Manutenção no Setor Alimentício
Summary
TLDRThis video discusses the critical importance of machine maintenance in the food industry, focusing on how timely and effective maintenance prevents production shutdowns and ensures food safety. It emphasizes the role of monitoring systems, like online sensors, in detecting issues early—such as a malfunction in an ammonia compressor. By aligning maintenance strategies and using real-time monitoring, industries can avoid costly disruptions, extend the lifespan of equipment, and guarantee product quality. The video also highlights the significance of a proactive maintenance management system (MMS) for ensuring continuous production and safety in the food sector.
Takeaways
- 😀 Machine maintenance is critical in the food industry to ensure smooth food production and prevent unexpected shutdowns.
- 😀 Proper maintenance is essential for maintaining food quality and consumer safety, especially in industries dealing with perishable goods.
- 😀 Failure to maintain machines properly can lead to significant losses, such as food spoilage, production downtime, and quality degradation.
- 😀 Maintenance management should be planned and executed carefully to ensure high reliability and availability of production lines.
- 😀 Interventions and repairs should be well-timed and executed with minimal impact on production, extending the useful life of equipment.
- 😀 Real-time online monitoring and sensor systems, like the Tim system, play a vital role in identifying issues before they escalate.
- 😀 Automating maintenance management systems helps track and monitor machine performance, ensuring proactive measures can be taken to avoid failures.
- 😀 A failure in critical equipment, like an ammonia compressor, can have catastrophic effects, making early detection vital to prevent major losses.
- 😀 Using mathematical models and AI-based systems, maintenance issues like misalignment in compressors can be detected through vibration changes.
- 😀 Proactive maintenance allows issues to be resolved during scheduled downtime, ensuring production continues smoothly and safely.
- 😀 Online monitoring and maintenance management systems help companies in the food industry avoid unexpected stops and maintain food safety through constant oversight.
Q & A
Why is machine maintenance critical in the food industry?
-Machine maintenance is crucial in the food industry to ensure the constant flow of production and prevent unexpected shutdowns, which can affect product quality, food safety, and lead to financial losses.
How does poor maintenance affect food safety and product quality?
-Poor maintenance can lead to equipment breakdowns that disrupt the production process, causing product spoilage, contamination risks, and potential failures in refrigeration, all of which compromise food safety and quality.
What specific role does refrigeration play in food production?
-Refrigeration is essential in food production, especially for perishable items. A failure in refrigeration, such as an ammonia compressor breakdown, can result in significant losses, including discarded products and raw materials.
What kind of impact does a machine failure have on the production line?
-A machine failure can lead to an entire production line stopping, resulting in lost production hours, damaged products, and significant downtime, all of which can severely impact profitability and production continuity.
What is the importance of predictive maintenance in food production?
-Predictive maintenance helps detect potential failures before they occur, allowing manufacturers to address issues in advance. This approach prevents costly shutdowns, extends equipment lifespan, and maintains product quality and safety.
How does online monitoring improve maintenance management?
-Online monitoring provides real-time tracking of machines, allowing maintenance teams to identify problems early and schedule repairs before failures occur. This minimizes unexpected stops and ensures the smooth functioning of the production line.
Can you explain the role of AI in detecting machine failures?
-AI helps detect machine failures by analyzing vibration frequencies and other operational data. For example, it can identify misalignments in critical equipment, such as ammonia compressors, by recognizing unusual patterns that indicate potential issues.
What happened when the ammonia compressor failed, and how was it detected?
-When the ammonia compressor experienced a failure, it was detected by an online monitoring system that identified a misalignment in the coupling. The system’s AI detected an increase in vibration intensity, triggering an alert and allowing the maintenance team to resolve the issue promptly.
Why is the alignment of maintenance strategies so important in the food industry?
-Aligning maintenance strategies in the food industry is crucial because it ensures the uninterrupted operation of the production line. Properly planned and executed maintenance minimizes the risk of unexpected downtime, which directly affects food safety and product quality.
How does the maintenance system contribute to reducing risks in food production?
-The maintenance system reduces risks in food production by continuously monitoring machines, identifying early signs of failure, and allowing for proactive interventions. This helps avoid unexpected shutdowns and ensures safe, high-quality products for consumers.
Outlines
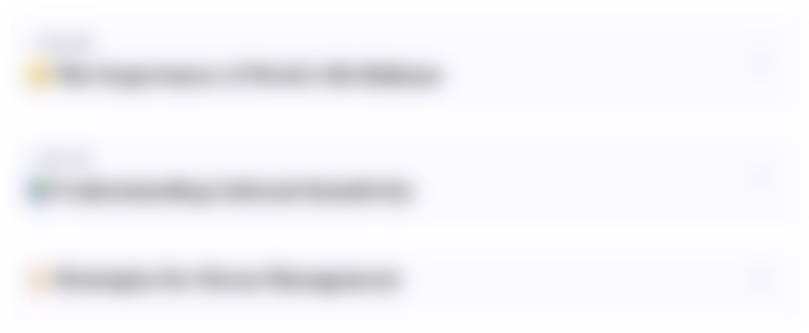
This section is available to paid users only. Please upgrade to access this part.
Upgrade NowMindmap
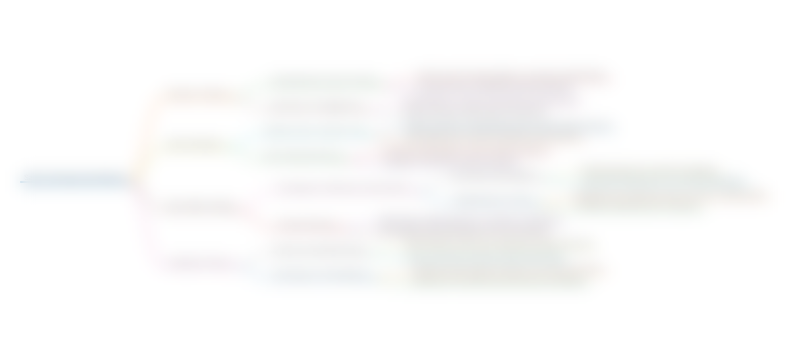
This section is available to paid users only. Please upgrade to access this part.
Upgrade NowKeywords
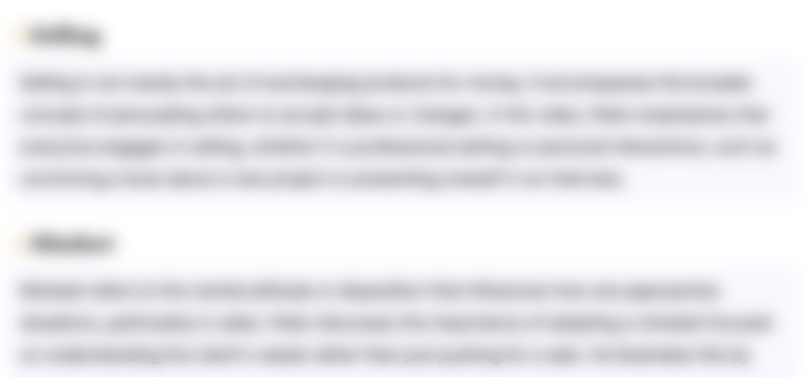
This section is available to paid users only. Please upgrade to access this part.
Upgrade NowHighlights
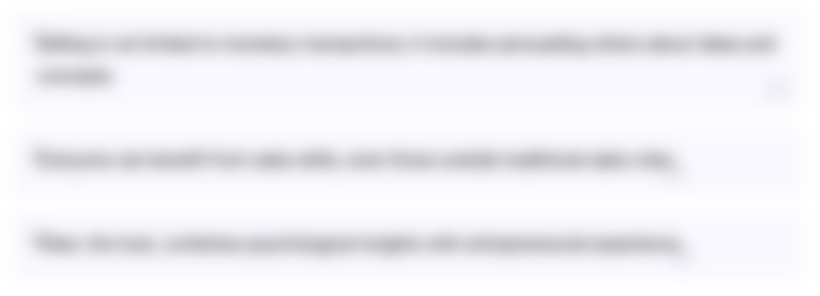
This section is available to paid users only. Please upgrade to access this part.
Upgrade NowTranscripts
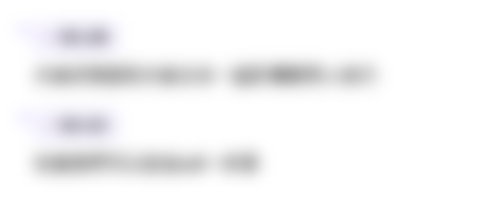
This section is available to paid users only. Please upgrade to access this part.
Upgrade NowBrowse More Related Video
5.0 / 5 (0 votes)