Safety and Health Assessment System in Construction (SHASSIC) - Workplace Inspection (Part 4)
Summary
TLDRThis video provides a comprehensive guide to conducting workplace inspections as part of the Shastic assessment process. It focuses on identifying the top three high-risk activities at a construction site, using a detailed checklist to evaluate safety standards. Key aspects include assessing overall site management, safety signage, working environments, equipment compliance, and personnel training. The video also emphasizes the importance of proper documentation, including traffic plans and safety certifications, to ensure a safe working environment. The goal is to help assessors perform thorough inspections and calculate a Shastic score for effective risk management.
Takeaways
- 😀 Workplace inspections are performed to assess the implementation of Occupational Safety and Health (OSH) practices at a site.
- 😀 The top three high-risk activities for workplace inspection are working at height, mechanical lifting, and works involving temporary structures and false works.
- 😀 The Shastic assessor determines high-risk activities at a site by referring to a priority table or identifying additional risks not listed in the table.
- 😀 For a road construction project in a tunnel, an activity like blasting can be identified as an additional high-risk activity not listed in the priority table.
- 😀 If only one high-risk activity is identified from the table, other activities such as bricklaying or plastering works at height may be considered additional high-risk activities.
- 😀 High-risk activities may also include piling work, working at height on a mobile platform, or working with electrical ducting.
- 😀 The checklist for workplace inspection includes two parts: general workplace inspection and inspection of the identified high-risk activities.
- 😀 Elements A, B, and C in the general checklist focus on OSH management, traffic control, and safety signage for PPE and hazards.
- 😀 For each high-risk activity, the checklist assesses factors such as appointed personnel competency, equipment safety standards, and the handling/storage of materials.
- 😀 The total Shastic score for workplace inspection is calculated by evaluating the total number of compliant items and non-applicable items, then using a specific formula.
Q & A
What is the purpose of conducting a workplace inspection according to the script?
-The purpose of a workplace inspection is to assess the Occupational Safety and Health (OSH) implementation at a site, specifically focusing on high-risk activities to ensure safety compliance.
How are the top three high-risk activities identified at a construction site?
-The top three high-risk activities are identified by referring to a priority table, which includes activities such as working at height, mechanical lifting, works involving temporary structures, earthworks excavation exceeding 2 meters, and other identified high-risk activities.
What happens if only one or two high-risk activities are identified at a site?
-If only one or two high-risk activities are identified, the assessor should identify other relevant high-risk activities not listed in the priority table, such as blasting or other common hazards.
What are some examples of high-risk activities that might be identified during a workplace inspection?
-Examples include blasting in tunnel construction, bricklaying and plastering at height (even below 2 meters), and activities like piling work or working at height on a mobile platform.
What should be done if no high-risk activity can be identified from the table?
-If no high-risk activities are identified, the assessor should refer to common high-risk activities such as piling work or fixing electrical ducting, or mark items in the checklist as 'Not Applicable' (N/A).
What are the two main parts of the workplace inspection checklist?
-The checklist has two parts: the first part includes general workplace inspection items (9 checklist items), and the second part focuses on the three identified high-risk activities (21 checklist items).
What should be checked under Element A of the checklist for overall site wash management?
-Under Element A, the assessor must verify if the OSH policy is displayed on-site, and check that the project site's registration number and hard copies of necessary forms are available.
What does Element B of the checklist focus on?
-Element B focuses on the traffic movement plan, ensuring that road safety signage, flagmen, and route indicators are in place where necessary to manage traffic effectively.
In Element C, what are the requirements for safety signages?
-In Element C, safety signages must use international color codes. These include mandatory blue signs for PPE usage, yellow warning signs, red prohibition signs, and green safety signs, all of which must be displayed appropriately.
What steps are taken to assess equipment and machinery used in high-risk areas according to Element E?
-In Element E, the assessor checks for the approved design for equipment and machinery, ensures that valid certificates of fitness are available, verifies the competency of the machinery operator, and ensures that safety guards are in place for power-operated tools.
Outlines
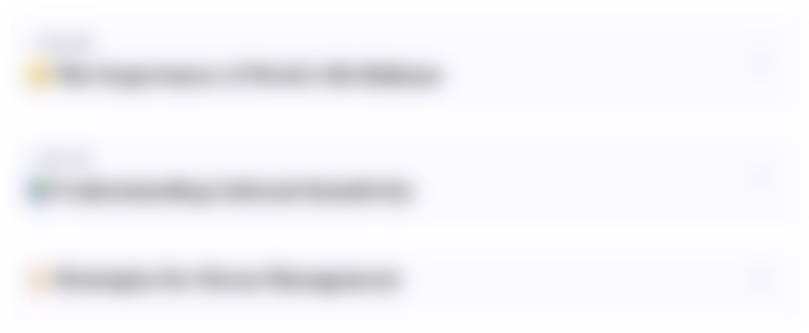
This section is available to paid users only. Please upgrade to access this part.
Upgrade NowMindmap
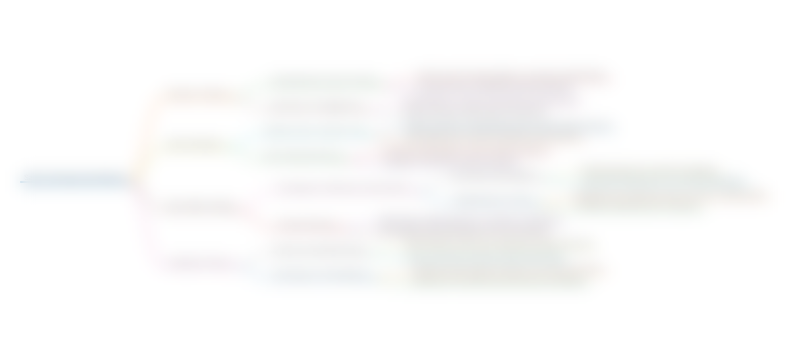
This section is available to paid users only. Please upgrade to access this part.
Upgrade NowKeywords
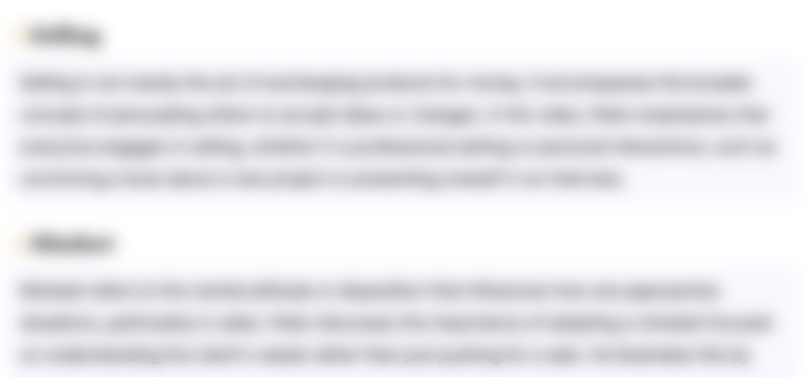
This section is available to paid users only. Please upgrade to access this part.
Upgrade NowHighlights
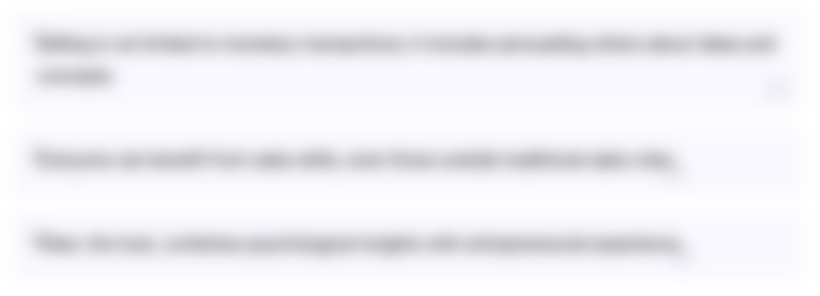
This section is available to paid users only. Please upgrade to access this part.
Upgrade NowTranscripts
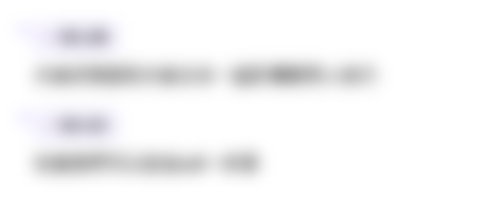
This section is available to paid users only. Please upgrade to access this part.
Upgrade NowBrowse More Related Video
5.0 / 5 (0 votes)