Lean Manufacturing - Kaizen Methodology - Lean FastCap Style
Summary
TLDRThis video demonstrates how Kaizen, a methodology for continuous improvement, was applied to streamline a specific task in a workplace. By identifying and refining small inefficiencies—like fumbling with tools and unnecessary motions—the team managed to reduce task time from 45 seconds to as low as 14 seconds. Through adjustments such as repositioning tools and improving handling techniques, the team demonstrated that small, consistent changes can lead to significant time and cost savings. This process highlights the importance of always seeking ways to improve, showing that even the most refined methods can always get better.
Takeaways
- 😀 Kaizen is about continuous improvement, focusing on refining processes step by step.
- 😀 Small changes, like repositioning the cone and adjusting movements, can significantly improve efficiency.
- 😀 The goal of Kaizen is to eliminate wasted motion and time, leading to smoother and faster processes.
- 😀 By reducing the time spent on each task, companies can achieve massive time and cost savings over time.
- 😀 The process of improvement involves experimenting with different methods and learning as you go.
- 😀 Repeatedly refining and adjusting processes is key to making incremental improvements that add up.
- 😀 Even when a process seems efficient, there is always room for further refinement and optimization.
- 😀 In this example, the time to complete a task was reduced from 45 seconds to as low as 14 seconds through adjustments.
- 😀 Small changes made to the method of grabbing and handling items can drastically improve the speed of the task.
- 😀 Continuous improvement isn't just about getting faster, it's about making the process easier and more sustainable in the long term.
- 😀 Kaizen's success is not just in the result but in the process of constantly striving to make things better, no matter how small the improvements.
Q & A
What was the initial challenge in the process described in the video?
-The initial challenge was that the task took 45 seconds to complete, with problems related to fumbling, positioning the sleeve over the cone, and inefficient handling of components.
How did the team address the issue of reaching for the cone?
-The team moved the cone closer to the worker to reduce the wasted motion of reaching behind. This change allowed the worker to more easily grab and place the components in one smooth motion.
What is the key improvement that made a significant difference in the process time?
-A major improvement was using one consistent motion to grab the components, particularly by using both hands to grab the insert and can in a single, efficient motion.
How did the sleeve placement contribute to the improvement?
-The sleeve was placed on the cone first and then pulled down smoothly. This adjustment allowed for a more efficient process by reducing fumbling and ensuring the sleeve was positioned correctly before the cone was placed on the activator.
What was the final time achieved for the task after implementing the improvements?
-After implementing the improvements, the task time was reduced to 14-16 seconds, down from the original 45 seconds.
What is the philosophy behind Kaizen, as demonstrated in this video?
-Kaizen focuses on continuous improvement. Even after making significant gains, the process is further refined to eliminate inefficiencies and improve performance. The goal is to achieve constant, incremental improvements over time.
How much time and money were saved by improving this process?
-The improvements saved 200 man-hours annually and $3,000 in labor costs, demonstrating the significant impact of streamlining the process.
What role does collaboration play in the improvement process?
-Collaboration is critical, as the video shows multiple team members, including Megan and Andre, working together to identify inefficiencies, share ideas, and implement changes that enhance the process.
What does the video say about the importance of maintaining a relaxed pace during the process?
-The video emphasizes that maintaining a relaxed and consistent pace is important. Rapid execution under pressure can lead to mistakes, so the focus is on making the task simple, efficient, and sustainable throughout the day.
How does the Kaizen methodology help in the long run?
-By continuously refining processes, Kaizen helps eliminate small inefficiencies that, over time, result in substantial savings in time and money. The ongoing improvements make operations more efficient and productive.
Outlines
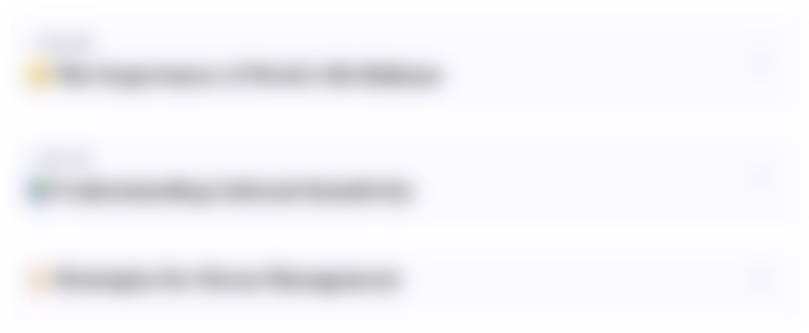
This section is available to paid users only. Please upgrade to access this part.
Upgrade NowMindmap
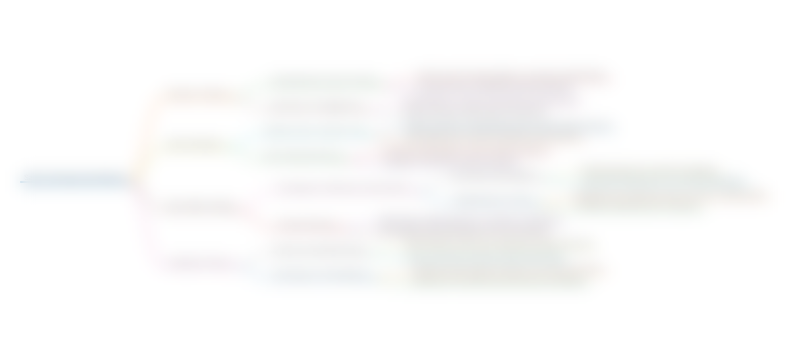
This section is available to paid users only. Please upgrade to access this part.
Upgrade NowKeywords
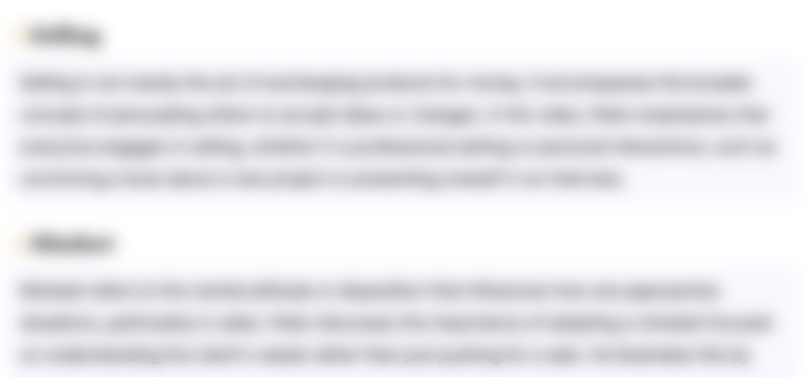
This section is available to paid users only. Please upgrade to access this part.
Upgrade NowHighlights
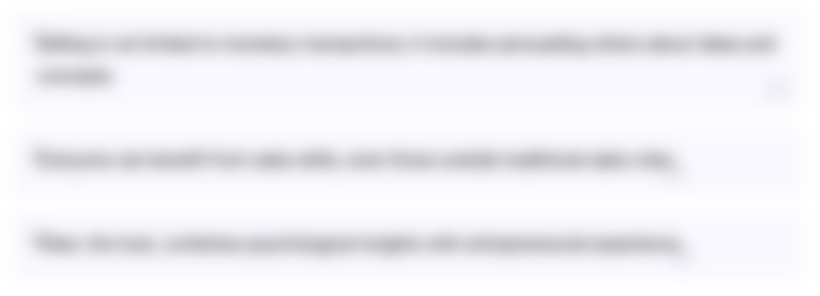
This section is available to paid users only. Please upgrade to access this part.
Upgrade NowTranscripts
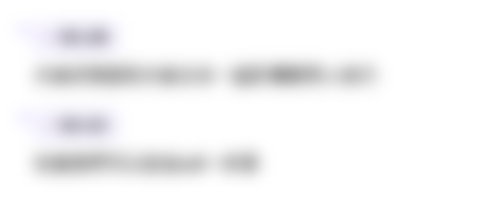
This section is available to paid users only. Please upgrade to access this part.
Upgrade NowBrowse More Related Video

Strategi 5S/5R Kaizen di Tempat Kerja Untuk Meningkatkan Produktivitas Usaha

Continuous Improvement Explained: Whiteboard Animation

KAIZEN RAHASIA DIBALIK PRODUKTIVITAS JEPANG
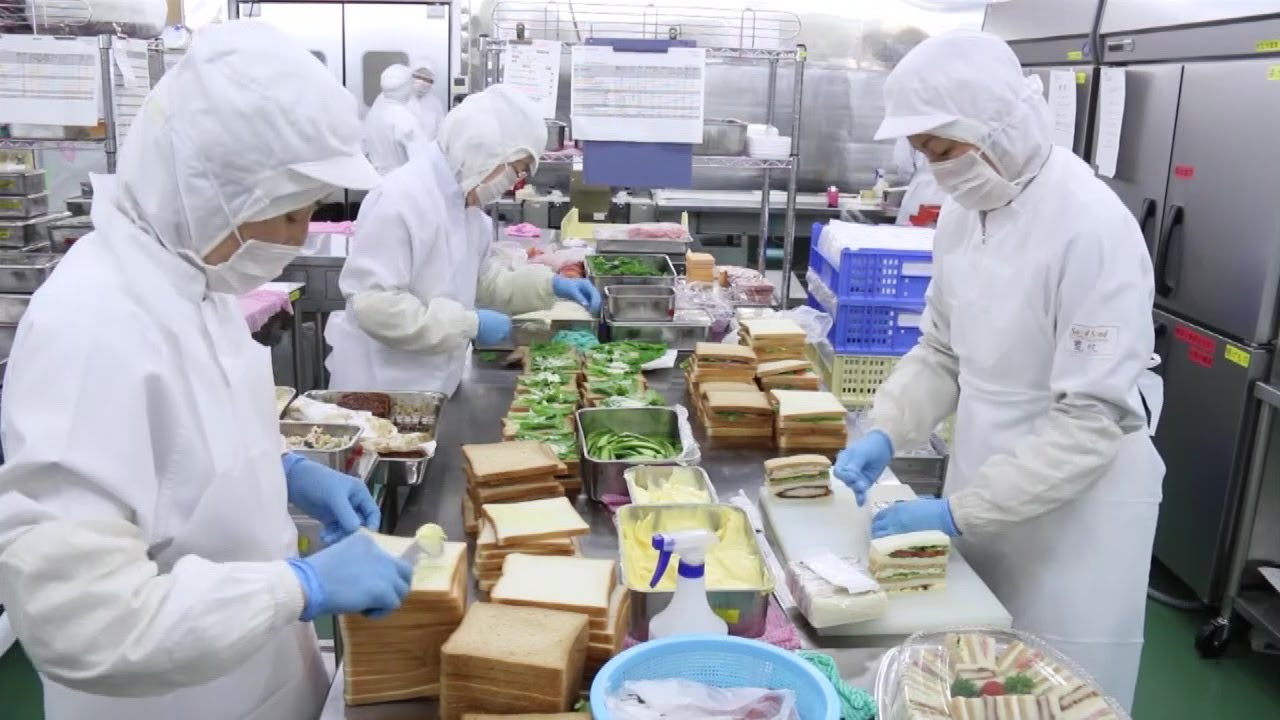
Kaizen The Secret behind Japanese Productivity

The 5S Game (Lean Six Sigma)

Exemplos de Lean Manufacturing, Kaizen, 5S e inclusão social em empresas japonesas
5.0 / 5 (0 votes)