Biaya Overhead Pabrik Dlm Akuntansi Biaya Sesi 1
Summary
TLDRThis video explains the concept of Factory Overhead Costs in manufacturing, detailing how these indirect costs are categorized, such as indirect materials, labor, and other operational expenses. The video covers how overhead rates are calculated using allocation bases like labor or machine hours, emphasizing the importance of accurate cost allocation for pricing, profitability, and decision-making. Additionally, it discusses different types of overhead costs, including fixed, variable, and semi-variable costs, and how businesses can efficiently manage and allocate these costs for better production management.
Takeaways
- ๐ Factory overhead costs are indirect costs that cannot be traced directly to a product, such as indirect labor, materials, and other factory-related expenses.
- ๐ Factory overhead is categorized into three groups: by nature (e.g., materials, labor), by behavior (fixed, variable, semi-variable), and by department.
- ๐ The characteristic of factory overhead costs is that they are not proportional to the level of production, making it difficult to allocate them to individual products.
- ๐ Factory overhead costs include indirect materials, indirect labor, depreciation of equipment, maintenance costs, and utilities required to maintain factory operations.
- ๐ The method for determining overhead rates involves creating a budget, selecting an allocation base (e.g., direct labor hours, machine hours), and calculating the rate.
- ๐ Factory overhead is charged to products using a predetermined rate, which helps in managing cost fluctuations and maintaining consistency in pricing.
- ๐ The rate for overhead costs can vary based on production volume, with lower production leading to higher overhead allocation per unit and vice versa.
- ๐ It's essential to consider the factory's capacity when estimating overhead costs, with different methods for calculating capacity, such as theoretical, practical, and normal capacity.
- ๐ Overhead allocation methods include using direct labor, direct materials, or machine hours as the allocation base, depending on which factor most closely relates to the overhead incurred.
- ๐ Effective cost management and proper allocation of factory overheads are crucial for achieving accurate product costing and maximizing operational efficiency.
Q & A
What is the definition of factory overhead costs?
-Factory overhead costs are indirect costs that cannot be directly traced to specific products but are necessary for production. These include expenses such as materials, labor, and various factory maintenance costs.
What are the three main classifications of factory overhead costs?
-Factory overhead costs are classified into three main categories: materials, labor, and other indirect costs. They are also categorized as fixed costs, variable costs, and semi-variable costs based on their behavior with production levels.
What is the difference between fixed and variable overhead costs?
-Fixed overhead costs remain constant regardless of production volume, such as depreciation on factory machines. Variable overhead costs fluctuate with production levels, such as electricity used for running machines.
What is a semi-variable cost in the context of factory overhead?
-A semi-variable cost is an overhead cost that changes, but not in direct proportion to production levels. For example, certain factory utilities may increase as production rises but not linearly.
How is the overhead rate calculated?
-The overhead rate is calculated by dividing total overhead costs by a suitable allocation base, such as direct labor hours, machine hours, or direct material costs, depending on the company's cost structure.
What are the steps involved in budgeting factory overhead?
-The steps in budgeting factory overhead include estimating the total overhead costs, choosing an appropriate allocation base, and then calculating the overhead rate based on that base.
What is the significance of capacity levels in determining the overhead rate?
-Capacity levels are important because they help determine how much overhead will be incurred at different production levels. Theoretical, practical, and expected capacities guide how the overhead rate is set and adjusted.
What is a flexible budget, and how does it relate to factory overhead?
-A flexible budget adjusts for changes in production levels, allowing businesses to accurately allocate factory overhead costs based on actual activity rather than initial estimates.
Why is accurate overhead cost allocation critical for a company?
-Accurate overhead cost allocation is essential for determining product pricing, controlling costs, and ensuring that financial reports reflect true expenses, which supports better decision-making.
Can you give an example of how an overhead rate is calculated?
-For example, if a company estimates total overhead costs of $100,000 for the year and expects 50,000 direct labor hours, the overhead rate would be $2 per labor hour ($100,000 รท 50,000 labor hours).
Outlines
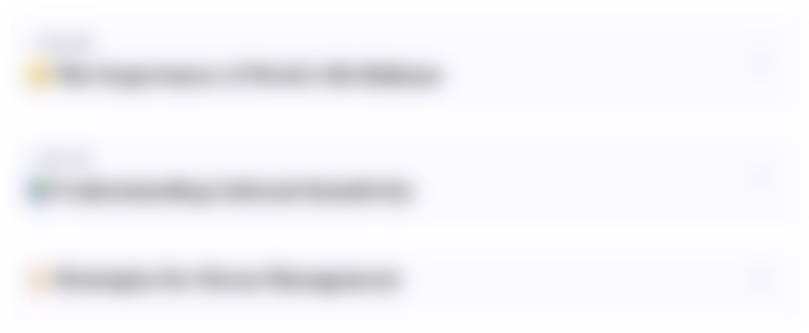
This section is available to paid users only. Please upgrade to access this part.
Upgrade NowMindmap
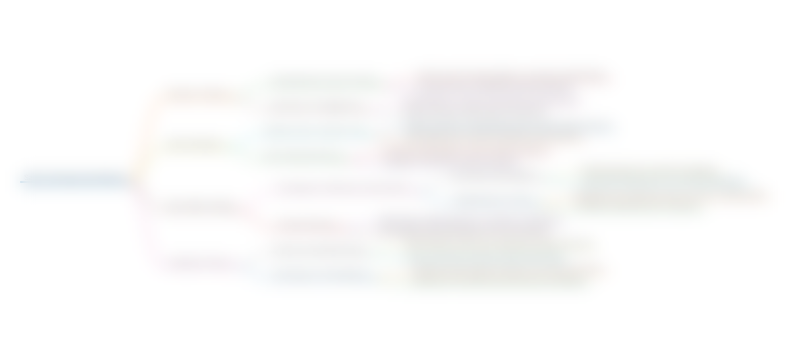
This section is available to paid users only. Please upgrade to access this part.
Upgrade NowKeywords
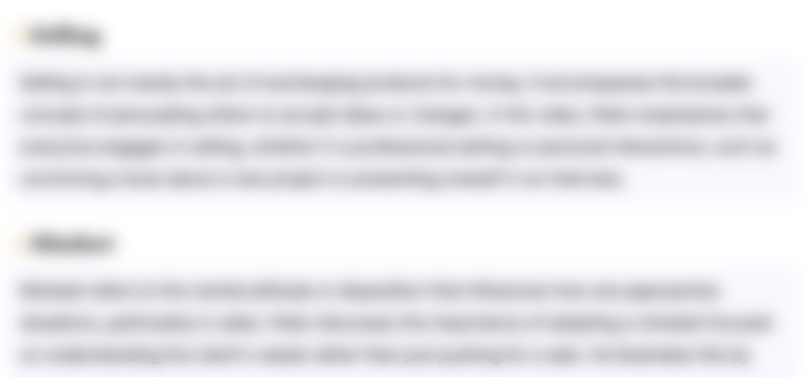
This section is available to paid users only. Please upgrade to access this part.
Upgrade NowHighlights
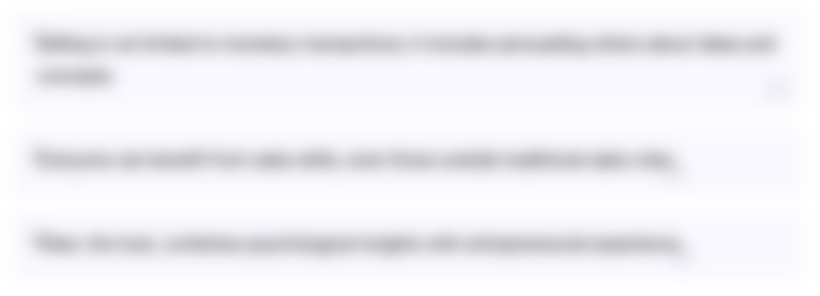
This section is available to paid users only. Please upgrade to access this part.
Upgrade NowTranscripts
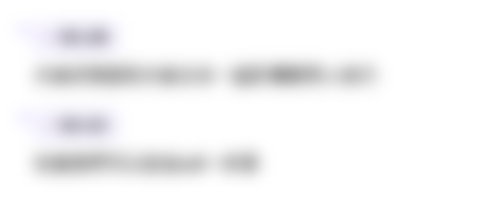
This section is available to paid users only. Please upgrade to access this part.
Upgrade NowBrowse More Related Video

(FACIL) Materiales Directos, Mano de Obra Directa, Costos Indirectos de Fรกbrica

Unsur Unsur Biaya Produksi (Produk Kreatif Kewirausahaan) XII SMK
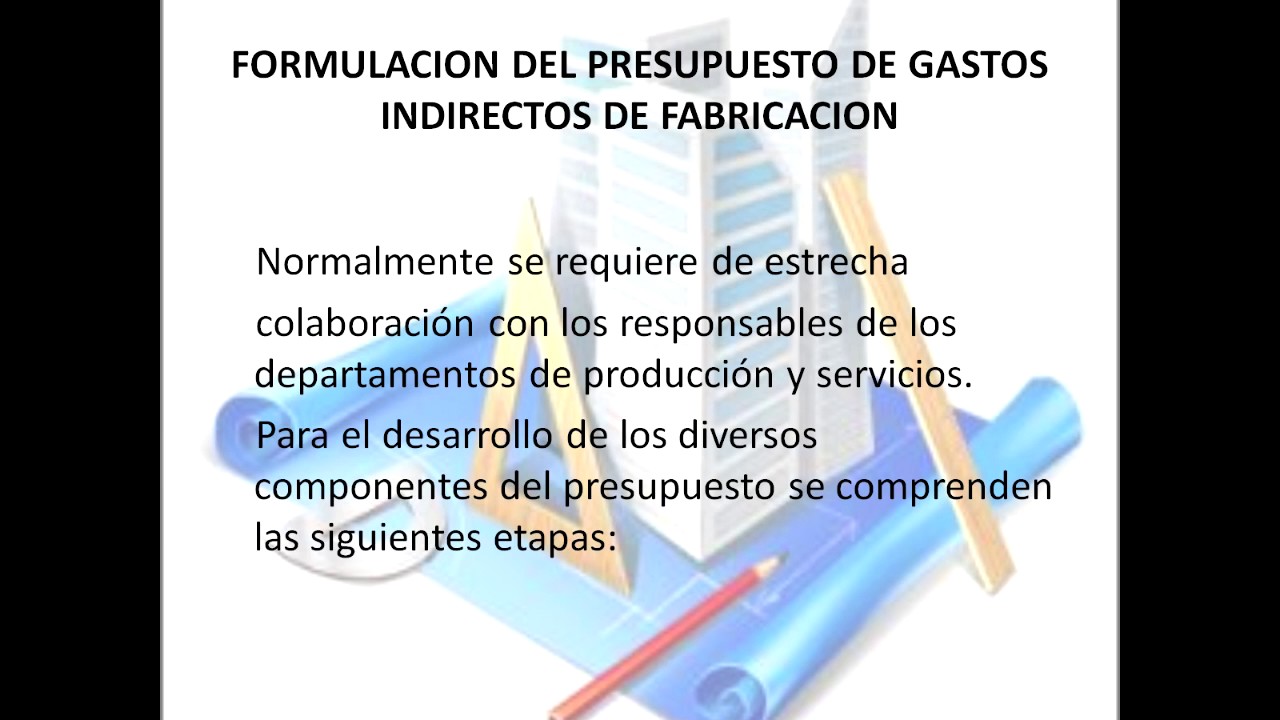
Presupuesto de gastos indirectos de fabricaciรณn
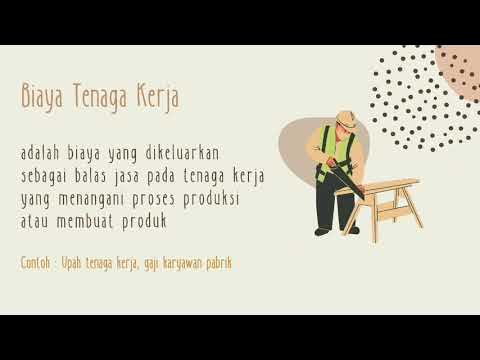
Menghitung Harga Pokok Produksi - Part 1

UNDERSTAND MANUFACTURING ACCOUNTS WITHIN 10 MINUTES!!!

Akuntansi untuk Tenaga Kerja part 1
5.0 / 5 (0 votes)