Pembuatan tungku pembakaran sampah tanpa asap
Summary
TLDRIn this video, the creator demonstrates how to construct a smoke-free waste incineration furnace using secondhand Pertamina barrels. The process includes cutting the barrels, adding ventilation for oxygen flow, and ensuring proper heat circulation to reduce smoke. The furnace design aims to burn waste efficiently, creating minimal smoke and reducing pollution. Despite some initial challenges, such as imperfect ventilation holes, the test fire reaches temperatures above 460 degrees. The creator plans to continue refining the furnace to achieve optimal temperatures and a completely smoke-free design in the next phase.
Takeaways
- 😀 The project involves creating a smoke-free waste incineration furnace using a secondhand Pertamina barrel.
- 😀 Water should be added to the barrel before cutting to prevent explosions due to oil residue.
- 😀 The furnace is designed to be efficient with minimal smoke by ensuring proper oxygen flow and ventilation.
- 😀 The small barrel is inserted into the larger one, and a conical shape is created at the top to prevent excessive wind entry.
- 😀 Holes are drilled in the furnace for ventilation, creating air circulation for better combustion.
- 😀 The furnace base is created from the original barrel lid, shaped into a windmill structure to improve airflow.
- 😀 The furnace is tested using plywood, cardboard, and flammable paper, with the initial smoke coming from the paint on the barrel.
- 😀 The furnace temperature reaches 460-500°C during the test, but the goal is to achieve 800°C for optimal performance.
- 😀 The smoke reduction was significant, but more improvements are needed, including adding heat-resistant cement to maintain higher temperatures.
- 😀 The furnace construction is a work in progress, and future upgrades will focus on making it entirely smoke-free and pollution-free.
- 😀 The video encourages viewers to subscribe for future updates on the furnace’s development and improvements.
Q & A
Why is it necessary to fill the barrel with water before cutting it?
-Filling the barrel with water prevents it from exploding due to residual oil traces inside the barrel, ensuring safety during the cutting process.
What is the purpose of cutting one barrel smaller than the other?
-The smaller barrel is inserted into the larger barrel, and its reduced diameter is meant to create a controlled flow of oxygen into the combustion furnace, aiding in better combustion.
Why is the rope used when cutting the barrel?
-The rope is used to keep the barrel from bursting open when cutting, ensuring the structural integrity of the barrel while the bottom part is removed.
How does the design of the bottom ventilation contribute to the furnace’s efficiency?
-The bottom ventilation holes are designed to induce wind rotation or turbulence, enhancing airflow and promoting better combustion within the furnace.
What role does the cone-shaped curve at the top of the furnace play?
-The cone-shaped curve is designed to reduce the amount of wind entering from above, ensuring more controlled airflow and improving combustion efficiency.
Why were multiple ventilation holes drilled into the furnace?
-The ventilation holes allow for stable airflow, which is essential for optimal combustion. The precise arrangement helps regulate the furnace's internal temperature and combustion process.
What is the purpose of the circular windmill-like base at the bottom?
-The base is designed to facilitate wind circulation and create turbulence, which strengthens the airflow entering the furnace and aids in more efficient burning.
Why does the furnace produce smoke, and how is it reduced?
-Initially, the furnace produces smoke due to residual paint on the barrel and incomplete combustion of wood. However, the design and ventilation holes help burn the smoke, significantly reducing its visibility.
What was the maximum temperature reached during the first burn test?
-During the first burn test, the temperature reached up to 500 degrees Celsius, which was lower than the target temperature of 800 degrees Celsius.
What improvements are planned for the furnace to make it more smoke-free?
-The next step involves upgrading the furnace by adding a heat-resistant cement layer to improve heat retention, which should help achieve higher temperatures and further reduce smoke production.
Outlines
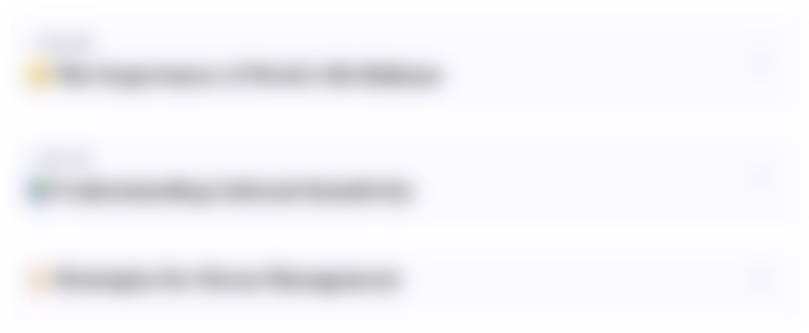
This section is available to paid users only. Please upgrade to access this part.
Upgrade NowMindmap
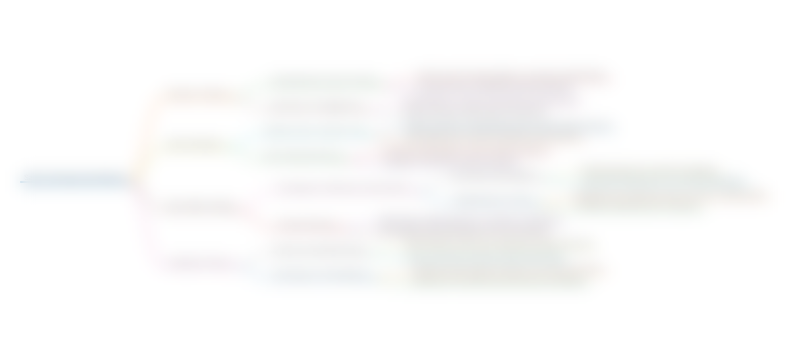
This section is available to paid users only. Please upgrade to access this part.
Upgrade NowKeywords
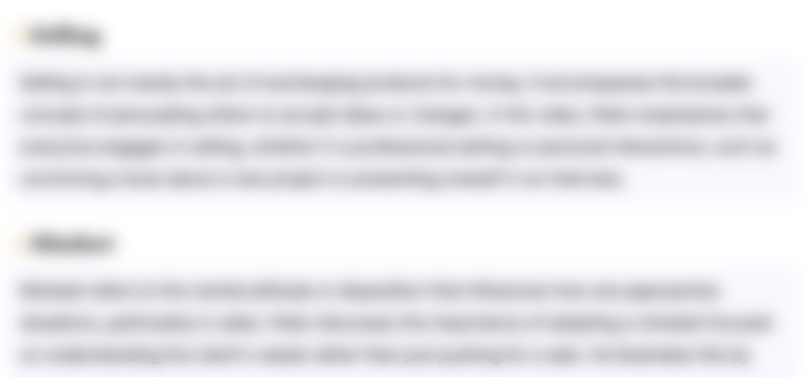
This section is available to paid users only. Please upgrade to access this part.
Upgrade NowHighlights
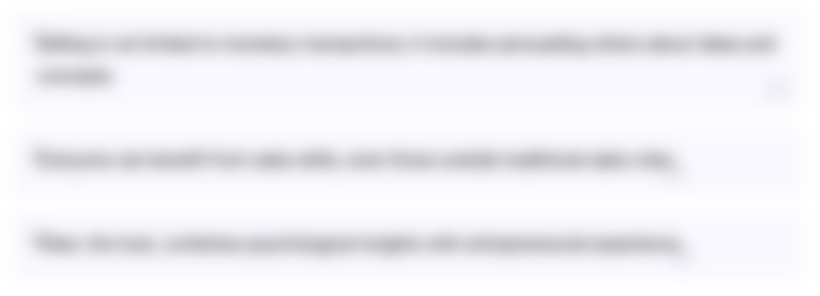
This section is available to paid users only. Please upgrade to access this part.
Upgrade NowTranscripts
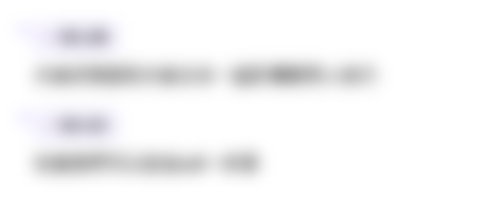
This section is available to paid users only. Please upgrade to access this part.
Upgrade NowBrowse More Related Video
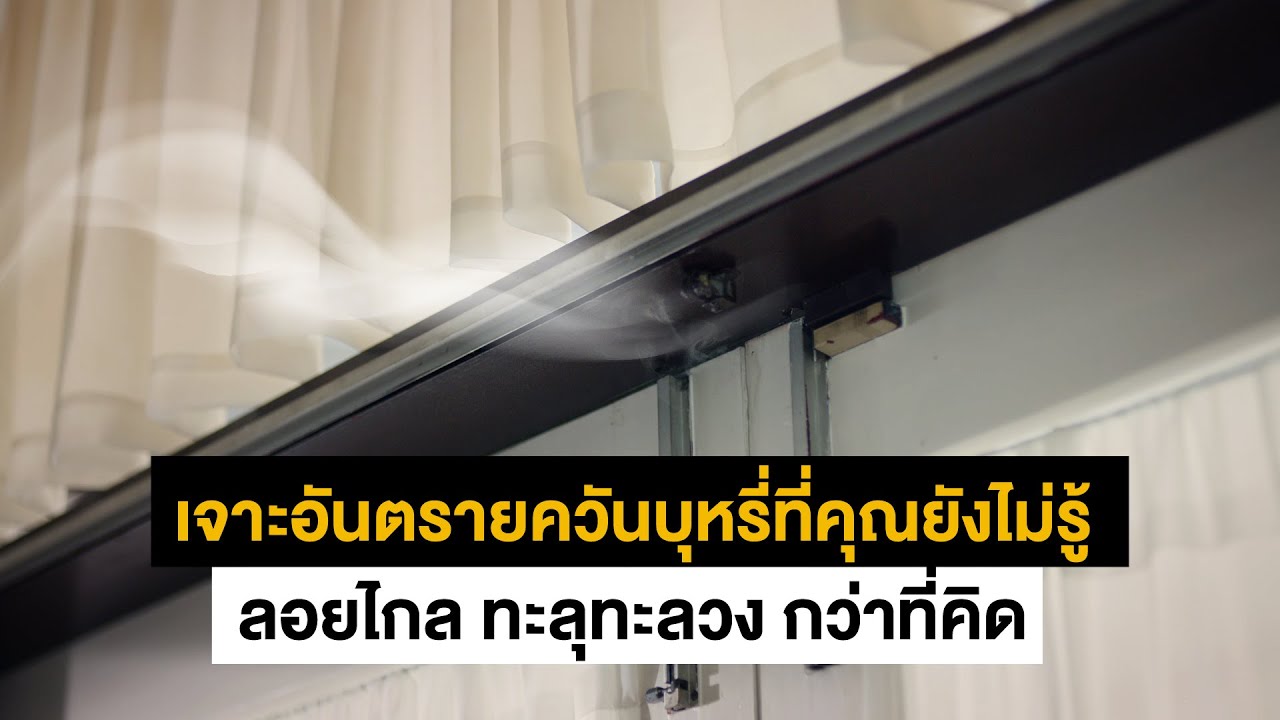
เจาะอันตรายควันบุหรี่ที่คุณยังไม่รู้

Teknologi Insenerasi - Jasman Kurnia Rahim - Konsultan Pengelolaan Sampah Perkotaan #zerowaste
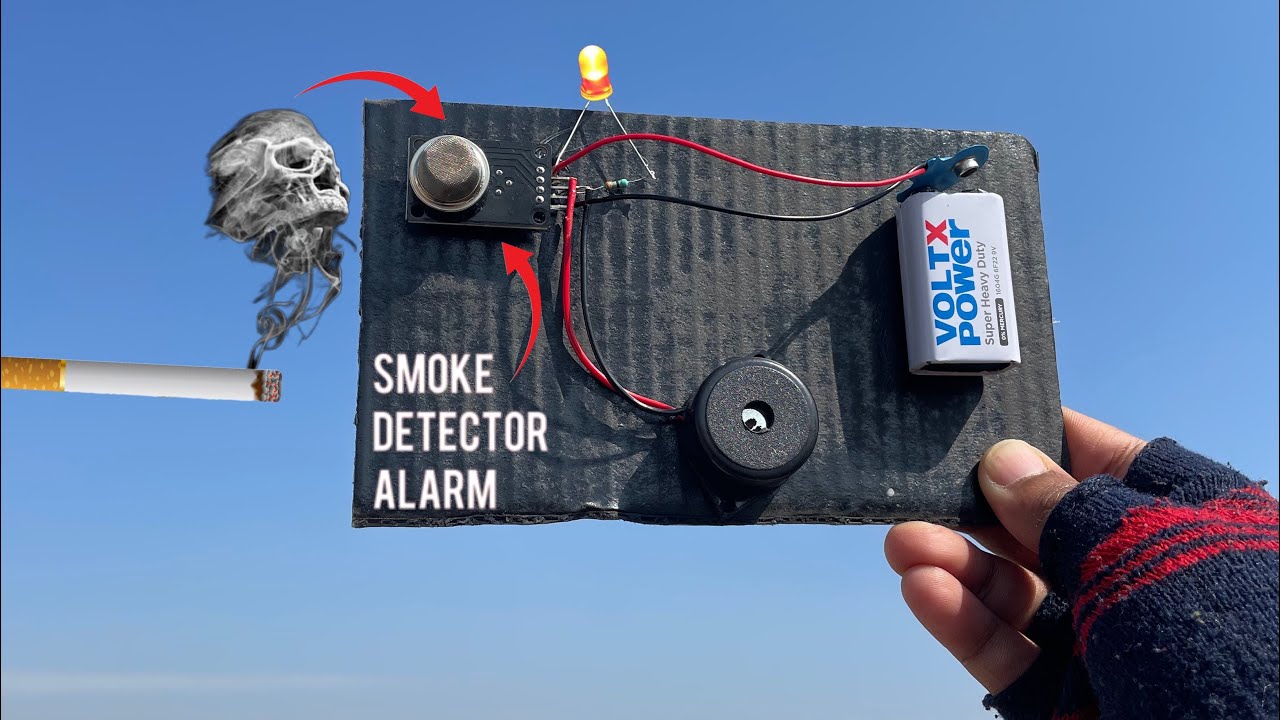
How to make a Smoke detector Alarm | school science project smoke detector Alarm

Vinted Explained + Posting Orders

Children Exposed to Secondhand Smoke - American Medical Association (AMA)

Cara Membuat Pupuk Organik Cair (POC) dari Sampah Dapur dengan EM4 || Kakpit
5.0 / 5 (0 votes)