MIKROBIOLOGI TEORI KELOMPOK 11 "Denah Tata letak ruang produksi steril"
Summary
TLDRThis video script provides a detailed explanation of the layout and sterilization processes in a pharmaceutical production facility. It discusses various rooms and their functions in ensuring sterile conditions, from material entry to component sterilization. The rooms are categorized into different cleanliness levels, such as Class A, B, C, and D, with specific air pressure and sterilization protocols to minimize microbial contamination. The script also emphasizes the role of personnel and equipment, outlining strict hygiene and protective measures required to maintain sterile environments, ensuring the production of safe and high-quality pharmaceutical products.
Takeaways
- 😀 The script outlines the layout of a sterile production room for aseptic product manufacturing and sterilization processes.
- 😀 Material entry into the sterile production area is carefully controlled, with pressure regulation to prevent contamination.
- 😀 Several rooms within the facility are designated for different stages of sterilization, each with specific pressure levels (ranging from 10 to 50 Pa).
- 😀 Air filters play a critical role in ensuring that the air entering clean areas is free of contaminants, especially in pharmaceutical production.
- 😀 The sterilization process involves multiple stages, starting from pre-sterilized components to final product sterilization.
- 😀 Some areas, such as those for raw material preparation and component washing, are less sterile but still follow rigorous contamination control standards.
- 😀 Personnel working in sterile areas are required to follow strict hygiene protocols, including wearing head and face covers, protective clothing, and gloves.
- 😀 Sterilization rooms are classified into different cleanliness levels, such as Class A, B, C, and D, based on the risk and sensitivity of the processes occurring in each room.
- 😀 The final sterilization process involves the sealing and packaging of products in environments designed to minimize microbial contamination.
- 😀 Pressure differences between rooms (such as Class A or Class C) are maintained to ensure that clean air flows from higher to lower cleanliness areas, preventing contamination.
Q & A
What is the main focus of the presentation?
-The presentation focuses on the layout of rooms in a pharmaceutical production facility for aseptic processing and sterilization of products.
How is the sterility of different rooms maintained in the facility?
-Sterility is maintained through controlled air pressure, with different rooms having varying pressures to minimize microbial contamination, such as 10 Pa, 20 Pa, and 30 Pa.
What is the role of the first room in the production layout?
-The first room is designated for receiving raw materials or components and is maintained at a sterile environment with a pressure of 10 Pa to ensure cleanliness before processing.
How is sterilization achieved for components in the facility?
-Sterilization is carried out in specific rooms, such as through ovens, filters, or autoclaves, with the materials being subjected to proper temperature and pressure conditions to eliminate microbial contamination.
What is the significance of 'Class A' and 'Class B' areas in the facility?
-'Class A' areas are critical zones with the highest sterility levels, such as those used for filling vials or other high-risk procedures. 'Class B' areas have a slightly lower level of sterility and are used for tasks with a reduced risk of contamination.
What are the conditions necessary for personnel in the sterile environment?
-Personnel must wear full protective clothing, including head coverings, face masks, gloves, and other sterile gear, to prevent contamination in the clean areas.
What is the role of air filtration in maintaining the cleanliness of the rooms?
-Air filtration systems, such as high-efficiency particulate air (HEPA) filters, are used to maintain a sterile environment by filtering out airborne particles and microorganisms before air is circulated into the clean rooms.
Why is there a need for different pressure levels in the rooms?
-Different pressure levels in the rooms help prevent contamination by ensuring that air flows from cleaner to less clean areas, minimizing the risk of cross-contamination between rooms.
What processes are performed in 'Class C' areas?
-Class C areas are used for processes with lower contamination risks, such as preparing and filling products like ointments, creams, or emulsions. These areas have a lower level of sterility than Class A or B areas.
How is the cleanliness of packaging materials ensured in the production process?
-Packaging materials are cleaned and sterilized before use in the production process. The materials are stored in sealed, clean environments and handled with minimal exposure to contamination.
Outlines
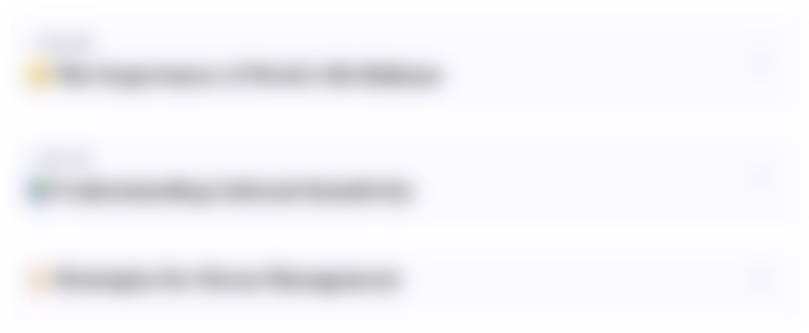
This section is available to paid users only. Please upgrade to access this part.
Upgrade NowMindmap
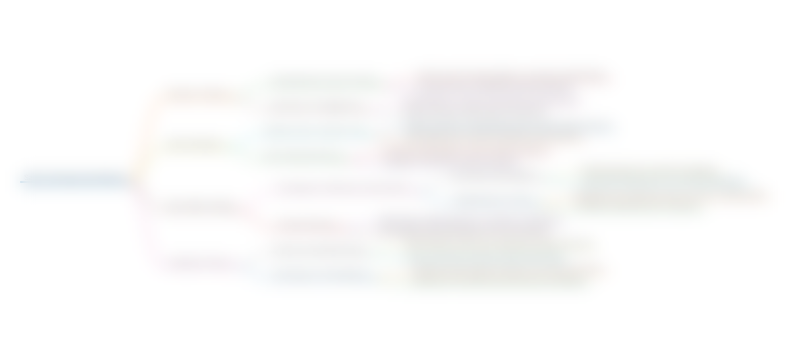
This section is available to paid users only. Please upgrade to access this part.
Upgrade NowKeywords
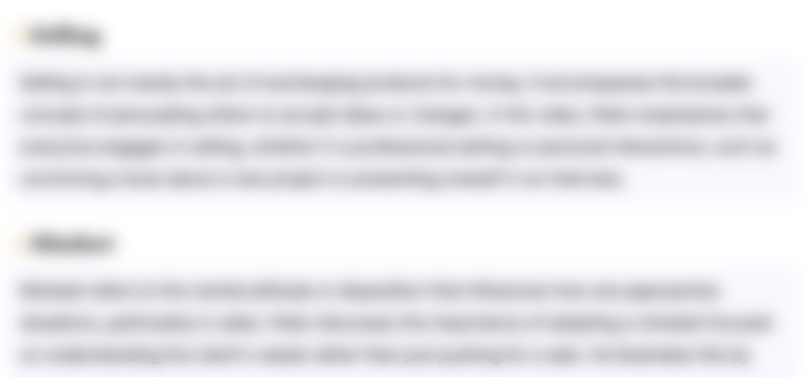
This section is available to paid users only. Please upgrade to access this part.
Upgrade NowHighlights
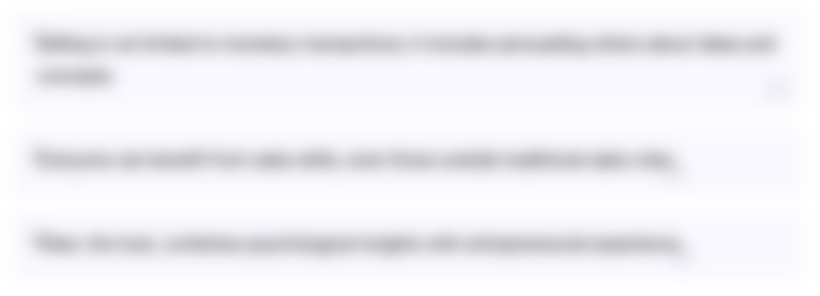
This section is available to paid users only. Please upgrade to access this part.
Upgrade NowTranscripts
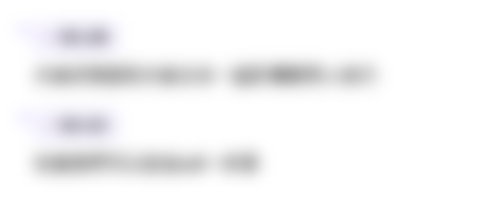
This section is available to paid users only. Please upgrade to access this part.
Upgrade NowBrowse More Related Video
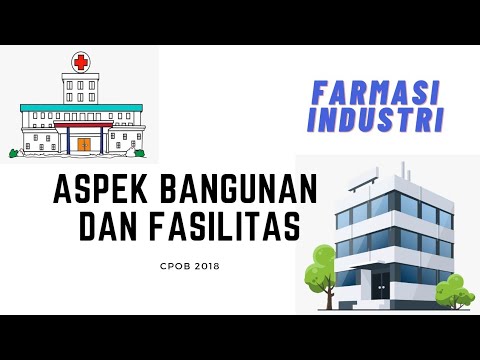
FASILITAS DAN BANGUNAN (FARMASI INDUSTRI)
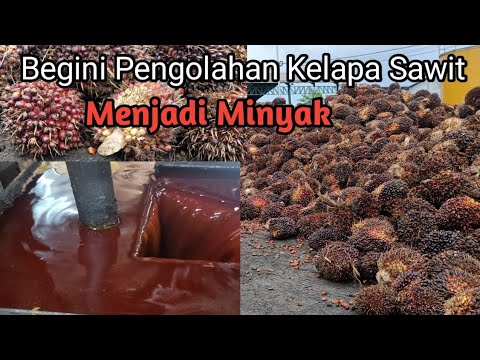
Process of processing fresh palm oil from the beginning to become CPO oil #Sitanggang_Tanggarube
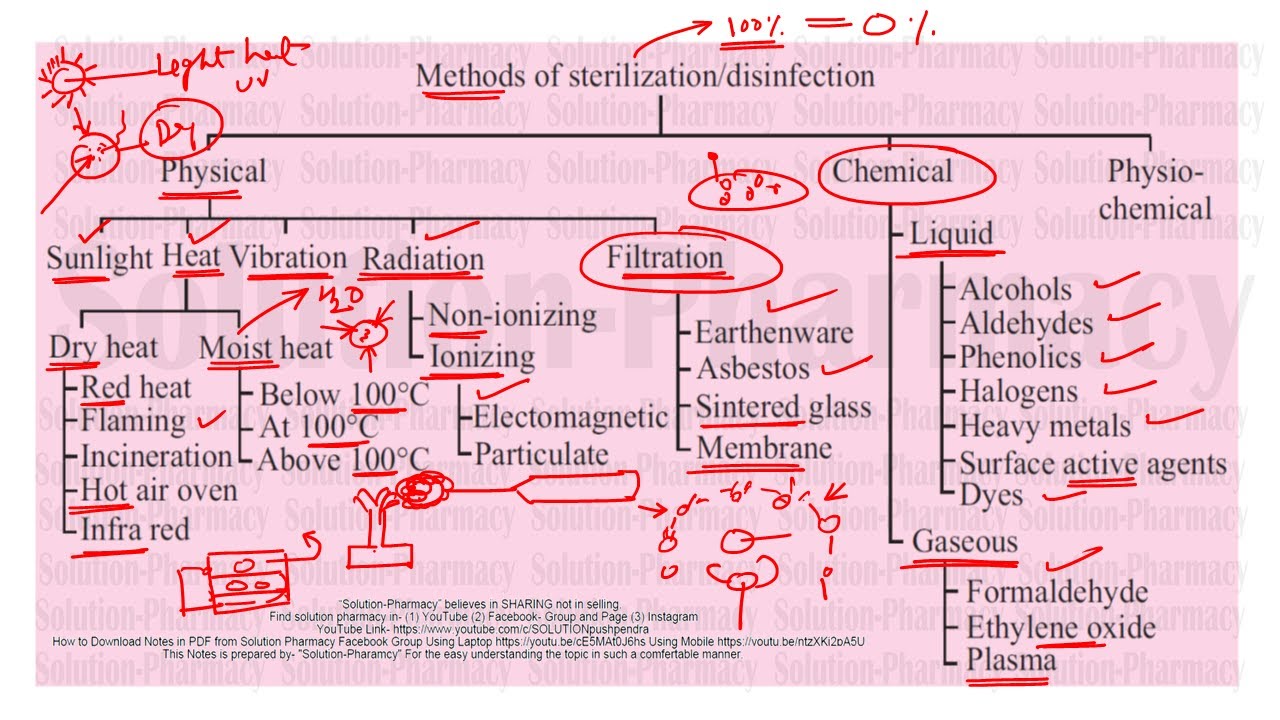
Sterilization (Microbiology) | Method of Sterilization | Physical + Chemical Method of Sterilization

Experience the Future: Inside Our State-of-the-Art Pharma Factory

Layout dan Proses Produksi Eps 2
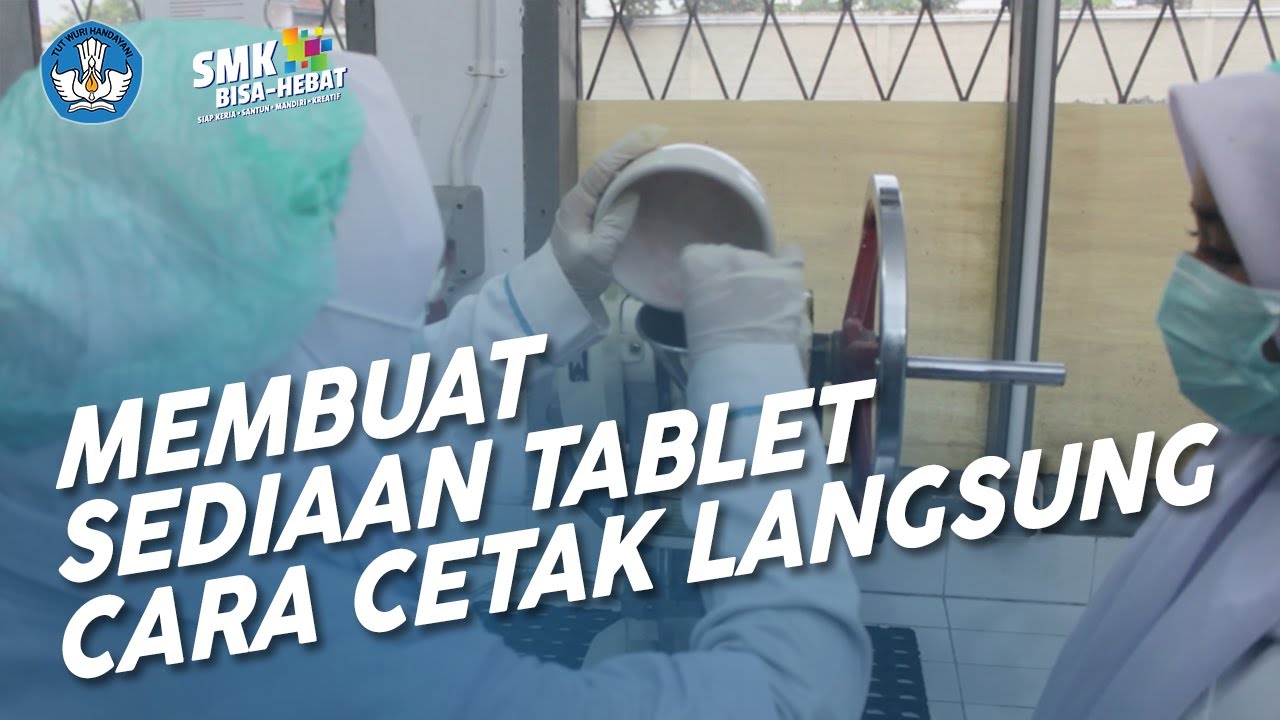
Membuat Sediaan Tablet Cara Cetak Langsung - Farmasi
5.0 / 5 (0 votes)