cst auto forno
Summary
TLDRThe video script explains the process of iron production in a blast furnace. It details the steps of charging materials such as iron ore, sinter, pellets, fluxes, and coke into the furnace. The coke reacts with heated air in the combustion zone to generate gases, which reduce and melt the metallic charge. The result is molten pig iron and slag, which are separated by density and channeled into torpedo cars and granulators. The entire process is carefully monitored from the control room to ensure efficient operation.
Takeaways
- 😀 The blast furnace process begins with the shutdown of activities in the iron production area, also known as reduction, which involves removing oxygen from raw materials.
- 😀 Pig iron, the main product of the blast furnace, is the primary raw material used in steel production.
- 😀 The furnace is charged with a combination of iron ore, sinter, pellets, fluxes, and coke, which are fed through a conveyor belt to the furnace's hoppers.
- 😀 These raw materials are distributed alternately in the furnace using a loading system, ensuring uniform processing.
- 😀 Heated air is blown into the furnace from regenerators, entering through vents at the bottom in the combustion zone, where it reacts with the raw materials.
- 😀 In the combustion zone, pulverized coal, coke, and hot air interact at high temperatures, creating gases that help reduce and melt the metallic charge.
- 😀 The high-temperature gases rise and react with the descending iron ore, reducing it and melting it into pig iron while forming slag.
- 😀 The molten pig iron and slag are separated by their differing densities, with pig iron flowing into designated channels and slag moving to another channel.
- 😀 The pig iron is transferred to torpedo cars for further processing, while slag is directed to granulators for cooling.
- 😀 The entire process is closely monitored and controlled from a control room, ensuring efficient operation and product quality.
Q & A
What is the purpose of a blast furnace in iron production?
-The blast furnace is used to produce pig iron (ferro gusa) by reducing iron ore. The main product, pig iron, serves as the primary raw material for steel production.
What is meant by the term 'reduction' in the context of a blast furnace?
-In the context of a blast furnace, 'reduction' refers to the process of removing oxygen from iron ore, which results in the production of iron. This reaction is key to turning iron ore into usable metal.
What are the primary raw materials used in the blast furnace?
-The primary raw materials are iron ore (in the form of pellets or sinter), fluxing agents, and coke.
How are the materials loaded into the blast furnace?
-The raw materials are loaded into the blast furnace through a conveyor belt that delivers them to hoppers at the top of the furnace. These materials are then distributed alternately inside the furnace.
What role does the hot air play in the blast furnace?
-Hot air is blown into the furnace through the tuyeres at the bottom, creating the combustion zone. The hot air reacts with the coke and other materials to generate high temperatures necessary for the reduction of iron ore.
What happens in the combustion zone of the blast furnace?
-In the combustion zone, pulverized coal and coke react with the hot air to generate gases at very high temperatures. These gases rise through the furnace and react with the descending charge, facilitating the reduction of iron ore.
What are the products formed in the blast furnace?
-The main products of the blast furnace process are pig iron (ferro gusa) and slag. The pig iron is the molten iron, while the slag is a by-product of the reduction process.
How is the pig iron separated from the slag?
-Pig iron and slag are separated due to their difference in density. The pig iron, being denser, sinks to the bottom, while the slag rises to the top and is removed separately.
What is the function of the refractory channels in the blast furnace?
-The refractory channels are used to transport the molten pig iron and slag. The pig iron is channeled through these to the torpedo cars, and the slag is directed to granulators for further processing.
How is the entire blast furnace process monitored and controlled?
-The blast furnace process is closely monitored and controlled from a control room, where various parameters such as temperature, pressure, and material flow are continuously tracked to ensure the process runs efficiently.
Outlines
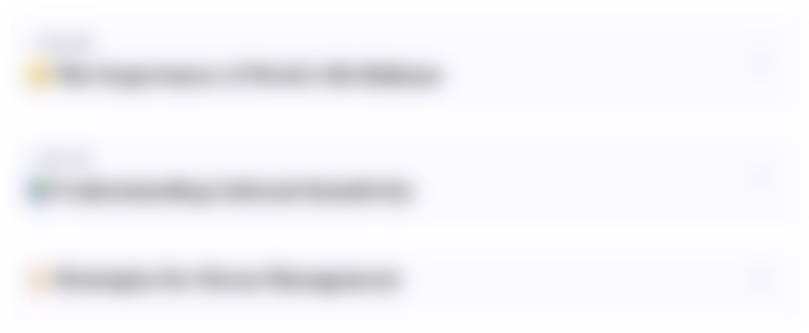
This section is available to paid users only. Please upgrade to access this part.
Upgrade NowMindmap
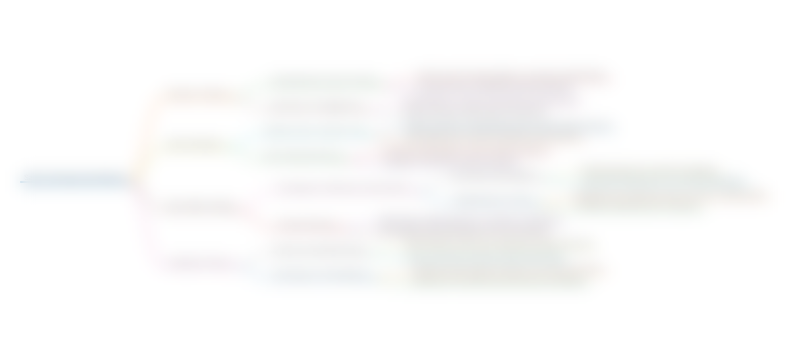
This section is available to paid users only. Please upgrade to access this part.
Upgrade NowKeywords
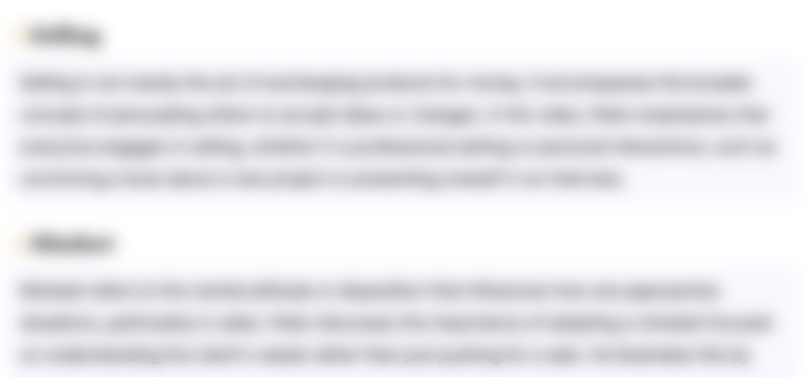
This section is available to paid users only. Please upgrade to access this part.
Upgrade NowHighlights
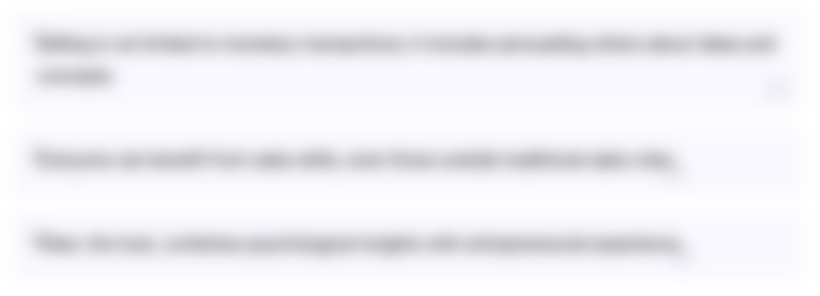
This section is available to paid users only. Please upgrade to access this part.
Upgrade NowTranscripts
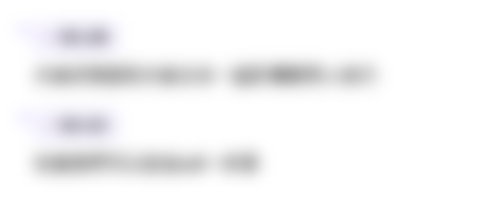
This section is available to paid users only. Please upgrade to access this part.
Upgrade NowBrowse More Related Video

The Extraction of Iron (GCSE Chemistry)
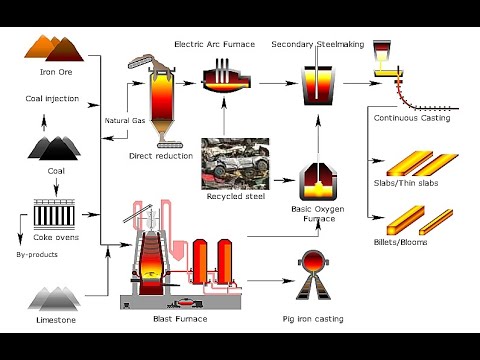
Complete Steel Making Process in easy steps ll. TATA VOCATIONAL TRAINING
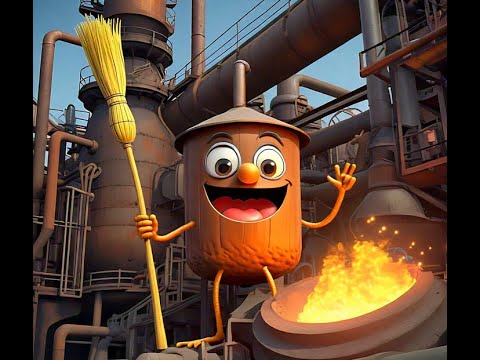
Managing blast furnace slag - its chemical and physical features - Metallurgical waste management
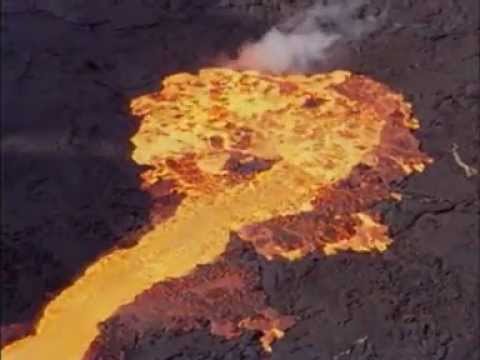
Iron and Steel

How Iron Ore is Turned Into Steel?
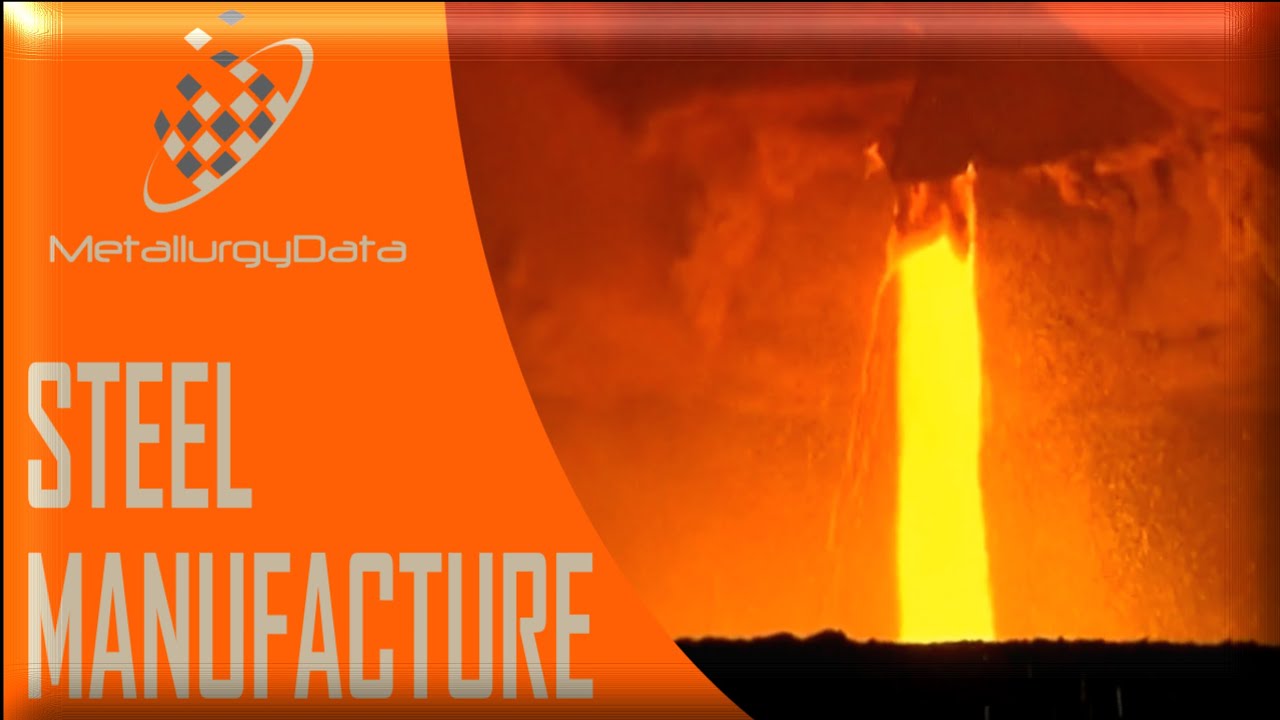
Steel Manufacturing - Including Blast Furnace and BOS
5.0 / 5 (0 votes)