How 1.5 Million Plastic Bottles Are Turned Into Clothing Every Day | World Wide Waste
Summary
TLDRThe video script narrates the transformation of plastic bottles into polyester fibers by Shree Renga, an Indian company, which recycles 1.5 million bottles daily. It explores the environmental benefits and challenges of using recycled polyester in fashion, highlighting the efforts of brands like Adidas and Nike to increase its use. The script delves into the recycling process, the history of synthetic fibers, and innovative technologies aiming to revolutionize textile recycling, emphasizing the growing importance of sustainable fashion.
Takeaways
- 🌿 Shree Renga, an Indian company, recycles 1.5 million plastic bottles into polyester daily, a process expected to triple in the next few years.
- 👕 Fashion brands like Adidas, Nike, and Shein are increasing their use of recycled polyester to market their products as more sustainable.
- 🔁 The global production of plastic bottles is enormous, with 600 million produced yearly, but most are not recycled, highlighting the importance of companies like Shree Renga.
- 👔 The recycling process at Shree Renga is meticulous, separating PET from other materials and ensuring no waste, including using water from washing for other purposes.
- 🧬 PET, or polyethylene terephthalate, is a common plastic used in bottles and is chemically the same as polyester, making it ideal for fiber production.
- 🎨 Shree Renga uses dope-dyeing to color their polyester fibers, a process that doesn't require water or additional energy for coloring.
- ♻️ Recycling polyester is complex due to the need to separate it from other materials like cotton, spandex, chemicals, and dyes.
- 👚 Shree Renga launched its own clothing brand, Ecoline, in 2021, focusing on 100% recycled polyester garments.
- 🌐 The fashion industry's reliance on synthetic fibers like polyester is growing, with projections for it to make up nearly three-fourths of all textile production by 2030.
- 🔍 The environmental impact of synthetic fibers includes microplastics from washing, which contribute significantly to ocean pollution.
- 🔄 Innovative recycling technologies, such as the Looop by H&M and Ambercycle's chemical process, are being developed to recycle clothes back into clothes, though scaling up remains a challenge.
Q & A
What is the primary material used by Shree Renga to produce polyester?
-Shree Renga primarily uses PET, which stands for polyethylene terephthalate, a common type of plastic derived from plastic bottles, to produce polyester.
How much polyester does Shree Renga produce daily?
-Shree Renga spins about 25 metric tons of polyester on a daily basis.
What is the significance of Senthil quitting his IT job to join his father's business?
-Senthil's decision to quit his IT job and join his father's business signifies his desire to be an entrepreneur in India and contribute to the recycling and sustainability efforts of Shree Renga.
What is the global production of plastic bottles annually, and how does Shree Renga contribute to recycling efforts?
-Globally, about 600 million plastic bottles are produced every year, with most not being recycled. Shree Renga contributes by buying approximately 900 metric tons of trash each month, focusing on PET for their production.
How does Shree Renga ensure the purity of PET during the recycling process?
-Shree Renga uses advanced sensing technologies to separate PET from other plastics like PVC. They also go through a meticulous process of washing, rinsing, and sorting the flakes to ensure purity.
What is the environmental advantage of Shree Renga's dyeing technique?
-Shree Renga's dyeing technique, known as dope-dyeing, involves melting the plastic flakes with colored pigments, which allows them to produce colored fibers without using a single drop of water or additional energy for the coloring process.
How does the recycling process at Shree Renga's factory contribute to a circular economy?
-The recycling process at Shree Renga's factory exemplifies a circular economy by ensuring that nothing is wasted. For instance, water used in the process is recycled, and even the dirt and sand collected from washing bottles are used to make bricks for the factory floor.
What is the role of the simplex machine in the production process at Shree Renga?
-The simplex machine is used to stretch the fibers and make them more parallel, resulting in a more compact and uniform rope known as roving, which is ideal for spinning into yarn.
How does the recycling of polyester compare to the recycling of plastic bottles in terms of environmental impact?
-Recycling polyester generates about 70% less emissions than producing virgin polyester. However, washing synthetic fibers can introduce microplastics into waterways, and if discarded improperly, they do not break down easily in the environment.
What is the current state of polyester recycling technology, and what are the challenges faced by the industry?
-The current state of polyester recycling technology faces challenges such as the difficulty of separating polyester from dyes and other fabrics, the need for blending with virgin materials, and the high costs and energy use associated with restarting production machines. Moreover, scaling up the process for commercial use is a significant hurdle.
What is the significance of the Looop machine developed by H&M and the Hong Kong Research Institute?
-The Looop machine is significant as it represents an innovative approach to garment-to-garment recycling, turning used clothes into new ones in about three days. It offers a potential solution for textile waste, although the current process is time-consuming and not yet scalable for mass production.
Outlines
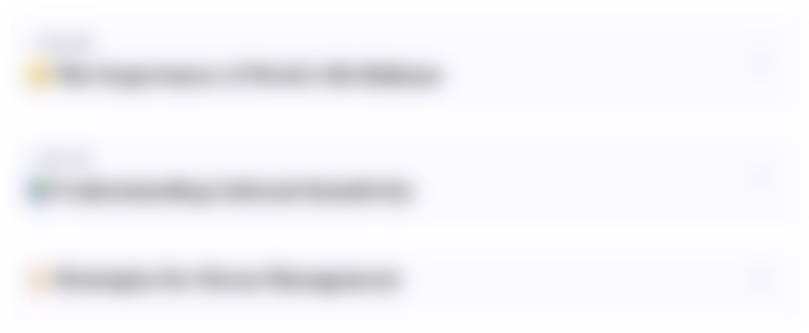
This section is available to paid users only. Please upgrade to access this part.
Upgrade NowMindmap
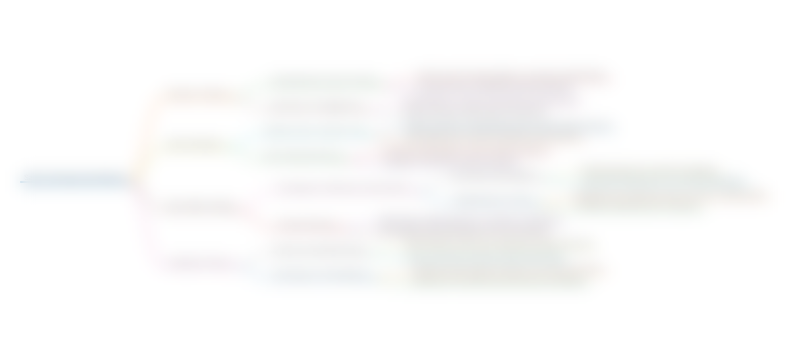
This section is available to paid users only. Please upgrade to access this part.
Upgrade NowKeywords
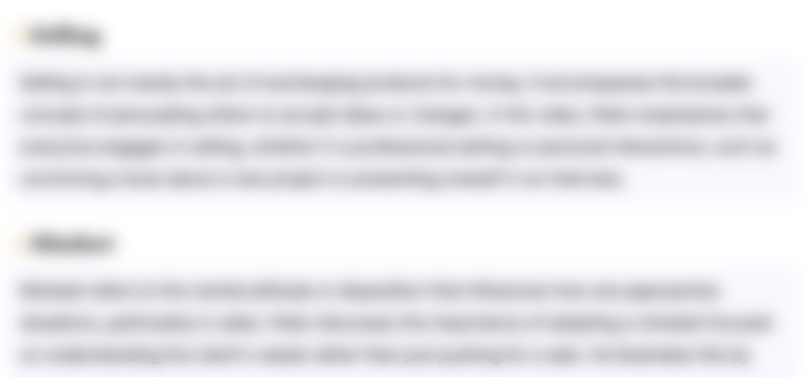
This section is available to paid users only. Please upgrade to access this part.
Upgrade NowHighlights
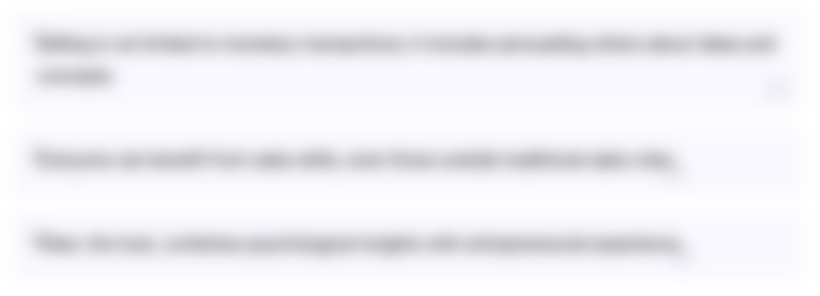
This section is available to paid users only. Please upgrade to access this part.
Upgrade NowTranscripts
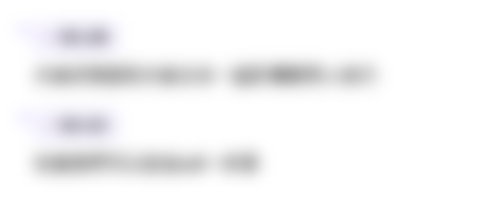
This section is available to paid users only. Please upgrade to access this part.
Upgrade NowBrowse More Related Video

How Plastic Bottles Are Recycled Into Polyester
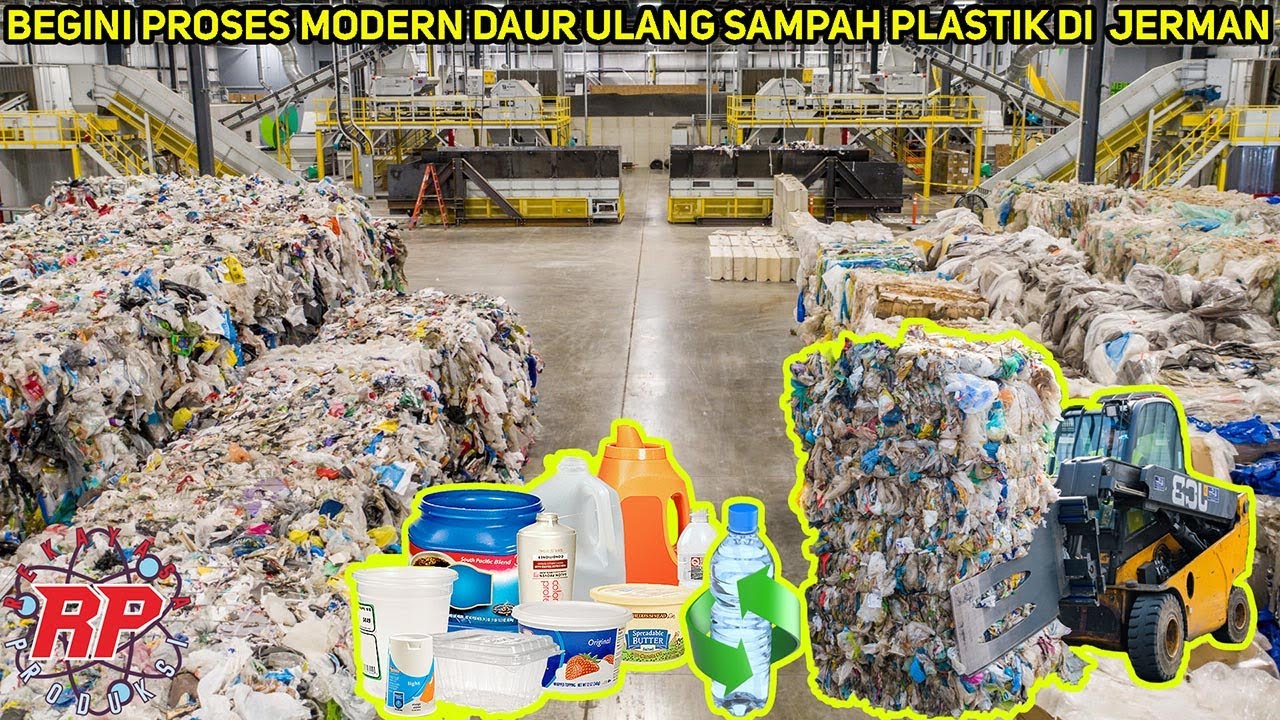
KEREN! BEGINI PROSES MODERN DAUR ULANG SAMPAH PLASTIK MENJADI PRODUK JADI DI NEGARA MAJU
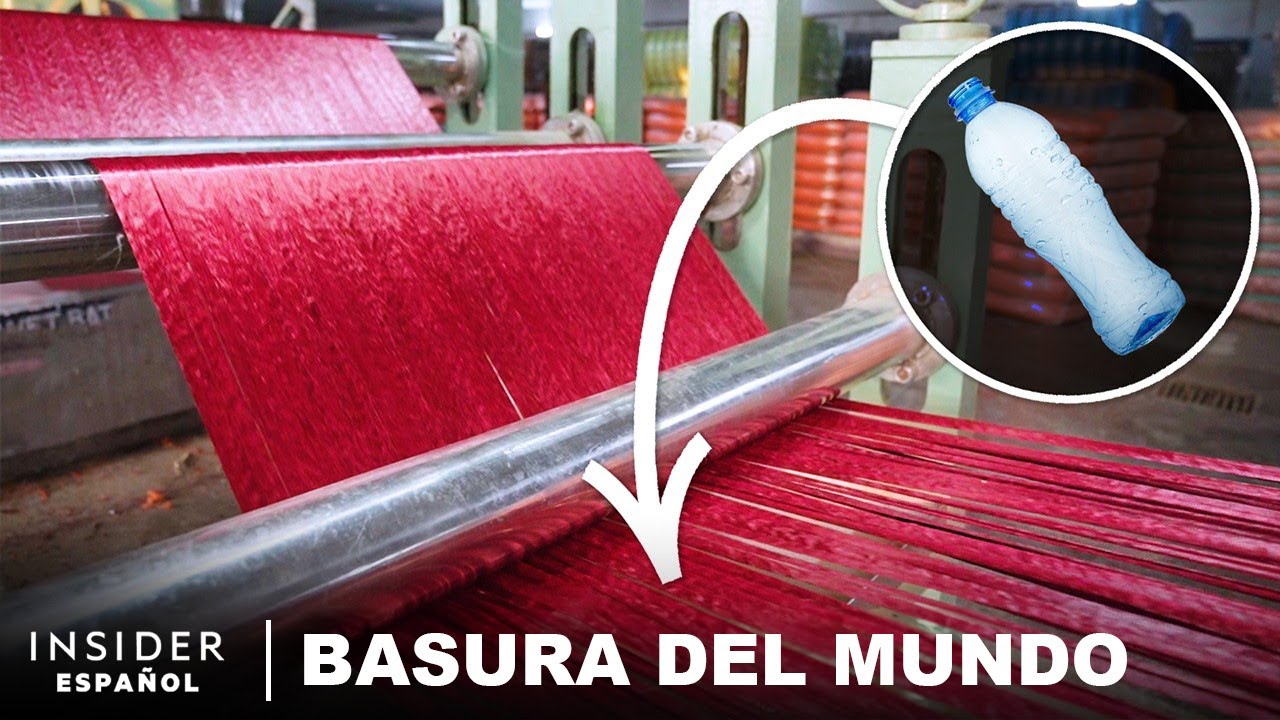
Un Millón y Medio de Botellas de Plástico se Transforman en Ropa Todos los Días | Basura del Mundo
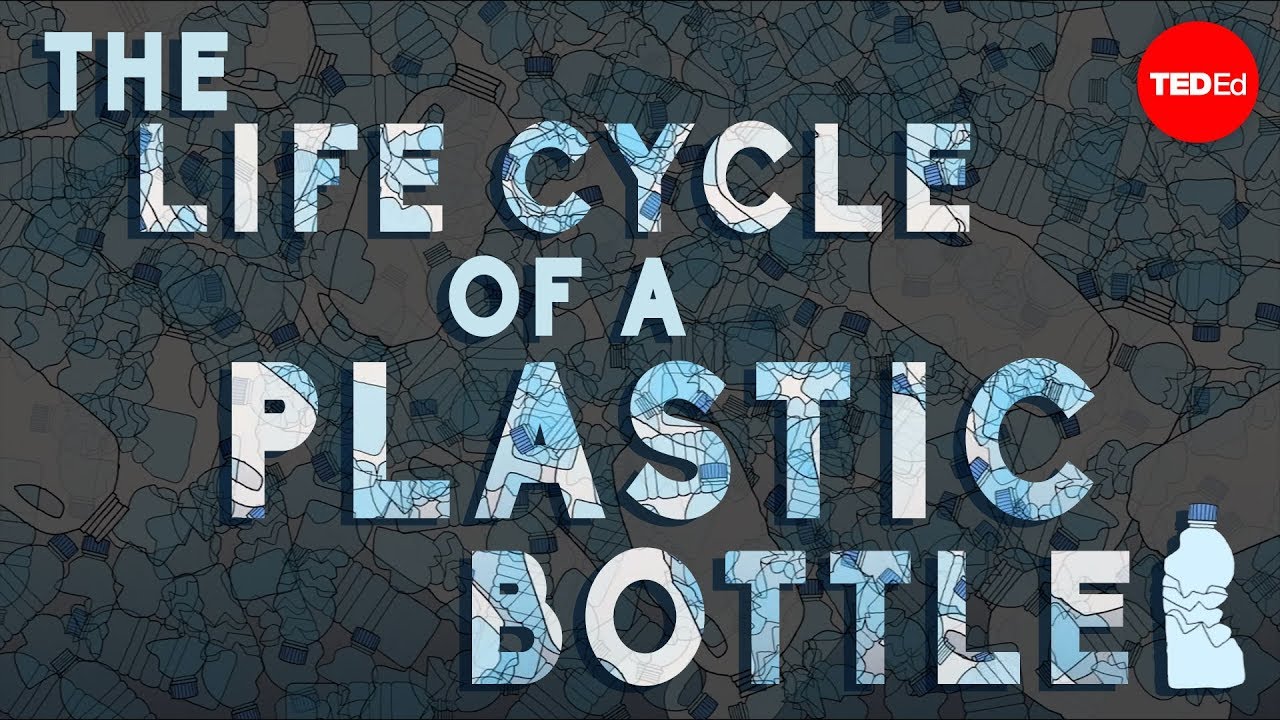
What really happens to the plastic you throw away - Emma Bryce
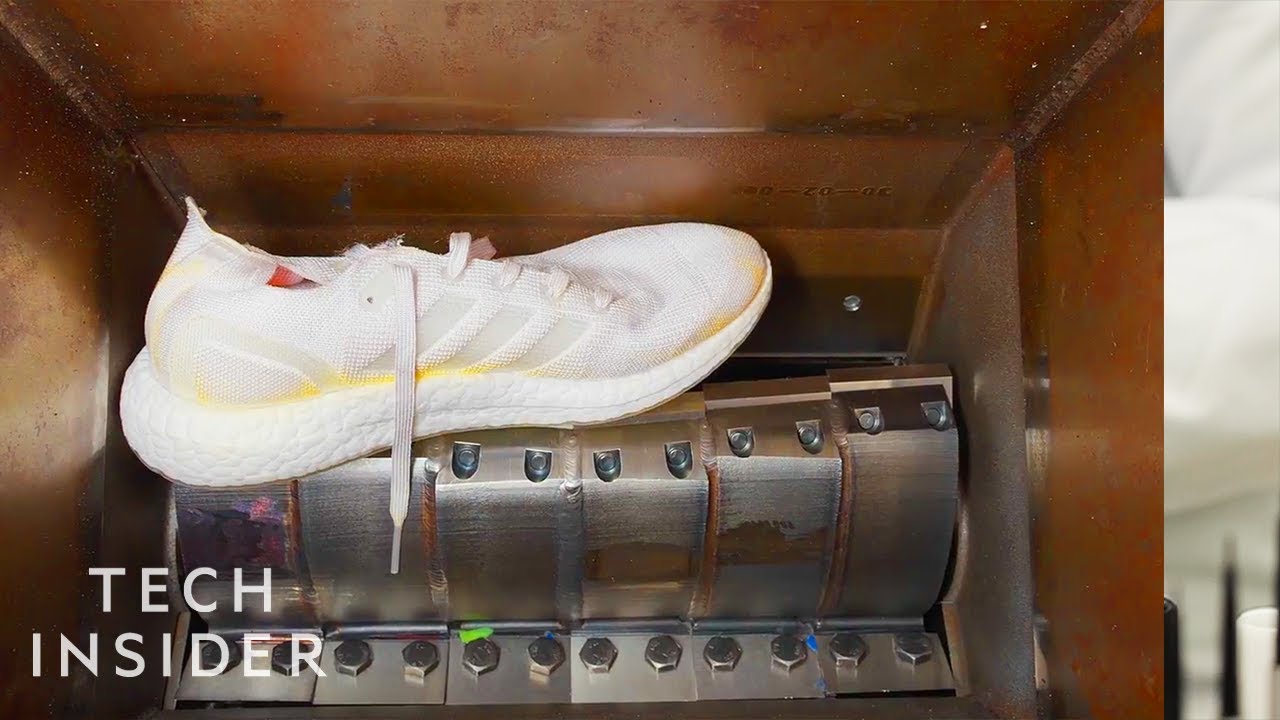
How Adidas Turns Plastic Bottles Into Shoes
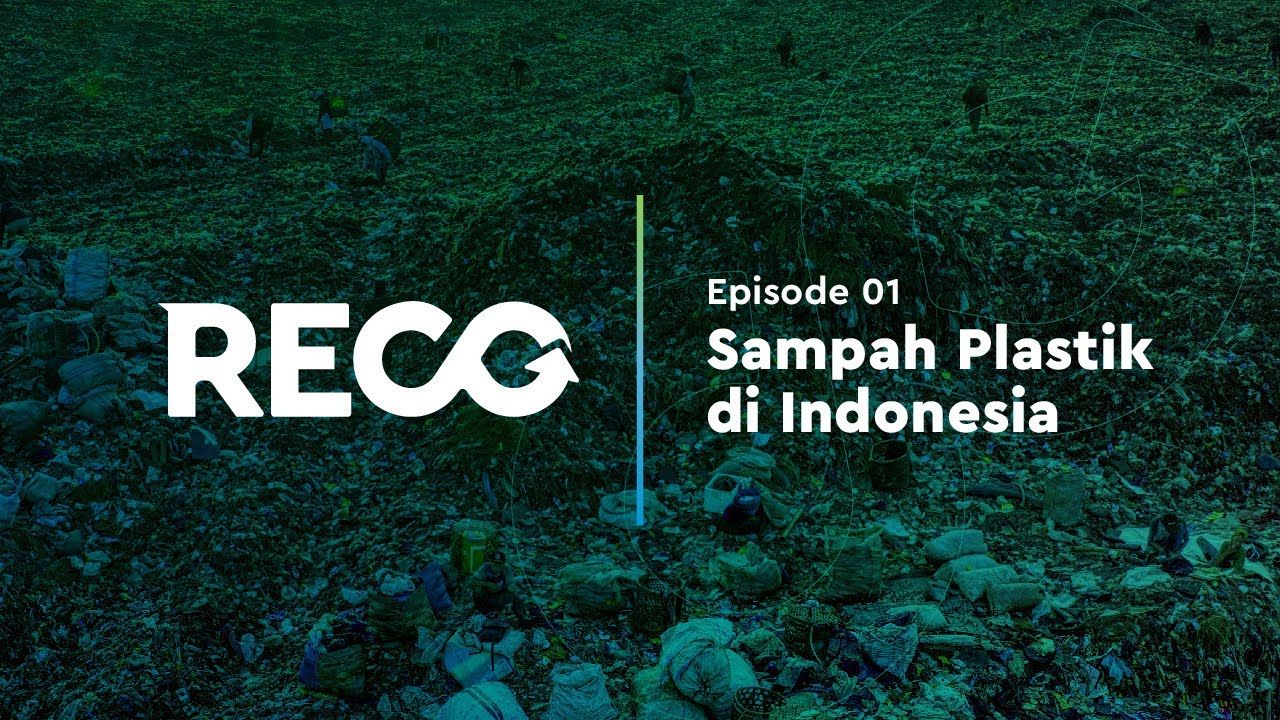
RECO EP. 1 - SAMPAH PLASTIK DI INDONESIA
5.0 / 5 (0 votes)