Taylorismo║Conceito, Contexto Histórico, Características, Objetivos, Princípios║RESUMO animado
Summary
TLDRThis video discusses the Taylorism model, developed by Frederick Winslow Taylor in the late 19th and early 20th centuries. It aims to increase productivity and reduce the time and effort involved in industrial work by applying scientific methods. Key principles include planning, worker preparation, control, execution, and task specialization. The approach focuses on optimizing tasks, enhancing worker efficiency, and standardizing processes, which led to the development of subsequent production models like Fordism and Toyotism. The video provides an overview of these principles and their impact on industrial production.
Takeaways
- 😀 Taylorism, also known as Scientific Management, was developed by Frederick Winslow Taylor during the late 19th and early 20th centuries.
- 😀 Taylorism aimed to increase productivity by reducing the time and effort spent on tasks in industrial settings.
- 😀 The model emerged during the Second Industrial Revolution to address issues like low productivity and conflicts between employers and workers.
- 😀 The primary goal of Taylorism is to optimize tasks in companies and improve worker efficiency to reduce production time.
- 😀 Key features of Taylorism include the replacement of empirical methods with scientific methods, and the division of tasks within organizations.
- 😀 Taylorism promotes increasing workers' pay while reducing working hours to enhance productivity and worker satisfaction.
- 😀 The system also includes structured promotion and reward schemes for workers, aiming to boost motivation and morale.
- 😀 The model includes strict time control, standardization of work processes, and continuous training to improve worker skills and efficiency.
- 😀 Five main principles form the foundation of Taylorism: planning, worker preparation, control, execution, and job specialization.
- 😀 Taylorism introduced the division of labor into production lines, making each worker responsible for a specific task to increase productivity.
- 😀 Although criticized for dehumanizing workers, Taylorism had a lasting impact on industrial production models, influencing later systems like Fordism and Toyotism.
Q & A
What is Taylorism?
-Taylorism, also known as Scientific Management, is an industrial production model developed by Frederick Winslow Taylor in the late 19th and early 20th centuries. It aimed to increase labor productivity by optimizing tasks and reducing time and effort in production processes.
What were the main problems that Taylorism sought to address?
-Taylorism was created to solve several problems faced by the industrial society, including increasing conflicts between employees and employers, low productivity, and systemic inefficiencies in the workplace.
What are the main goals of Taylorism?
-The main goals of Taylorism are to optimize tasks within companies, improve worker efficiency, and reduce production time to achieve the highest possible output in the shortest time.
How did Taylorism change traditional management methods?
-Taylorism replaced traditional empirical methods with scientific methods in management. It emphasized using data, analysis, and experimentation to determine the most efficient ways of performing tasks and managing workers.
What are the key characteristics of Taylorism?
-The key characteristics of Taylorism include the substitution of empirical methods with scientific management, task division and hierarchy, higher wages, shorter work hours, promotion and reward systems for workers, creation of managerial positions, strict time control, standardized training methods, and division of responsibilities between workers and management.
What are the five fundamental principles of Taylorism?
-The five fundamental principles of Taylorism are: 1) Planning principle: Replace empirical methods with scientific ones. 2) Worker preparation: Assign workers to specific tasks based on their skills and provide training. 3) Control principle: Monitor workers to reduce inefficiencies. 4) Execution principle: Distribute tasks efficiently to maximize productivity. 5) Job fragmentation: Divide tasks into smaller, specialized components to optimize labor.
What does the 'Principle of Planning' in Taylorism emphasize?
-The 'Principle of Planning' emphasizes the need to replace traditional, empirical methods with scientifically proven approaches to ensure better decision-making in the workplace.
What is the role of worker preparation in Taylorism?
-Worker preparation in Taylorism involves matching workers to specific tasks that suit their skills and providing them with the necessary training to perform those tasks efficiently.
How does Taylorism control worker efficiency?
-Taylorism controls worker efficiency through strict monitoring of tasks, preventing idle time, reducing unnecessary physical effort, and managing resistance to the work process, all aimed at maximizing productivity.
How did Taylorism influence later production models like Fordism and Toyotism?
-Taylorism laid the foundation for later production models such as Fordism and Toyotism. These systems built on Taylor’s ideas of efficiency and task specialization, with Fordism introducing assembly line production and Toyotism focusing on continuous improvement and worker empowerment.
Outlines
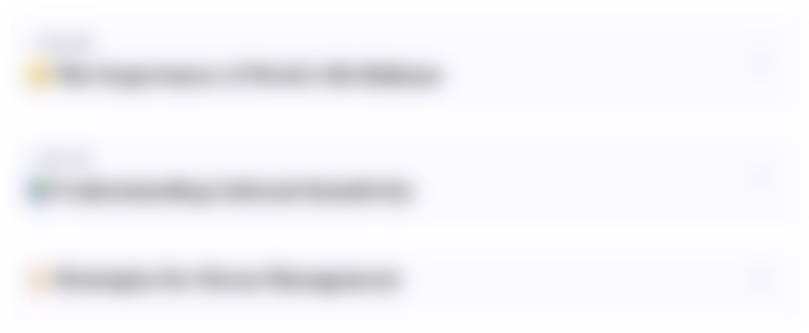
This section is available to paid users only. Please upgrade to access this part.
Upgrade NowMindmap
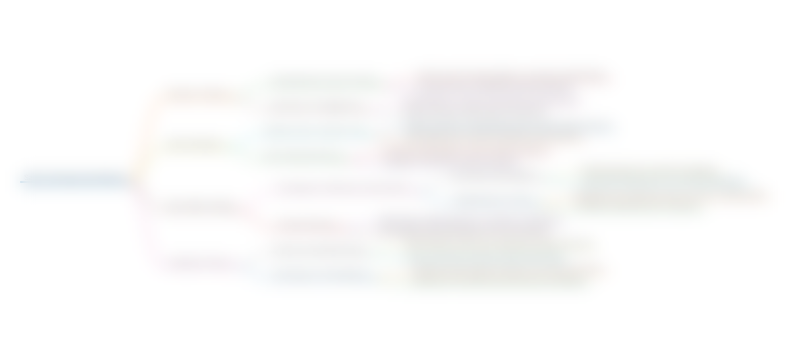
This section is available to paid users only. Please upgrade to access this part.
Upgrade NowKeywords
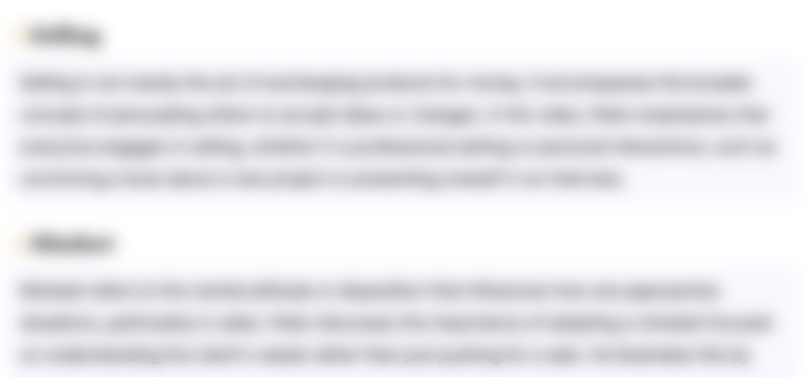
This section is available to paid users only. Please upgrade to access this part.
Upgrade NowHighlights
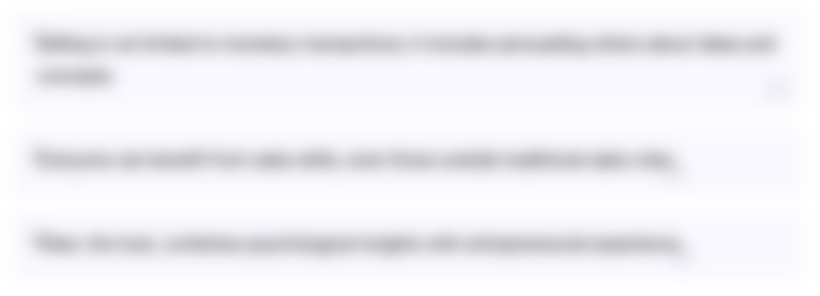
This section is available to paid users only. Please upgrade to access this part.
Upgrade NowTranscripts
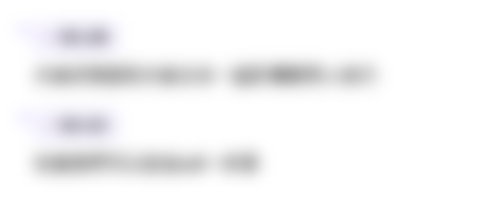
This section is available to paid users only. Please upgrade to access this part.
Upgrade Now5.0 / 5 (0 votes)