An Axial Flux BLDC Motor Build
Summary
TLDRIn this video, the creator explores the process of building a brushless direct current (BLDC) motor with a modern axial flux design, utilizing 3D printed parts for efficiency and innovation. The script covers the detailed steps involved, from choosing the motor's components to assembling and testing it. The motor's performance is evaluated through various tests, such as determining its KV rating, efficiency, and maximum speed. Challenges like high resistance in ball bearings are addressed, and despite setbacks, the motor demonstrates impressive results. The video wraps up with insights on future projects and encourages audience interaction.
Takeaways
- 😀 The project involves building a brushless DC (BLDC) electric motor, starting with understanding the motor's design and choosing the appropriate type.
- 😀 The motor chosen is an axial flux BLDC motor, which is more efficient and has a greater power-to-weight ratio compared to radial flux motors.
- 😀 To reduce wasted magnetic flux, the design includes a second rotor in addition to the stator with electromagnets and permanent magnets on the rotor.
- 😀 The number of electromagnets and permanent magnets is based on a combination of six electromagnets to eight magnetic poles, which affects the motor's speed and torque.
- 😀 The motor was 3D modeled and printed with complex parts that included rotors, stator, and winding mechanism for the electromagnet coils.
- 😀 The rotor magnets were glued using superglue (despite concerns about durability), arranged in a Halbach configuration to enhance the magnetic field's strength.
- 😀 A Y configuration was used for the electromagnets to control the polarity of the North and South poles, simplifying the motor's control system.
- 😀 Assembly of the motor involved using a steel rod for the shaft, ball bearings, and multiple nuts and bolts for alignment and fixation.
- 😀 The motor required specific timing from the speed controller to manage the phases and ensure proper rotation of the rotor.
- 😀 Efficiency tests showed the motor had a 50% efficiency, which is better than traditional combustion engines but still lower than existing electric motors.
- 😀 The motor's maximum speed was tested to reach approximately 2,650 RPM, and the motor's weight was measured at 830g, which is on the heavier side given its power output.
Q & A
What motivated you to build an electric motor?
-I had always wanted to understand and build an electric motor. After gaining experience from making a historic motor design, I felt it was the right time to try my hand at a modern and potentially useful design.
Why did you choose to build a brushless DC motor (BLDC)?
-I chose a BLDC motor because it doesn't require a commutator or brushes, which are known for creating sparks, wearing out, and causing noise. BLDC motors are more efficient and reliable compared to traditional motors with brushes.
What is the difference between radial flux and axial flux motors?
-The primary difference lies in the orientation of the magnets. In radial flux motors, the magnets are perpendicular to the axis of rotation, while in axial flux motors, the magnets are parallel to the axis of rotation. Axial flux motors are typically more efficient and have a better power-to-weight ratio.
Why did you choose an axial flux motor design over a radial flux one?
-I decided on an axial flux design because it's more efficient, and 3D printers are excellent at producing the complex parts required for such a design.
What is the role of the rotor and stator in the motor?
-The rotor contains permanent magnets that rotate and align with the electromagnets in the stator. The stator houses the electromagnet coils, which create a magnetic field that interacts with the rotor's permanent magnets, causing the rotor to spin.
What was the issue with the superglue used to attach the magnets to the rotor?
-Superglue isn't ideal because it deteriorates at high temperatures, around 80°C. However, I used it because I expected that the PLA plastic parts would already deform at 60°C, so the glue's failure wasn't likely to be a major issue.
What is a Halbach configuration and why did you use it for the motor's magnets?
-A Halbach configuration is a specific arrangement of magnets that strengthens the magnetic field on one side and weakens it on the other. This configuration is used to create a more uniform and stronger magnetic field, which improves the motor's performance.
How did you ensure that the electromagnet coils were identical?
-I built a simple winding and counting mechanism to make sure that all the coils had the same number of turns (52 turns each), ensuring consistency in the electromagnet coils.
What is the significance of the Y-configuration in wiring the motor's phases?
-The Y-configuration connects the coils in a way that allows for the control of which electromagnets generate north or south poles by switching which phase is connected to power and which to ground. This setup is easier to implement compared to the alternative Delta configuration.
What was the problem you encountered during testing, and how did you solve it?
-During testing, the motor had trouble starting. I realized that the ball bearings were likely causing resistance. After removing their protective coverings, cleaning them, and applying my own lubricant, the motor ran much more smoothly.
What method did you use to determine the KV rating of the motor?
-I measured the rotation speed of the motor while using an electric drill to rotate it. By recording the voltage and speed, I was able to calculate the KV rating, which turned out to be around 230.
What was the motor's efficiency, and how did you measure it?
-The motor achieved an efficiency of over 50%, which is better than many internal combustion engines. I measured this using a prony brake to apply a load while logging the speed, voltage, and current supplied to the motor.
What was the maximum speed the motor could reach in your tests?
-The motor could reach up to 2,650 revolutions per minute (RPM) before I wrapped up testing.
How much did the motor weigh, and how does this compare to its power output?
-The motor weighed around 830 grams, which is on the heavy side for the power output it produces. However, the results were satisfactory for a learning project.
Outlines
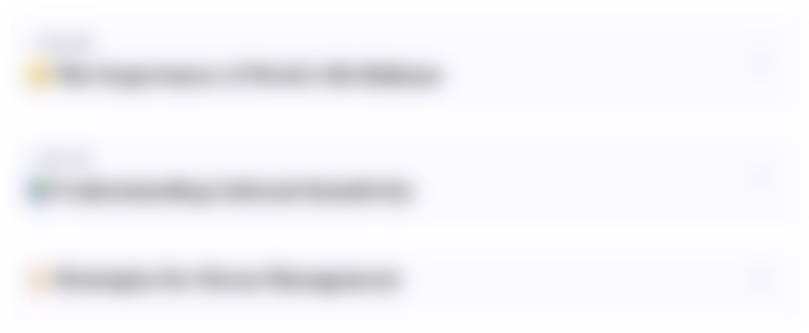
This section is available to paid users only. Please upgrade to access this part.
Upgrade NowMindmap
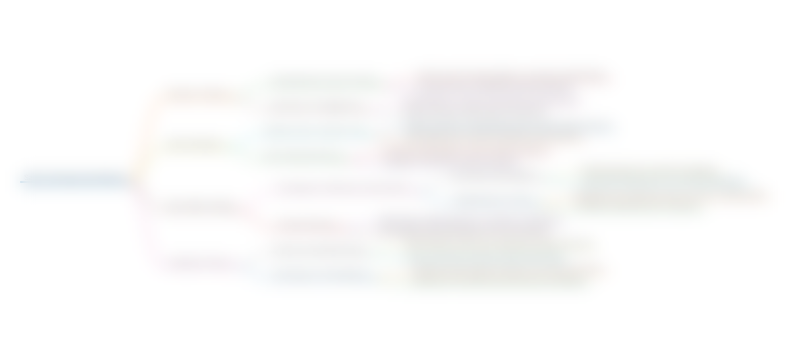
This section is available to paid users only. Please upgrade to access this part.
Upgrade NowKeywords
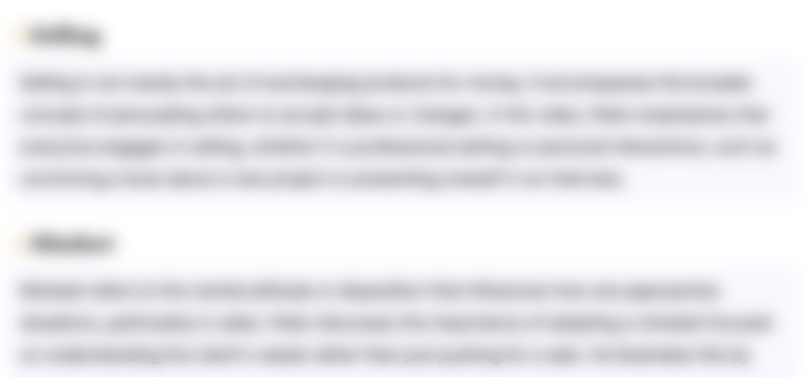
This section is available to paid users only. Please upgrade to access this part.
Upgrade NowHighlights
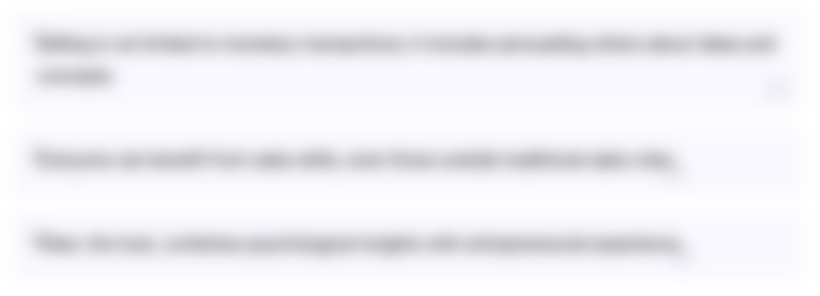
This section is available to paid users only. Please upgrade to access this part.
Upgrade NowTranscripts
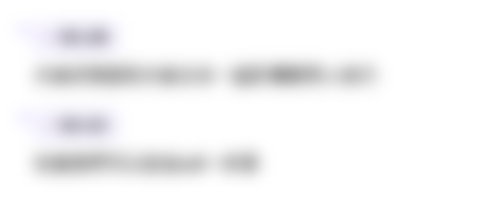
This section is available to paid users only. Please upgrade to access this part.
Upgrade NowBrowse More Related Video
5.0 / 5 (0 votes)