DIE ATTACH PROCESS
Summary
TLDRThis video provides a detailed overview of the die attach process in semiconductor packaging. The process involves several machine sub-assemblies working in sync, from handling leadframes and substrates to dispensing epoxy or solder for die attachment. Key components like the wafer handler, pick and place system, and ejector assembly are explained, along with specifications for epoxy coverage, bond line thickness (BLT), and die placement. The video emphasizes the importance of precise setup and quality control to ensure proper die attachment and adhesion, including shear strength tests to verify the device's reliability.
Takeaways
- 😀 The die attach process is a crucial step in semiconductor packaging, involving multiple machine sub-assemblies that must work in sync.
- 😀 The workholder handles the leadframes or substrates from input to output, using the input loader to feed them into the system.
- 😀 Epoxy is dispensed at every programmed position of the die attach pad (DAP) by the epoxy dispenser, which is mounted along the indexer.
- 😀 For soft solder die attach, an epoxy dispenser is replaced by a solder wire feed station, while eutectic die attach does not use either.
- 😀 The wafer handler manages sawn wafers mounted on tape, ensuring the tape expands for proper die placement and avoiding die damage.
- 😀 The pick and place system includes a bond arm for die placement and an ejector assembly to push the die from the mounting tape.
- 😀 A pattern recognition system (PRS) helps identify and reject defective dice during the die attach process, ensuring only good dice are used.
- 😀 Epoxy coverage must be 100% under the die, with visible epoxy fillet of at least 90% on each side to meet quality standards.
- 😀 Bond line thickness (BLT), or the thickness of adhesive epoxy under the die, should be at least 25um before curing to maintain the proper die attachment.
- 😀 Die placement and orientation are driven by wire bonding layout, and correct nozzle sizes must be used for dispensing epoxy according to die size.
Q & A
What is the die attach process in semiconductor packaging?
-The die attach process involves attaching a semiconductor die to a leadframe or substrate using an adhesive, typically epoxy, solder, or eutectic materials. This process is crucial for device performance and requires precision in dispensing and placing the die.
What role does the input loader play in the die attach process?
-The input loader handles stacks of leadframes or substrates and feeds them into the indexer, ensuring proper alignment and movement throughout the process.
What is the purpose of the epoxy dispenser in the die attach process?
-The epoxy dispenser is mounted along the indexer and dispenses epoxy onto the die attach pad (DAP) at programmed positions, ensuring the die is securely attached during the process.
How does the wafer handler contribute to the die attach process?
-The wafer handler is responsible for handling sawn wafers mounted on tape. It ensures that the dice are spaced properly to avoid damage or chipping during the pickup process.
What is the significance of the bond arm and ejector in the pick and place system?
-The bond arm picks up the die from the wafer and places it onto the leadframe or substrate. The ejector assembly, with a special ejector needle, ensures the die is correctly separated from the mounting tape.
What is the role of the pattern recognition system (PRS) in die selection?
-The PRS scans each die to identify and separate the good dice from defective ones by recognizing their unique patterns or ink markings, ensuring only the good dice are processed.
What are the key requirements for epoxy coverage in the die attach process?
-Epoxy coverage must be 100% under the die, with a visible epoxy fillet of at least 90% on each side of the die to ensure proper adhesion and performance.
What is BLT, and why is it important in the die attach process?
-BLT stands for Bond Line Thickness, which refers to the thickness of the adhesive epoxy under the die. A typical requirement is at least 25um, and it ensures proper die adhesion and thermal performance.
Why is the proper die orientation critical in the die attach process?
-The die placement and orientation are critical for wire bonding, as they need to align with the layout specified in the build diagram. Misalignment can lead to issues in the bonding process.
What are the potential risks of using a piercing needle for die pickup?
-Using a piercing needle with a small tip radius can cause microcracks on the die's backside during pickup, particularly for large, thin dice, which can compromise the die's reliability and performance.
Outlines
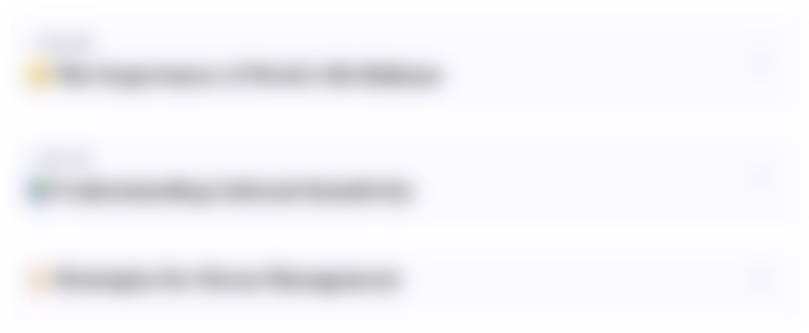
This section is available to paid users only. Please upgrade to access this part.
Upgrade NowMindmap
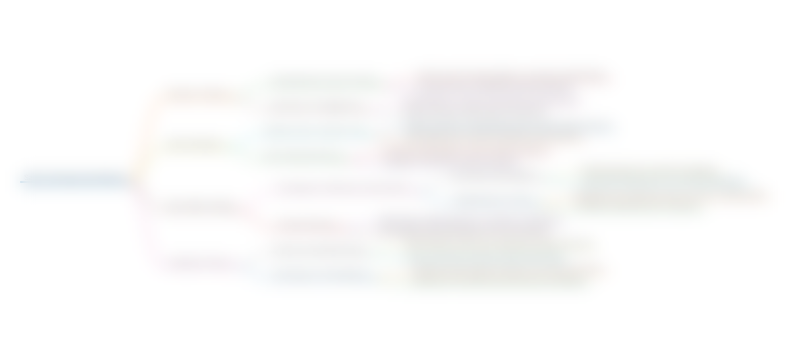
This section is available to paid users only. Please upgrade to access this part.
Upgrade NowKeywords
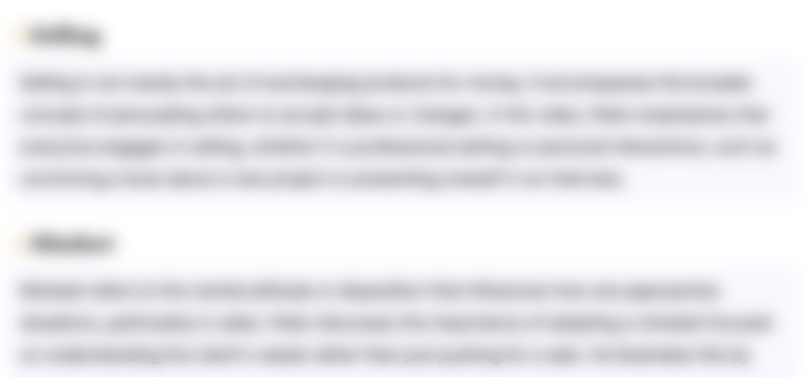
This section is available to paid users only. Please upgrade to access this part.
Upgrade NowHighlights
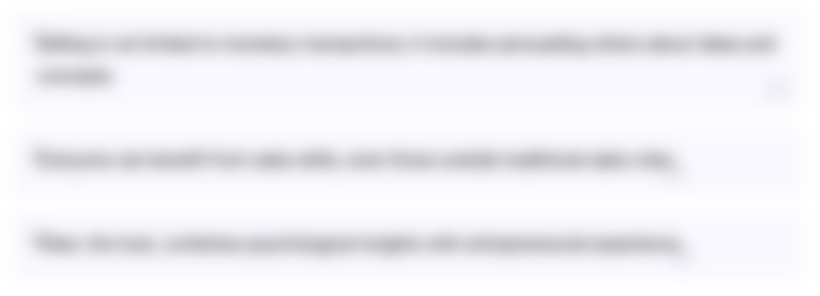
This section is available to paid users only. Please upgrade to access this part.
Upgrade NowTranscripts
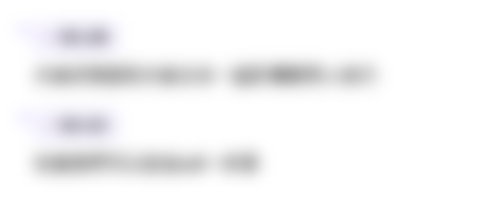
This section is available to paid users only. Please upgrade to access this part.
Upgrade NowBrowse More Related Video
5.0 / 5 (0 votes)