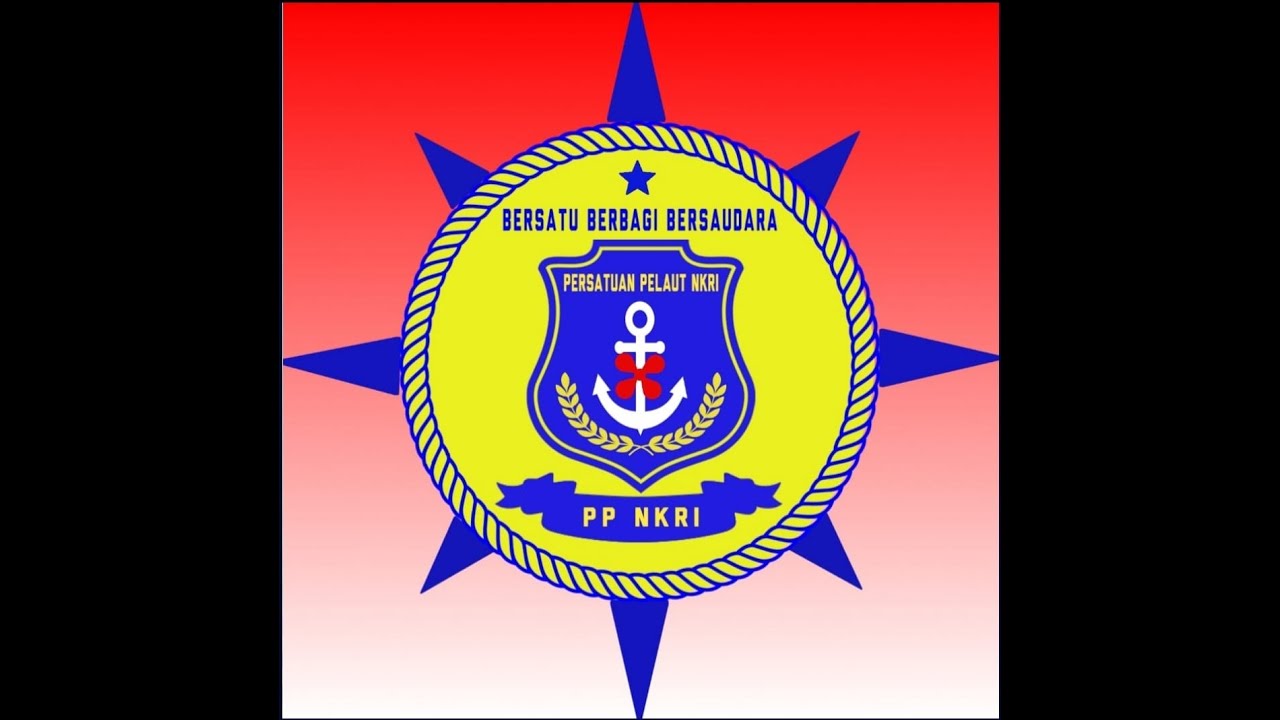
tindakan pencegahan terjadinya kecelakaan kerja di saat menangani tali di atas kapal

Safety Training Video : Why Lock-Out, Tag-Out Is Vitally Important By Panduit
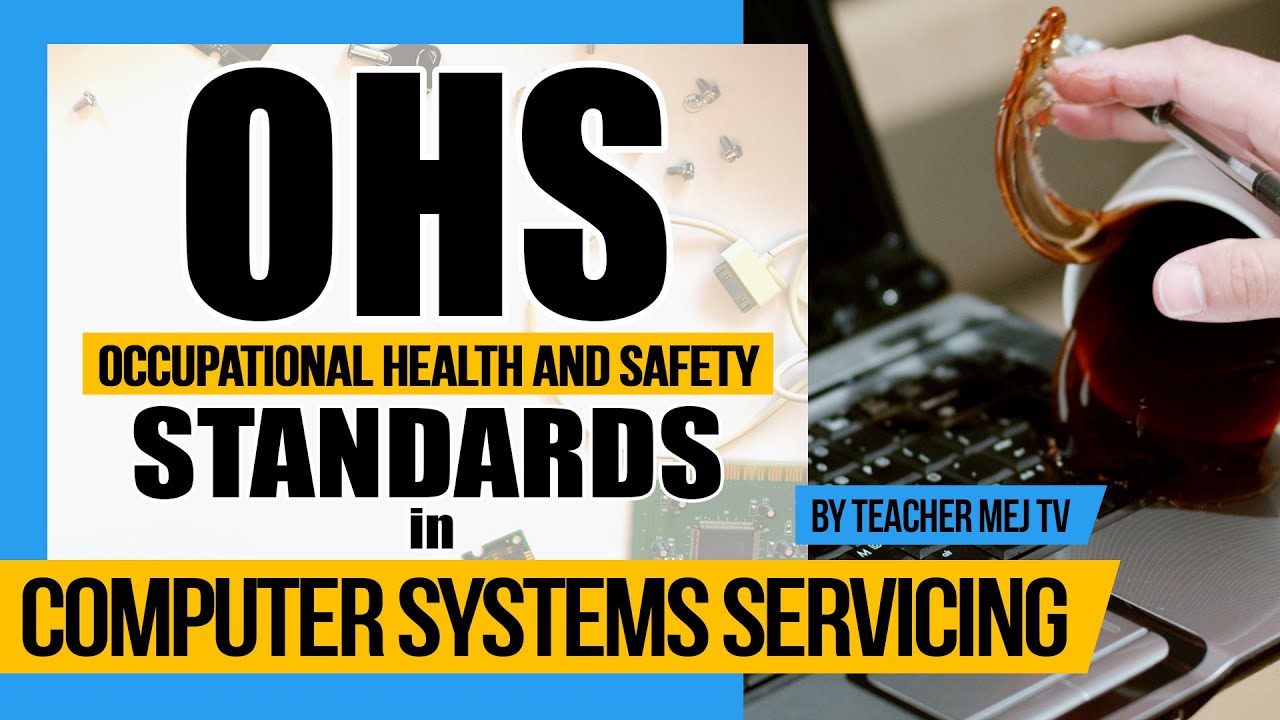
Occupational Health and Safety (OHS) Standards in CSS | Computer Systems Servicing Guide
5.0 / 5 (0 votes)