Torsion Test Demonstration: Cast Iron and Carbon Steel
Summary
TLDRIn this video, Andy from the Engineer's Academy demonstrates torsion testing on two materials: cast iron and 0.4% carbon steel. Using a torsion tester, each material undergoes twisting until failure, with torque and angle of twist monitored. The cast iron sample fails quickly after minimal plastic deformation, highlighting its brittleness. In contrast, the carbon steel sample deforms more significantly, showcasing its malleability and ductility before eventually failing. The video offers valuable insights into the differences in material properties and their behavior under torsion stress.
Takeaways
- π The video explains the process of conducting torsion tests on two different material samples: cast iron and 0.4% carbon steel.
- π Torsion tests are carried out using a machine that applies rotational force to a material sample to measure its response.
- π The machine has two key displays: one shows the torque required to twist the sample, and the other shows the angle of twist.
- π Each click of the machine indicates a rotation of 9.3 degrees of the test piece, and the test continues until the sample fails.
- π The cast iron sample is tested first, and the process begins slowly to observe elastic deformation before accelerating to plastic deformation.
- π During plastic deformation, the torque required to twist the material levels off, indicating that the material is no longer increasing in stiffness.
- π The test on cast iron ultimately leads to material failure in the center, indicating that it is more brittle compared to the second sample.
- π The second material sample tested is 0.4% carbon steel, which behaves differently due to its greater ductility and malleability.
- π As the 0.4% carbon steel undergoes torsion, the torque rises steadily, indicating a more gradual response during elastic deformation.
- π The 0.4% carbon steel sample goes through significantly more plastic deformation before failure, demonstrating its greater ability to withstand twisting.
- π The failure of the carbon steel sample occurs after a significant number of revolutions, and its surface shows signs of oxidation as it twists.
- π The video emphasizes that one thousand clicks on the machine represents approximately 300 degrees of twist, and the test continues until failure occurs.
Q & A
What is the primary objective of the torsion test in the video?
-The primary objective of the torsion test is to evaluate how different materials, cast iron and 0.4% carbon steel, behave under torsional stress, specifically measuring the torque required to twist the material and the angle of twist until failure.
What are the key components of the torsion testing machine?
-The key components of the torsion testing machine are the two chucks that hold the test piece, the torque measurement display, and the angle of twist display. The machine applies torque to twist the material and records the corresponding angle of twist.
How does the machine measure the amount of twist applied to the test piece?
-The machine measures the twist through an audible click every 9.3 degrees of rotation. The torque required for each twist is displayed, and the angle of twist is shown on a separate display.
What happens to the test piece during the elastic deformation phase?
-During the elastic deformation phase, the test piece begins to experience tension as it is twisted, but the material returns to its original shape once the applied torque is removed. The torque increases steadily as the material deforms elastically.
What occurs during the plastic deformation phase of the torsion test?
-During plastic deformation, the torque reading levels off as the material undergoes permanent deformation. The material continues to twist, but there is a limited increase in torque as it becomes more malleable.
What is the main difference between cast iron and 0.4% carbon steel in the torsion test?
-Cast iron is more brittle and fails after less plastic deformation, showing a leveling off of torque early in the test. In contrast, 0.4% carbon steel is more ductile and undergoes more plastic deformation before it eventually fails.
How does the torque behavior of 0.4% carbon steel differ from that of cast iron?
-The torque behavior of 0.4% carbon steel increases steadily through both elastic and plastic deformation phases, showing a gradual rise in torque as the material becomes more malleable. Cast iron, however, exhibits a sharp leveling off of torque once it enters plastic deformation, indicating its brittleness.
What does the audible click signify during the torsion test?
-The audible click signifies that the test piece has twisted by 9.3 degrees, providing a real-time indication of the angular rotation as the test progresses.
What is the significance of the number of revolutions before failure?
-The number of revolutions before failure indicates how much the material can twist before it breaks. This measurement helps in understanding the material's capacity for plastic deformation and its overall durability under torsional stress.
How does the appearance of the 0.4% carbon steel test piece change during the test?
-As the torsion test progresses, the surface of the 0.4% carbon steel test piece shows signs of oxidation and crumbling, indicating the material is undergoing significant plastic deformation before it fails.
Outlines
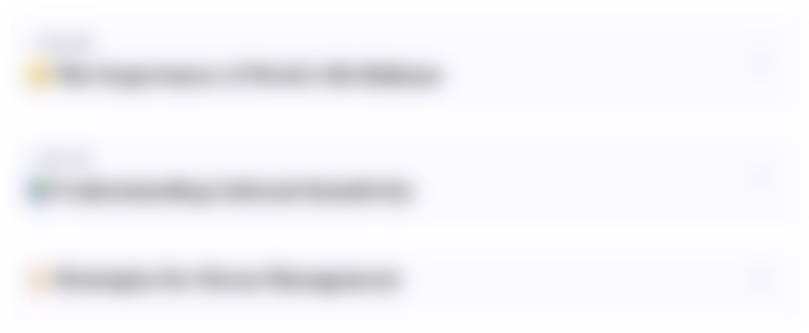
This section is available to paid users only. Please upgrade to access this part.
Upgrade NowMindmap
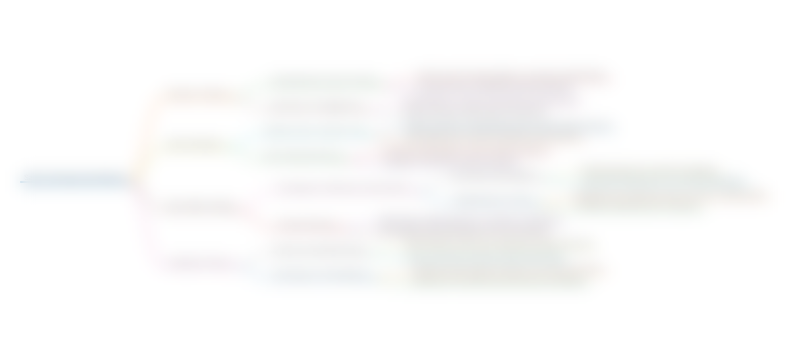
This section is available to paid users only. Please upgrade to access this part.
Upgrade NowKeywords
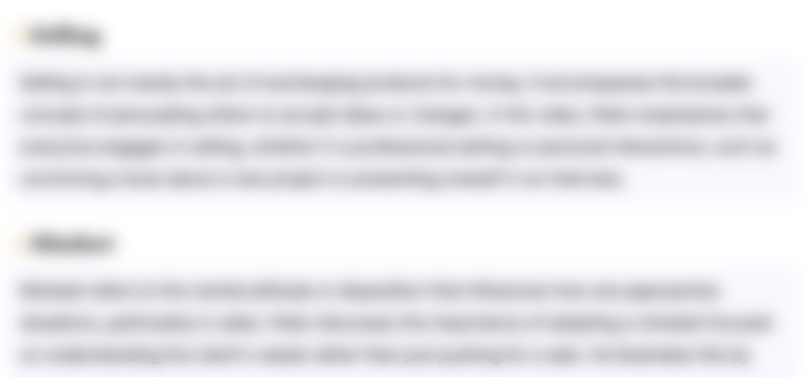
This section is available to paid users only. Please upgrade to access this part.
Upgrade NowHighlights
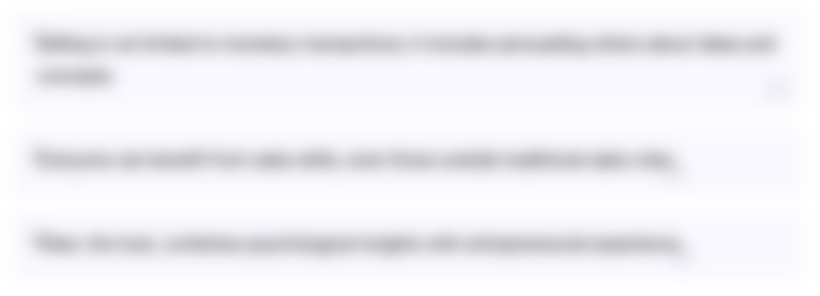
This section is available to paid users only. Please upgrade to access this part.
Upgrade NowTranscripts
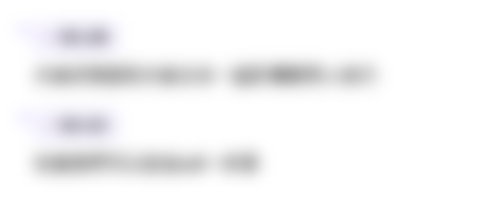
This section is available to paid users only. Please upgrade to access this part.
Upgrade NowBrowse More Related Video

What is Torsion Testing?

ultrasonic testing
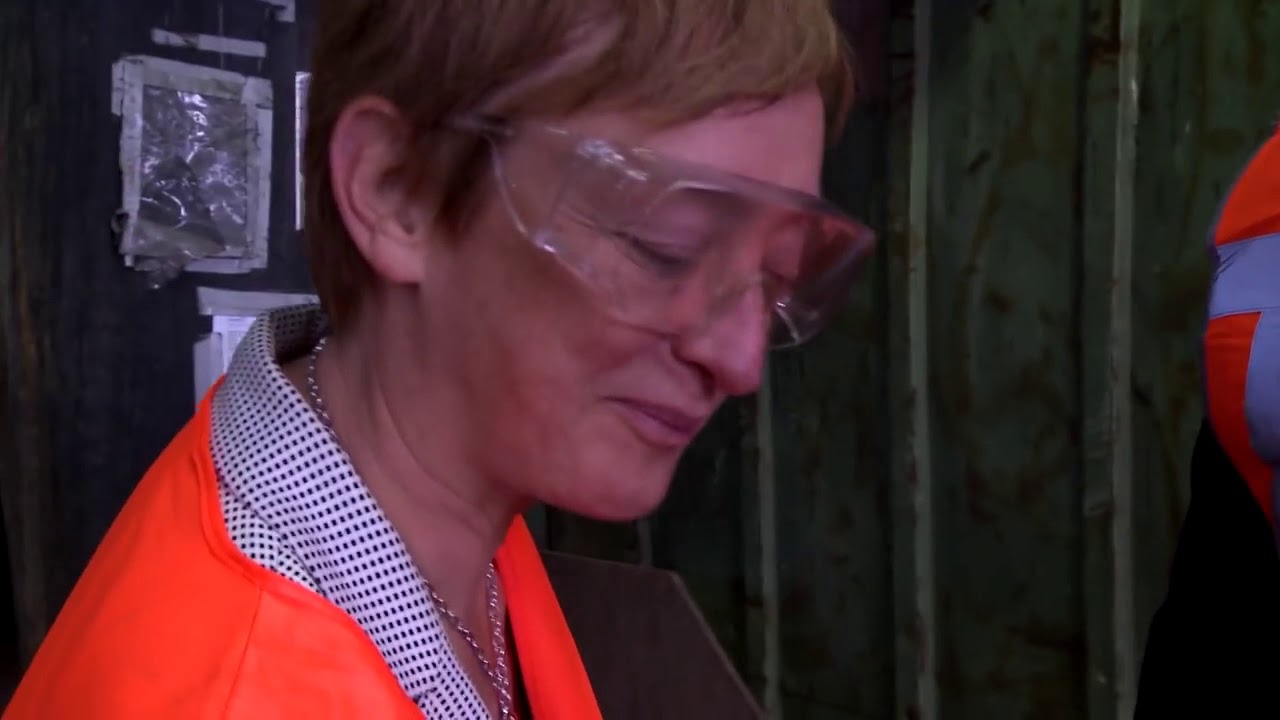
5.2.1 Recycling case: Coolrec
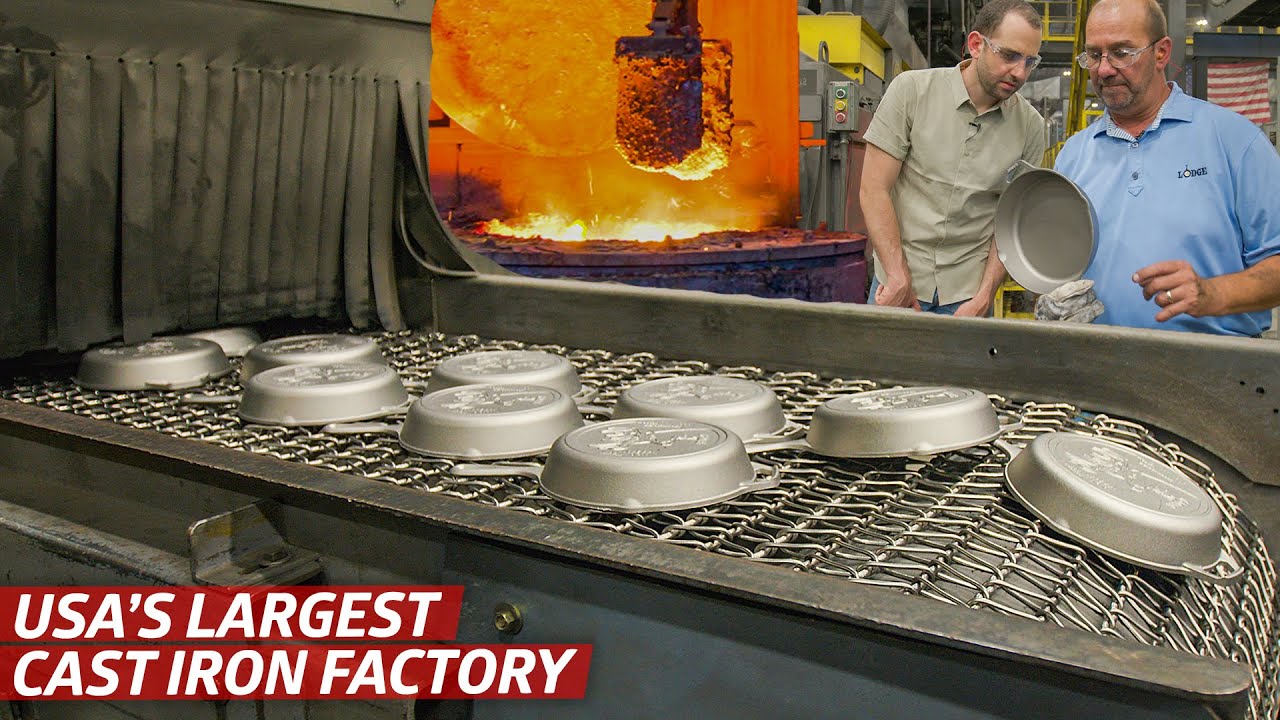
How America's Largest Cast Iron Pan Factory Makes Almost Two Million Pans per Month β Dan Does

Kampas Ganda Pantekan atau Relining Buat Motor Matic | Gridoto Tips
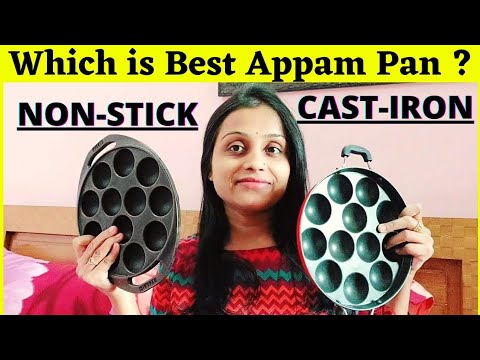
Cast Iron Appe Pan VS Non Stick Appe Pan ~Amazon Great Republic Sale 2022 ~Best Panniyaram Pan India
5.0 / 5 (0 votes)