Procedimento ad elementi termici per contatto testa a testa
Summary
TLDRThis video script provides a detailed explanation of the head-to-head contact welding process for thermal elements such as tubes and fittings. It outlines six key stages of welding, focusing on parameters like temperature, pressure, and timing, as specified by the Italian standard UNI 10520. The process includes preparation, heating, removal of the heating element, welding pressure, cooling, and final rest. The script emphasizes the importance of precise pressure values, careful timing, and consistent quality for a successful weld. The use of a welding machine manual and a welding report simplifies the process for the welder.
Takeaways
- 😀 The welding process involves heating two surfaces (tube heads and fittings) to a specified temperature and then joining them with force, causing material fusion.
- 😀 The parts being welded must have the same thickness; welding elements with different thicknesses is prohibited.
- 😀 The welding procedure consists of at least six distinct phases, each with specific parameters for temperature, pressure, and timing.
- 😀 The graph representing the process shows pressure (force applied) on the vertical axis and time on the horizontal axis.
- 😀 The welder can determine the appropriate pressure to apply using the machine's instruction manual, which contains pressure tables for different element sizes.
- 😀 The drag force (pressure) increases with the weight of the tube or fitting being welded and requires the use of rollers.
- 😀 Once the correct pressure is identified, it must be added to pressures at specific phases (e.g., Phase 1 and Phase 5).
- 😀 The welding protocol simplifies the welder's task by listing all necessary parameters, ensuring consistency in the welding process.
- 😀 Pressure for drag force (Pd) should be checked for every weld to maintain accurate and successful joining.
- 😀 The six welding phases include preparation, heating, removal of the thermo-element, actual welding pressure, cooling, and post-cooling outside the machine.
- 😀 Phase durations are based on tube thickness and must be followed precisely to avoid poor weld quality, such as cold welding due to rapid cooling.
Q & A
What is the basic principle behind head-to-head thermal welding of elements?
-The basic principle is to heat two surfaces, such as the heads of tubes and fittings, to a specified temperature and then unite them with force. This force allows the molten material to penetrate, mix, and fuse the parts together.
Can elements with different thicknesses be welded using this technique?
-No, the elements to be welded must have the same thickness. It is prohibited to weld elements with differing thicknesses.
What are the six phases of the welding process described in the script?
-The six phases are: 1) Pre-contact and preheating, 2) Heating, 3) Thermal element removal, 4) Achieving welding pressure, 5) Cooling under pressure, 6) Cooling outside the machine.
How is the pressure for welding determined?
-The pressure is calculated based on the thickness of the elements to be welded. Specific values for pressure are outlined in the welding machine manual and are used to adjust the force required during the welding process.
Why is it important to monitor the thermal element removal phase?
-It is important because polyethylene, when in a molten state, cools quickly. Removing the thermal element for too long could cause the material to cool prematurely, leading to a poor or incomplete weld.
What happens during the heating phase, and how long does it last?
-During the heating phase, heat is applied to ensure that the temperature reaches deep within the elements to be welded. The duration of this phase depends on the thickness of the elements, calculated using a specific formula (12 times the thickness of the tube).
What is the role of the welding machine's manual in the process?
-The welding machine manual is crucial for determining the correct pressure to apply based on the diameter and thickness of the elements being welded. It contains tables that provide pressure values to guide the welder.
What is the significance of the welding pressure in phase 4?
-In phase 4, the welding pressure is the key to achieving a proper bond between the elements. The pressure is calculated using the tube thickness, and it is applied to ensure a solid and lasting connection between the elements.
How long should the cooling under pressure phase last, and what is the formula for its duration?
-The cooling under pressure phase should last a time equal to the thickness of the tube in minutes, plus three minutes. The pressure applied during this phase is p5, ensuring the joint solidifies properly.
What is the role of the welder during the welding process?
-The welder's role is to ensure that the correct parameters are followed during the welding process, including applying the right pressures and monitoring the timings for each phase. The welder's skill is crucial in achieving a successful weld.
Outlines
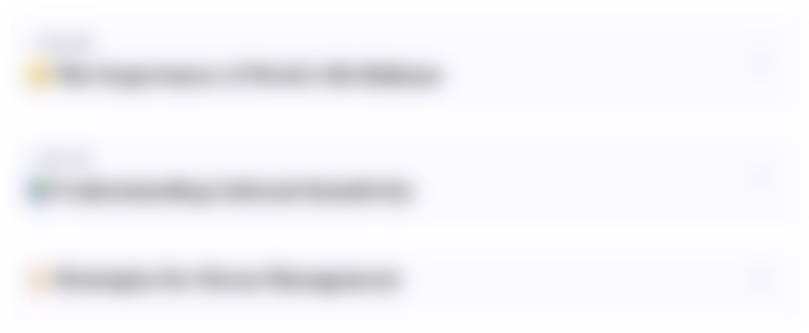
This section is available to paid users only. Please upgrade to access this part.
Upgrade NowMindmap
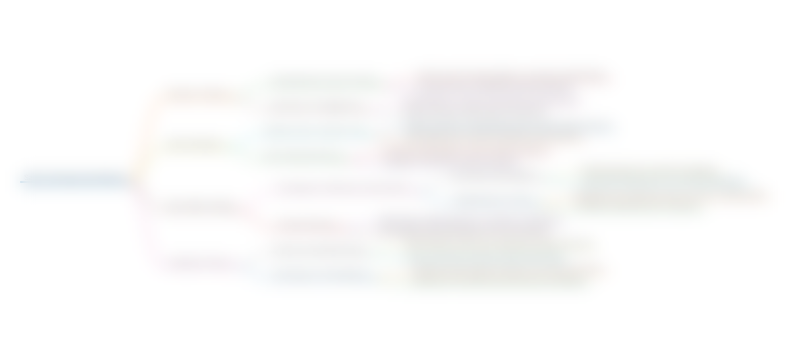
This section is available to paid users only. Please upgrade to access this part.
Upgrade NowKeywords
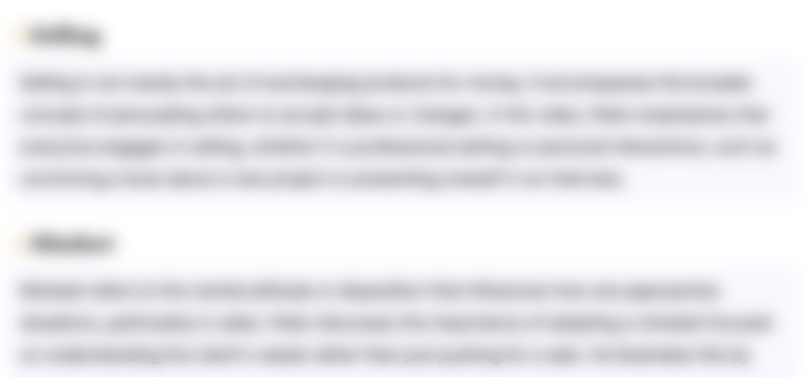
This section is available to paid users only. Please upgrade to access this part.
Upgrade NowHighlights
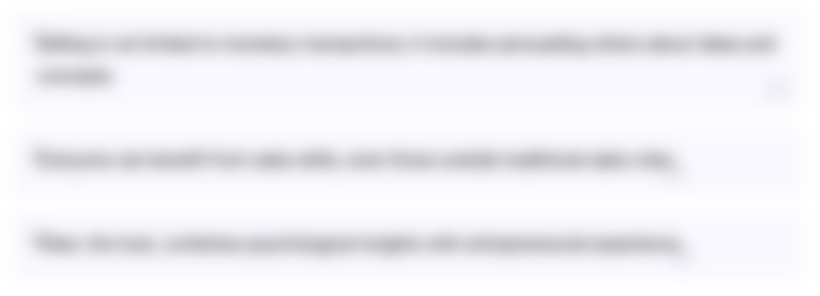
This section is available to paid users only. Please upgrade to access this part.
Upgrade NowTranscripts
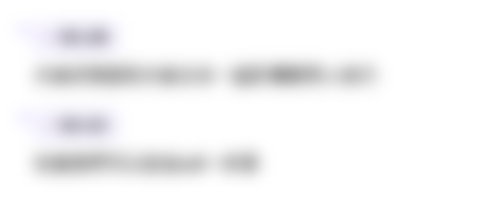
This section is available to paid users only. Please upgrade to access this part.
Upgrade Now5.0 / 5 (0 votes)