How to Design a Performance Optimized Power Module in a Week
Summary
TLDRThis webinar focuses on enhancing design workflows with an automated solution that bridges electrical and mechanical design tools. The presenters discuss how their software, Heeds, automates data flow between tools, speeding up processes and improving efficiency. They emphasize how this solution integrates seamlessly with existing workflows, allowing companies to gradually adopt the system without disrupting their operations. The solution also accelerates optimization and offers quick financial returns by minimizing the need for manual engineering resources. The session highlights the benefits of automation in design and optimization, tailored to meet the specific needs of each customer.
Takeaways
- 😀 The integration of electrical and mechanical design workflows enhances the ability to import bondwire structures directly into layouts, improving the design process.
- 😀 The solution supports both traditional mechanical flows and highly automated software solutions to streamline design and simulation.
- 😀 Heeds software automates the workflow between tools, allowing efficient data transfer and parallel processing to reduce overall time.
- 😀 The software can be customized with pre-built or user-created portals to connect different tools in ways that best suit the user’s needs.
- 😀 Workflow automation minimizes manual scripting, making the process faster and more reliable while controlling hardware resource use.
- 😀 Transitioning to the new workflow does not require replacing existing systems but allows incorporating the best elements of current tools.
- 😀 The solution offers flexibility, allowing for integration of customer-specific tools into the workflow to meet their unique requirements.
- 😀 The new workflow is designed to be low-risk, ensuring a smooth deployment without significant disruptions to existing work processes.
- 😀 Engineers can continue to work with their current tools and processes while benefiting from a highly automated new workflow that accelerates design optimization.
- 😀 The introduction of this solution provides a quick return on investment, requiring minimal engineering resources after the initial setup.
- 😀 The session closed with appreciation for the audience and the presenters, with contact information provided for further support.
Q & A
What is the main benefit of using the ECAD to MCAD interface mentioned in the script?
-The ECAD to MCAD interface allows users to integrate bondwire structures directly into the layout, enabling seamless electrical connectivity and workflow between tools, which is essential for optimizing the design process.
What is the role of Heeds software in the workflow automation?
-Heeds software automates the workflow between tools by managing data transfer, performing necessary modifications, and controlling the operation of subsequent tools. It also optimizes the use of hardware resources and supports parallel simulations to speed up the process.
How does the Heeds software handle parallel simulations?
-Heeds software can run parallel simulations that require the same design input data but do not depend on each other for results. This parallelization reduces the overall time scale of the process.
Can the Heeds software be customized to connect different tools?
-Yes, Heeds provides a range of predefined 'portals' for commonly used industry tools. These portals can be modified or customized to connect different tools based on the user's specific requirements.
Why is it important to deploy the new workflow alongside an existing one?
-Deploying the new workflow alongside the existing one minimizes risk during transition. It allows for a gradual integration of new tools while ensuring the productivity of the current system is not disrupted.
How does the deployment of the new workflow impact productivity?
-The deployment is highly automated, meaning that after the initial design setup, it requires little engineering resource, allowing existing engineers to continue their work with minimal disruption. This results in accelerated design optimization.
What is the financial benefit of introducing this new workflow?
-The financial benefit lies in the quick return on investment (ROI) provided by the automated processes. After a brief setup period, the system can yield results almost immediately, making it cost-effective for businesses.
How does the new workflow contribute to design optimization?
-The new workflow accelerates design optimization by streamlining the process and enabling efficient simulations and adjustments. This leads to faster iterations and more accurate design outcomes.
What are some of the challenges when transitioning to a new workflow?
-Challenges include the need to train staff on the new system, ensuring the new tools do not disrupt current processes, and integrating custom or legacy tools into the new automated workflow.
What role does customization play in the new workflow's flexibility?
-Customization allows the workflow to be tailored to the specific needs of the customer, enabling the integration of existing tools and processes, and making the transition smoother for organizations.
Outlines
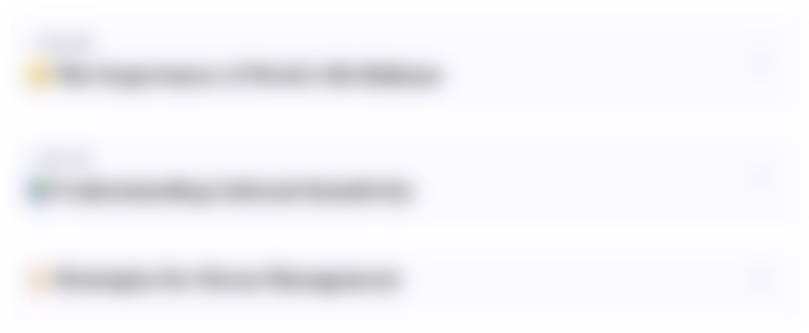
This section is available to paid users only. Please upgrade to access this part.
Upgrade NowMindmap
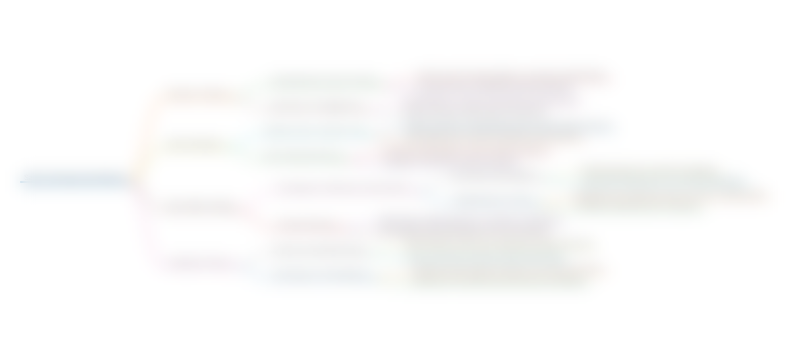
This section is available to paid users only. Please upgrade to access this part.
Upgrade NowKeywords
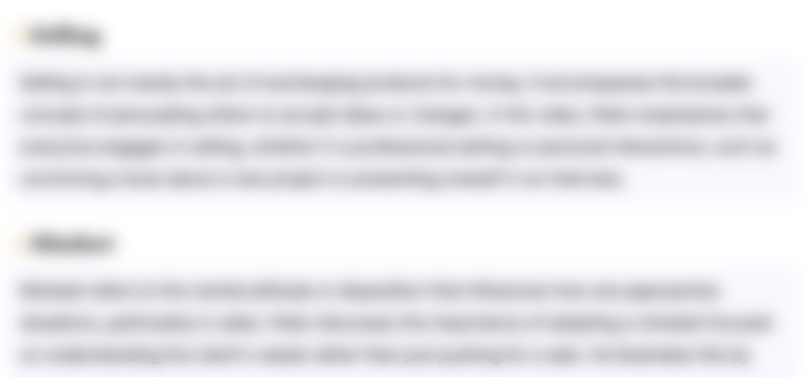
This section is available to paid users only. Please upgrade to access this part.
Upgrade NowHighlights
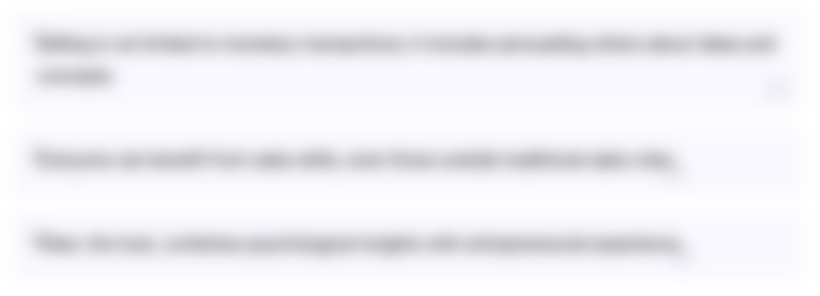
This section is available to paid users only. Please upgrade to access this part.
Upgrade NowTranscripts
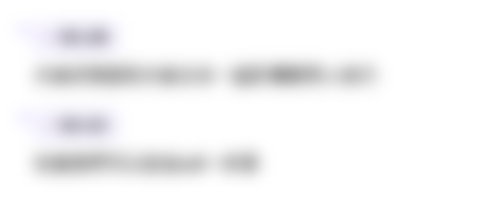
This section is available to paid users only. Please upgrade to access this part.
Upgrade NowBrowse More Related Video
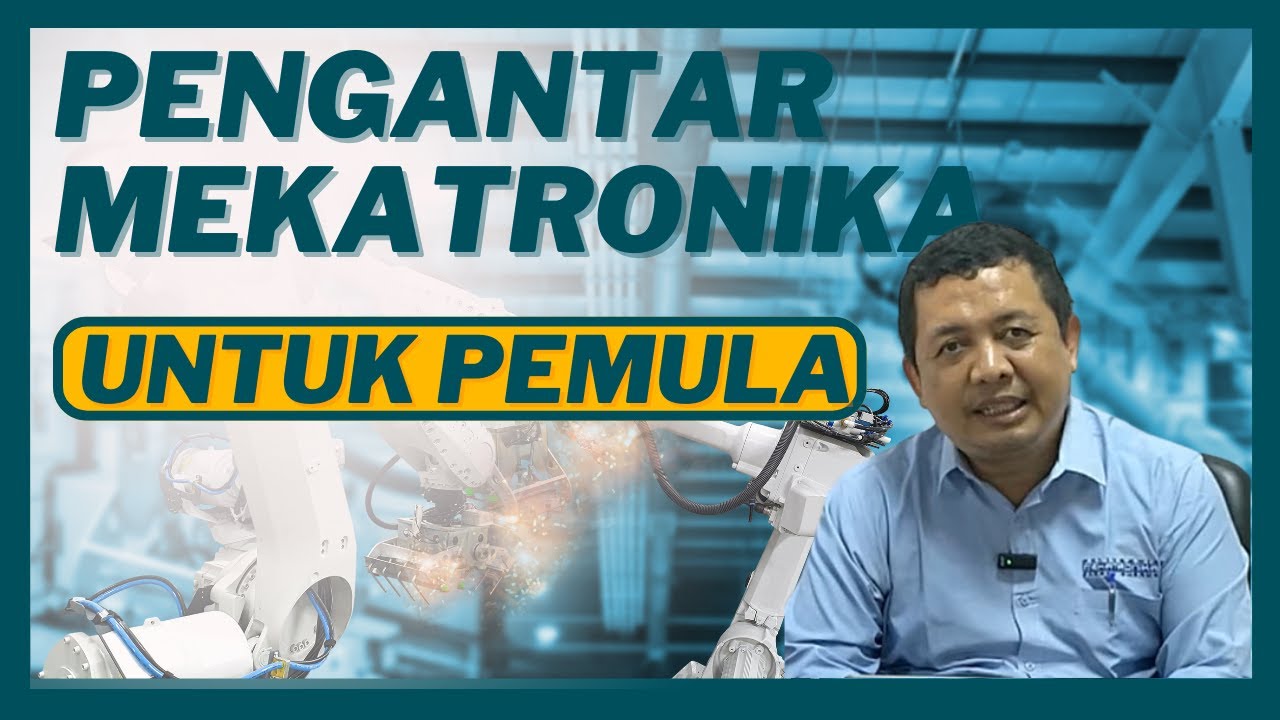
1. Memulai Petualangan Mekatronika: Kuliah Pengantar Mekatronika!
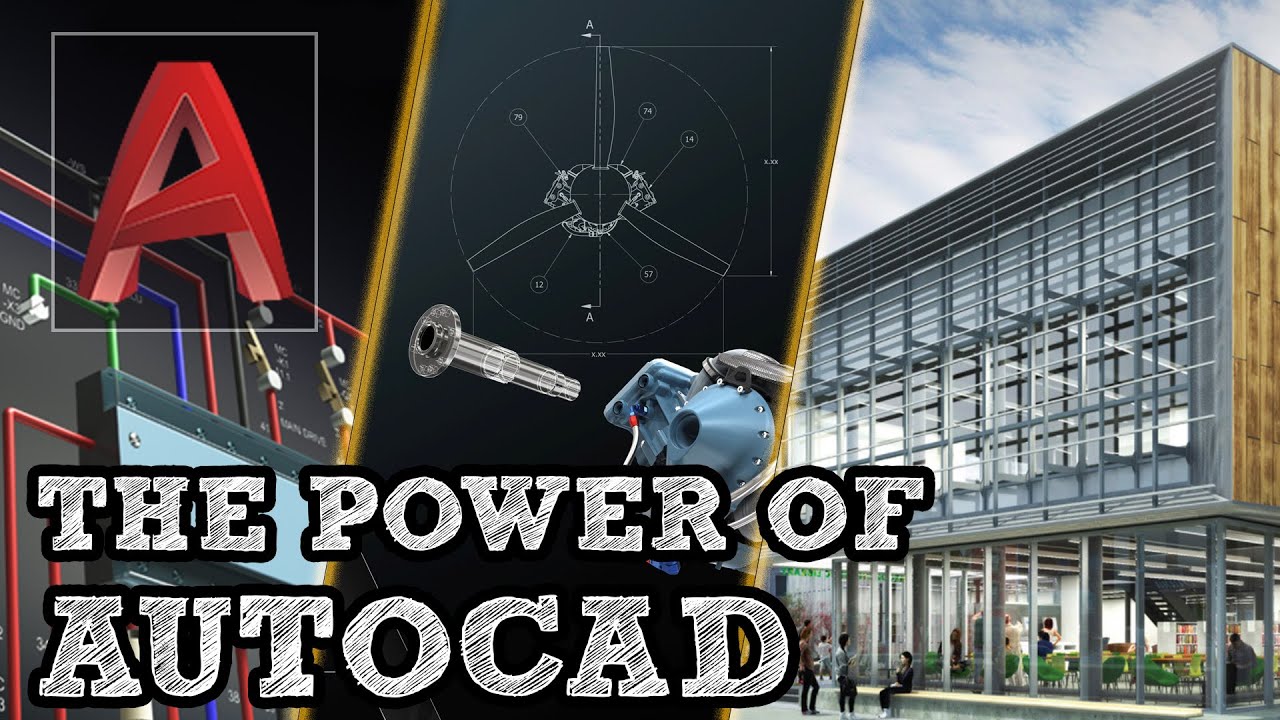
What is Autocad used for
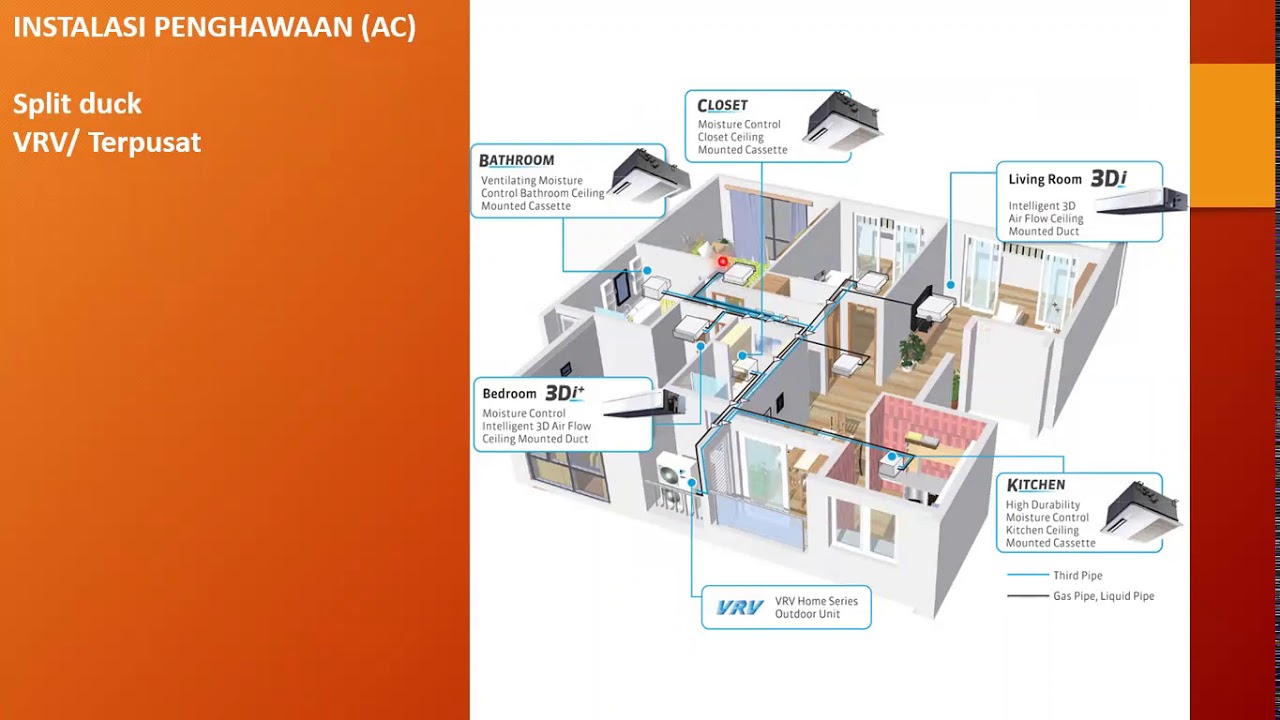
PERTEMUAN 04

AI Agents vs MCP Servers, which is better?

So You Want to Be a MECHATRONICS ENGINEER | Inside Mechatronics Engineering

How to use Artificial Intelligence in Mechanical Engineering - a detailed analysis in 10 min
5.0 / 5 (0 votes)