Case Study 2: Flash Fire in Pontoon Tank
Summary
TLDRA tragic flash fire occurred in a confined space where a team of workers was performing roller painting and cleaning tasks. Despite passing multiple gas tests, the mixing of flammable paint and hardener, coupled with poor ventilation and unmonitored gas concentrations, led to the accumulation of dangerous vapors. Electrical hazards, including exposed filaments and unmaintained lighting, contributed to the ignition. The incident resulted in one fatality and three injuries. Key lessons learned include the need for thorough risk assessments, better vapor control, gas monitoring, flame-proof lighting, and improved ventilation to prevent similar accidents in the future.
Takeaways
- 😀 The incident involved a flash fire in a confined space where six workers were performing roller painting, resulting in one fatality and three injuries.
- 😀 Before work began, a gas test was conducted, showing the confined space was safe, and an entry permit was approved.
- 😀 Workers used flammable substances, such as thinner, during the work, which contributed to the accumulation of dangerous vapors in the confined space.
- 😀 A second gas test was conducted, and the quality of the painting was checked, but the mixing of paint and hardener in the confined space contributed to the fire risk.
- 😀 The flash fire occurred after workers brought in drums of paint and hardener, and one worker mixed them in the confined space.
- 😀 The activities performed in the confined space led to the accumulation of flammable solvent vapors, which were not properly monitored or managed.
- 😀 No portable gas detectors were used to monitor the concentration of flammable gases in the confined space during the work.
- 😀 Lighting with exposed filament electrical wires posed a fire hazard, and there was no effective maintenance regime to ensure their safety.
- 😀 A risk assessment should always be conducted before working in confined spaces to identify potential hazards and implement risk minimization measures.
- 😀 To avoid flammable vapor accumulation, workers should mix paint and hardener outside the confined space and use portable gas detectors to monitor gas concentrations.
- 😀 Flameproof lighting should be used in confined spaces, and a regular maintenance regime should be established to ensure proper lighting and electrical wire safety.
- 😀 Ventilation techniques, such as dilution or forced ventilation, should be used to prevent the accumulation of flammable vapors, especially during increased painting activities.
Q & A
What happened in the incident described in the script?
-A flash fire occurred in a confined space where six workers were performing roller painting and cleaning activities. One worker died, and three others were injured.
What safety procedures were followed before the incident occurred?
-Before the work started, an entry permit for painting and cleaning in a confined space was applied. The safety assessor conducted a gas test, which showed that the confined space was safe for entry, and the permit was endorsed.
What actions were taken by the workers on the day of the incident?
-On the day of the incident, the workers carried out vacuuming, cleaning with thinner (a flammable substance), and performed roller painting. After mixing paint and hardener, they began applying the paint.
How many gas tests were conducted during the day, and what were their results?
-Three gas tests were conducted. The first and second tests showed no abnormalities, while the third test was done after the workers began mixing paint and hardener, just before the flash fire occurred.
What activities contributed to the accumulation of flammable vapors in the confined space?
-Activities such as mixing paint and hardener, distributing the mixture into empty drums, and drying paint contributed to the build-up of flammable vapors in the confined space.
What safety equipment or measures were lacking during the incident?
-Portable gas detectors were not provided to monitor the concentration of flammable gases, and the lighting system had exposed filament electrical wires, which posed an ignition risk.
What role did lighting play in the accident?
-The lighting system had exposed filament electrical wires, which became an ignition source, potentially contributing to the flash fire.
What were the key lessons learned from this incident?
-Key lessons include conducting a thorough risk assessment, avoiding the mixing of flammable substances in confined spaces, using portable gas detectors, implementing flameproof lighting, and ensuring proper ventilation.
How should ventilation be managed in confined spaces during high-risk activities?
-Ventilation should be managed using dilution or forced ventilation methods to prevent the accumulation of flammable vapors. Ideally, both exhaust and forced ventilation methods should be used together.
What measures can prevent the build-up of flammable vapors in confined spaces?
-To prevent the build-up of flammable vapors, activities like mixing paint and hardener should be done outside the confined space, and continuous monitoring with portable gas detectors should be in place.
Outlines
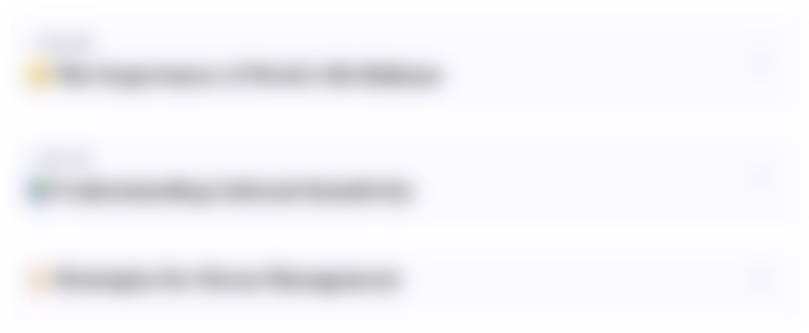
This section is available to paid users only. Please upgrade to access this part.
Upgrade NowMindmap
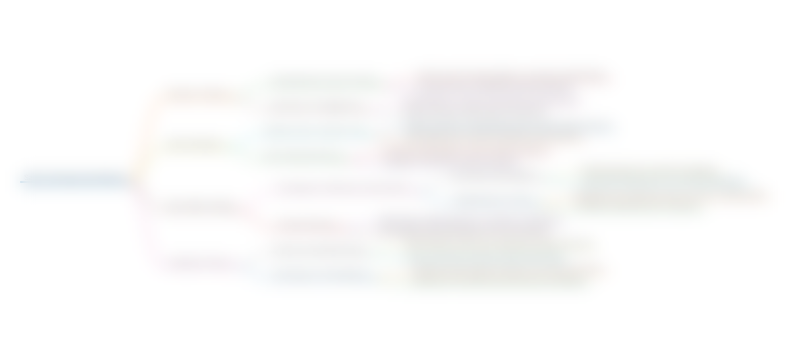
This section is available to paid users only. Please upgrade to access this part.
Upgrade NowKeywords
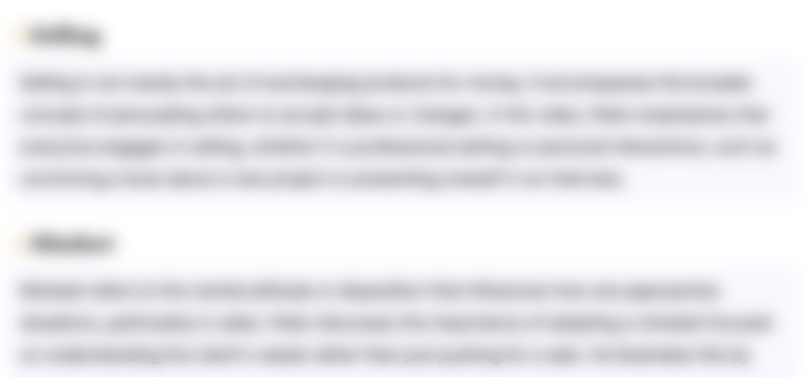
This section is available to paid users only. Please upgrade to access this part.
Upgrade NowHighlights
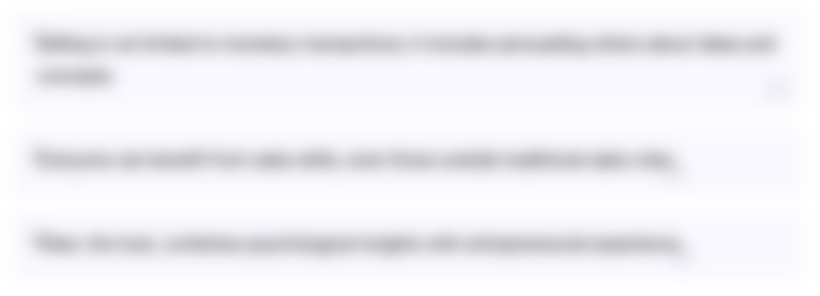
This section is available to paid users only. Please upgrade to access this part.
Upgrade NowTranscripts
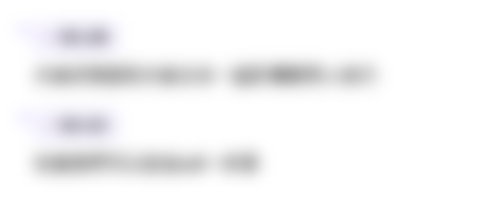
This section is available to paid users only. Please upgrade to access this part.
Upgrade NowBrowse More Related Video
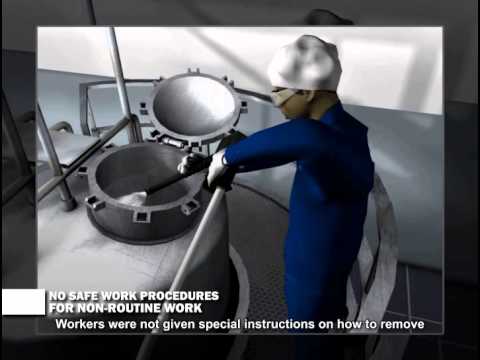
Case Study 4: Workers Overcome by Toxic Gas During Reactor Washing
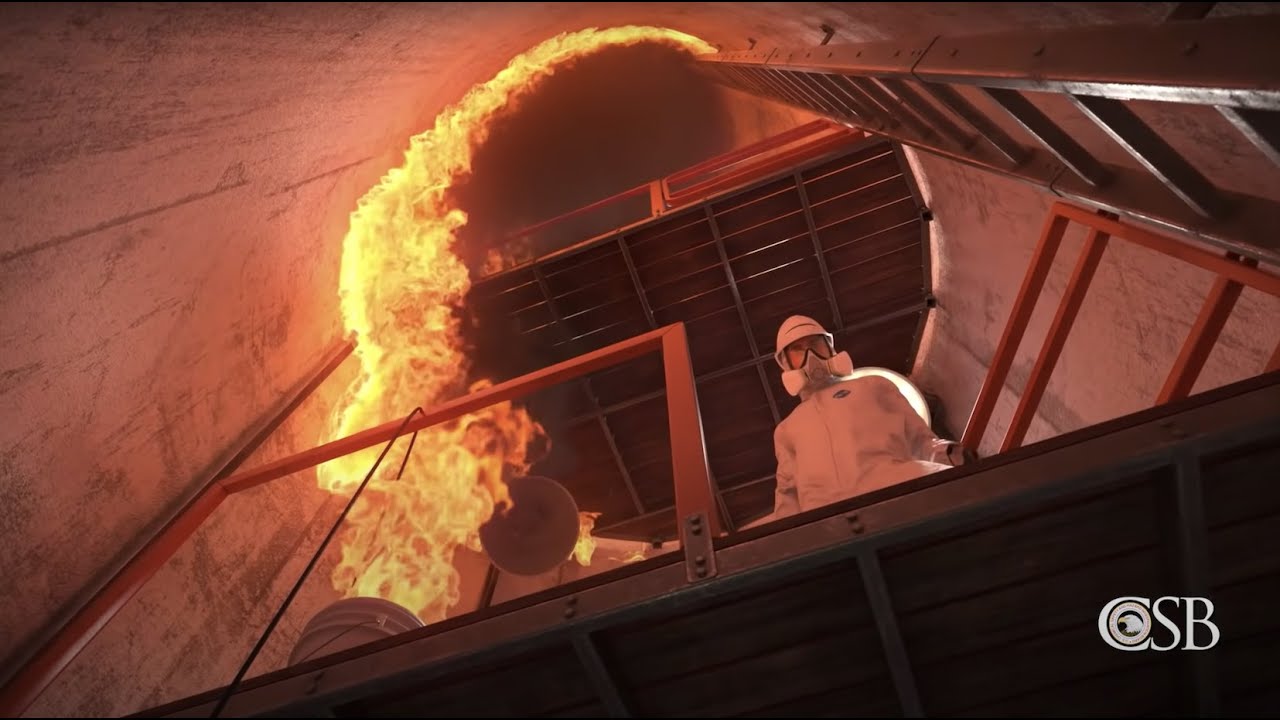
Simultaneous Tragedy: Fire at Evergreen Packaging

Case Study 3: Toxic Gas Poisoning in Manhole
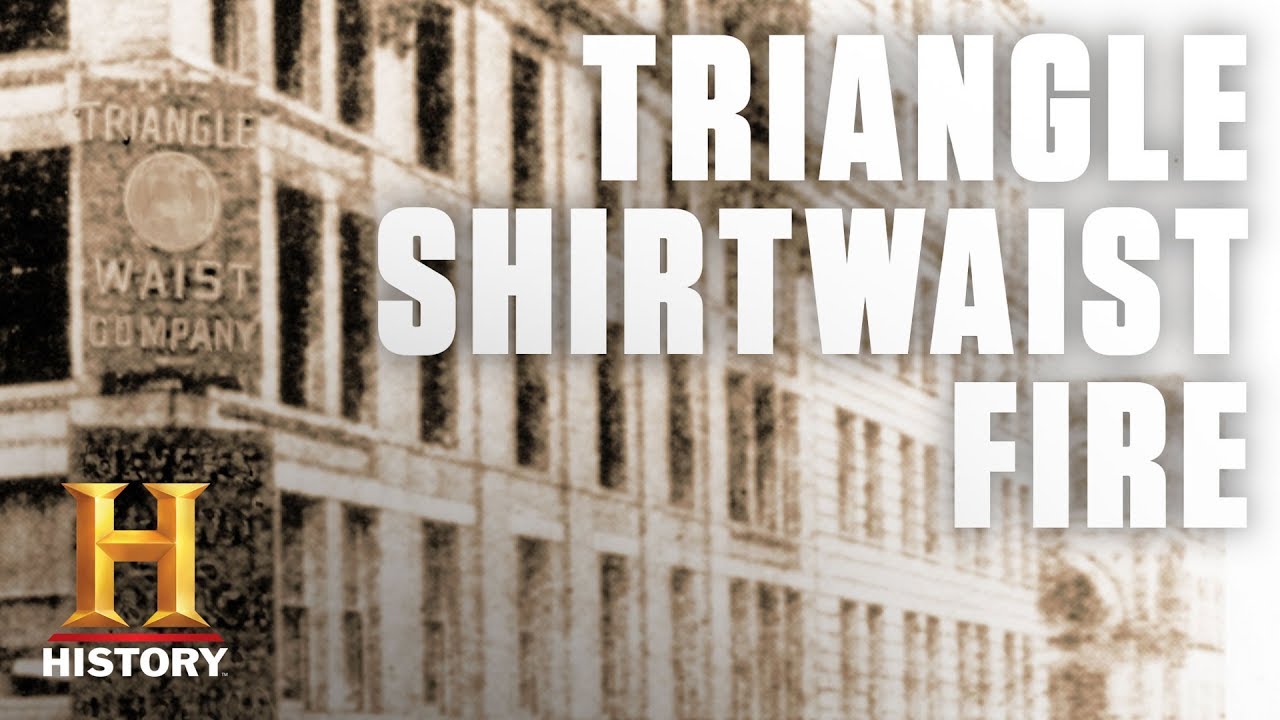
The Triangle Shirtwaist Factory Fire | History
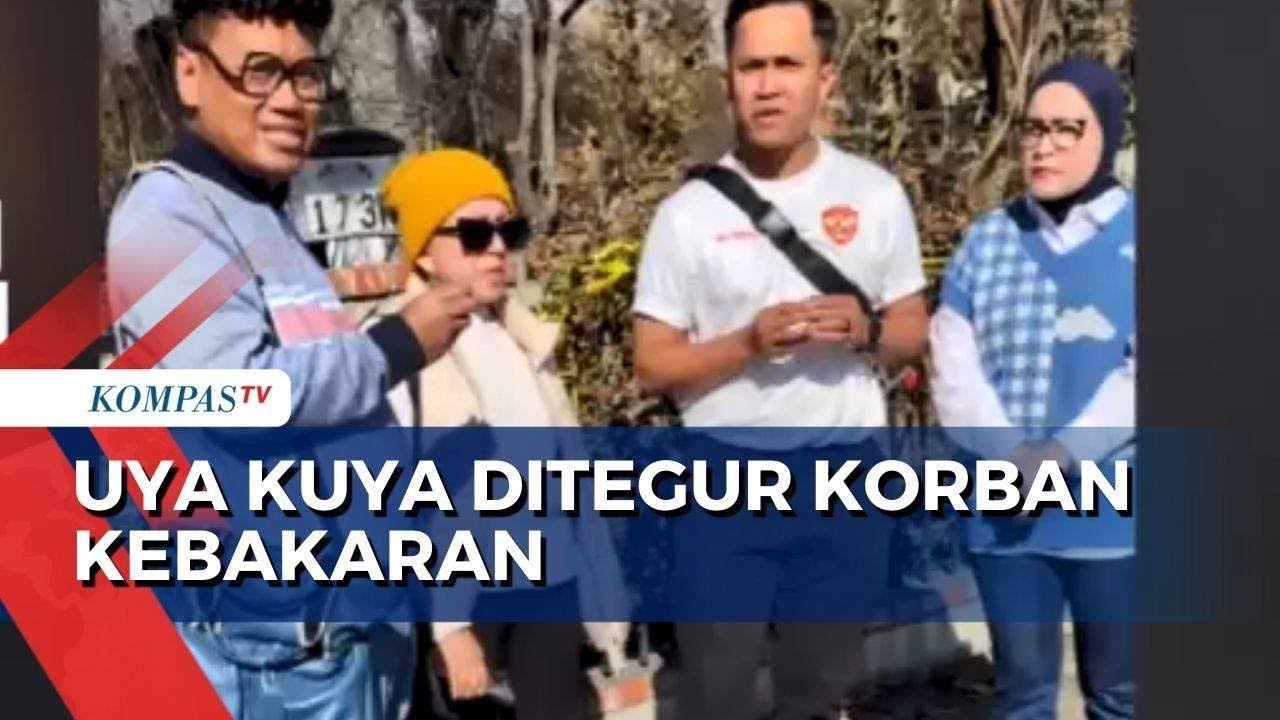
Uya Kuya Ditegur Korban Kebakaran di Los Angeles saat Rekam Konten
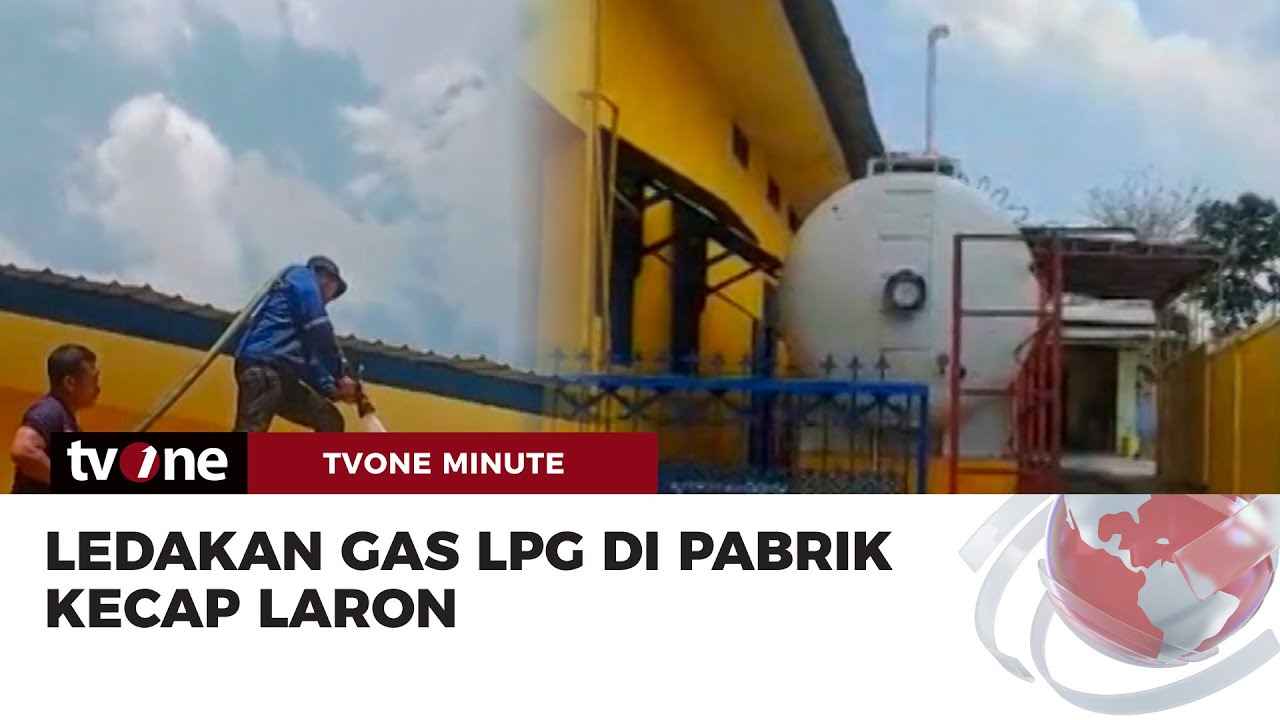
Tangki Gas Pabrik Kecap di Tuban Meledak, 4 Pekerja Luka-luka | tvOne Minute
5.0 / 5 (0 votes)