DIY | Casting Vacuum Chamber
Summary
TLDRIn this video, the creator builds a vacuum chamber for their workshop, highlighting its versatility in tasks like making molds and metal casting. After several attempts, the final design features a clear acrylic side, heat resistance, and easy-to-use lid. The process includes building the chamber from scratch using epoxy resin, wood, and various parts like valves and a vacuum gauge. The video also details the creation of a second chamber for lost wax casting, including the construction of heat-resistant gaskets and the final testing of the chamber's vacuum functionality, achieving excellent results.
Takeaways
- 😀 A vacuum chamber is essential for various applications such as making plaster molds, silicone molds, and metal casting.
- 😀 The chamber needs to be clear on one side to observe the process, and it must withstand high temperatures (up to 800°F or 430°C) for metal casting.
- 😀 The lid must be easily opened and sealed completely to ensure proper vacuum conditions, a crucial feature for success.
- 😀 A failed first attempt led to a second, more successful design with modifications, particularly to the lid for better sealing.
- 😀 Using acrylic sheets for the chamber is not enough, as they must be at least ¾ inch thick for proper vacuum sealing.
- 😀 Epoxy resin was used to create a clear sheet that provides durability and strength for the chamber, alongside other wood and material components.
- 😀 The lid was made from a round plastic container and sealed with silicone to ensure air-tightness during operation.
- 😀 The vacuum chamber includes various components like brass ball valves, vacuum gauges, and pipe fittings for proper functionality.
- 😀 The system uses a dust collection hose and vacuum tube to connect the main chamber to a secondary chamber for metal casting processes.
- 😀 After painting and sealing the chamber, epoxy resin was applied for added strength and to make cleaning easier.
- 😀 The vacuum system was successfully tested with silicone molding, demonstrating the effectiveness of the design by achieving a smooth, bubble-free result.
Q & A
Why is a vacuum chamber important in the user's workshop?
-A vacuum chamber is important because it serves multiple purposes, including creating plaster and silicone molds, and metal casting, which is useful for achieving high-quality results in intricate mold designs and precise measurements.
What was the major issue the user faced during their first attempt at creating the vacuum chamber?
-The major issue was with the lid, which needed to be easily opened and closed while being completely air-sealed. This challenge led to a failure in the first attempt.
What material did the user initially use for the vacuum chamber's clear side, and why was it not sufficient?
-The user initially used a half-inch thick acrylic sheet, which felt strong by hand but was not sturdy enough when vacuuming. The user later upgraded to a three-quarters inch thick acrylic sheet for better durability.
How did the user solve the issue of sealing the lid of the vacuum chamber?
-The user solved the issue by using a round plastic container with a silicone sealant, ensuring the lid would fit securely and create a strong seal without sticking, thanks to a layer of Vaseline on the container’s mouth.
What tools and materials did the user use to assemble the vacuum chamber?
-The user used a variety of tools including a trim router, band clamps, and screws. They also utilized materials like black silicone sealant, epoxy resin, wood pieces, and acrylic sheets for the chamber's construction.
What specific vacuum components did the user purchase for the chamber, and why are they important?
-The user purchased two ¼ inch brass ball valves, a check valve, air hose pipe fittings, a vacuum pressure gauge, and pipe sealant tape. These components are necessary for controlling airflow, sealing the chamber, and monitoring the vacuum pressure during operation.
How did the user ensure that the vacuum hose connection would be secure and capable of handling pressure?
-The user reinforced the vacuum hose by inserting a stainless steel coil inside the hose to handle pressure, and they sealed the connections with heat shrink tubing and electrical tape for added strength and durability.
Why did the user choose to paint the vacuum chamber black?
-The user chose to paint the vacuum chamber black for practical reasons: it would hide any imperfections and make the cleaning process easier while providing an aesthetic appearance.
What additional feature did the user add to the vacuum chamber for better performance in casting?
-The user added a heat resistance chamber for lost wax casting, which was made using a mixture of fine sand and refractory cement. This chamber helps with casting metal at high temperatures.
What were the final results after testing the vacuum chamber with silicone for rubber sprue bases?
-The results were highly satisfying, as the vacuum chamber successfully removed air bubbles from the silicone, resulting in a smooth and shiny product. The chamber was able to maintain a strong vacuum for efficient silicone molding.
Outlines
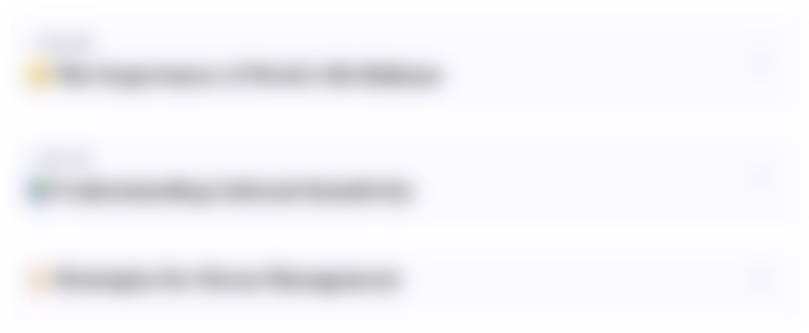
This section is available to paid users only. Please upgrade to access this part.
Upgrade NowMindmap
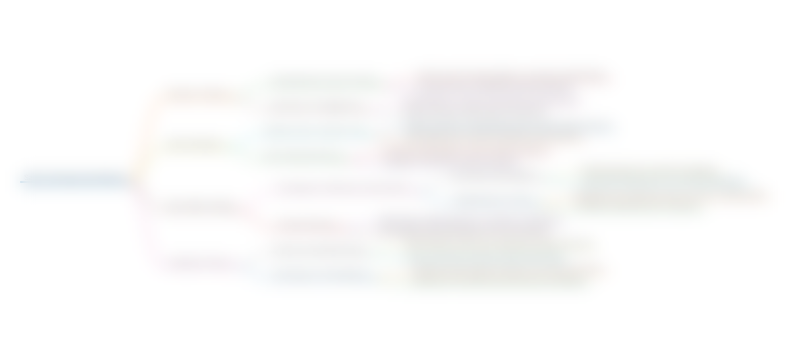
This section is available to paid users only. Please upgrade to access this part.
Upgrade NowKeywords
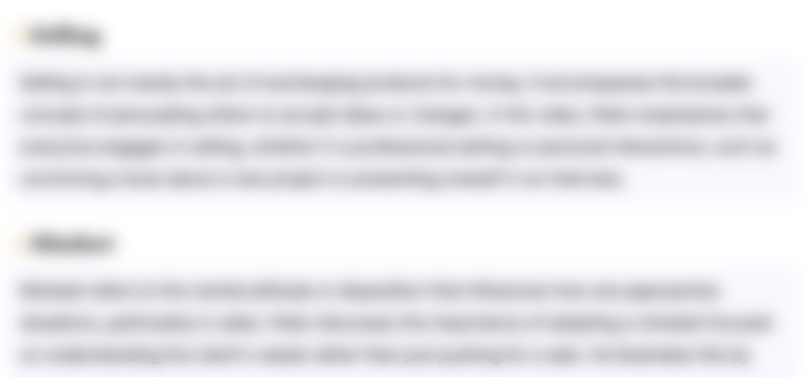
This section is available to paid users only. Please upgrade to access this part.
Upgrade NowHighlights
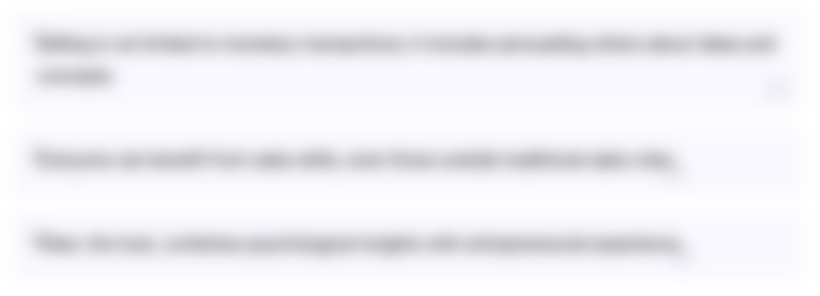
This section is available to paid users only. Please upgrade to access this part.
Upgrade NowTranscripts
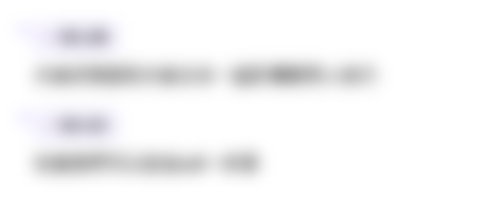
This section is available to paid users only. Please upgrade to access this part.
Upgrade NowBrowse More Related Video

What Is Casting? 11 Types of Casting Processes Explanation
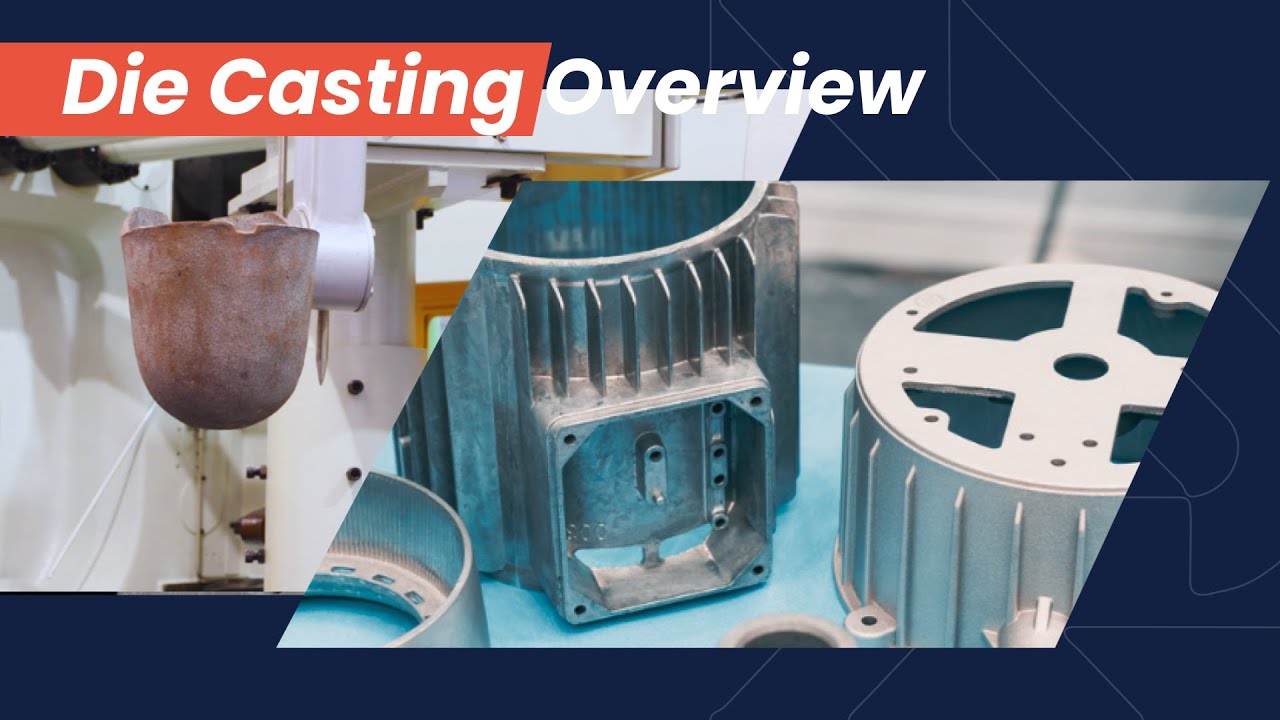
What Is Die Casting? Understand the Most Efficiency Metal Casting Process
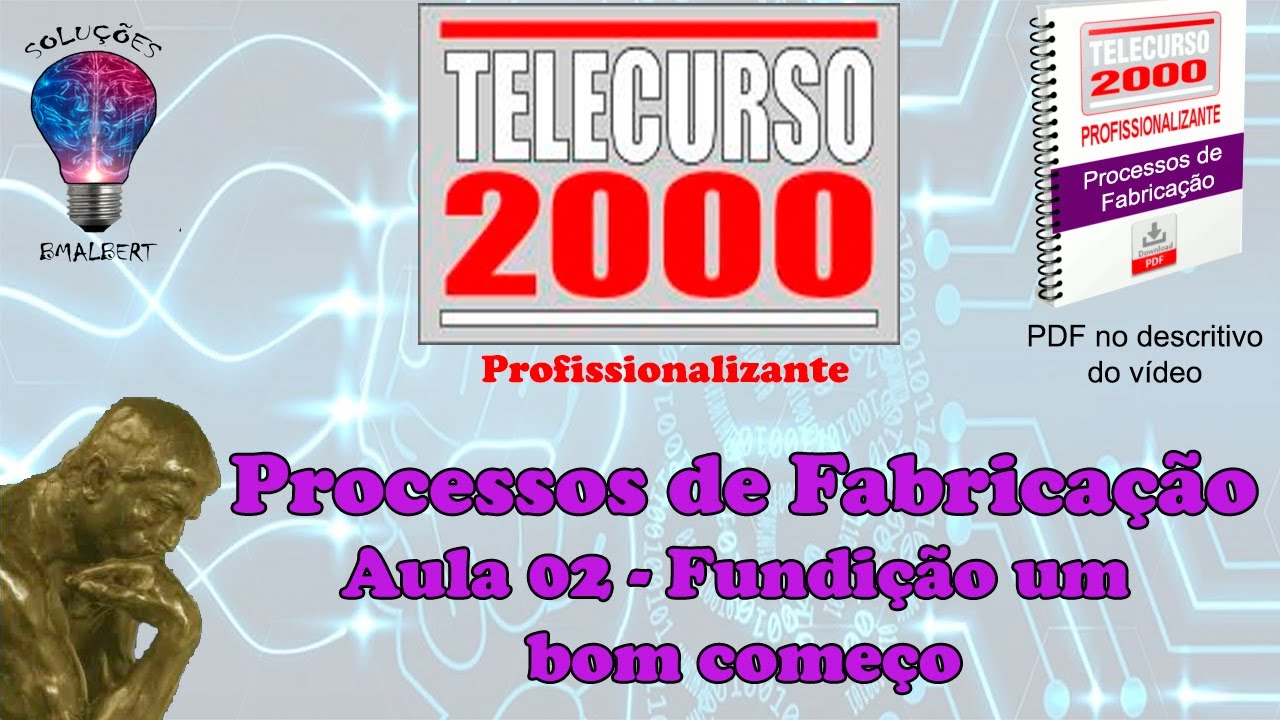
Telecurso 2000 - Processos de Fabricação - 02 Fundição um bom começo

Proses Pengecoran

PENGECORAN LOGAM | Praktikum MK Teknologi Manufaktur
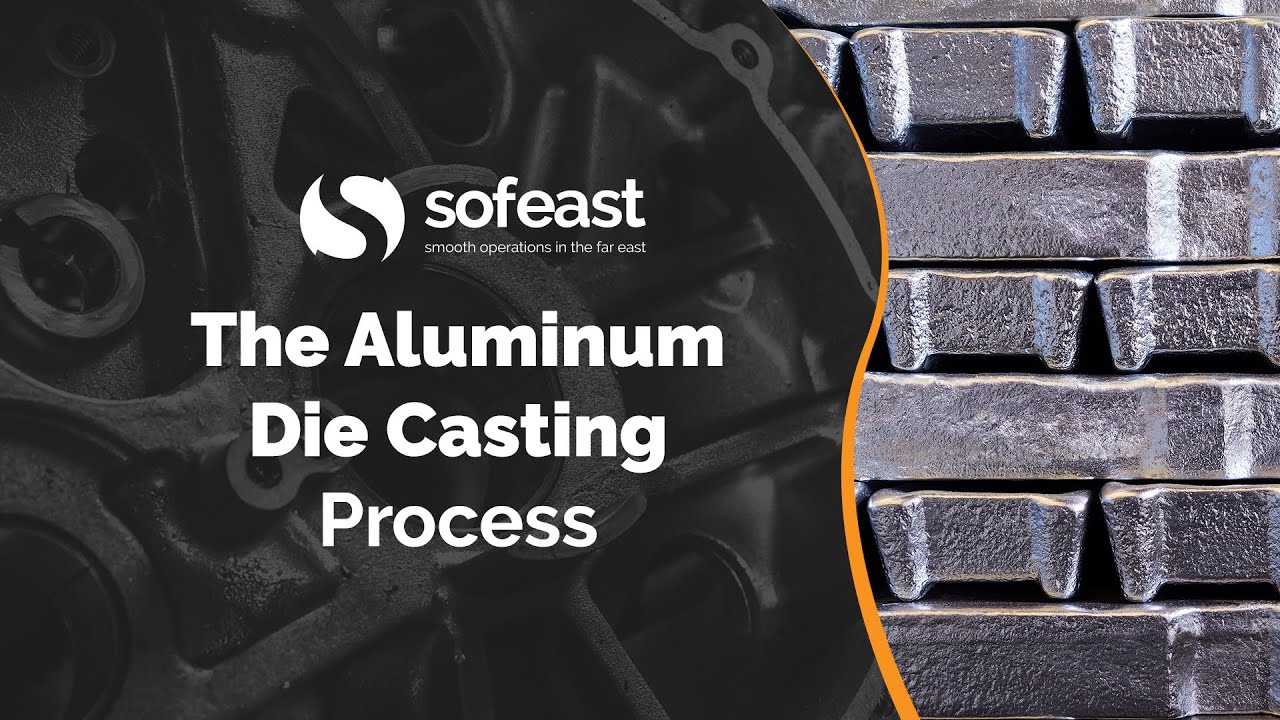
The Aluminum Die Casting Process
5.0 / 5 (0 votes)